Chapter 5 – Installation of Driven Piles
For a complete version of this document click here.
Few fields of construction can generate more unpleasant surprises than the installation of deep foundations in general and pile foundations in particular. These “unpleasant surprises” can result in lost time and money; they can and have broken contractors and suppliers and put owners in untenable situations. Fortunately, most of these problems can be avoided with proper planning, contingency provisions and competent, experienced personnel on site.
5.1. Before The Project: Bidding, Specifications and Estimating
5.1.1. Specifications
For any project in which there is an interest, obtain the plans as soon as they are available and review them promptly. This will give an idea of what is to be done and the crews and equipment needed. Consideration can be given to what people and machines may be available when the project must start. It can be determined if a firm may be in a competitive position. Sometimes it may be desirable to fully estimate and price a project it is not practical to bid to keep abreast of the market.
Bid documents can be improved; any contractor’s estimator, field engineer or lawyer will gladly confirm this, as will the engineer or owner’s field forces. Even the specification writer might be enthusiastic about an opportunity to do a better job.
Encouragement for cooperation among all concerned parties can help. Specification writers can get help from their own field forces who have had to work with their previous documents. Contact should be established early with the field supervisor; he can be asked to mark up a set of project documents for return to the specification writers. Contractors and engineer/estimators will usually be pleased to review proposed materials and discuss on a friendly basis what can be done to minimize problems. Competent contractors are willing to take the time for this as a contribution to reducing cost of construction and obtaining early knowledge of a project.
Many times change of a phrase or suggestion of a different item can avoid problems for the project and save money for the owner. Often on foundation work, a review of the borings and draft specifications by an experienced pile person can result in improved requirements or elimination of expensive and unnecessary stipulations. If later change orders, with their attendant paperwork, can be avoided, all parties have more time for other activities.
A foundation project of any magnitude should have specifications specially written by a person with technical knowledge of the foundation problems of the project. Too often specifications are assembled by cutting sections from previous documents and pasting them into a mixed assembly that just invites misunderstanding and litigation. If a foundations specialist and field person cannot be assigned to help with the writing, they should review the draft documents – with definite instructions to be critical and to make suggestions. Of course, final arrangements should be made by the professional specifications writer.1
5.1.1.1. Supply All Information
Place borings in the bid documents. Reference where and how the geotechnical report can be reviewed. Soil and rock samples can be included if available. All known information pertaining to a construction site should be made available to bidders. Courts have held that information either an owner or the engineer has or should have had about subsurface conditions is pertinent to a contract. Not supplying all available information can be a basis for a claim. If a project presents difficult site conditions for pile installation (such as boulders), say so in the bid documents. If all parties are aware of difficulties, the project should be staffed and equipped for it. Instead of an adversary relationship, the field forces will work together to meet problems. Courts may consider such warnings in case of litigation.
5.1.1.2. Changed Conditions
A changed conditions clause in a contract can be helpful to the contractor and save money for the owner. With such a clause, an estimator can minimize the contingency reserve. If there is no problem, the owner saves. If there is a problem without a change of conditions clause, the contractor will file a claim. Litigation is an expensive and lengthy process whose only real victors are usually the attorneys.
A changed conditions clause suggested by the Association of Soil and Foundations Engineers follows:
Subsurface Conditions Clause
The owner has had a subsurface investigation performed by a foundation consultant, the results of which are contained in the consultant’s report. The consultant’s report presents his or her conclusions on the subsurface conditions based on his or her interpretation of the data obtained in the investigation. The contractor acknowledges that he has reviewed the consultant’s report and any addenda thereto and that his or her bid for earthwork operations is based on the subsurface conditions, as described in that report. It is recognized that a subsurface investigation may not disclose all conditions as they actually exist and further, conditions may change, particularly ground water conditions, between the time of a subsurface investigation and the time of earthwork operations. In recognition of these facts, this clause is entered in the contract to provide a means of equitable additional compensation for the contractor if adverse unanticipated conditions are encountered and to provide a means of rebate to the owner if the conditions are more favorable than anticipated.
