Non-Steel Alternatives for Dewatering, Erosion Control, and Other Marine Applications
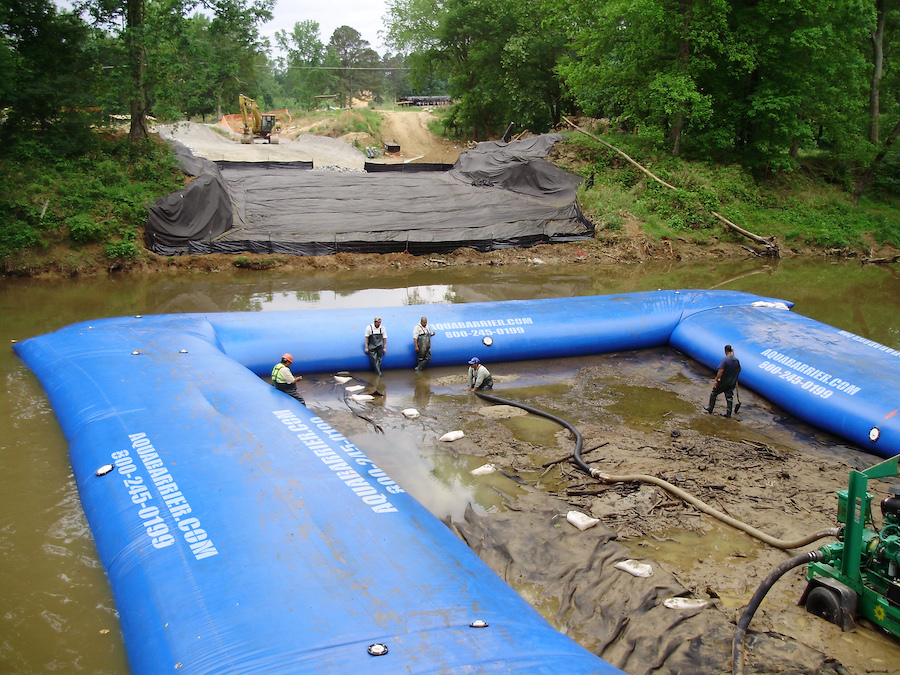
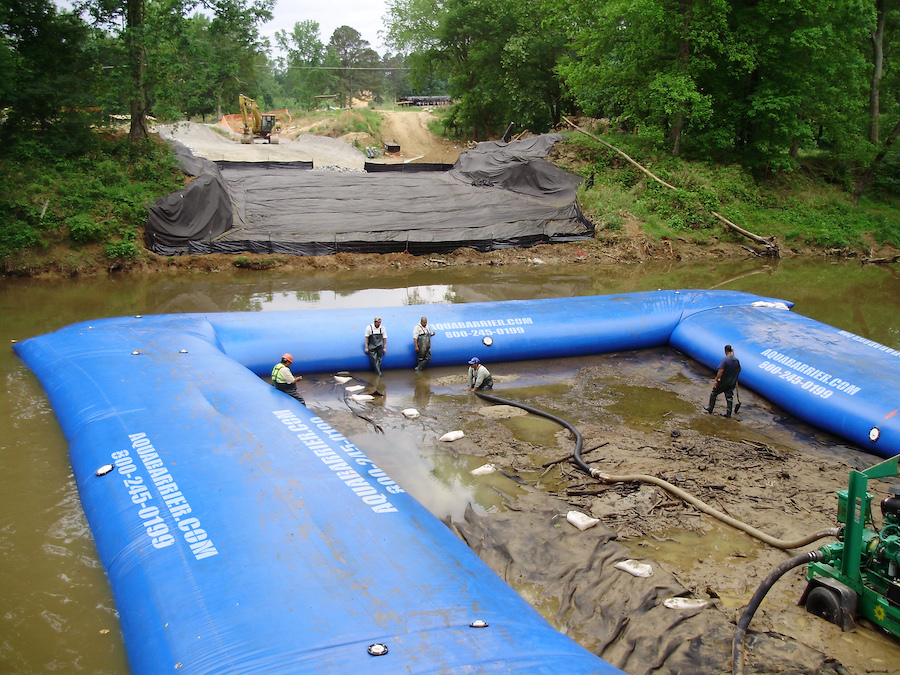
View the complete article here.
