Chapter 2 – Pile Types and Guidelines for Selection
For a complete version of this document click here.
Piles can be categorized in two main types: load bearing piles and sheet piles.
There are numerous types of load bearing piles. Figure 2-1 shows a pile classification system based on type of material, configuration, installation technique and equipment used for installation. Load bearing piles can also be classified based on their method of load transfer from the pile to the soil mass. Load transfer can be by friction, toe bearing or a combination.
2.1. Bearing Piles
2.1.1. Steel Piles
The general category of steel piles includes H-piles and pipe piles. Since steel piles are a manufactured product, their properties are controlled and well known prior to installation. Among all piling materials steel piles are allotted the highest allowable unit working stresses, but not necessarily the highest in proportion to the ultimate strength of the material. Steel piles are generally considered to be high capacity piles but have been historically used for a wide range of loadings.
2.1.1.1. Steel H-Piles
Steel H-piles are a specially designed sub-group of wide flange shapes with equal thickness in the web and flanges. The depth of the section is approximately equal to the width. H-piles are hot rolled from ingots on the same type mill used to manufacture wide flange structural shapes. A table of the various sizes commonly available is shown in Table 2-1. Other wide flange shapes have been used for foundation piles in special situations.
H-piles are very versatile pile type. They can be used for both friction and end bearing applications. They are manufactured as a finished product, which can be driven with standard equipment. Advantages and disadvantages of H-Piles are shown in Table 2-2.
H-piles can be considered for a design load between 80 kips (356 kN) and 500 kips (2224 kN). They function most efficiently for end-bearing or partial end-bearing applications. They are a standard in many states for highway bridge piers and abutments where the job sites are remote, compacted fill approach embankments must be penetrated, battered piles are often required and pile loadings are in the medium to high medium range (80 kips (356 kN) to 180 kips (800 kN)).
H-piles are also commonly applied for high unit dead and live loads associated with multi-story buildings. The magnitude of these loads generally requires high capacity piles driven to end-bearing conditions to limit settlements and for space and economic reasons. H-piles have carried design loads of over 400 kips (1779 kN) in a number of such applications.
H-piles are good piles in tension – the constant cross-section together with the entrapment of soil between the flanges provides excellent resistance to pullout when that is a factor. H-piles are used as battered tension piles to anchor sheet pile bulkheads. Uplift due to hydrostatic or wind conditions is an important consideration in many foundation designs, and steel H-piles have the ability to work both as compression and tension piles. Their low-displacement characteristic would favor H-piles over displacement piles where ground heave might be a problem.
The ability to resist hard driving enable H-piles to penetrate soils where other piles may not.
2.1.1.1.1. Grades of Steel H-Piles
Steel H-piles are produced to either ASTM Specification A-36 or A-572. The properties for these specifications (and their grades) are shown in Table 2-3. In addition, they can be produced to ASTM A-690 when specified. This formulation is a 50 ksi (345 MPa) steel with improved corrosion performance in the salt-water splash zone. This grade is occasionally specified as ”weathering” type steel for appearance-sake above ground.
Experience indicates that corrosion is not a practical problem for steel piles driven in natural soil, due primarily to the absence of oxygen in the soil. However, in fill ground at or above the water table, moderate corrosion may occur and protection may be needed. Commonly used protection methods include coatings applied before driving. Coal-tar epoxies, fusion bonded epoxies, metallized aluminum and Phenolic mastics are used to provide protection. Encasement by cast-in-place concrete or precast concrete jackets or cathodic protection can also provide needed protection for piles extending above ground. Sometimes heavier sections are used to meet long-term service requirements.
Splices are commonly made by full penetration butt welds. The splice should be as strong as the pile. Proprietary splicers are also used for quick splicing H-piles.
A steel load transfer cap is not required if the head of the pile is adequately embedded in a concrete cap.
H-piles may require toe reinforcement for driving through dense soil or soil containing boulders or rock. Toe reinforcement is also used for penetration into a sloping rock surface. Proprietary pile points welded to pile toes are used commonly. H-piles are suitable for use as end bearing piles, and combinations of friction and end bearing. Since H-piles generally displace a minimum of material, they can be driven more easily through dense granular layers and very stiff clays. Using H-piles often reduces the problems associated with soil heave and ground vibrations during foundation installation. H-piles can be used for driving into soils containing obstructions such as boulders when properly protected at the toe. They are commonly used for any depth since splicing is relatively easy.
2.1.1.1.2. H-Piles as End-Bearing Piles
H-piles are most efficient when they can be driven to refusal or practical refusal on rock, or into dense materials overlying rock. The pile functions as a short column, hence the rock may be stronger than the steel for the maximum design load that can be applied. It is generally accepted that competent rock in its natural bed can resist very high stress concentrations without crushing, except when the pile is installed through extremely soft soils. This combination therefore provides at least the potential for some high and therefore very efficient pile loadings. Other end-bearing materials include hardpan, marl, dense sand, and softer rock. Here the strength of the supporting material is often considerably less than that of the steel. H-piles driven into these materials obtain support by the development of an increased bulb of pressure around the toe and friction along the embedded development length.
