Selecting the Right Weight-Handling Equipment for the Job
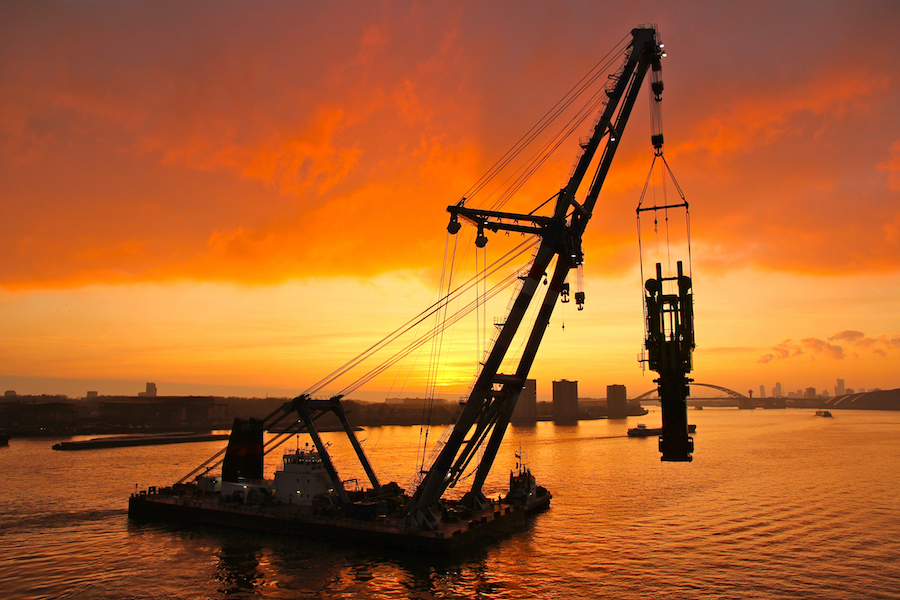
When operating cranes and other weight-handling equipment the potential for property damage or serious injury always lingers.
If a specific job is being conducted with improper equipment or without a crucial accessory the likelihood of property loss or bodily harm to workers is magnified. To avoid such a situation, a working knowledge of how to correctly select new equipment is necessary.
General Selection Factors
Deciding between a rotating or non-rotating machine is the initial step in choosing weight-handling equipment for a given application. This selection is primarily determined through evaluation of the space to be covered by the hook, known as the area of coverage.
In most projects, it is necessary to position the load hook over a spot within a sizable area, with mechanisms added to the basic hoist to accomplish this task. The greater the area to be covered and the greater the flexibility, accuracy, and speed with which this positioning must be accomplished, the more complex and costly the equipment becomes.
Typically, traveling rotating cranes have a decided advantage over non-rotating machines when it comes to potential area of coverage. Rotating cranes can essentially go anywhere if enough track or pavement is available, or the area’s terrain is not too rough. On the other hand, non-rotating cranes are limited to fixed runs of track.
Choosing between the two general types of weight-lifting machines is primarily based on area of coverage, yet consideration of height limitations, capacity and reach, and tail swing also hold importance.
Height Limitations
Non-rotating cranes must clear the top of a load to be lifted and all neighboring obstructions making them most useful in lumber yards or shops, where the height to be cleared is nominal to moderate. In these facilities, straddle carriers and overhead traveling cranes are commonly utilized.
When servicing a ship, the clearance under the bridge required to clear the masts is often more than 200 feet (61 meters). In these situations, rotating cranes equipped for luffing are frequently utilized rather than gantry or overhead traveling cranes, as a lift of that height is unusual for the latter machines.
Capacity and Reach
Consideration of the weights to be lifted and an individual crane’s reach often dictate the appropriate machine to utilize. Reach is dependent on the layout of a facility, clearances, size of a load to be handled, height of boom hinge pins and other variables.
Ideally, a crane’s hook should reach the farthest limits to be served, dubbed maximum reach. A machine’s minimum reach must be as small as possible, with the closest reach position of the hook of most importance on fixed cranes and derricks.