Marine construction applications often present challenges—such as dewatering and erosion control—that require innovative solutions. Historically, steel-based solutions have been the industry standard for addressing these issues. Although steel structures are still considered to be the strongest and—arguably—the most effective in most cases, there is a case to be made for non-steel alternatives for a variety of applications.
The Case for Steel
With its unique combination of strength, durability, and workability, steel has been at the forefront of the most important marine projects around the world—proving its reliability in dewatering, erosion control, and a range of other marine applications. The longevity and adaptability of steel have made it a cornerstone of the marine construction industry.
Consider dewatering—for instance—a process crucial in creating dry, workable conditions in marine environments. Steel cofferdams have been widely used for this purpose. Comprised of interlocking steel sheet piles driven into the seabed to form an impermeable barrier—these structures allow water within the enclosed area to be pumped out to create a dry work area. Steel’s inherent strength and resistance to bending makes it ideal for the heavy loads and stresses experienced in these situations.
Steel has always been an essential material used for erosion control. Consider how steel sheet piles have been used to stabilize riverbanks and coastlines—providing strong and durable barriers against the erosive forces of water. The corrosion resistance of certain types of steel also makes it suitable for long-term contact with water and soil—contributing to the longevity of these structures.
Steel has been equally vital in a wide range of other marine applications. In the construction of ports, harbors, and jetties—steel piles are driven into the seabed to provide the necessary support structures. In addition, offshore platforms in the oil and gas industry rely heavily on large steel piles for stability.
Despite the emergence of non-steel alternatives, steel is likely to remain a fundamental material in marine construction. While other materials may provide advantages in specific contexts or applications—the overall strength, durability, and versatility of steel make it irreplaceable in many scenarios.
So why consider non-steel solutions, and in what cases are they beneficial?
Non-Steel Solutions
It’s important to note that the evolution of marine construction shouldn’t focus on “replacing” steel—but rather about expanding the range of solutions available to better address the diverse challenges of working in marine environments.
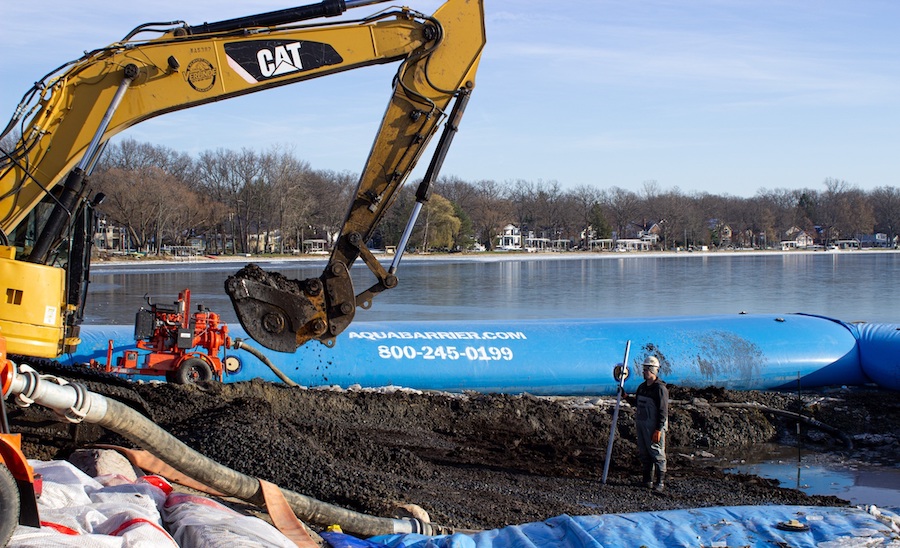
Inflatable Cofferdams
A cofferdam is a temporary structure built within a body of water that allows the enclosed area to be pumped dry—creating a safe and accessible workspace. This is typically necessary for construction projects such as bridges, dams, locks, or any other structure that requires work to be done below the waterline.
The majority of cofferdams are designed using steel sheet piles. These are—of course—long, flat pieces of steel that have interlocking edges. The sheet piles are driven into the ground to form a watertight wall. The water inside the enclosed area is then pumped out—allowing construction work to proceed in dry conditions.
