New McInnis Cement Terminal in the Bronx, NY, Equipped with ShibataFenderTeam Solutions
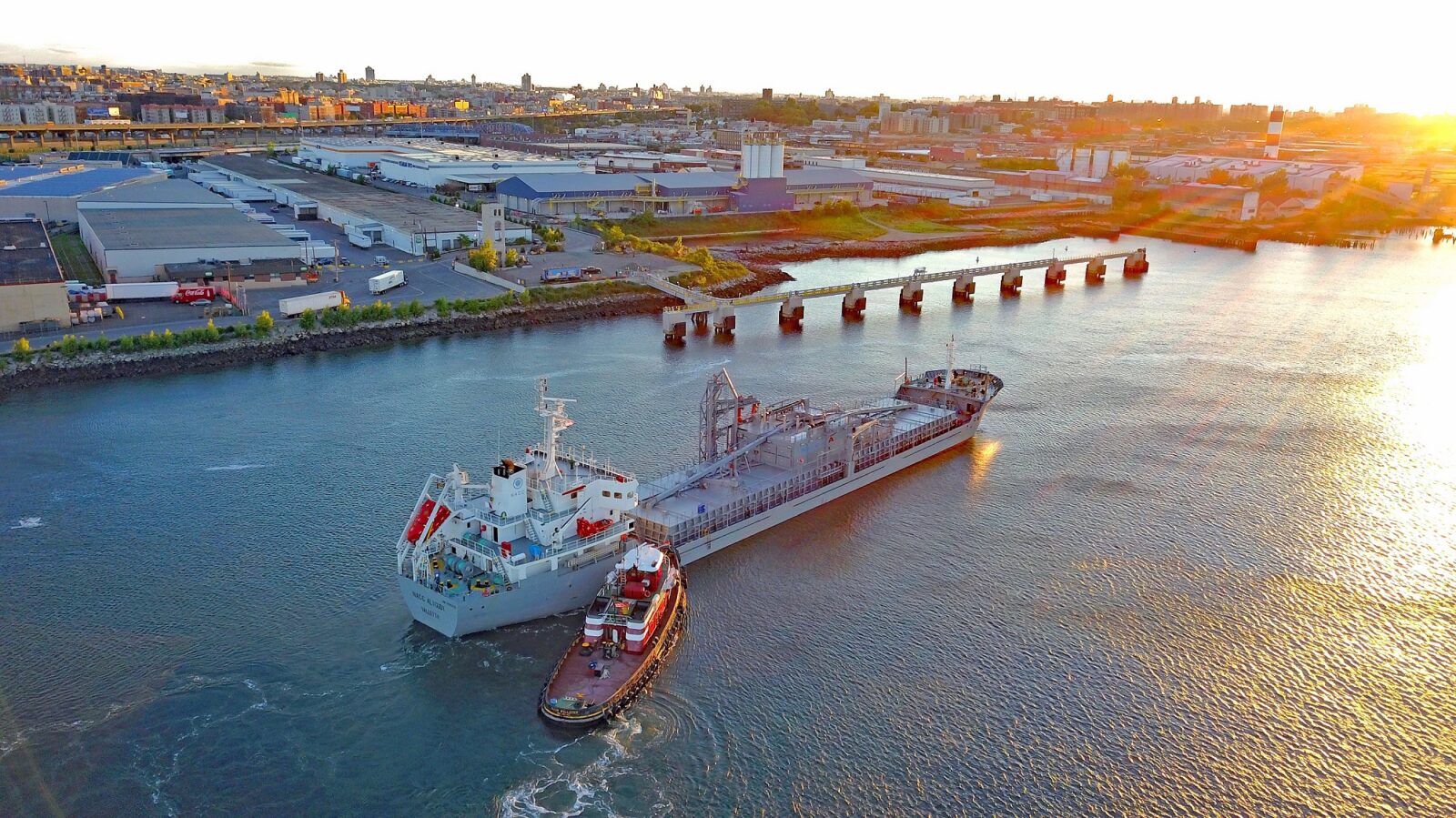
Perfectly located for the storage and distribution of cement in New York City and beyond, the Cement Terminal will allow the McInnis plant to receive 90% of the cement by vessels, significantly reducing the traffic across bridges and roads. The new terminal is part of an industrial operation that seeks to set a new standard in harmonizing the needs of the community, the environment and the industry.
SFT designed and delivered a customized solution consisting of three different fender systems to provide safe berthing at the new facility:
- 10 sets of SPC Cone Fender Systems (1300, G1.5) for large bulk vessels and 1 SPC Cone Fender System (900, G1.0) as barge stop fender
- 1 Donut Fender (13.3 ft diameter x8 ft flat) for a turning dolphin
- 8 sets of quadruple CSS Cell Fender Systems (500, G1.9) for the cement barges
Barge fenders have been designed with special wings to avoid any collision with the mooring lines.
The project scope also included 1 marker Buoy, 18 Single Bitt Bollards and 9 custom-made Pin Bollards, whose design posed an interesting challenge for our in-house team of engineers as the mooring lines needed to be analyzed in great detail. Since the terminal is new, assumptions had to be made based on our engineer’s extensive experience in fender system design.
Special adjustments were as well done for the steel panels on the barge side to allow for different line angles and to avoid any contact between the lines and the fender systems. Furthermore, the U Anchors for the CSS 500 fender systems had to be recessed to avoid any contact between the anchors and the panel when the system is compressed.
Finally, given the size of the materials and the narrow roads in the area, the last mile delivery was challenging. However, a coordinated work between SFT and the contractor ensured we supplied the appropriate fender solution in a short period of time, from summer to winter.
ShibataFenderTeam Group are proud to have accomplished this challenging project developing a customized solution; yet another great example of the SFT holistic approach that considers all the project conditions, along with the fender components and the manufacturing process.