Generally, rotating cranes with a capacity exceeding 150 to 200 tons and a reach up to 200 feet are unusual; whereas gantry cranes with a 600- to 800-ton rated capacity and a reach exceeding 600 feet are becoming more common for use.
Tail Swing
In situations where tail swing is restricted, like inside a building, rotating cranes are not a suitable option, unless the mast can be supported top and bottom, or cantilevered. Normally, without the aid of a counterweight, the capacity of a rotating crane is limited.
Instead, overhead traveling cranes are the typical choice for relatively large areas of coverage inside a building, where columns and framing provide the basic layout for the runway and spans are short.
Rotating Crane Considerations
Overall, rotating cranes are the preferred machine type for most lifting operations. When determining the type of rotating crane to utilize for a job many factors must be considered.
Travel Speed
The speed of mobile, traveling tower, traveling hammerhead, portal and gantry cranes that travel on pavement or rails at ground level is generally limited to a brisk walking pace. For safety reasons these pieces of equipment are preceded by a trackwatcher that walks ahead of a crane to ensure that the path of travel is clear with switches in correct positions.
When fast travel speeds are required, an overhead traveling crane mounted on a high structure, clear of the lower work area, are recommended.
Transfer Speed
When loading or offloading cargo or bulk materials at a fast speed, while in a temporarily fixed location, a crane with a fixed boom and a high-speed trolley or a luffing crane is effective.
Ability to Travel with Load
Not all traveling cranes are equally capable of traveling with a load. Overhead traveling and gantry cranes, traveling portals and traveling hammerheads are designed to travel with the rated load suspended from the hook – one of the most valuable characteristics of these types of equipment.
Truck and crawler cranes can only travel with very light suspended loads, as they are intended to work with outriggers down, which reduces these cranes’ capacity in transit. Several devices, extensible side frames and rolling outriggers, exist that improve the transit capacity of mobile cranes. Use of either device increases the cost of equipment and reduces a crane’s mobility.
Cost of Collateral Facilities
The cost of trackage, track foundations, grading and paving, reinforcement of travel paths and runway structures must be factored into the procure of new equipment for a specific job. Operating and maintenance costs must also be considered, as it is not unusual for the cost of collateral facilities to account for a large portion of a crane’s cost.
Available Power Supply
Some weight-handling equipment, including truck, crawler, portal and locomotive cranes, feature self-contained power supplies fueled by gasoline or diesel engines. These cranes can operate independent of a central power source and are required in situations where furnishing outside power is impractical or the cost to connect to a central supply is excessively pricey.
These types of equipment are often utilized for outside work, as they prevent accidental contact with the conductor. Indoors, overhead traveling cranes are a popular selection when a source of power is readily available and conductors don’t need protection from the elements.
Rotating Crane Equipment
While a vast amount of equipment can be utilized with rotating cranes, selecting between fixed and traveling equipment, along with a luffing boom or fixed boom with a trolley, are basic considerations.
Fixed vs. Traveling Equipment
When feasible to use fixed equipment, based on the area of coverage, the cost is less than a machine of similar capacity, reach and lift. Usually, fixed equipment is used where the work involves a high-duty cycle in a localized area. When checking the feasibility of fixed equipment, it is pertinent to consider the possibility of bringing the loads to the weight-handling device. Hammerhead and tower cranes equipped with fixed equipment are widely used in the erection of concrete buildings, with fixed hammerhead cranes tasked with servicing a plate or storage yard.
Traveling equipment is widely used in situations where future change of crane use is anticipated and there exists heavy traffic around the base of the machine. Because these machines and their main components must be frequently tested, it is recommended to move the equipment out of the way, with another crane brought in during out-of-service periods.
Additionally, when heavy lifts are required, a traveling machine of lighter capacity should be considered and coupled with another machine, making the lift in lieu of a fixed machine of greater capacity.
Luffing and Trolleying
Deciding whether to utilize a luffing boom or a fixed boom with a trolley is based on the need to clear obstructions when positioning the load, along with other considerations.
