Maintenance and Repair Best Practices for Barges and Other Marine Vessels
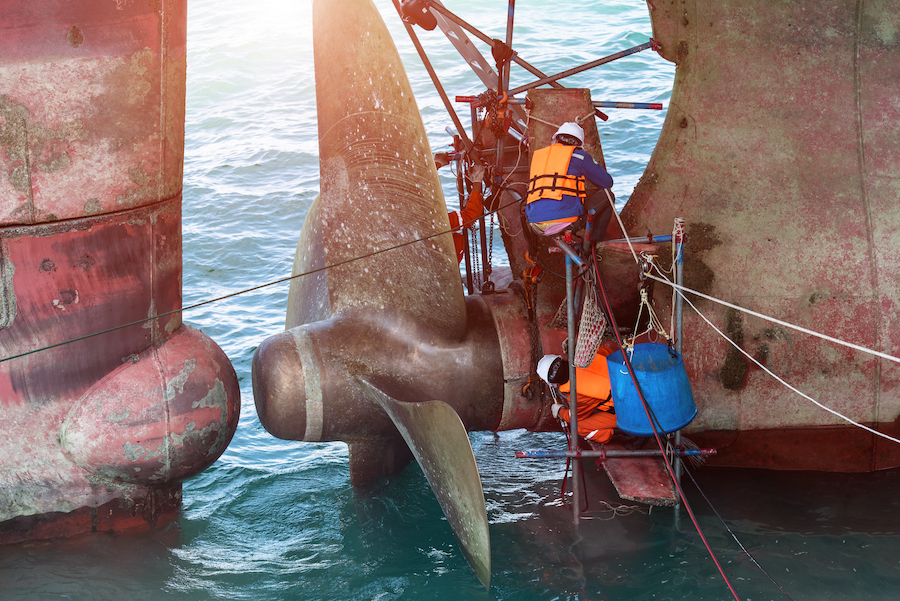
View the complete article here.
In the vast and unpredictable expanse of the marine environment, a barge’s endurance and performance are tested relentlessly. From the silent encroachment of corrosion to the relentless wear-and-tear of daily operations, vigilance is crucial. This comprehensive guide dives deep into the challenges barges face—highlighting the importance of regular check-ups, maintenance practices, and the undeniable role of human expertise. Armed with this knowledge—owners and operators of barges and other marine vessels can ensure that their vessels not only stand the test of time but also navigate waters safely, efficiently, and cost-effectively.
Regular Check-ups are Crucial
Identifying minor barge issues early prevents them from becoming major, costly problems. A small leak, when promptly addressed, avoids extensive damage to the hull and onboard equipment—saving both money and operational time.
Regular maintenance is also vital for crew and cargo safety. By addressing wear-and-tear, the barge remains safer and serves longer—maximizing its operational life and ensuring the safety equipment’s readiness.
And, of course, establishing a routine maintenance culture ensures that barge checks are consistent and become an ingrained practice. This disciplined approach passes on the culture of regular upkeep to future crews, keeping the barge in prime condition regardless of its age or challenges faced.
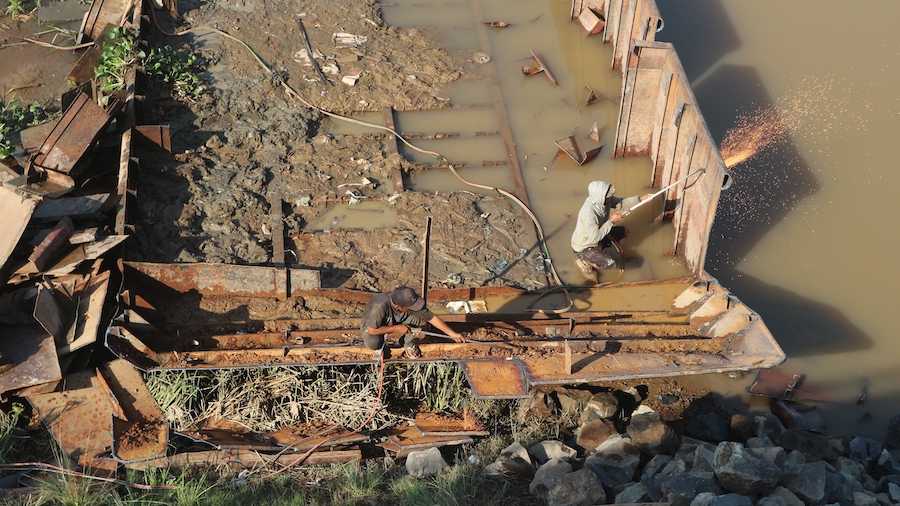
Regular Check-ups for Barges and Other Vessels
Maintaining the robust functionality of a barge hinges not only on understanding its intricate components but also on the timing and thoroughness of inspections. In the wide range of barge operations, the emphasis on maintenance varies—catering to the unique demands of each component and its wear patterns.