An inflatable cofferdam—as the name suggests—is a type of cofferdam that is filled with water to form a temporary, reusable barrier that can effectively isolate a working area from the surrounding water. It is essentially a large, durable, water-filled tube made of industrial-grade vinyl or similar materials.
The inflatable cofferdam is brought to the site in a deflated state, placed in the desired location, and then filled with water—causing it to inflate and form a barrier. Once the work is completed, the water is removed—allowing the cofferdam to be deflated, removed, and potentially reused.
The advantages of inflatable cofferdams include:
- Ease of installation: Inflatable cofferdams are generally easier and faster to install and remove than steel cofferdams—reducing labor costs and construction times.
- Adaptability: Inflatable cofferdams can conform to uneven ground surfaces and can accommodate varying water levels—making them a versatile solution for a wide range of projects.
- Reusability: Inflatable cofferdams can often be deflated, transported, and reused in a new location—adding to their cost-effectiveness.
- Safety: In many cases, inflatable cofferdams are safer to install and remove—reducing the risk of injury during these processes.
Potential disadvantages of inflatable cofferdams include:
- Durability: Although made from tough, industrial-grade materials—inflatable cofferdams will not withstand sharp or abrasive materials as well as steel sheet piles. They could potentially be punctured or damaged by sharp rocks, debris, or by the inadvertent impact of construction equipment.
- Limitations in size and strength: While they can be made quite large, inflatable cofferdams will likely not offer the same level of strength and stability as steel sheet piles for very large or demanding applications—such as deep water projects or environments with heavy water flow.
- Maintenance needs: Inflatable cofferdams require monitoring and potential maintenance to ensure that they remain properly inflated and positioned. Any leaks or shifts in position need to be promptly addressed to avoid failures.
Inflatable cofferdams are appropriate for a variety of applications—including bridge repair, pipeline crossings, boat ramp construction, and dewatering for shoreline restoration projects—among others. They are a particularly good choice when project conditions require a temporary, reusable, and environmentally friendly dewatering solution.
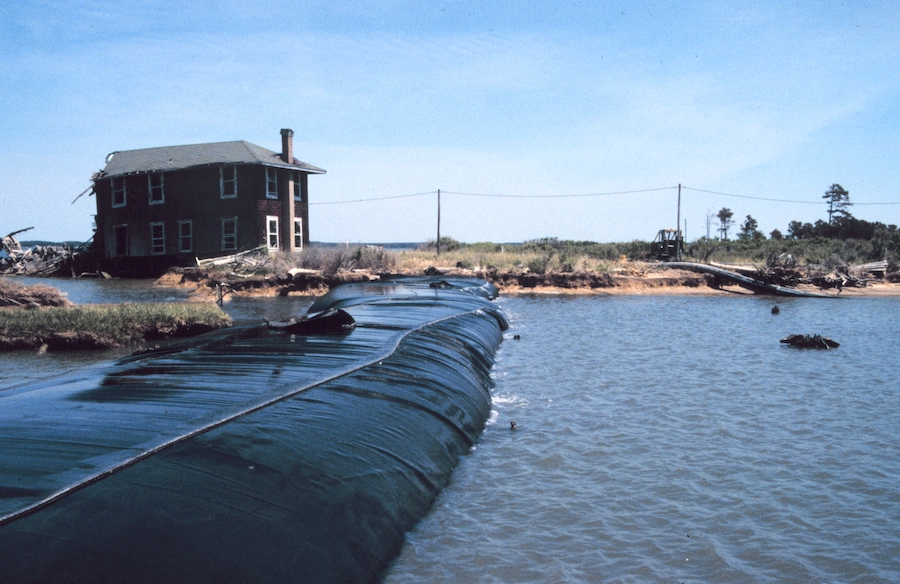
Geotextile Tubes
A geotextile tube is a large, elongated bag made from a permeable fabric—designed to be filled with sediment or other material. It is used in various marine construction and environmental management applications such as erosion control and shoreline protection. The permeable fabric allows water to escape—leaving behind the solid material in a compact and contained form.
While they don’t replace the structural properties of steel, geotextile tubes offer a different approach to solving some of the same problems—often in a more environmentally friendly way.
Some of the common applications for geotextile tubes include:
- Erosion control and shoreline protection: Filled with sand or other suitable material, geotextile tubes can serve as a protective barrier against wave action and erosion—helping to stabilize shorelines, riverbanks, and other landscapes.