At any point in time during earthwork operations that the contractor encounters conditions that are different from those anticipated by the foundation consultant’s report, he shall immediately (within 24 hours) bring this fact to the owner’s attention. If the owner’s representative on the construction site observes subsurface conditions that are different from those anticipated by the foundation consultant’s report, he shall immediately (within 24 hours) bring this fact to the contractor’s attention. Once a fact of unanticipated conditions has been brought to the attention of either the owner or the contractor, and the consultant has concurred, immediate negotiations should be undertaken between the owner and the contractor to arrive at a change in contract price for additional work or reduction in work because of the unanticipated conditions. The contractor agrees that the (following) unit prices would apply for additional or reduced work under the contract.
5.1.2. Pay Schedules and Assigned Risk
An equitable schedule of payment for piling can result in the best overall price to the owner and minimize adversary developments. Money, of course, is the problem. Specification writers and designers should understand that there is a substantial difference in conditions where piles are known to drive easily and uniformly and where obstructions may be encountered. The cost of splicing also can vary enormously. Provision for equitable pay will bring the best bid price.
Most specifications state that the contractor must take all the risk. However, he does not; he puts in as much contingency as he thinks the project will stand and hopes for the best. If trouble develops, he can ask for relief.
Specifications may state, for example, that if toe protection is needed the contractor will supply and use them at no increase in the contract price. This is unfair to the contractor and actually specifies controversy on the project. The owner selected the land, with its obstructions. The engineer has had weeks or months to study borings and obtain additional data if needed. The contractor has the plans for a relatively short time, usually with little opportunity for additional investigation. Besides, it would be wastefully expensive if each bidder made a separate subsurface investigation.
5.1.3. Mobilization
For foundation work, a separate bid item for mobilization of equipment should be used. Mobilization is put into the bid as one lump sum item. Then, if quantities of excavation and length of piles vary, the usual inequities of changed quantities are minimized. If a Mobilization item is not used, the contractor is likely to “load” the items on which he can get the earliest return, that is, excavation and piling. These are also the items most likely to vary in quantity. If a high unit price is assigned to piling bid on a per foot of length and quantities increase, the contractor makes a windfall profit. If piling is short, the contractor gets much less return to apply to bringing in the equipment required for pile installation. He will immediately ask for renegotiation of a changed condition. Most specifications have an automatic renegotiation clause for a 15% quantity change.
5.1.4. Prompt Payment
Provide in the bid document for prompt partial and final payment. On large projects, partial payment for materials on hand should be helpful. Such provisions indicate an awareness of contractor’s needs and financing problems. The owner probably obtains financing at much lower rates than the contractor so the project should be bid at a lower overall cost to the owner.
5.1.5. Negotiating as a Pile Subcontractor
Several items require consideration and discussion in developing a subcontract for pile installation: time to start and complete a project; space for pile storage and an office; labor arrangements should be compatible; excavation for pile caps-if done by others-to be such that pile equipment can move where required; who provides security for the subcontractor’s equipment and for driven piles. Most of these items, and many more, are covered in standard forms of subcontracts.
Be sure to have an understanding with the owner’s comptroller that what is promised should be done. Arrange in advance for the mechanics of preparing, routing and processing the estimates. Having money for payroll and for taking discounts on invoices makes a big difference in a contractor’s financing and his or her attitude toward the project.
5.1.6. Estimating
“Do it yourself” is the best way to estimate, plan and bid a project. There are competent quantity take-off organizations that will provide accurate quantities, but not full knowledge about the project. If a firm gets the work, its personnel then have to go through this carefully. The commercial take-off quantities can be invaluable as a check on materials needed-and sometimes a reminder of an item that may have been missed. However, such firms are fallible.
Read the entire specification; make marginal notes and dog-ear or paper clip pages for restudy and perhaps discussion with associates. Don’t take anything for granted.
While taking off quantities, planning the project can be done: How many drivers should be needed? What hammers will probably be most effective? Will fixed or hanging leads be most suitable? Most important, how many working shifts should be required?
For foundation work, examine the borings. For all projects, review all subsurface investigation reports. A prospective bidder is entitled to all subsurface information that is known to exist.
5.1.7. Noise, Neighbors, Workers and OSHA
Excavators and pile drivers are the first on a project. They are likely to feel the full thrust of environmental enthusiasts’ activities. It is good business to investigate the existing regulations and potential for increased control of noise and air pollution at any site where construction is planned.