Building codes set limits on loads and unit stresses as well as allowable settlements, which reflect the experience and recommendations of the related engineering community. Piles installed to end bearing are often permitted much higher loads than friction piles and those that are tested are allowed higher loads than those that are not.
Based on recorded experience, H-piles are probably most efficient when driven through relatively deep, soft to medium stiff clays to end bearing.
Fine grained soils (clays) are the most likely to exhibit large increases in capacity after installation. The extent to which soil freeze contributes to capacity of end-bearing piles is subject to much discussion. Soil freeze may be estimated using experience and static methods. With wave equation analysis, incorrect modeling of the setup (freeze) effects may lead to the discrepancies that are observed between estimated and actual driving performance.
2.1.1.1.3. H-Piles as Friction Piles
While many meters of H-piles have been driven for friction applications, they are non-displacement piles and tend to drive further in loose sands and silty sand. There may be good reasons however to select H-piles for this use if, for example, a significant scour depth is computed for a bridge pier abutment.
When H-piles are driven into stiff clays with cohesion between 1 and 2 ksf, soil is usually trapped between the flange and the web and is compacted. In this case, the soil becomes a part of the pile and is carried down with it. An example of this (known as “H-pile plugging”) is shown in Figure 2-2. This core aids in compressing the surrounding soil and building up resistance to further displacement. The principal load transfer is through frictional forces and not from end bearing. It is somewhat difficult to predict the capacity of any given length of pile driven in stiff clays and load testing is generally advisable. When soft or medium clays and silts are encountered, piles will develop shaft friction resistance almost equal to the surface area of the pile multiplied by the shear strength. These soils have high moisture content, which will make the pile resistance to driving seem lower than predicted. A time interval of a few hours to several weeks may be necessary to attain the true measure of the pile’s long term geotechnical capacity.
2.1.1.1.4. H-Piles as Soldier Beams
One common application of H-piles is their use as soldier beams for retaining walls. These retaining walls can be either permanent or temporary for excavations and braced cuts. Typically, the H-piles are driven on 6’ – 8’ (1.8 – 2.4 m) centers in a row with the flanges facing each other. The lagging – either concrete or timber – is then stacked with the ends of the flanges facing the webs. The flanges of the H-piles thus retain the lagging. Cross bracing (in the case of braced cuts) or tieback systems can be used to provide additional lateral support for higher walls or loads.1 H-piles also are used in conjunction with sheeting to form high-modulus walls; these are discussed in detain in the Pile Buck Sheet Piling Design Manual.
2.1.1.2. Steel Pipe Piles
Pipe piles usually consist of seamless, welded or spiral welded steel pipes of wall thickness in the range of 0.109” to 2.500” (2.8 – 63.5 mm). The piles are available in 8” (203.2 mm) to 48” (1219 mm) diameters. Typical pipe pile sizes are shown in Table 2-4. Much larger sizes and also used in special situations.
Common sizes of pipe piles can be considered for loads between 60 kips (267 kN) to over 400 kips (1779 kN). They are very competitive as combination end-bearing/friction piles for loads from 120 kips (534 kN) to 240 kips (1068 kN), driven closed-end and filled with concrete (particularly where pile lengths do not favor mandrel-driven piles.) Pipe also provides a strong casing for concrete fill where underground pressures are high. Pipe piles may be driven with an open end or a closed end.
Advantages and disadvantages of steel pipe pile are shown in Table 2-5.

2.1.1.2.1. Specifications
The basic specification for pipe piles is ASTM A-252, which covers welded and seamless product. There are three grades listed:
• Grade 1 has a minimum yield strength of 30 ksi (207 MPa);
• Grade 2 has a minimum yield of 35 ksi (241 MPa); and
• Grade 3 has a minimum yield of 45 ksi (310 MPa).
There are elongation requirements for ductility, but only minimum chemistry requirements.
2.1.1.2.2. Manufacture
Seamless pipe is rarely specified for pipe piles due to its relative cost. It generally comes on the market as surplus pipe. As the name implies, seamless pipe has no seams but is made in one piece from a hot steel billet by piercing the centre and expanding the steel to the shape and size desired.
Electric weld pipe is the most common type of pipe used for piles. Several manufacturing processes can be used:
• Electric resistance welding
• Fusion welding
• Flash welding.