- Dewatering: When filled with sludge or slurry, the permeable fabric of the geotextile tube allows water to escape—effectively dewatering the material. This can be useful in a wide range of applications—from wastewater treatment to sediment management in dredging operations.
- Containment and remediation: Geotextile tubes can be used to contain contaminated sediment or other waste material—aiding in environmental remediation efforts.
The advantages of geotextile tubes include:
- Versatility: Geotextile tubes can be used in a wide range of applications—from shoreline protection to waste containment—and they can be custom-sized to fit the specific requirements of a project.
- Cost-effectiveness: The cost of geotextile tubes can cost significantly less than some steel methods—especially for large-scale applications.
- Ease of use: Geotextile tubes are relatively simple to install—requiring less heavy machinery and labor than steel structures.
- Environmentally friendly: Geotextile tubes are typically more environmentally friendly than steel methods. For instance—when used for erosion control—they help to stabilize the soil and promote the growth of vegetation.
Potential disadvantages of geotextile tubes include:
- Handling of heavy materials: Filling geotextile tubes with heavy materials like sediment can be a challenging task and may require specialized equipment and trained personnel.
- Potential for damage: The geotextile material—while durable—can be susceptible to damage from sharp objects or rough handling. Any damage to the fabric could lead to leaks or a breach of the tube.
- Long dewatering times: For dewatering applications, the process can be quite slow as water slowly permeates out of the tube. This could potentially delay projects where time is a critical factor.
- Disposal of filled tubes: The disposal of the geotextile tube and its contents can be a challenge, especially if it contains contaminants. Appropriate disposal methods must be determined and can add to the overall cost of a project.
In the sphere of marine construction and environmental management, geotextile tubes provide a versatile and cost-effective alternative to steel methods in some cases. While they come with their own set of challenges, their advantages outweigh the potential downsides in most applications.
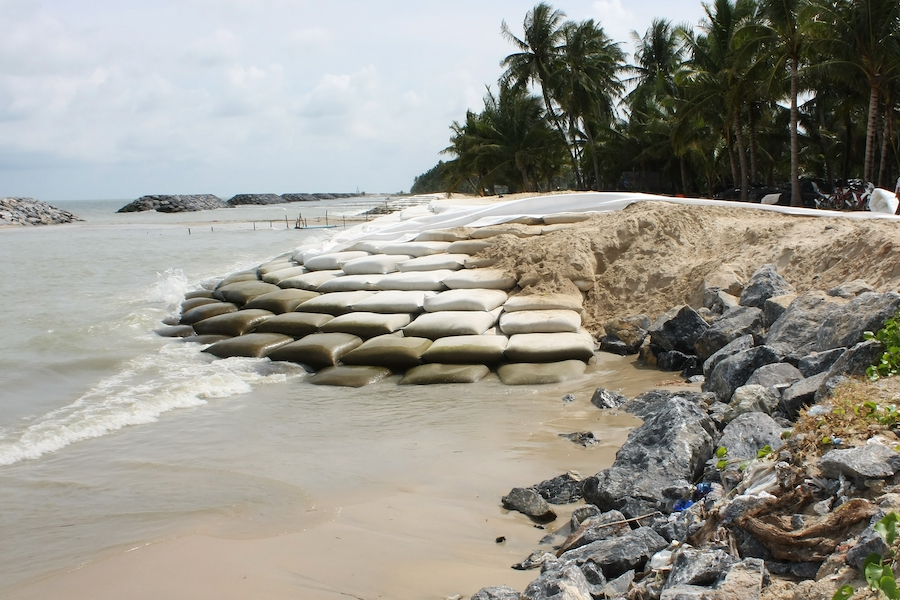
Sandbags and Geobags
Sandbags and geobags are versatile solutions used in a variety of marine construction and environmental applications, including shoreline stabilization and coastal protection.
A sandbag is a sack made of hessian/burlap, polypropylene or other materials—filled with sand or soil. Historically, sandbags have been used in flood control and military fortifications, because they are easy to transport when empty and can be filled with local sand or soil.
