Ground Modification Methods for Deep Foundations Part II – Vertical Drains and Accelerated Consolidation
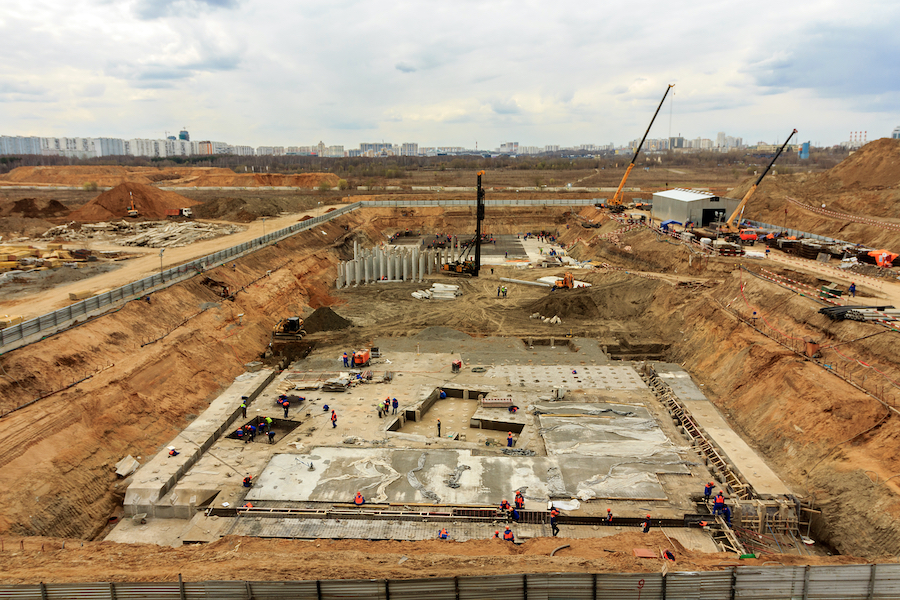
View the complete article here.
Ground modification techniques can be utilized to improve sites with either marginal or unsuitable in-situ soils. There are a variety of methods that can be used, including techniques to consolidate the soil. One common method is the use of vertical drains and preloading to consolidate soft ground.
This technique has been used since the 1920s. Vertical drains offer a shorter pathway for water to exit the soil, while preloading using fill surcharges the foundation soils. Historically, a number of different types of drains were used, from sand drains to cardboard drains. Today, the most common vertical drain for ground modification is a prefabricated vertical drain, or PVD. These are sometimes referred to as wick drains, but function by creating drainage via pressure (not wicking). The term “wick drain” came from how PVDs look. They may also be referred to as drainage wicks, band drains, and strip drains. PVDs are used to accelerate consolidation of soft saturated compressible soils under load.
PVDs consist of a geotextile jacket that surrounds a plastic core with drainage channels, and re band-shaped. With this configuration, pore water in the soil can seep into the drain for collection. The water is then transmitted through the length of the core. In most cases, a PVD is 4 inches wide by 1/8 to 3/8 inches thick.
Other vertical drain systems may be used to consolidate soil, including aggregate columns and geotextile encased columns. Because PVDs are the most cost-effective vertical drain, they are used in nearly all situations by contractors for ground modification applications.
In transportation projects, the most common use of PVDs is to accelerate consolidation at approach embankments at bridges and at other embankment construction over soft soils. Preloading is typically used in conjunction with PVDs. This involves applying load to induce settlement and consolidation of the foundation soils. The load is often the amount of fill material that is required to bring the site to its final elevation (taking settlement into account). If extra load or added fill — surcharge — is added above the final elevation to accelerate settlement and/or minimize secondary consolidation, it is removed after the required consolidation is achieved.
Vacuum preloading may also be an option on some sites. This method involves removing atmospheric pressure from a confined and sealed soil, and then maintaining that pressure to a predetermined period of time. It is often used in combination with PVDs, with the soil loaded approximately uniformly throughout its depth (by the equivalent of one atmosphere of vacuum). This method is rarely used in the United States, but is more common in the rest of the United States.