A crane with a fixed boom and trolley, a hammerhead crane, is typically required to clear the highest obstruction in, or neighboring, the area to be serviced to minimize the possibility of accidents. If notable obstructions are present, the height of the tower for a crane with a fixed boom will be greater than that for a crane equipped for luffing. Because this extra tower height is an item of added expense, it must be weighed against the cost of the luffing mechanism, which includes the hoist, ropes and sheaves, to determine what boom type is most cost effective for a project.
A hammerhead crane typically allows an operator better visibility than a luffing crane, unless an elevated operator’s cab is provided. However, a crane fitted for trolleying generally will have a larger wind presentment, meaning greater sensitivity and sway in a high wind, which influences control of the load.
A luffing machine is more versatile in situations where the required number of lifts per shift is low to moderate, while fixed boom machines operate more efficiently when transferring numerous lifts between two fixed locations.
Operating Fixtures
Various weight-handling equipment may be equipped with several other boom types, along with additional hooks, limit switches and devices depending on the requirements of a proposed application.
Booms
Hydraulic telescoping booms, demountable boom extensions and gooseneck booms may be selected for a crane if the requirements of a job dictate their use.
Demountable boom extensions are typically utilized for light lifts at long or high reach, while gooseneck booms may be used when a straight boom would result in unacceptable interference – either with a wide load, close in or with some obstruction.
Hooks
In addition to the main hook, a crane may be equipped with auxiliary hooks or whip hooks. Auxiliary hooks aid in making lifts of intermediate weight at faster speed, with whip hooks utilized for making lifts of light to intermediate weight at fast speed.
Usage of more hooks reduces the floor coverage for any one hook and increases the weight on the boom and the machine. Additionally, more hooks also translate to increased maintenance, power requirements, machinery and ultimately higher costs. That being said, it is less costly to increase hoisting speed by use of proper controls and hoist motor than by providing extra hooks.
Limit Switches
Important to hook travel, limit switches are desirable features on any crane of derrick. Upper limit switches allow a safe margin against contact of upper and lower blocks to be maintained when a hook handles a load at the required elevation, ensuring a vertical clearance of a foot or more is maintained.
Utilized when working with ships, drydocks, pits and excavations, lower limit switches ensure that no less than two dead wraps remain on the drum of any hoist at the lower limit of hook travel.
Signal, Communication and Safety Devices
Depending on the situation, cranes can be equipped with many devices that allow for safe lifting operations. All cranes must feature some type of device that indicates to the operator when the machine is working near its safe load capacity. Additionally, all cranes handling critical materials must be equipped with a device that stops and holds the motion of the machine should the operator become incapacitated, dubbed a dead-man safety device.
Telephone or radio communication from the operator to a station at ground level is common, namely when work involves a complex series of steps or movements.
For traveling portal, tower and gantry cranes audible warning devices are typically provided at ground level to clear a travel path. Truck or locomotive cranes are equipped with simple, yet rugged, horns, bells, or other devices that will receive continuing usage. Audible devices can also be provided in the operator’s cab to warn of intruders or problems in the machinery room. Where applicable, warning lights can be provided in lieu of audible devices.
Floodlights are often needed at the boom tip and for under-portal lighting for external illumination and night work. Emergency lighting is also necessary for access or egress in a situation where the main lighting power is off.
A Foundation for Successful Handling
Proper selection of weight-handling equipment and lift-related accessories is an in-depth process that requires many considerations on the part of a contractor or agency. For these groups, a thorough understanding of various rotating cranes’ capabilities must be combined with a detailed analysis of a job site and procedures to be conducted to ensure the correct machine is procured. Put directly, the accurate selection of equipment lays the initial groundwork for what should be safe and effective lifting operations within varying environments.
How do I choose between rotating and non-rotating weight-handling equipment for my construction project?
The choice depends on factors like area coverage, height limitations, capacity, reach, and tail swing, with rotating cranes often having advantages in versatility and coverage.
What factors should be considered when selecting weight-handling equipment for lifting operations?
Considerations include height limitations, capacity and reach requirements, tail swing restrictions, travel speed, transfer speed, ability to travel with a load, cost of collateral facilities, available power supply, and the type of equipment, such as fixed or traveling cranes, luffing or trolleying booms, hooks, limit switches, and additional safety devices based on the specific needs of the job.