Frequency Recommendations: From Daily Checks to Annual Inspections
In barge operations, maintenance isn’t a one-size-fits-all activity—it depends on the component in question and its susceptibility to wear-and-tear. Here are some general frequency guidelines to consider…
Daily checks are routine inspections, primarily aimed at ensuring the vessel’s operational safety. It includes basic operational tests, checks for leaks, and a quick survey of equipment status.
Monthly checks take a deeper look into machinery, equipment, and certain areas of the vessel. This could include inspecting the integrity of seals, testing safety equipment, and looking for signs of wear in high-use areas.
Quarterly/Seasonal checks are inspections that might involve a more thorough examination of the barge’s structural components, considering factors like the effects of seasonal changes.
Annual inspections scrutinize almost every aspect of the barge. It often requires partial or complete docking and is essential for ensuring the vessel’s long-term health and compliance with safety standards.
Key Components to Examine
Not sure where to start your examination? Well, here are the key components to consider:
- Hull and deck: These form the barge’s primary structure and are exposed to constant water pressure and potential impacts. Regularly inspect for signs of corrosion, damage, or deformations.
- Watertight compartments: Ensuring these compartments remain sealed is critical. They should be inspected for any leaks, rust, or seal damage that could compromise their watertight integrity.
- Propulsion and steering systems: The heart of the barge’s mobility. Regular checks should be conducted to ensure the efficiency of engines, rudders, and propellers—looking for wear and ensuring proper lubrication.
- Electrical systems: A vital system that powers on-board machinery, lighting, and more. Inspections should ensure no loose connections, potential short circuits, and that all components are shielded from moisture.
- Safety equipment: Life vests, fire extinguishers, alarms, and other safety gear need to be in top condition. Regular checks ensure they function properly in emergencies.
Understanding and Combating Corrosion on Marine Vessels
Corrosion, especially in the maritime sector, is a silent enemy that constantly undermines the durability and functionality of barges and marine structures. For that reason—it is essential to understand the causes, types, and prevention techniques for corrosion.
Causes of Corrosion in Marine Environments
Corrosion, the gradual degradation of materials by chemical reactions with their environment, is a formidable adversary in marine settings. The unique challenges posed by the marine environment exacerbate the rate and severity of corrosion, for reasons such as…
Ocean and sea water are rich in salts, primarily sodium chloride. When metals come into contact with saline water, the salt acts as an electrolyte—facilitating the electrochemical reactions that cause corrosion. This makes marine environments particularly hostile to metals.
The high humidity levels in marine environments mean that surfaces are frequently wet, providing an ideal environment for corrosion—especially when combined with salts from the surrounding water. In addition—condensation on metal surfaces, especially during temperature fluctuations, can further accelerate the corrosion process.
Continuous operation, frequent docking, and collisions with debris can cause wear-and-tear and minor damages to protective coatings or paints on marine vessels. These small breaches expose the underlying metal to water and oxygen, catalyzing the corrosion process.
When two different metals come into close contact in a marine environment, galvanic corrosion can occur. This type of corrosion happens because of the potential difference between the two metals—causing one metal to corrode as it acts as an anode to the other metal, which acts as a cathode. Such scenarios are common in marine machinery and structures where different metals are often bolted or welded together.
Types of Corrosion
Corrosion, while often painted with a broad brush, is nuanced and manifests in various forms—each with its unique characteristics and triggers. Here’s a deep dive into some of the most prevalent types:
As the most common form, general attack corrosion impacts the entire surface of a metal uniformly. This type is primarily an electrochemical process—where the metal turns into its oxide, hydroxide, or sulfide. It’s predictable and, fortunately, can be managed with proper care—though it can lead to thinning and weakening of the material over time.
As the name suggests, localized corrosion affects specific, confined areas of a metal’s surface—leaving the majority untouched. There are three main types of localized corrosion: pitting (small pits or holes), crevice corrosion (occurs in stagnant locations, like those found between two joining surfaces), and filiform corrosion (underneath coatings, leading to worm-like patterns).
When two different metals or alloys come into electrical contact in the presence of an electrolyte (like saltwater), galvanic corrosion can occur. One metal (the anode) will corrode faster than it would alone, while the other metal (the cathode) will experience a reduced rate of corrosion. This is due to the potential difference in their electrochemical properties, making it a common concern in marine settings.