Pile driving is accompanied to varying extent by noise generation. Noise levels at 23’ (7m) are typically 90-115 dBA for impact hammers and 70-90 dBA for vibratory ones. Moreover, one can expect at the same distance 100 dBA from the crawler crane and 85 dBA from the air compressor; however, the impulsive noise of an impact hammer is more disturbing that the steady noise of, say, the air compressor. If the pile project is in an area where pile-driving noise may annoy the neighbors, special record keeping and precautions may be in order. Additionally, OSHA (Occupational Safety and Health Administration) has very stringent rules on protecting the hearing of workers on construction and industrial projects. Air pollution from equipment emission and from job dust and debris also is a problem.
Noise from construction is being severely limited to not more than 85 dbA at 50’ (15 m) from the machines. Compressors for use with steam/air hammers have achieved this and lower. One method that can be used with air/steam hammers to mitigate the noise is an exhaust muffler. An example of this is shown in Figure 5-1. Steel piles, where exposed for some length above the ground, have a loud metallic ring when struck with a hammer. Enclosing hammers – or at least the impact area and pile, as shown in Figure 5-2 – in acoustically lined shrouds helps.

5.1.8. Considerations Due to Pile Driving Induced Vibrations
Since impact or vibratory hammers drive piles, ground vibrations of some magnitude are almost always induced into the surrounding soils during pile installation. Damage to nearby structures can result from vibration induced soil settlements or from the effects of vibrations on the structure itself. If a sensitive existing structure is located within approximately 150 meters of the pile driving location, vibrations or vibration induced soil densification may result in settlement damage to the existing structure.
In many highway projects, vibrations are of limited concern, as surrounding structures are often greater than 150 meters from the location of pile driving.
For projects in urban areas, and for widening of existing bridges, the proximity of existing structures is often within the zone of potential damage. Careful evaluation of the pile driving procedures and/or monitoring of ground vibrations during pile installations should be performed for these projects. Wiss2, reported “safe” levels of ground vibration have typically been recommended between 12 and 100 mm per second. Lacy and Gould3 found that vibration induced soil densification settlements and structural damage can occur at peak particle velocities much less than 50 mm per second and that soil gradation is an important factor in this phenomenon. For a specific project, the ground vibration level where structural damage may occur will be dependent upon the type of soils, pile type(s), pile hammer, pile installation techniques, as well as the condition and type of existing structure.
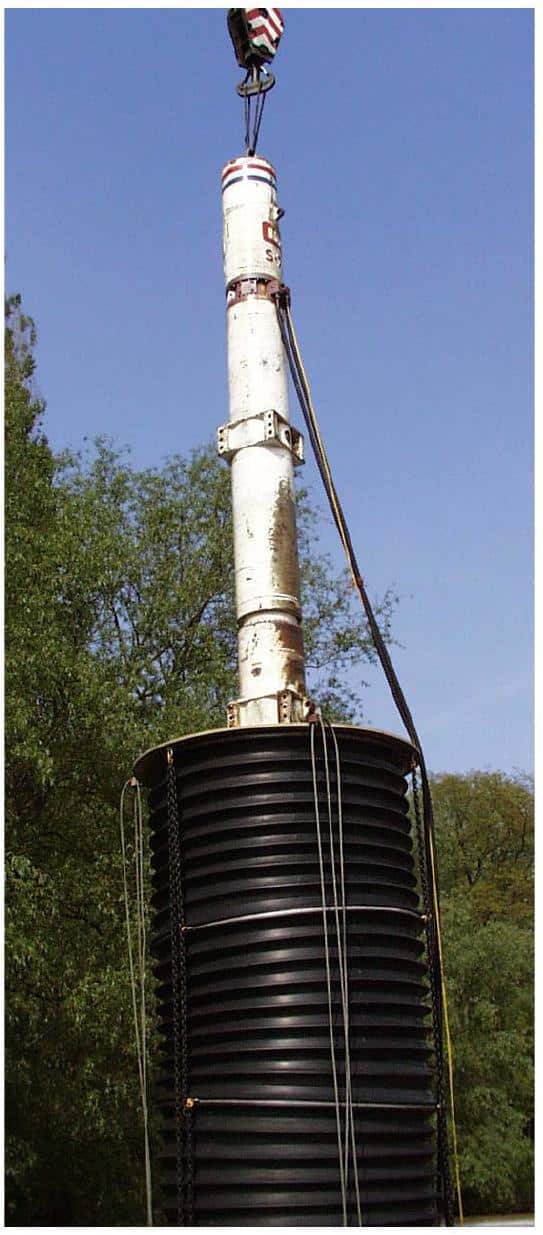
If the potential for damaging ground vibrations is high, pile installation techniques should be specified to reduce vibration levels. Specifications could require predrilling or jetting as well as use of a different pile type or use of a specific type of pile hammer. Since predrilling and jetting influence compression, uplift, and lateral pile capacities, a determination of probable vibration levels and remediation measures should be evaluated in the design stage. A case history illustrating how a change in pile installation procedures reduced vibration induced densification and off-site settlement damage was reported by Lukas and Gill4.
