Choosing Sheet Pile Repair Methods
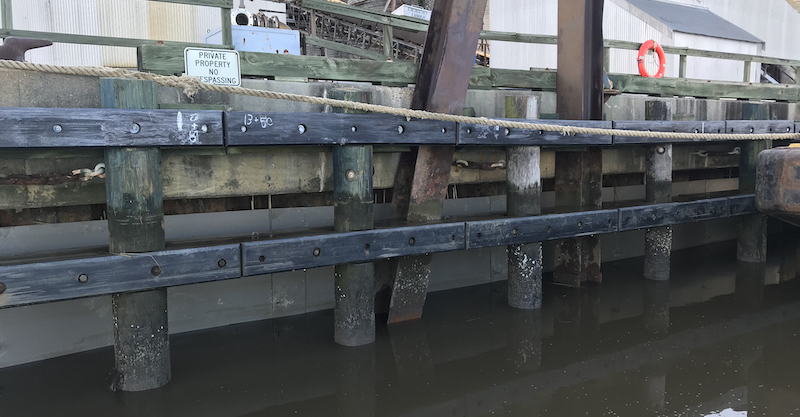
By Paul A. Thomas, PE, MBA, Senior Structural Engineer, QuakeWrap Inc., and Steve Delgado, Marketing Manager, QuakeWrap Inc.
Introduction
Sheet piles are one of the most common types of earth retention structures. Steel sheet piles have been in existence for over 100 years, and the methods to repair them and written descriptions of those methods have been in existence almost as long.
This article, it is hoped, will be a reference document that addresses the basic components of steel sheet pile repair.
For clarity and the purpose of this article, seawalls are defined as shore-parallel structures designed to protect upland installations, such as houses, roads, port facilities or artificially filled land areas. The term “bulkhead,” while sometimes used interchangeably with seawall, in this case will mean structures designed as docks, wharves or boat landings.
History of Sheet Piles
Steel sheet piling, also known as Larssen sheet piling, was originally developed in 1912 for use in the construction of piers, oil terminals, waste storage facilities, bridges, houses, buildings, dry docks and other construction sites. This sheet piling remains popular today as a marine retaining wall. Segments with indented profiles (troughs) interlock to form a wall with alternating indents and outdents. The troughs increase resistance to bending, with segments typically made of steel or another metal.
Steel sheet piles have been widely used in construction as ground retaining structures and seepage barriers or bulkheads. Steel, as we all know, is susceptible to corrosion when in extended contact with the environment, so the first evaluation point for your repair should be the durability of your replacement sheet pile structures against corrosion.
Advantages of Steel Piles
Steel sheet piling is the most widely used bulkhead material. Some of the advantages of steel piles:
— Steel piling can be driven into the foundation without extensive excavation. It can be driven into hard, dense soils and even soft rock.
— It is suitable for structures requiring deep soil penetration, large water depth, free standing, or most combinations of these.
— The interlocking feature of the steel sheet pile sections provide a relatively sand- or soil-tight fit that generally precludes the need for filters. This close fit may also be essentially water-tight, so regularly spaced drain holes are recommended. These and lifting holes in the piling should be backed with a proper filter to preclude loss of backfill material.
— In marine environment, the steel material is susceptible to corrosion, particularly in warm climates. The splash zone (between mean low water and the upper limit of wave contact) and areas near mud line are most vulnerable to corrosion. Protective coatings such as bitumen or concrete encasement are recommended.
Recall that steel sheet piles are heavy and require heavy equipment for installation.
Review of Basic Engineering Concepts
Prior to deciding on any sheet pile repair method, it is prudent to understand the usual construction techniques of the sheet pile wall and the forces inherent in the design of the wall because any repair method used must account for these conditions.
Recall the basic shear and moment diagrams that are present for the typical sheet pile installation (reference 1) shown below. Of course, any repair will have to consider these criteria both from the original installation and how these criteria may change due to the repair method.
Backfill and Drainage
Backfill in the anchor zone should be compacted to achieve desired resistance. Near the wall, however, the material should be sufficiently porous to allow adequate drainage. Drain holes should be tapped on the wall with adequate frequency. The location of the drain hole should be above the mean high-water line. If the material behind the wall contains fine soil, filter cloth might have to be installed to prevent excessive leaching of material.
For seawalls of inadequate elevation, it is advisable to install a drain field using pebbles or gravel. A hard surface made of reinforced concrete also could prove to be effective against erosion caused by overtopping. Such hard surface must be constructed on an adequate and well-drained foundation to be effective.
Assessing Condition
Assessing the condition of bulkheads on a regular basis can extend the service life of the sheet pile seawall or bulkhead.
The following design considerations need to be addressed to properly assess the condition of a bulkhead.
- Topography: Elevations, grading, etc.
- Soil Properties: Unit weight of soil, clay vs. sand, etc.
- Embedment/Stability: Depth of bulkhead for stability
- Water Table: Differential water levels behind and in front of walls can introduce additional loading on the wall
- Exposure: Climate, saltwater vs. fresh water
- Material Properties: Strength and performance in the marine environment
- Surcharge: Live loads behind the wall such as vehicles
- Ice Loads: As with northern climates
- Prior Maintenance
- Changes in Use.