This article will explain the use of various vertical drain methods for the consolidation of soft souls through preloading and/or surcharging. Given the many benefits of PVDs, including decreasing settlement time and increasing the rate of strength gain in soils, these techniques are particularly useful for contractors working on infrastructure and/or transportation projects.
Feasibility Considerations
Vertical drains — and specifically, PVDs — are used most frequently where consolidation of moderately to highly compressible soils with low permeability and full saturation is needed. These soils may be described as silts, clays, organic silts, peats, organic clays, muskeg, sludge, swamps, or muck.
To use PVDs on these soils, they must be saturated and normally to slightly over-consolidated before loading. PVDs may also be used on under-consolidated soils when performing land reclamation. For the PVDs to be completely effective, the loading should exceed the preconsolidation stress.
Generally, PVDs are not used for highly organic materials, or in situations where secondary consolidation will lead to substantial post-construction settlement. In these cases, additional surcharging may be utilized to minimize the impact of secondary consolidation.
A relatively new application of PVDs involves installing drains to reduce the possibility that saturated granular soils will be liquified. The PVDs provide a way for excess pore water pressures that result from seismic excitation to dissipate rapidly through drainage pathways. In this way, PVDs replace gravel drains that are traditionally used for liquefaction mitigation. High flow capacity drains of 3 to 6 inch diameter are used in this application to allow for the rapid dissipation of excess pore water pressures.
Advantages and Disadvantages of PVD Use
If a particular project requires ground modification in order to improve the soils, the use of vertical drains may be necessary. There are numerous benefits to using PVDs in these situations — as well as some drawbacks.
For most projects, PVDs are a cost-effective alternative to other vertical drains, such as aggregate drains. PVDs can be installed fairly quickly, at up to 15,000 lineal feet per day per rig. Because each reel of PVD is relatively small — approximately 3.3 feet in diameter and 4 inches thick — this material can easily be stored.
Once installed, PVDs offer a permanent path for drainage, even with considerable lateral displacement or buckling under soil movements. At the same time, the typical size of mandrel used for PVDs is small enough to create minimal displacement. The impact of displacement can be taken into account during the design process and increase the time needed for consolidation if necessary.
Quality control is also improved through the use of PVDs. As drain continuity is assured during installation, inspection only requires ensuring proper drain anchorage and depth attainment. In addition, there is rarely a need to remove spoil with the use of PVDs. Except in situations where drilling through stiff layers is necessary to reach the compressible layer, there is generally no significant excess material to be removed from the site.
Because there are a range of types and sizes of PVD installation equipment, the method can be adapted to field conditions. In most cases, PVDs are installed with a static or vibratory installation force. However, lightweight equipment can be used where the ground is unstable.
Finally, PVDs are installed without jetting in the majority of sites. This means that no water is required to install PVDs. Even if a minimal amount of jetting is required, the surface runoff is small.
There are two primary potential disadvantages to utilizing PVDs. First, there are headroom limitations, as the equipment used to install PVDs must be 5 to 10 feet taller than the depth of the installation. This may limit the use of PVDs for some sites. Second, PVD materials — while relatively small in size — must be stored properly, including out of the sun (or covered) to prevent degradation.
Evaluating Feasibility
If PVDs are to be used to accelerate settlement during loading, the subsoil must meet specific criteria. It must have:
- Moderate to low compressibility
- Low permeability
- Full Saturation
- Low-to-moderate shear strength
In addition, the final embankment loads must exceed preconsolidation stress, and secondary consolidation must not be a significant concern. Even if the soil meets this geotechnical criteria, a full evaluation for environment and other effects must be made.
To determine if soils at a site meet the geotechnical criteria for the use of PVDs, and initial subsurface investigation must be undertaken. This investigation must be extensive enough to determine the extent and depth of the compressible soils, as well as to obtain undisturbed samples for strength and consolidation testing. Laboratory tests to determine moisture content, Atterberg Limits, and organic content in short depth intervals should be performed. This testing can help engineers choose the depth at which undisturbed samples should be recovered.