Woods5 provides a synthesis of pile driving induced vibrations and typical mitigation practices. This synthesis noted that vibration problem management is the key to minimizing vibration damage, delays and claims. Two important elements in vibration management are a vibration specification with limits on the maximum peak particle velocity and a predriving survey of surrounding structures. An example vibration specification that details the requirements of a preconstruction survey as well as particle velocity controls is included. The predriving survey needs to document conditions within the potential effected area. Woods reported that vibration damage a distance greater than one pile length away from driving is relatively uncommon but settlement damage in loose clean sands can occur up to 400 meters away. Woods also concluded that piles with low impedances, EA/c, tend to transmit the hammer energy to the soils along the pile shaft and thus increase ground vibrations, whereas piles with higher impedances tend to more effectively transmit the hammer energy to the pile toe resulting in lower ground vibration levels. Hence, selection of a stiffer pile section at sites where vibrations are a concern may reduce vibration problems.
5.2. Planning and Project Organization
A good start is one of the best ways to achieve a successful completion. The contractor must know what he or she is required to do, how he or she is going to do it and be prepared to cope with difficulties that bound to arise.
Pre-project planning should be as detailed as time permits. Unfortunately, the contractor may not have time to plan as thoroughly as his or her judgment indicates. Even the simplest project should have every point covered in this section considered.
With a quantity estimate and a general idea of the project, a visit to the site to study of field conditions is next in order. Experienced field forces can be most helpful in planning the project. If an engineer and superintendent who may get the project assignment can assist with the estimating, it will bring practical input. They can suggest the optimum work force and outline the equipment most suitable for the project. Just as important, the field supervisors will then have an added responsibility to make their ideas work and understand why some were not used. They should be part of the team from the start.
5.2.1. Study the Project
The superintendent should receive both a written and an oral briefing on the project scope and be given copies of the following documents:
1. Contract
2. Specifications
3. Plans and Borings
4. Estimate and estimate work sheets
5. Project Data or Information Sheet
6. Method of Pricing; Results hoped for by Estimator
7. Copies of orders, shipping documents, etc.
8. Set of forms
9. Insurance Certificates and Safety Information
All of these items should be reviewed completely and the parts applicable to contracted work studied in detail, before starting. Items 4 and 6 should be treated as confidential and not left lying around the project office or easily accessible in the computer.
5.2.1.1. Contract
The contract with the client outlines what the contractor must do or not do and how it should be paid for its work. Be sure the superintendent understands:
1. Scope of the work; number of piles and base length or aggregate footage; any variations between estimated quantities and bid quantities.
2. Other items of work, such as test piles, load tests or reinforcing.
3. Method of payment for various items of work.
4. Provisions for payment for longer or shorter piles.
5. Time of starting and completion; specified progress, if any; penalty clauses.
6. Provisions concerning order in which project is to be done, if any exist.
7. Any delays anticipated and provisions in the contract for the reimbursement for them.
8. Who is responsible for grading, excavations, sheeting and bracing removal of pre-excavated or heaved material (if contemplated), pumping and drainage and protection of adjacent structures, provision for payment for piles driven through overburden and who cuts off piles after excavation.
9. Responsibility for permits, access and ramps, maintenance of access roads for rig and material trucks, provision of storage for shells and pile materials, sites for offices, parking and tool houses, and utilities.
10. Provisions for removal of overhead, lateral or underground obstructions, payment for delays if not done in advance, acceptance of piles hitting obstructions, responsibility for footing redesign and replacement or additional piles.
11. Responsibility for furnishing boiler, compressor, drilling or jetting water.
12. Responsibility for staking out piles, maintaining stakes and giving cut-off grades for each pile, logging piles and making “as built” survey and drawings.