The seams of these pipes may be straight, spiral-butt or spiral-lap construction. In each case, the manufacturer begins with hot rolled sheets or plates in either coils or flats. The production equipment determines how the pipe is assembled and the seams are welded. So-called “spiral mills” produce spiral pipe by butting or lapping the seams. This process accounts for a large share of the pipe pile produced. Larger and thicker pipe piles are generally made on the same mills which produce large diameter line pipe by the straight seam, electric butt-weld process. In some cases very heavy wall pipe piles are fabricated in specialty shops where penstocks or caissons might be fabricated. There seems to be no particular advantage of one process over the other as far as the pile foundation designer is concerned.
2.1.1.2.3. Closed Ended Pipe Piles
A closed ended pipe pile is shown in Figure 2-3. They may be filled with concrete or left unfilled. They may be filled with a structural shape such as an H-section in addition to the concrete and socketed into bedrock (rock socketed piles). If bearing capacity from the entire pile toe area is required, the pile toe should be closed with a plate or a conical tip. Mandrels are usually not used for driving pipe piles, which are generally driven from the pile head. When the end of a pipe pile is equipped with a closure device, the pile becomes a displacement pile and functions well as a friction pile particularly in loose sands. When driven open or closed end it can also function as a high capacity end-bearing pile.
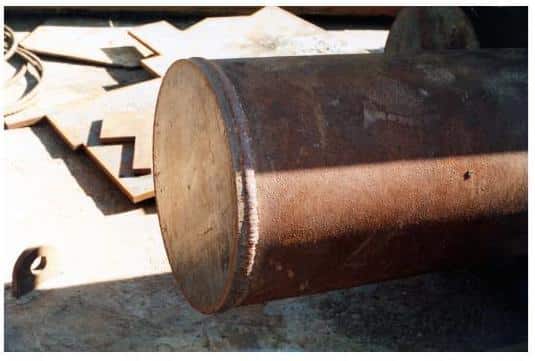
A flat plate of 1/2” to 2” (13-51 mm) thickness, or a conical point generally forms a closed ended pile. When pipe piles are driven to weathered rock or through boulders, a cruciform end plate or a conical point with rounded nose is often used to prevent distortion of the pile toe.
2.1.1.2.4. Open Ended Pipe Piles
Open-ended pipe piles are driven when hard driving, caused by the presence of debris, small boulders and the like is anticipated. The pipe can be fitted with a special driving shoe, which adds steel thickness at the toe to reduce stresses and damage. Periodically, the plugger materials are removed to aid in driving. Open-ended pipe piles may also be partially socketed into rock at site of steeply sloping bedrock or where pile fixity at the toe is a design requirement. Pipe piles driven open-end may be filled with concrete after cleaning out the plug, backfilled with sand, or the plug ignored. In the last two cases, the steel wall takes all stress and the pile would be treated similar to an H-pile for design purposes.
In driving through dense materials, open-ended piles may form soil plugs. The plug may make the pile act like a closed end pile and increase the pile toe bearing capacity significantly. The plug should not be removed unless the pile is to be filled with concrete. For open-ended pipe piles not filled with concrete, the formation of soil plug should not be considered in computing pile end bearing capacity. Behavior of the plug during and after driving is a function of pile size and soil type and consistency. Only preliminary design guidance is available, which should always be confirmed by field observations and measurements.
This type of pile is also common in the installation of offshore oil platforms, whether driven from the surface or underwater. In these applications, they primarily are designed for uplift loads due to wave or wind action on the structure. Unless the pile plug generated during driving creates drivability problems, the plug is generally not removed. An illustration of this application is shown in Figure 2-4.
Open ended pipe piles are recommended where the pile or pile group is to be subjected to horizontal loads and bending moments such as vessel impact and scour on large structures such as bridges. With a constant radius of gyration, pipe piles are also the most efficient columns and should be considered where freestanding columnar strength is important (such as open-platform marine piers and docks). This is advantageous in seismic situations, where liquefaction and several other factors have a strong influence on the design of deep foundations. In all of these applications, the pile size can range up to 3000 mm in diameter. Since such applications can require considerable length, this frequently requires adding-on to pipe piles, which is shown in Figure 2-5.
An example of this kind of application was the Jamuna River Bridge in Bangladesh, built in the mid-1990’s. The river is capable of scouring to a depth of 50 m, with a flood discharge of 100,000 m3/sec. To deal with this, groups of high yield strength piles 2500 – 3150 mm in diameter up to 80 m long with a wall thickness of 45 – 60 mm were installed. After driving, the plug was removed and the toe of the pile was sealed with concrete, then the pile was grouted.
-
SPW911 Sheet Pile Design Software
Rated 5.00 out of 5$150.00 – $599.99Price range: $150.00 through $599.99 -
Sheet Pile Design (PDF Download)
Rated 5.00 out of 5$89.00 -
Pile Driving (PDF Download) $89.00
-
Marine Construction Volumes 1 & 2 (PDF Download) $157.00
-
Pile Driving (Book) $89.00