In addition, consolidation testing should be performed to determine over-consolidation ratios with depth. Shear strength testing can help to evaluate undrained and drained shear strengths. Other tests, such as piezocone soundings and piezocone pore pressure dissipation tests, can also be performed to confirm that the soils meet the geotechnical criteria.
Beyond the geotechnical considerations, the environmental impact must also be assessed. If the in situ soils are contaminated with hazardous waste or material, then excess pore water that drains through the PVD may need to be collected and treated. In this situations, the PVD should not be allowed to penetrate into a highly permeable layer.
In addition, both site topography and the soil conditions at the site can significantly raise the cost of using PVDs. For example, uneven working surfaces will have to be benched with widths of 25 feet or greater to allow for equipment. This can make the installation of PVDs less economical.
Where there is limited headroom, such as under an existing bridge, the installation of PVDs may not be cost-effective. The PVDs may be installed vertically in segments, but this may raise the cost to 5 times as much as the normal installation price.
If there are obstructions above the compressible layer that must be penetrated, it may add a substantial amount to the total cost. If pre-drilling is not required, these extra costs will be minimal. However, if obstructions such as concrete, riprap, slag, or brick exist, pre-drilling may be required.
Where the work surface is unstable, geosynthetics and granular soil can be used to make the drainage layer stable. The installation equipment can typically penetrate these materials easily. However, if the ground cannot be stabilized, movable timber mats can add support, or lightweight equipment may be utilized — both at an increased cost.
If PVDs need to be installed at a depth of over 100 feet, a crane and other specialized equipment may be necessary. This can increase the cost substantially.
Where there are stiff layers, the entire length of the PVDs may need to be pre-augered. In this situation, it is best to not use PVDs, as this process will create a large void area around the drain. The collapse around the grain will result in excessive soil disturbance. Instead, if the void could be filled with sand, then the PVD will not be necessary.
If a site has an extremely soft layer, the low shear strength will make it difficult to anchor the drain at that depth. There are two options to resolve this issue: to go to an additional depth, or to use special equipment procedures. Either option will slow production and increase costs.
When a site has accessibility issues, such as multiple overhead obstructions or steep access roads, it may be difficult for the equipment needed to install the PVDs to get to the site. If an access road must be built, then it may not be economically feasible to install PVDs.
Finally, overhead or subsurface utilities may obstruct PVDs. If there are multiple utilities, including large sewer pipes, the drains may not be installed for a significant width. Similarly, overhead wires may prevent the installation of PVDs in large areas.
If any of these site conditions are encountered, then a speciality contractor who works with PVDs may be consulted to determine the difficulty of the proposed project. This should include a cost analysis.
Limitations on the Use of PVDs
Generally, there is no structural purpose for PVDs. Instead, these drains provide a faster release of excess pore water, which allows for faster settlement and quicker strength gain through consolidation. If a site has a stability issue, the soil will have the same initial strength whether PVDs are installed or not. Where stability is a concern, the rate that the load is increased must be carefully controlled and monitored. If the final or stage fill height is under 12 feet, then vacuum consolidation may be considered.
PVDs that are used without a surcharge load can accelerate primary consolidation — water coming out of the soil via the application of pressure. Secondary consolidation, which is caused by the soil particles deforming or reorienting under constant load, should be estimated as well. It can be minimized through the placement of excess surcharge or the extension of waiting periods prior to final construction. Importantly. soils with a high percentage of organic content are more likely to experience significant secondary consolidation, and as a result, the potential magnitude of that consolidation should be carefully evaluated.
While PVDs can be installed beyond 100 to 200 feet, there are special considerations that must be taken into account. With extremely deep PVDs, the flow capacity of the system could limit design considerations. In some cases, well resistance in the drain may occur; here, the consolidation time will be determined more by the discharge capacity of the drain as opposed to the horizontal permeability of the soils.
If the entire length or lower length of a PVD site will require pre-drilling, PVDs are not recommended. Other methods of ground modification, such as the use of sand drains, should be considered.