A more insidious type, environmental cracking, occurs when environmental conditions cause a material to become brittle and crack. It encompasses a range of corrosion types, including stress corrosion cracking (when tensile stresses and specific corrosive conditions align) and corrosion fatigue (cracking due to cyclic stresses in a corrosive environment). The dangers lie in its unpredictable nature and potential for rapid material failure.
Corrosion Prevention Techniques for Marine Vessels
In the face of the persistent threat posed by corrosion, especially in marine environments where barges operate, prevention becomes a key strategic component. Adopting effective techniques to combat the onset and progression of corrosion is essential to safeguard the integrity and longevity of barges and marine structures. Some of the most pivotal corrosion prevention methodologies include…
At the foundation of any anti-corrosion strategy is the choice of materials. Opting for metals that are inherently more resistant to corrosion, like stainless steel or aluminum, can provide an inbuilt defense. For marine applications, bronze and brass—which resist saltwater corrosion—are commonly used. Understanding the environment in which the material will operate can help in choosing alloys specifically designed to resist corrosion in those conditions.
As a direct and effective method, applying protective coatings or paints provides a barrier between the metal and corrosive agents. Modern coatings are formulated to be resistant to specific corrosive challenges, be it saline water or industrial chemicals. In addition to protection, these coatings can also offer aesthetic benefits—making them a popular choice for both functional and visual purposes.
As a sophisticated method primarily used for submerged or buried structures, cathodic protection involves making the metal structure act as a cathode—thus preventing its corrosion. This is achieved by either attaching a more reactive metal to act as an anode (sacrificial anode method) or by applying an external electrical DC current, ensuring that the entire structure remains cathodic.
Sometimes, the simplest measures are the most effective. Regular cleaning ensures that deposits, which can trap moisture, are removed—reducing the risk of localized corrosion like pitting. In addition, periodic inspections can help detect early signs of corrosion—facilitating timely interventions and preventing more extensive damage.
Essential Maintenance Practices Beyond Corrosion
Navigating waters demands meticulous attention to a vessel’s integrity—whether it’s the watertight barriers that shield against intrusive waters, the propulsion systems driving its course, or the electrical networks powering its operations. In addition to the machinery, it’s the human element—the well-trained crew—that stands as the most versatile line of defense against the unpredictable challenges of the marine realm.
Ensuring Watertight Integrity on Marine Vessels
Seals, crucial for preventing water ingress, degrade over time due to wear and marine exposure. Regular checking of the seals can prevent moisture entry, averting potential corrosion, and equipment damage.
The bilge pump expels unwanted water from the vessel’s lowest compartment, safeguarding buoyancy and safety. Periodic bilge pump tests ensure its readiness, highlighting potential blockages or malfunctions.
Watertight doors and hatches are central to a vessel’s compartmentalization strategy, containing flooding and ensuring buoyancy. Routine maintenance of watertight doors and hatches checks their sealing efficiency, locking mechanisms, and overall structural integrity.
Propulsion and Steering Maintenance on Marine Vessels
Oil plays a pivotal role in ensuring the smooth operation of marine engines and machinery. Like all engines, those on vessels accumulate impurities over time—compromising efficiency and potentially causing damage. Regular oil changes not only extend the lifespan of the machinery but also maintain optimal performance and fuel efficiency.
Propellers are the driving force behind a vessel’s movement. Over time—they can sustain damage from debris, corrosion, or regular wear-and-tear. Regular propeller inspections can detect deformities, cracks, or inefficiencies. Prompt replacement or repair ensures the vessel maintains its speed, maneuverability, and reduces unnecessary fuel consumption.
The rudder system governs the direction and stability of a vessel. A malfunctioning or compromised rudder can seriously affect a vessel’s navigability. Periodic rudder system checks ensure that the rudder’s mechanisms, like the tiller and pintles, are free from corrosion and damage. In addition, making sure the hydraulic or mechanical systems that control the rudder are functioning properly is essential for safe navigation.
Electrical System Maintenance on Marine Vessels
Electrical systems on vessels are intricate networks that depend on stable connections. Loose or corroded connections can lead to power losses, inefficiencies, or even hazardous situations. Regularly inspecting and tightening loose connections ensures consistent power flow and reduces the risk of electrical fires or short circuits.
