Hoisting & Rigging – Part III: Operator and Crew Member Safety
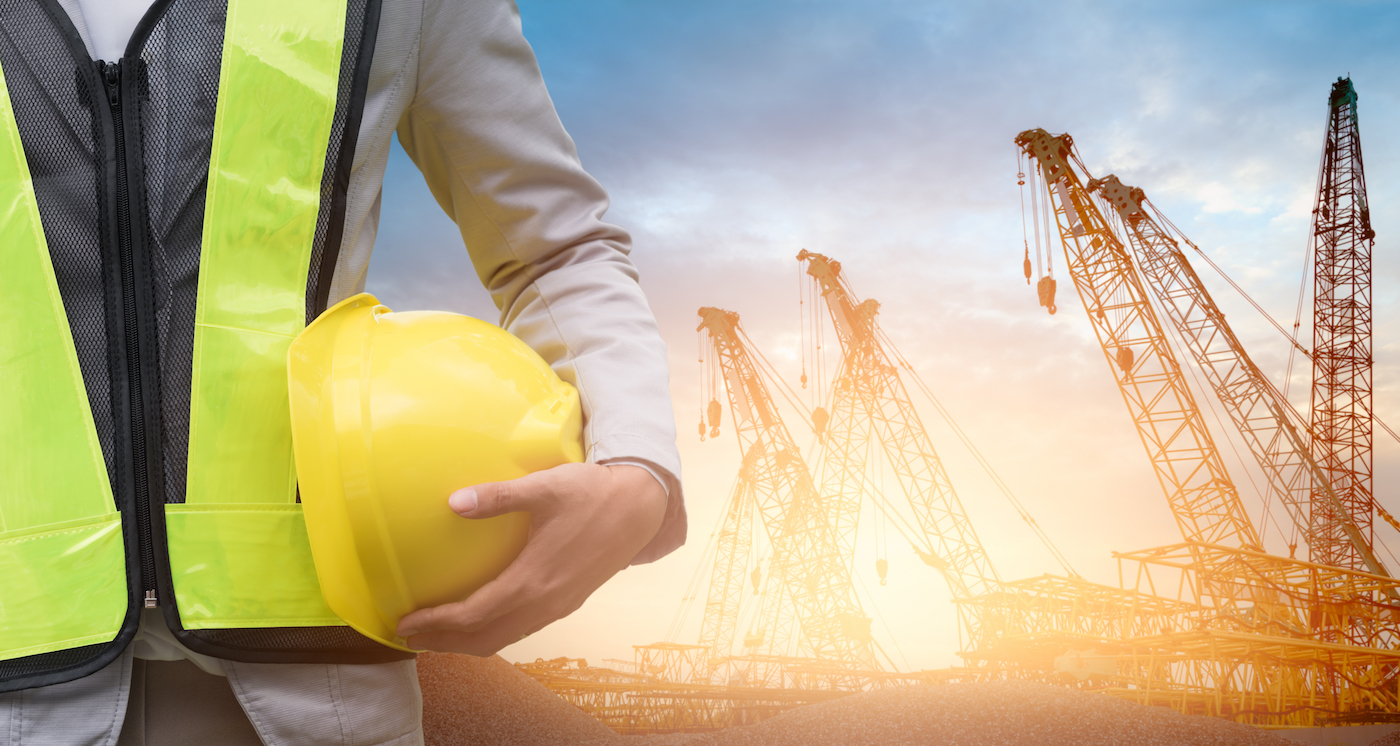
When conducting both ordinary and critical lifts, an operator and signal person must be familiar with all crane or hoist operating characteristics and related safety rules. While general practices vary based on the circumstances of each lift, some standards always hold true.
Regardless of lift type, the most important step in any rigging operation is determining the weight of the load to be hoisted. If this information can’t be obtained from shipping papers, design plans, or another dependable source, the operator may have to calculate the weight.
Determining load angle factors is also important, as this will dictate how the load is carried by slings.
To obtain a load angle factor and the proper sling tension, an operator must first define the load’s designated pick point. Measurement of the sling’s length and the vertical height from the horizontal plane of the load to the point where the sling attaches to the suspended hook should follow.
Dividing the slings length by the vertical height will result in the load angle factor, which is then to be multiplied by the portion of the weight placed to the pick point. The result is the total stress that can be applied to the sling.
Ordinary Lifts
Hoisting and rigging operations for ordinary lifts require that a designated leader be present at a site during an entire lifting operation. If a lift is being made by only one individual, that person assumes all responsibilities.
Once the load weight is determined, the leader will select the proper equipment and accessories, ensuring the rated capacity is not exceeded. Before starting operations, this individual will survey the lift site for unsafe or hazardous conditions, and ensure that all equipment is properly set up, positioned, and inspected.