Alternatives to PVDs
As described above, there may soil conditions, site conditions, or other factors that recommend against the installation of PVDs. There are four types of alternative solutions: (1) accepting the time constraint without the use of a vertical drain system; (2) bypassing the compressible soul by using deep foundation elements; (3) reducing the compressibility of the soil using a different ground modification method; or (4) reducing the load on the compressible soil by using lightweight fill.
If a project allows for enough time for settlement to occur, PVDs are not necessary. In some situations, a preload without PVDs may all that is needed to obtain consolidation within the allowable time constraints. The cost of doing a preload as opposed to installing PVDs with preload should be calculated to determine the best option.
In some cases, engineers may be able to design the project to encompass excessive post-construction settlement. This design should account for the anticipated cost of repairs or corrections to the ground or the structure itself.
Deep foundations may also be used to bypass compressible soils, such as to support a bridge or embankment. Although this method is effective, it tends to be expensive, and may limit the flexibility of future uses of the site.
Reducing the compressibility of the in situ soils is usually more costly than installing PVDs, but offers a number of potential solutions. This includes creating stone columns, deep soil mixing, excavation and replacement, and using lightweight fills. Both stone columns and deep soil mixing will strengthen the soil while reducing its compressibility. The use of lightweight fill to minimize settlement will not improve the soil, but it will reduce both settlement and stability issues by reducing the imposed loads. If stability is an issue at the site, these solutions may be combined to achieve the best result. For example, stone columns may be used to increase stability while PVDs can be installed to accelerate consolidation in more stable areas.
Construction and Materials
There are a number of methods that can be used to install PVDs. Most of these methods employ the same principles, such as an anchoring system to hold the drain in place while a steel covering mandrel that protects the PVD is withdrawn. Similarly, the PVD material used for all methods comes in rolls, and is threaded through the mandrel. The main difference between these techniques is how the mandrel is inserted into the ground.
Generally, an installation mast is used. This mast contains the material reels, mandrel, as well as a method of installation force. A carrier — either a crawler excavator or a crawler race, depending on the depth of installation — is also used. Static, vibratory, and/or static-vibratory are the most common methods of installation.
Typically, the mandrel has a diamond or rectangular shape. A stabilizing fin may be added for vibratory installations. The PVD will usually be fed through the mandrel from a storage reel that is mounted at or near the base of the mast. The material will then travel up through the mast, over a sheave at the top, and then down through the steel mandrel.
Installation begins when the steel mandrel has been threaded with the PVD material, and then attached to an anchor at the bottom. The answer is usually a small piece of cable or rebar, or a special anchor plate made of sheet metal. When a sheet metal anchor is used, the PVD material is inserted through the handle and then reinserted into the bottom of the mandrel.
After the anchor is in place, the mast is positioned over the drain location, and the mandrel (together with the PVD material) is inserted into the soil. The drain is completely protected from damage during installation by the steel mandrel. After the proper depth has been reached, the mandrel is withdrawn, and the PVD material is left in the ground. Once the bottom of the mandrel is above ground level, execs PVD material is pulled through it to allow for a sufficient “cut-off” above the working surface. The PVD is then cut and attached to another anchor. The process is repeated at other drain locations.
The length of the drain material must be slightly lower than the desired depth of installation. For extremely deep drains of 150 feet or deeper, specialized or large equipment may be necessary.
Once the PVD material on a reel is done, another reel is spliced to the previous role. This is usually done by inserting the core at the end of the old roll into the new roll, at a minimum length of 6 inches. The core and the geotextile must both overlap in order to maintain continuation of both the flow channel and filtration. Where the rolls are spliced, at least 10 staples are inserted to hold the ends together. The splice must be formed in a way that the bottom side of a vertical drain can be inserted into the upper end to allow for continuous flow.
If there are obstructions above the compressible stratum that cannot be penetrated using the normal procedures, pre-drilling or offsetting the drains may be necessary. If there is an obstruction that cannot be penetrated using normal installation procedures, it can be offset.