A geobag is a similar concept but is typically larger and made of geotextiles—permeable fabrics that—when used in association with soil—have the ability to separate, filter, reinforce, protect, or drain. These geobags are filled with soil or sand and are used in a variety of geotechnical, hydraulic, and marine structures.
Sandbags and geobags—like geotextile tubes—do not replace the structural properties of steel. However, they can offer an alternative solution for various problems traditionally addressed by steel structures.
Some of the common applications for sandbags and geobags include:
- Shoreline stabilization and erosion control: Sandbags and geobags can be used to create protective barriers along shorelines—helping to reduce the impact of wave action, prevent soil erosion, and stabilize the shoreline. This can be particularly useful for beach restoration or stabilization projects.
- Reef creation: In some cases, geobags filled with sand or other appropriate materials are used to create artificial reefs in marine environments. These structures can help protect shorelines from wave erosion and also provide a habitat for marine life.
- Breakwaters and groynes: Sandbags or geobags can be used in the construction of breakwaters or groynes to reduce wave energy and limit sediment transport.
- Underwater foundations: In certain conditions, sandbags can be used to provide a stable foundation for underwater structures. They can be strategically placed and filled to level the seafloor or provide support for other structures.
- Dredging and sediment containment: Similar to geotextile tubes, geobags can be used in dredging operations to contain and dewater dredged material.
The advantages of sandbags and geobags include:
- Flexibility: Sandbags and geobags are extremely flexible—allowing them to conform to the ground surface. This is particularly beneficial in uneven terrains.
- Ease of installation: Sandbags and geobags are easy to handle and can be installed quickly with minimal equipment and manpower.
- Cost-effective: Sandbags and geobags can be more cost-effective than steel—especially for smaller projects or in difficult-to-reach areas.
- Environmentally friendly: Like geotextile tubes—sandbags and geobags tend to be more environmentally friendly compared to steel structures.
Potential disadvantages of sandbags and geobags include:
- Durability: Sandbags—especially those made from natural fibers—can degrade over time due to environmental factors such as UV radiation, moisture, and microbial activity. Geobags—made from synthetic materials—are more durable but can still be damaged by sharp objects, rough handling, or extreme environmental conditions.
- Maintenance: Over time, sandbags and geobags may require maintenance or replacement as they can shift due to wave action, water currents, or other forces.
- Limited structural strength: While sandbags and geobags can be effective in certain applications, they do not provide the same structural strength or stability as steel or concrete structures. Therefore, they are not suitable for applications requiring significant load-bearing capacity.
- Wildlife interaction: In marine environments, there’s a possibility of interaction with local wildlife. Some animals may cause damage to the bags, or they may become entangled or trapped.
Sandbags and geobags are most useful in applications requiring flexibility, ease of installation, and cost-effectiveness. However, it is important to remember their limitations in terms of durability, maintenance, and structural strength.
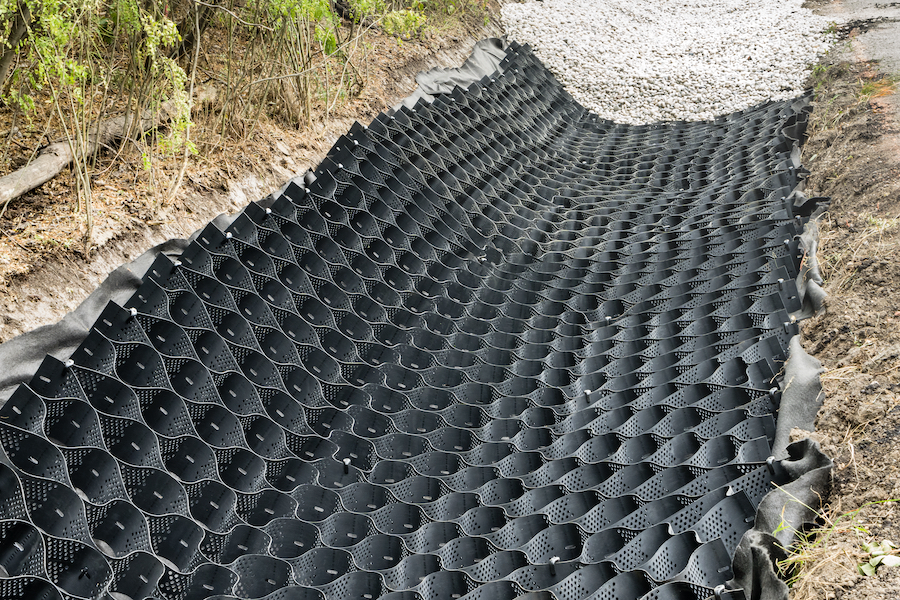
Cellular Confinement Systems
Cellular confinement systems—also known as geocells—are a type of geosynthetic material used in various marine construction and geotechnical engineering applications. They are essentially a honeycomb-like grid structure made from high-density polyethylene (HDPE), polyester, or other materials. The cellular structure is expanded on-site and then filled with soil, gravel, or concrete to create a strong and stable layer.