Confirming that all personnel involved understand how a specific lift is to be made represents another crucial requirement of the leader.
Once lifting commences, the leader should direct all operations, stopping a job if an accident, injury, or unsafe conditions occur.
Critical Lifts
A lift should be deemed critical if a collision or load drop would significantly delay a project, jeopardize future operations, release radioactive chemicals, or put personnel at unacceptable risk of injury.
Before conducting critical lifts, a pre-lift meeting involving all participants must be held. During this conference, the entire lift plan must be reviewed and all questions resolved. Included in the plan should be an identification of all items to be moved, including their weights, dimensions, and centers of gravity. The presence of any hazardous or toxic materials must also be acknowledged in the plan, along with an identification of all operating equipment and its rated capacities.
Workers should also review a detailed rigging sketch that properly recognizes all its components, along with their rated capacities. These components include slings, lifting bars, accessories below the hook, load indicating devices, load vectors, lifting points, sling angles, boom and swing angles, attachments, and crane orientations.
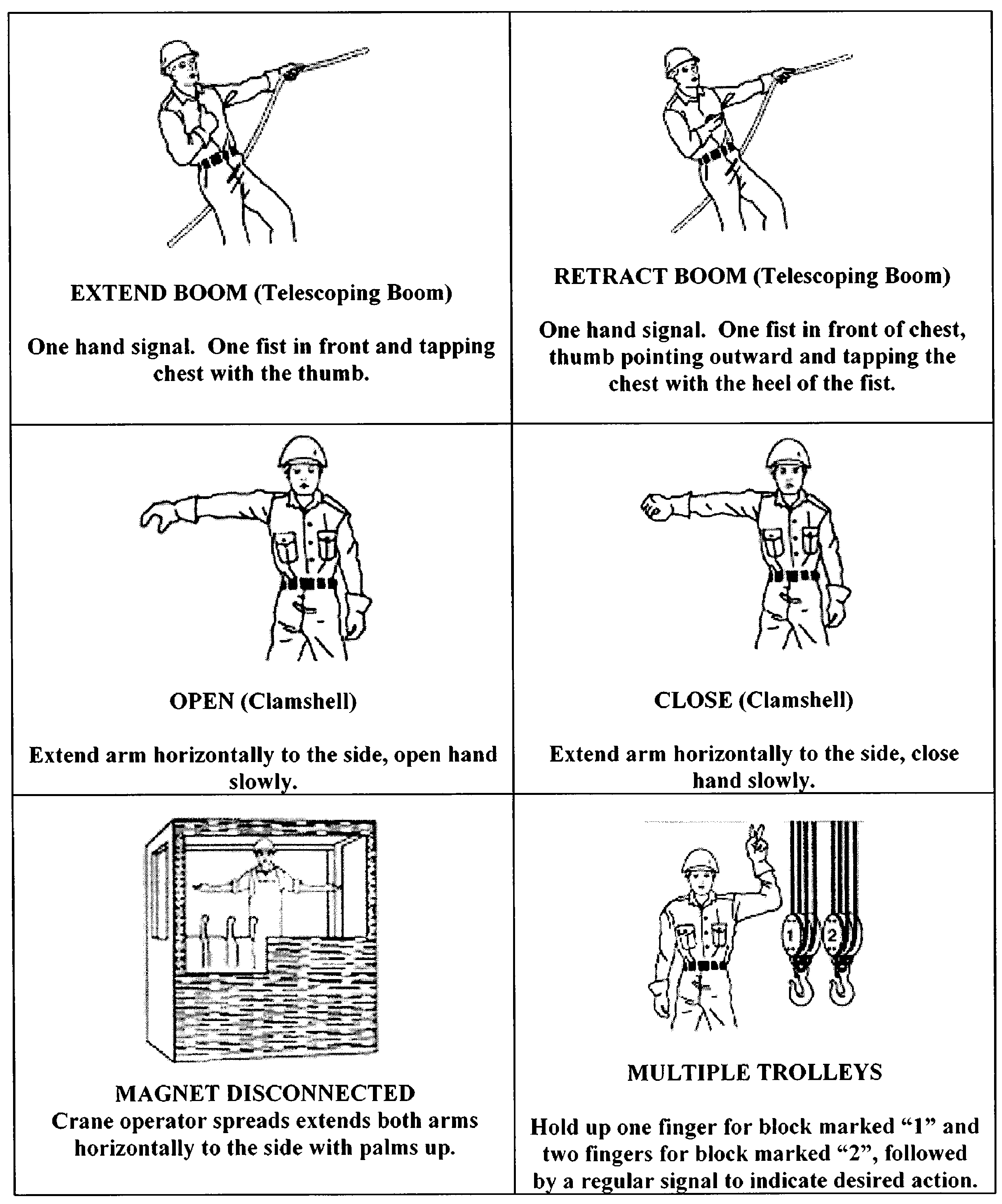
Moving the Load
Prior to the lifting of any weight, many tasks are required of the operator and designated signal person; however, both should confirm that no crane, hoist, or rigging hardware is loaded beyond the rated capacity.