For PVD installation, a labor crew of 1 to 2 people is usually needed to handle drain preparation, cutoffs, changing of drain rolls, and anchor attachment. In addition, performing occasional repairs to the equipment may be necessary.
If there is an unstable working surface, a sloped surface, if the subsoils are difficult to penetrate, or in the case of extremely deep drains, specialized equipment may be necessary. For example, marsh buggies may be used on unstable surface situations. External jetting equipment mounted on lightweight skid platforms may be used on steep slopes, while test boring equipment may be used to install pipe drains with PVD materials for relief wells in existing dams.
Staged Construction
When a foundation is soft, with soils that have low strength and high compressibility, excessive settlement and fill instability may occur when embankments of moderate to large heights, particularly if the fill is placed too quickly or too high. One solution to this issue is to build the fill in stages, so that the soils can consolidate and gain strength between additions of fill material. The rate of fill placement is related to the consolidation characteristics of the foundation soils. By monitoring settlement and pore water pressures, engineers can predict when more fill can be added without causing excessive settlement and/or slope instability. Staged construction is usually used when there is sufficient time to allow for settlement during the construction process. PVDs can be used in this process to reduce the wait time between placement of fill.
Construction Materials for PVD Installation
PVDs usually consists of a plastic core that is formed to make channels, along with a loose geotextile cover. This material is relatively flat, approximately 4 inches wide by 1/8 to 3/8 inch thick.
The core works to create low resistance flow channels so that water can flow along the length of the material. The core also maintains the drain configuration and shape, supports the filter jacket, and provides both compressive and tensile strength. The core must have both strength and flexibility to function properly.
The geotextile cover provides a surface that prevents soil particles from entering the core channels while still allowing water to pass into the drain. It also prevents the interior core channels from closing while forming the outside of the flow channels.
The apparent opening size (AOS) of the geotextile should be small enough so that only a few particles can penetrate, without soil particles clogging the core. An AOS range of 0.15 to 0.074 mm sieve size (#100 to #200 in the U.S.) is typically effective in all projects.
The selection of the PVD type is a critical part of the overall design process. The primary parameters must include jacket filterer permeability and characteristics, equivalent diameter, material strength, flexibility, drain resistance, durability and discharge capacity. The filter should either prevent soil particles from passing through, or should allow the formation of a natural filter cake. It should also resist eating during installation, and be durable enough to stay in place for the duration of the consolidation period.
Soil disturbance will depend on the shape and size of the mandrel, as well as the soil micro fabric and the installation procedure used. If the soil is disturbed, it may slow the rate of consolidation. Through proper mandrel selection, the effects of a smear zone can be minimized.
Beyond the PVD and mandrel, another important consideration is the drainage layer, or how the water will be conveyed and discharged from the drains. In most cases, a drainage blanket made of a granular material is used. Synthetic or strip drains may also be laid horizontally along the surface of the installation and then connected to each PVD to allow for a clear drainage path without any head loss. The strip drains may then be outletted in gravel ditch drains.
If sand or gravel is used, the drainage blanket can also be used as a working platform to support equipment for PVD installation. The sand or gravel should be clean and washed. The design of this drainage layer is based on the materials’ ability to transport the excess pore water without head loss. Sand should have a thickness of between 1.5 to 3 feet (with a minimum of 1 foot). If it is applied directly over soft soils, at least 1 foot of extra thickness should be added to reduce the risk of contamination. Alternatively, a geotextile separator may be used.
If a strip drain material is used instead of a drainage lawyer, there are several techniques that may be used. In most cases, a strip drain is attached to each individual PVD. However, a single strip drain can be used for as many as 3 rows, with each PVD connected to each strip drain.
The stability of the working surface will impact the thickness of the granular blanket used. Generally, the less stable the surface, the thicker the granular blanket should be to support the PVD installation equipment. Alternatively, the drainage blanket may be reinforced with geotextiles and/or geogrids. This can both provide stable working surface and minimize the thickness of the drainage layer.