Some of the common applications for cellular confinement systems include:
- Slope and erosion control: The geocell structure stabilizes the soil—reducing erosion on slopes and embankments. It also helps to promote vegetation growth, which further prevents erosion.
- Ground stabilization and load support: Geocells can be used to stabilize the ground for roads, railways, and similar applications. They distribute loads evenly—reducing pressure on the underlying soil and preventing deformation.
- Channel and riverbank protection: By providing a stable structure, geocells can be used to protect channels and riverbanks from erosion.
The advantages of cellular confinement systems include:
- Versatility: Cellular confinement systems can be used in a wide range of applications—from road construction to erosion control.
- Durability: Cellular confinement systems are made from durable materials and are designed to withstand environmental factors such as UV radiation, chemical exposure, and mechanical stress.
- Environmental friendliness: Cellular confinement systems promote vegetation growth, which is beneficial for the environment.
- Cost-effective: Compared to traditional methods using steel or concrete—cellular confinement systems are often a more cost-effective solution for soil stabilization and erosion control.
Potential disadvantages of cellular confinement systems include:
- Installation: While not overly complex, the installation of cellular confinement systems does require some expertise to ensure the system is correctly installed and filled.
- Limited load-bearing capacity: While cellular confinement systems can improve load distribution, they may not provide sufficient load-bearing capacity for heavy-duty applications.
- Potential for damage: While made from durable materials, cellular confinement systems can be damaged possibly by sharp objects or improper handling.
- Maintenance: Over time, cellular confinement systems may require maintenance or replacement due to environmental degradation or mechanical stress.
In summary, cellular confinement systems are an innovative non-steel solution for various marine construction and geotechnical applications. They offer many advantages—particularly in terms of versatility, durability, environmental friendliness, and cost-effectiveness. However—like any construction material—they are not without their disadvantages, which need to be considered when deciding whether to use them in a project.
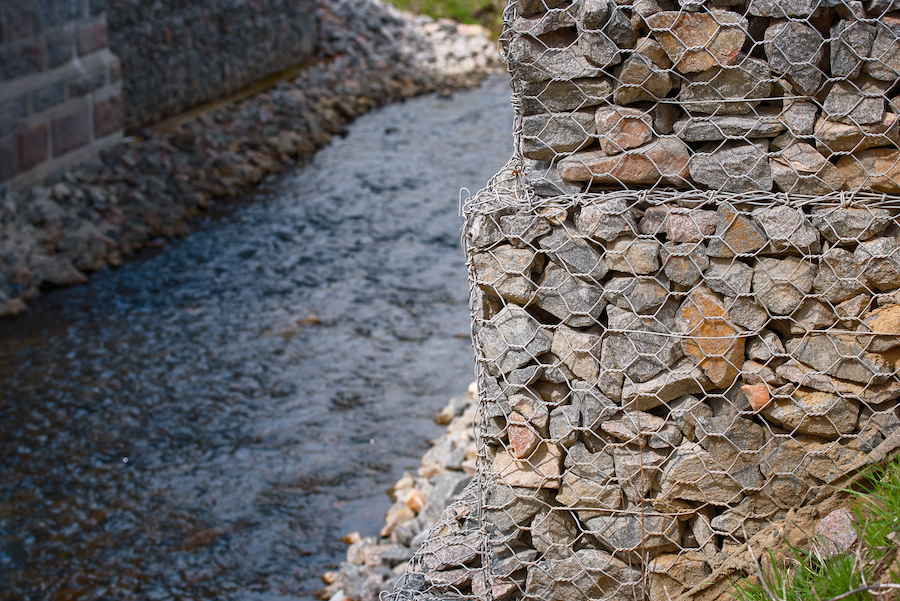
Gabions and Reno Mattresses
Gabions and reno mattresses are engineered structures designed for various construction and marine applications—such as erosion control, slope stabilization, and hydraulic works. Though traditionally filled with rock or stone, these structures present an alternative to steel structures in certain applications.