ASCE has published a standard practice manual to provide guidance for above and below water assessment of marine structures. Note that seawall and bulkhead evaluations should be conducted by experienced, qualified personnel under the supervision of a licensed professional engineer (PE).
Methods of Repairing Steel Sheet Piles
The best repair technique or method for steel sheet piling should have the capability to prevent, halt or highly resist the renewal of the corrosion cycle. Several of the repair techniques considered here can bring the bulkhead back to its original functional condition and strengthen the structure against the corrosive environment.
For the sake of space, we’ll review the top three repair methods for steel sheet piling: Welding Repair, Repair Using Concrete, and New Facing Using FRP.
Welding Repair
Steel sheet piles with limited corrosion may be repaired by welding new steel reinforcing plates onto the structure. This repair technique is particularly applicable with steel H-piling, where severe corrosion is generally limited to a small zone near the mean water level.
Holes in sheet-steel piling are not as easily repaired by welding. Local holes can be repaired by welding on plates or sections of sheet-steel piling, but a number of such holes along the length of a bulkhead would make it cost prohibitive. To patch these holes, plates would have to be carried to solid steel well above and below the accelerated corrosion zones, and would have to be welded to the heavy interlock sections. Such a repair system would be very expensive on a badly deteriorated sheet-steel bulkhead.
Repair with Concrete
If a deteriorated sheet-steel bulkhead still has adequate strength to support applied loads below specific sections, concrete encasement down to that section can be used to prevent further deterioration.
Depending upon the relative severity of corrosion attack on the inside and outside face, a steel piling wall concrete encasement may be extended to cover both faces. Concrete protection of both faces is expensive, mostly because of the additional excavation and material costs.
Since corrosion rates generally fall off rapidly below the active electrolytic zone – the area of the bulkhead just below the mean water line that typically is experiencing the most active corrosion — the concrete encasement technically needs to be carried down only a few feet below this area.
If abrasion or corrosion of the balance of the submerged sheet piling is unusually severe, the concrete encasement can be extended to the mudline.
New Facing Using FRP
One technique for preventing further deterioration of a steel sheet pile bulkhead is to place a new structure between the bulkhead and the sea water. A new facing resistant to the marine environment can be placed in front of the original bulkhead and inert fill inserted between the two.
If the fill material halts further sea water contact with the bulkhead – essentially by bonding tightly to the steel surface — the remaining structural integrity of the bulkhead will be maintained and further corrosion is nearly stopped.
As long as the original bulkhead system retains structural stability, the new FRP face encasements require only enough strength to retain the fill material between the bulkhead and the new facing. Therefore, a material like Fiber Reinforced Polymer, which is stronger, more corrosion resistant, lighter in weight and less expensive than steel sheet pile, is the best choice for this repair technique.
Again, the material used must be resistant to the erosive action of the waves and corrosive action of the sea water. The material used to fill in the annular space between the new FRP facing and the deteriorating bulkhead wall needs to be an inert filler capable of bonding to the face of the steel and resisting the compressive stresses imposed by static water head and wave action. It would also need to be stable in a marine environment, resistant to attack from sea water and marine organisms.
Considerations Before Repairs
If the bulkhead structure has deteriorated to the point where it is necessary to do major repair work, an overall review of the installation is required. It may be advisable to update the structure according to more modern design standards in the course of repair.
Future maintenance and repairs can be reduced by revising the original design to incorporate new, longer-lasting and corrosive resistant materials that were not available at the time of original construction.
Another consideration for any repair operations deployed is the necessity of carrying them out with minimal interruption of service or hampering of operations of adjacent facilities. These requirements should be taken into consideration during the repair planning stages, since any special techniques such as the construction of coffer dams or removal of existing marine craft or equipment that would result in construction delays can add substantially to the cost of a repair operation.
Environmental analysis will be required in almost every case, not only for impacts to the water quality, marine plants and animals, but the human environment near the project location. Included also is weather induced events such as periodic floods, ice accumulation, hurricanes, effects of climate change and so forth.
Conclusion
When strengthening or otherwise repairing an existing structure to extend its useful lifetime, ingenuity should be applied to get the maximum benefit from the existing structure.
Leveraging the optimal use of the existing structure is particularly important in large-scale projects, where one repair technique is chosen then applied repetitively. If the structure has many years of unaddressed deterioration, the remaining stability of a bulkhead may be due to mechanisms other than those supplied in the original design.
A detailed examination of existing construction should be included before any repair application is deployed, and the existing structure should not be disturbed until it has been thoroughly checked for long-term stability. Such a detailed check is necessary before any corrective repair can be designed.
Why is assessing the condition of sheet pile structures important before choosing a repair method?
Assessing the condition is crucial to understand factors like topography, soil properties, exposure, and prior maintenance, ensuring the chosen repair method addresses specific structural needs.
What are the advantages of using steel sheet piles for bulkheads, and how can corrosion issues be mitigated?
Steel sheet piles offer advantages like easy installation, suitability for various soil types, and interlocking features, but corrosion in marine environments can be mitigated through protective coatings like bitumen or concrete encasement.