The operator must ensure the hoist rope or chain is free of kinks, and that multiple-part lines are void of twists around each other if the load line is slack. This person must also confirm that the line sits on the sheaves as slack is removed and that the load line is plumb to prevent side pull.
Two degrees of plumb line is considered excessive, as it introduces stresses in the crane that were not necessarily accounted for during its design. These additional stresses may result in the bridge or trolley brakes holding the load, which can damage the rope as it runs up the side of a sheave or drum.
The signal person must verify a load is well secured and balanced in the sling or other device, while also confirming that the load path is clear of any obstructions. When utilizing a mobile crane, accessible areas within the swing radius must be barricaded off in order to prevent an individual from being struck or crushed.
When working around any powerline, a signal person must identify a location where he can safely stand and warn the operator when any part is approaching the minimum safe distance of 10 to 50 feet, depending on the line voltage. Of note, the most repeated killer of riggers is electrocution caused by the contact of the boom, load line, or load of a crane with electrical power lines.
During initial load application, the operator must first lift the load only a few inches. At this time, brake function, load balance, and sling/rigging hardware integrity can be checked. During this stop, there must be no downward drift of the load. Additionally, never raise the load higher than several inches at this stage.
When conducting outdoor operations, wind speed must be considered, as the load or hook is not permitted to swing during crane travel or hoisting. If wind speeds of more than 25 mph are encountered, operations should be halted. The conditions must be evaluated by a qualified person to determine if the size, shape, and weight of the load can be safely lifted moving forward.
During power hoisting, engage the load in a controlled, deliberate manner, ensuring that there is no sudden acceleration or deceleration of the load. Quick reversals, along with sudden acceleration or deceleration, creates a shock loading situation, which can easily cause the load tension on the crane, hoist, and rigging equipment to double.
When lifting weight, the safest method for a rigger to control a load suspended from a hook is via a tagline or restraining device, as these will give the rigger the distance needed should the load shift or move unexpectedly.
Taglines should be placed at points on the load during lift-off, traveling, and placement, with the person responsible for placement never looping the line around his/her arm or body. This person should have a clear view of the travel path and the signaler so that the load’s movement can be better anticipated. Additionally, the tagline person should trail the load while traveling with it to ensure optimum control.
An operator must never carry loads over people or perform work on a suspended load. All personnel, including the rigger, must remain clear of the load until it naturally settles. Once the load is within its final placement, it may be adjusted by hand.
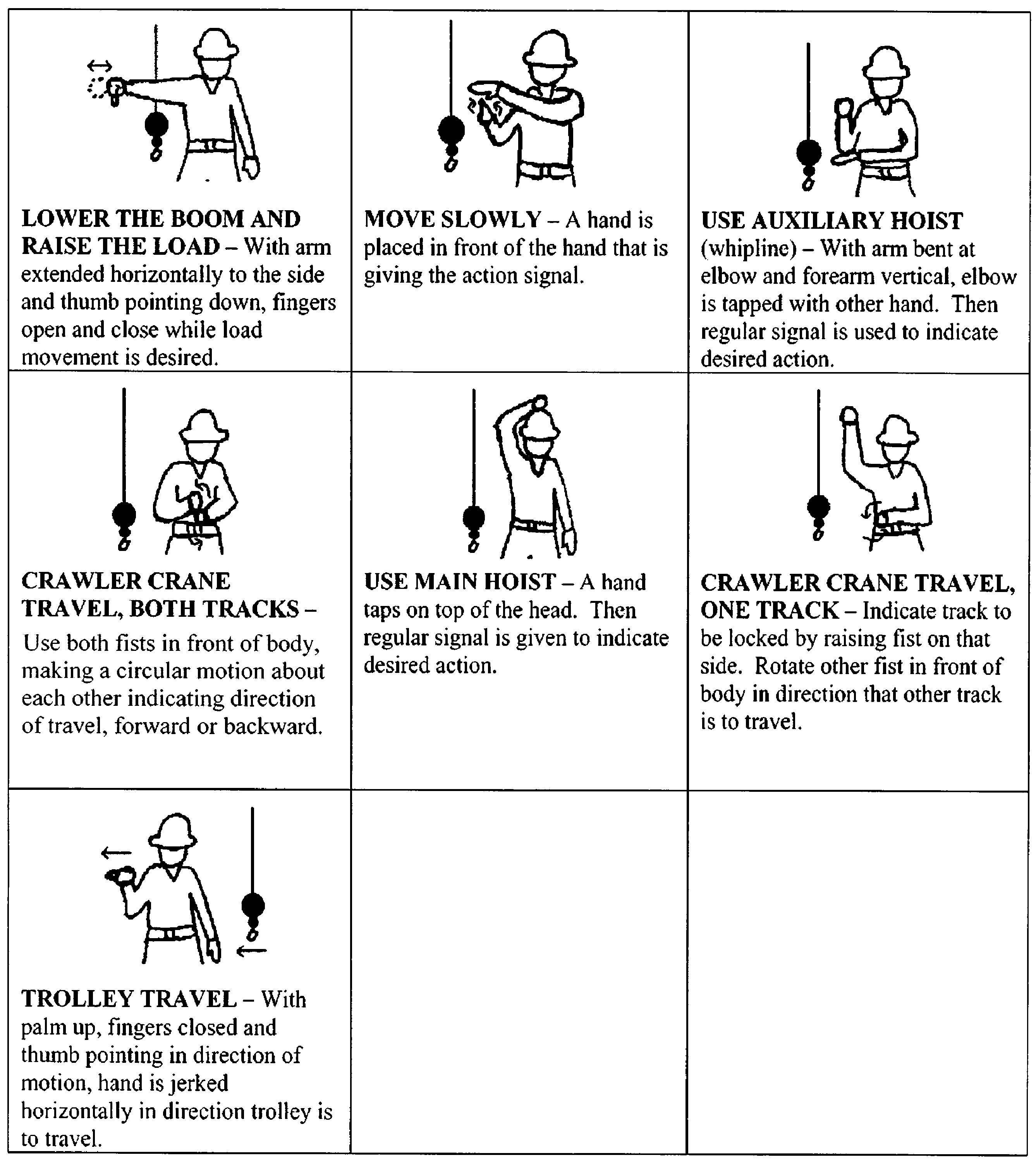
Hand Signals