When PVDs are installed on uneven surfaces, the effectiveness of the drainage layer and overall stability should be considered. The working surface may need to be altered to allow for the installation of PVDs, such as a benching procedure. This can disrupt the continuity of the drainage blanket. To make sure that the layer works as it should, the drainage layer should be outletted.
Design of Vertical Drains
The main objective of soil preloading — whether vertical drains are used or not — is to reach a disked degree of settlement within a specified period of time. The design of vertical drains is based on the use of fill or surcharge to preload the site soils and PVDs to reduce the length of the drainage path to achieve this goal. On some sites, vacuum consolidation may be used as well.
Preloading site soils to accelerate consolidation requires time to allow the excess pore pressures to dissipate, and for the soils to settle. PVDs will shorten the drainage path and speed up the settlement. To properly design a PVD installation, an engineer must understand the type and extent of the foundation soils as well as their engineering properties. An analysis of these soils must include factors such as predictions of the amount and rate and settlement and the stability of the embankment throughout construction.
The design of a PVD system should begin with a traditional settlement analysis to determine both the total and time rate of settlement under final project loads, without the use of drains. A settlement analysis of cohesive soils should be conducted to make this determination.
PVD system design requires selecting the type, spacing and length of the drains to accomplish the necessary degree of consolidation within the appropriate time constrains. The process begins with a settlement analysis without PVDs to evaluate the total magnitude of settlement as well as the time rate of that settlement under the expected final load. If the time to reach 90 to 95 percent of projected settlements is beyond the allowable construction time, PVDs can be used to reduce the time for settlement to occur.
If several layers of compressible layers of soil are present at a site, each lawyer should be evaluated separately to determine its effect on total consolidation. Computation of the settlement and time rate of settlement can be performed on each layer to determine if sufficient consolidation will occur within a specified time.
To determine PVD spacing, a preliminary calculation should be made using soil index data, including liquid limits and project geometry. This includes the area of loading, depth of compressible strata, and if excess surcharge will be necessary. If the desired percentage of consolidation has been established through testing of a preliminary design, the designer can use a computer program to determine final spacing of the PVDs.
Construction Specifications and Control
The design, installation, and construction of PVDs are well understood, with a track record of successfully completed projects over the past decades. Construction equipment, methods and material are all well-established for this type of work. For this reason, method specifications are typically used for this type of ground modification.
Specifications are used to reduce problems, cost, and risks associated with PVD installations. They also help to make sure that the installation achieves the intended objective. To accomplish this, a designer will detail the spacing, extent and length of the drains as well as the details of the drainage blanket as well as the horizontal discharge drains. In most cases, end result specifications are not included.
The specifications should provide the installer with as much flexibility as possible in order to achieve the desired result. They should include both quality control and assurance procedures, such as initial installation of trial drains to establish standard procedures. Materials and procedures should be carefully inspected for compliance.
As discussed above, a benefit of using PVDs as a vertical drain system is that quality assurance is relatively straightforward. After trial drains have been completed, inspection involves simply recording the depth and location of each drain, observing splices and verticality of equipment, taking material samples for testing, and noting any variances in the procedure.
The drains must be installed in accordance with the plans and specifications to ensure proper performance. The monitoring personnel should be familiar with both the contract drawings and specifications, and understand the goal of the PVDs. The drainage blanket material quality, embankment placement and compaction and the surcharge loading rate should also be monitored throughout the process.
Site Preparation
To prepare the site for installation of PVDs, the area should be cleared, excavation and/or filling operations should be performed to bring the site to grade and a working platform or drainage blanket should be constructed. The grade should not be so steep that surface drainage will erode the blanket; the drainage blanket should be continuous.
During construction, the field inspection personnel should monitor the location for any unusual soil movements. This may indicate mud waving or even a potential failure.
Field Observations
After verifying that the equipment and materials comply with the specifications, field inspectors should monitor the verticality, depth of installation, and location/placement of the drains. While most projects specify an estimated depth, there may be local variations from this estimate. Nevertheless, the depth of the PVDs should not vary significantly from adjacent drains.