Generators and batteries are the lifelines of a vessel’s electrical system. While generators ensure a continuous power supply, batteries play a vital role during emergencies or when auxiliary power is required. It’s essential to test both generators and batteries routinely, ensuring they can deliver optimal output when needed. For batteries, this includes checking for proper charge levels and potential signs of aging—like swelling or leakage. Generators should be run periodically to ascertain their efficiency and to detect any unusual sounds or vibrations.
The marine environment is inherently damp, posing a significant risk to electrical systems. Moisture can lead to short circuits, corrosion of components, or reduced equipment lifespan. To mitigate exposure to moisture—it’s essential to ensure all electrical components, especially connections and junctions, are well-insulated and sealed. In addition, dehumidifiers or ventilation can be used in areas prone to condensation to maintain a dry environment.
Regular Training and Drills on Marine Vessels
Marine operations rely heavily on human expertise and intuition. A well-trained crew not only ensures efficient operations but also minimizes risks during unexpected events. They can adeptly handle equipment, make informed decisions on the fly, and communicate effectively among themselves. A cohesive and knowledgeable crew enhances overall vessel performance, safeguards assets, and fortifies safety protocols.
Emergencies at sea can be unpredictable and unforgiving. Regular safety drills play a vital role in preparing the crew for such eventualities. These drills instill a sense of discipline, ensure quick reflexes during crises, and highlight areas needing improvement. Through repeated practice, crew members internalize critical steps—enabling them to act swiftly and confidently during real emergencies. In addition, drills provide opportunities to refine and perfect protocols—ensuring that the entire crew works as a unified front when faced with challenges.
The Role of Technology in Barge Maintenance
In the rapidly evolving maritime sector, technology has emerged as a pivotal force driving efficiency, safety, and operational excellence. From state-of-the-art monitoring systems to predictive maintenance techniques and the adoption of digital documentation, vessels are harnessing innovative solutions to streamline operations and stay ahead of challenges.
Modern Monitoring Systems and Their Benefits
In today’s interconnected world—modern monitoring systems represent the convergence of advanced sensors, artificial intelligence, and real-time data analytics. These systems provide a holistic view of a vessel’s condition and its operational parameters. Some of these benefits include:
- Real-time data collection: Sensors strategically placed throughout the vessel collect data continuously, offering instantaneous feedback on various systems’ statuses—from propulsion to electrical networks.
- Early detection of anomalies: With continuous monitoring, deviations from the norm are detected promptly—allowing for quicker interventions and potentially averting larger issues.
- Efficient resource allocation: By knowing precisely where issues might arise, resources can be optimally allocated—leading to cost savings and operational efficiencies.
- Safety enhancements: Modern monitoring systems can predict hazardous conditions, enabling preventive actions that ensure the safety of both the crew and the vessel.
The Importance of Predictive Maintenance with the Help of Technology
Predictive maintenance, powered by the combination of technology and analytics, goes beyond the traditional reactive or scheduled maintenance approaches. Instead of waiting for equipment to fail or sticking rigidly to maintenance timetables, predictive maintenance anticipates potential issues.
By anticipating problems before they manifest, vessels can minimize unplanned downtimes—ensuring consistent operations.
Addressing minor issues before they escalate can lead to longer operational lifespans for critical machinery.
Predictive maintenance often translates to less extensive repairs and fewer replacements, resulting in significant cost savings in the long run.
With technology providing actionable insights, decisions are based on concrete data rather than mere intuition.
Digital Documentation and its Role in Streamlining the Maintenance Process
The shift from paper-based to digital documentation is revolutionizing the maintenance process in marine operations.
Digital documents can be accessed on-demand, ensuring that maintenance logs, equipment manuals, and other critical documents are readily available whenever required.
With cloud storage solutions, documents can be stored centrally, ensuring they’re accessible to authorized personnel irrespective of their location.
Digital documentation facilitates real-time updates, ensuring that all records are current and reflect the latest information.
Digital platforms often come with tools that promote collaboration among crew members, streamlining communication and task delegation during maintenance processes.
Conclusion
The health and longevity of a barge are products of diligent maintenance, keen attention to detail, and a well-trained crew. Through regular check-ups and proactive strategies, owners and operators of marine vessels can combat corrosion and wear while ensuring the safety and operational efficiency of these marine giants. Above all—the key to successful and safe barge operations lies in a blend of knowledge, practice, and an unwavering commitment to routine care.
View the complete article here.
How often should marine vessels undergo maintenance?
Regular maintenance is recommended, typically scheduled annually or based on the vessel's operational hours and specific usage conditions.
What are common issues addressed in marine vessel repairs?
Repairs often focus on addressing issues like hull damage, corrosion, propulsion system maintenance, and ensuring compliance with safety and environmental regulations.