Standard overhead crane and hoist hand signals adopted by ANSI standards are always to be followed, with no movements made unless all signals are clearly understood by both the operator and the signal person. The operator should generally respond to signals only from the designated person, but a stop signal should be obeyed regardless of who gives it.
All persons acting as signalers during operations should be clearly identified to the crane operator via an orange hardhat, orange globes, or an orange vest. In situations where the crane operator can’t see the signaler, a relay signaler shall be stationed in view of both the signaler and the crane operator.
If the operator can’t see the signaler when operating in the blind, then radio communication should be implemented. Voice communication should only occur between the two individuals, not through a third person.
When communicating with an operator, a signaler must exaggerate all signals, making distinctive moves when choosing to stop one command and go to another action. The signaler must also train himself or herself to perform these signals in an exact, repeatable fashion, which will reduce or eliminate confusion between the two parties.
Included below is a list of standard hand signals and how to properly make them. For the most updated signals, it is advised that workers review American National Standards Institute manuals based on the specific type of crane or hoist being utilized for their lift.
Hoist: Extend one forearm vertically and point the forefinger upwards. Move the hand in a small horizontal circle.
Lower: Extend one arm downward with the forefinger pointing down. Move the hand in small horizontal circles.
Bridge Travel: Extend one arm forward with the hand open and slightly raised. Make a pushing motion in the direction of travel.
Trolley Travel: With the palm up, fingers closed, and thumb pointing in the direction of motion, jerk one hard horizontally.
Stop: Extend one arm palm down. Move the arm back and forth. When signaling for the operator to travel on an overhead crane, anticipate and give this signal in advance so the load doesn’t pass beyond its landing spot. Again, the stop signal must be recognized and followed by the operator regardless of who gives it.
Emergency Stop: Extend both arms with palms down. Move arms back and forth.
Multiple Trolleys: Hold up one finger for block marked 1 and two fingers for block marked 2. Apply regular signals.
Move Slowly: Use one hand to give any motion signal, with the other hand motionless in front of it.
Proper coordination between operator and signal person will always be a fundamental component of any lift. Both parties must maintain a clear understanding of what is required of them prior to, during, and after a critical or ordinary lift if a job is to be conducted in a safe and efficient manner.
How do you determine the weight of a load for hoisting when the information is not readily available?
If load weight information isn't available, the operator may have to calculate it using methods like checking shipping papers, design plans, or other dependable sources.
What precautions should be taken when conducting outdoor hoisting operations in windy conditions?
Wind speeds over 25 mph require operations to be halted, and a qualified person should evaluate if it's safe to proceed based on the size, shape, and weight of the load.