Before the PVD material is installed, it should be observed visually to ensure that it comports with the plan specifications. Both the core and the filter jacket should be continuous, and should not be damaged.
Inspection personnel should also make sure that the installation equipment complies with the specifications in the contract. This includes mandrel shape, size, and stiffness, anchor type and size, penetration method, method to measure and determine penetration depth, means and procedures for pre-drilling (if necessary) and method to measure and record installation force. Trial drains should be installed to evaluate the equipment on all projects.
Instrumentation Monitoring and Construction Control
Filed instruments can be used to monitor the performance of the PVDs, and may also be used to potential control the rate of construction of the embankment and/or surcharge. These instruments may include piezometers, settlement platforms and gauges and/or inclinometers.
Settlement measuring devices, such as platforms, deep settlement points, or horizontal deflection devices, can be used to measure the rate and total amount of consolidation. Inclinometers are used to warn against potential stability failure by measuring horizontal deflection with depth. Pore pressure devices, known as piezometers, can be used to calculate achieved consolidation rate and to determine if there is an executive build up of pore pressure, which may be an indication of potential failure.
To ensure a successful project, both the proper selection of instrumentation devices as well as frequent monitoring are important. The type of instrumentation used is based on the needs of the project. For example, if stability is critical, pore pressure measurements and measurements of horizontal deformations are both important.
Determining Cost
In many construction estimates, the cost of a PVD project is based on the unit cost of the installed PVDs, instead of the total cost that includes other items. A number of factors may affect the total cost of a PVD system, such as preload and surcharge materials, obstructions, installation methods, and allowable consolidation time. The unit cost of installation is just one factor that impacts the total cost.
Significantly, many of these factors are difficult to quantify. For this reason, these costs may be included in other bid items. For example, project topography may affect the cost of a PVD solution. Significant earthwork may be necessary on sites where there is great variation in grade in order to provide a level working surface for PVD installation. Similarly, the availability and cost of granular material can determine whether a granular blanket will be a more economical choice than a geosynthetic strip drain. In some cases, the granular blanks may be necessary for a working platform, even if it is the more expensive option.
Obstructions and dense soils will substantially increase the cost of a PVD solution. For this reason, the engineer should correctly identify both the soils to be penetrated as well as the need to achieve a particular depth, taking into account very stiff layers and possible obstructions.
While most contracts specify the installation method, installers should be given flexibility in choosing the type of equipment for installation. In this way, the most cost-effective solution can be used if and when difficulties arise. A specification that allows static, static vibro and vibro-type installation will typically allow for the most economical solution, with jetting only permitted on approval of the engineer. Impact methods should not be permitted.
The typical cost of PVD installations may vary significantly based on these and other variables. For projects of up to 50,000 lineal feet, $0.70 to $4.00 per lineal foot is a typical price range. In contrast, a project of 50,000 to 300,000 lineal feet may be priced at $0.50 to $1.00 per lineal foot, while a project of over 300,000 lineal feet may be priced at $0.30 to $0.50 per lineal foot. Importantly, these typical costs are for standard projects, where special equipment is not needed and there is no difficulty in penetration.
In addition to the unit installation cost per lineal foot, there is typically a mobilization charge of anywhere from $15,000 to $25,000 per rig, plus the cost of the drainage blanket and instrumentation. The total cost could be much higher in areas where there are labor shortages or severe weather, or if there are difficult site conditions.
Vertical drains are just one of many methods of ground modification. As an economical way of accelerating consolidation, it is an important option for contractors working on sites with unstable or marginal soils. Additional methods will be explored in future articles in this series.
View the complete article here.
How do vertical drains contribute to ground modification?
Vertical drains expedite water drainage, accelerate consolidation, and improve soil stability in deep foundation projects.
What is accelerated consolidation, and why is it essential in ground modification?
Accelerated consolidation is a rapid process of reducing soil settlement, crucial for stabilizing foundations quickly during construction, and it's achieved through techniques like vertical drains.