13. Special provisions for furnishing other services or materials, such as reinforcing steel.
14. Provisions covering extra work or countercharges by either party.
15. Inspection and tests; who performs and who pays for these services.
As the superintendent studies the contract, he or she should make notes about anything that is not clear or which he or she thinks will cause a problem. He or she will then be able to discuss it with his or her superior(s) before the work is started.
5.2.1.2. Specifications
Specifications are usually part of the contract by reference. Specifications should be read and understood. Are piles to be driven to resistance only, or is a specified bearing stratum to be reached? Is a minimum penetration (tip elevation or penetration into bearing stratum) required? What alternatives are permitted? What is the intended function of the piles (resistance to downward load; resistance to lateral load, resistance to uplift, compaction of soil, etc.)? Project specifications should present this information. Study the table of contents and check the sections that apply to your work, such as:
1) General Conditions
a) Authority of architect or engineer to amend specifications (usually only in writing).
b) Notice required to be given on discovery of errors or omissions in plans or specifications, unforeseen soil conditions, etc., to whom, when and how.
c) Provisions regarding delays and extra work and procedures to be followed before payment (such as having orders in writing).
d) Requirements concerning interruptions to nearby operations – railroad tracks, power lines, production lines, etc.
e) Safety restrictions, noise limitations, limitation on open flames, permits required for welding and cutting. Etc.
f) Description of special hazards, underground hazards, buried cables, gas mains, etc.
g) Right of owner or contractor to suspend work.
h) Equal Opportunity requirements.
i) Payroll submittal requirements.
2) Piling Specifications
a) Driving criteria and size of hammer to be used.
b) Minimum pile length, specified toe elevation or minimum penetration into bearing stratum, if any; alternatives if these cannot be reached without excessive driving.
c) Pile type, minimum head, toe, or average diameter.
d) Hammer cushion specification or limitation.
e) Provisions or limitations on jetting, spudding or pre-excavation.
f) Driving tolerances as to plumbness, location, or curvature.
g) Procedures to be followed if pile hits obstruction.
h) Concrete placing, concreting radius, dewatering requirements.
i) Pile capacity testing criteria
j) Test pile specifications; number, location, driving criteria, cutting off, concreting, etc.
k) How load tests, if any, are to be conducted; can driving be continued during load testing?
3) Material Specifications
a) In addition to driving specifications, material requirements pertaining to the specific types of material you are supplying should be reviewed6:
b) Concrete materials; mix design and approval; strength requirements.
c) Precast piles, design and fabrication
d) Reinforcing steel and placing reinforcing steel or dowels.
e) Structural steel for H-pile piles; pipe for piles; sleeves and plates; splicing or welding.
f) Structural timber; wood piles; treatment; handling; shoes or caps.
g) Tests of materials and reports to be furnished; concrete test cylinders, mill certificates for H-pile and pipe piles and inspection reports on precast and wood piles.
4) Plans and Borings
a) Review general plan to determine overall scope of project; review notes.
b) Review sheet or sheets covering foundation or piling layout and carefully read all notes.
c) Study foundation detail drawings:
i) Check notes; check dimensions on piling sketches
ii) Study pier layouts and pile spacing
iii) Be alert for isolated piles or piles with unusually high or low cut-off
iv) Note pile cut-off elevations and where you may have to drive through overburden or in deep excavations
v) Study plans, notes and symbols looking for batter piles.
vi) Count number of piles of each type or length and check with contract and estimate; if difference exists count again, being sure you find isolated piles, resolve differences.
vii) Plot location of borings on pile plan to scale and note boring numbers.
viii) Indicate on boring logs the average cut-off elevation in area of the boring.
ix) Indicate on boring logs probable pile toe locations, based on requirement of specifications and your experience.
x) Note the excavation needed at various locations with relation to existing grade or street level and pile cut-off elevation.
xi) Compare your probable pile lengths with those anticipated by the estimator.
xii) Estimate sheet gauges required and compare with those estimated and on initial order, if any.
xiii) Make note of all items you want to discuss with your superior.