A gabion is a cage or box filled with rocks, concrete, or sometimes sand and soil. They are typically made from a flexible, twisted wire mesh—with rectangular or cubical boxes that are filled on-site.
Reno mattresses are similar to gabions but are much thinner—giving them a flat, mattress-like appearance. They are typically used for river bank and scour protection, as well as channel linings for erosion control.
Some of the common applications for gabions include:
- Coastal erosion control and protection: Gabions and reno mattresses provide robust, flexible barriers against wave action and tidal forces. They can be used to stabilize shorelines, dunes, and cliff bases that are prone to erosion.
- Breakwaters and groynes: These structures are often built using gabions and reno mattresses to reduce wave energy, control sediment transport, and protect shoreline installations.
- Sea walls and revetments: Gabions and reno mattresses can be used to construct sea walls and revetments to protect coastal areas from wave erosion. Their flexibility allows them to absorb wave energy without cracking or breaking, as might occur with rigid structures.
- Underwater foundations and scour protection: Gabions and reno mattresses can provide a stable base for marine structures like piers or jetties. They can also be used to protect underwater pipelines or structures from scour—which is the removal of sediment such as sand or gravel from around bridge abutments or piers.
- Restoration and creation of marine habitats: Gabions and reno mattresses can also contribute to the creation or restoration of marine and estuarine habitats. They can be designed to create artificial reefs or to provide habitats for various species.
The advantages of gabions and reno mattresses include:
- Flexibility: Gabions and reno mattresses are flexible structures that can conform to ground settlement without losing their functionality.
- Permeability: The spaces between the fill material allow for free drainage—thus reducing hydrostatic pressures.
- Durability and strength: Gabions and reno mattresses are highly durable and can bear significant weight.
- Environmental compatibility: Gabions and reno mattresses can integrate with the surrounding environment and can be vegetated for a natural appearance.
Potential disadvantages of gabions and reno mattresses include:
- Aesthetics: Some people find the appearance of gabions and reno mattresses less appealing than other types of structures.
- Long-term maintenance: Over time, the metal wire can corrode—especially in marine environments—and may need to be replaced.
- Construction requirements: Assembling and filling gabions and reno mattresses can be labor-intensive compared to other methods.
In summary—while gabions and reno mattresses don’t replace the structural properties of steel—they offer a different approach to solving some of the same problems—often in a more environmentally friendly and cost-effective way. Their versatility makes them a valuable tool in a variety of marine construction and hydraulic engineering applications.
Conclusion
Steel isn’t going anywhere. It is the strongest material available for marine construction applications—proving its irreplaceability in a multitude of applications where durability, longevity, and high structural strength are required.
However, alternatives such as inflatable cofferdams, geotextile tubes, sandbags and other non-steel solutions should be considered for a range of marine construction applications.
These non-steel solutions—each with their unique advantages and disadvantages—often provide greater versatility, cost-effectiveness, and environmental compatibility.
Therefore, an integrated approach—where steel-based and non-steel alternatives coexist and complement each other—will be most beneficial in meeting the dynamic demands of marine construction.
View the complete article here.
What are some non-steel alternatives for dewatering and erosion control in marine applications?
There are several non-steel alternatives for dewatering and erosion control in marine applications. These include vinyl sheet piling, synthetic erosion control blankets, geotextiles, and cellular confinement systems. These options can offer benefits such as corrosion resistance, flexibility, ease of installation, and environmental friendliness.
Why are non-steel alternatives sometimes preferred in marine applications?
Non-steel alternatives are sometimes preferred in marine applications due to their resistance to corrosion, a common problem with steel when exposed to marine environments. Additionally, some non-steel materials can offer flexibility and ease of installation, which can be beneficial in certain applications. Moreover, certain non-steel alternatives can have less environmental impact than steel, making them a preferred choice for projects aiming to minimize their environmental footprint.