5.2.1.3. Estimate and Data Sheet
Review the schedules of the estimate and project data sheet with particular reference to:
1. Number, type, loading, length of piles.
2. Driving progress and planned sequence of driving.
3. Schedule, including allowance for on and off, tests, weather holidays and delays.
4. Shell gauges figured; allowance for shell waste and initial shell order placed.
5. Labor crew and rates.
6. Equipment estimated, equipment planned and its source; allowance for freight and set up.
7. Concrete, re-steel and other pile material required; anticipated sources and orders placed to date.
8. Special insurance requirements or hazards.
9. Compare all the above with contract, plans and specifications and make note of any differences to discuss with general superintendent.
10. Review allowance made in estimate for other items and note any you think you may improve on or may be inadequate and why you think so.
5.2.1.4. Site Visit
A site visit should be made before commitment of equipment and labor. Preferably, both the general superintendent and the Project superintendent should make it together. Specific items that should be covered include:
1. Progress made to date by others, excavations, access roads, etc. and order in which site should be available to us.
2. Access to site; road conditions, truckload limits on bridges, height or width restrictions, etc.
3. Overhead obstructions at or near site which might interfere with setting up or operation driver; power lines, overhead pipelines, etc.
4. Nature and condition of adjacent structures or facilities that might warrant special precautions or observations of possible movement; need for pre-project survey.
5. Nature of nearby buildings; hospitals, instrument factories, etc., that might be affected by noise or vibration of driving.
6. Adjacent or nearby activities that might present unusual fire hazard, extraordinary public liability exposure or danger to the employees or equipment.
7. Stability of the ground for safe movement of rig.
8. Evidence of possible underground facilities such as pipelines, cables or tunnels.
9. Availability of space for setting up equipment, temporary buildings, storage of material, welding yard, etc.
10. Availability of water and other utilities.
11. Determine ability of concrete plant and other local suppliers to meet specifications and delivery requirements.
12. Labor availability.
13. Plans and schedules of the owner, the general contractor and others for doing work related to the contract.
14. Discuss your requirements and plans with local representative of the client.
15. Street address of site and how to reach from nearest main highway and both light and heavy loads.
16. Location and designation of nearest railroad siding and name of railroad, if any shipments may come by rail.
17. Mail address and name of nearest post office; make application for post office box when needed.
18. Telephone number of client or general contractor’s field office; make application for telephone service if so instructed by general superintendent.
Edmund Prentis, a founder of the underpinning and foundation firm of Spencer, White and Prentis, was fond of telling that if a firm he knew had raised all bids ten percent they would have missed the toughest foundation projects and, over the years, made more money. Prentis also tells of being very low on a bid for a foundation project at Columbia University. The estimate had been made several months previously, and then shelved because of postponements. With a new request, the old estimate was dusted off and used. What a then five-cent subway ride would have disclosed was that 30,000 yd3 (23,000 m3) of rock from other excavation had meanwhile been dumped in the area. The moral of this incident is clear: always visit the site and check everything.
If the owner-engineer arranges a prebid conference, be sure to attend-with all the questions developed in estimating and planning. Do not hesitate to suggest an addendum to the specifications if it should be helpful. Nevertheless, remember, all bidders will share your ideas.
5.2.2. Overall Plan
Having studied the project, formulate a plan for doing the work that answers:
1. How can you best approach this project to
minimize costs and maximize profit?
2. What items of equipment should be required?
3. What labor and supervision should be needed?
4. What pile materials need to be ordered?
5. What are the best methods to follow?
6. What progress can you expect?
7. What is the best sequence or schedule for the work?
8. What problems are you likely to encounter and how should you prepare now to cope with them?
9. How can you reduce the risks inherent in the project?
Pile locations should be accurately established by survey and plainly marked ahead of driving. A chart should be prepared identifying each pile by number; this identification system shall be used in making a record of length, final driving resistance, location of the driven pile and any unusual occurrence with its installation.
The best answer to some of these questions may require improvisation or compromise to fit the people, materials and equipment available. Those parts of the plan that affect others will have to be discussed and any differences eliminated. Finally, the superintendent and general superintendent should develop a workable plan, acceptable to everyone.
-
SPW911 Sheet Pile Design Software
Rated 5.00 out of 5$150.00 – $599.99Price range: $150.00 through $599.99 -
Sheet Pile Design (PDF Download)
Rated 5.00 out of 5$89.00 -
Pile Driving (PDF Download) $89.00
-
Marine Construction Volumes 1 & 2 (PDF Download) $157.00
-
Pile Driving (Book) $89.00