Waterfront Facility Inspection: Part II – Planning for Inspection
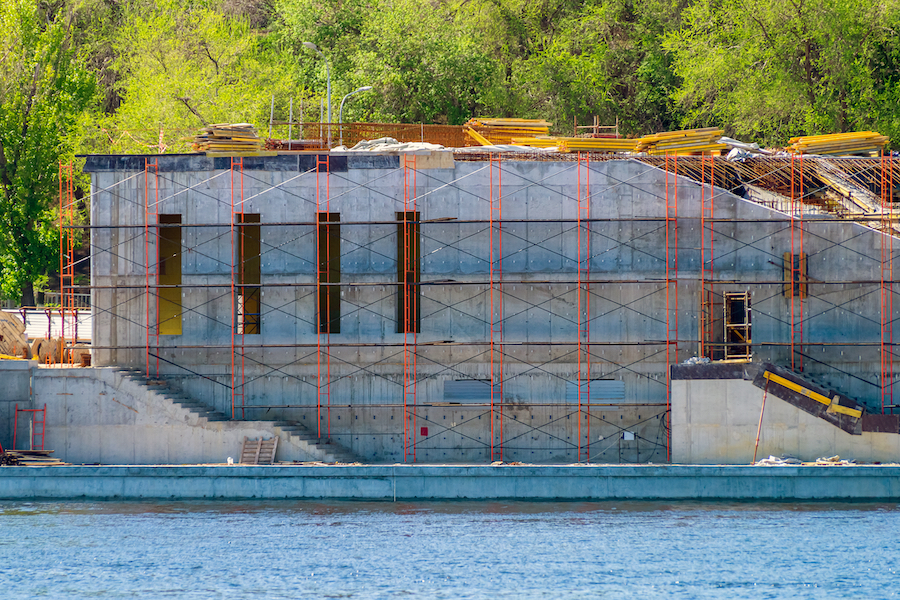
View the complete article here
5-3 PLANNING FOR INSPECTION
The levels of inspection to be used for a particular task must be decided early in the planning phase. The inspection objectives (i.e., baseline, design survey, repair acceptance, research) should be clearly defined. A site survey of the facilities should be obtained, or conducted if doing a first-time inspection. A site survey for underwater inspections includes: bathymetric, oceanographic, and geological data, as well as information on nearby obstructions or activities. A site survey accelerates the planning process and will help determine the levels of inspection to be used.
The time and effort required to carry out the three different levels of inspection are quite different. The time required also depends on whether the inspection is surface or underwater; on environmental factors, such as visibility, currents, wave action, water depth, tides, severity of marine growth; and on the inspector’s skill and experience.
Level III inspections depend on the extent of existing damage, the type of inspection techniques, and the equipment used (ultrasonic thickness measurements, increment borings, caliper measurements). Therefore, estimates of time for Level III inspection are not included in Table 5-2.
5-3.1 Inspection Frequency
The frequency of routine or periodic inspections will depend on whether the inspection is on the surface or underwater, and the expected rate of deterioration and damage. An example of an area requiring more inspections is ships berthing, which deteriorates both fender and bearing piling. The frequency and level of inspection should, therefore, be closely tied to the historical deterioration rate of the facility. Statistical software has been developed that identifies inspection frequencies based on cost when known or estimated structural data. The frequencies obtained will be unique to the activity’s situation (from NCEL CR 87-005, Inspection Frequency Criteria Models for Timber, Steel, and Concrete Pile Supported Waterfront Structures, December 1986.) As a general guide, recommended frequencies of inspection for the different types of waterfront structures are:
- All superstructure and piling/sheet piling above the waterline, including the splash and tidal zones (Figure 5-1), should be inspected annually.
- Concrete/steel structural members at the splash/tidal zones (Figure 5-1) and downward should be inspected at least every 6 years. As deterioration is discovered, the level of inspection and frequency needs to increase accordingly. For steel structures, the age of the structures is a primary factor since the rate of deterioration due to corrosion is fairly constant. Likewise, concrete in a saltwater environment deteriorates chemically with time, especially if cracks are present to allow the seawater to reach the structure’s interior.
- Timber members should be inspected at least every 3 years and, as above, more frequently and intently as deterioration is discovered. In areas where marine animal infestation is known to be a problem, increased inspections are especially important.
If it is not feasible to thoroughly inspect all elements of a structure (e.g., underwater inspection of a series of piers with many piles), selecting an optimum number of structural elements or members is crucial to obtaining accurate information representative of the overall condition of the structure. Development and validation of sampling criteria and procedures has been reported in Naval Civil Engineering Laboratory’s TN-1762 Sampling Criteria and Procedures for Inspection of Waterfront Facilities, September 1988. Statistical sampling techniques using probability theory provide a method for determining condition parameters for the entire population based on information from the sample elements, with a calculated confidence level and precision.
5-3.2 Inspectors
Inspections may be by a variety of individuals at different times for different reasons. It should be notes that periodic comprehensive inspections are done as part of the Underwater Inspection Program administered by the Naval Facilities Engineering Service Center, East Coast Detachment.
5-3.3 Collecting Inspection Plan Data
Before starting an inspection, all available information about the facility should be gathered. This includes prior maintenance and inspection records, facility drawings and site survey reports, general background information, and environmental data, including:
- Atmospheric temperature range
- Water temperature range
- Tidal range
- Water depths
- Water visibility
- Currents
Any condition could have a direct impact on the time required to perform an inspection, such as: the amount of biofouling growth on piles; ice; or seasonal flooding. Any other unique feature or special problems that may be encountered should also be noted.
The inspection plan should include CADD drawings showing individual piles and other structural members. The inspection could use pile numbering/designation systems often available on existing “as-built” drawings. Usually, combinations of numbers and letters are used with the number designating the bent and letter indicating the pile within the bent. CADD drawings should also be developed for the above and below deck portions of the pier. The existing positions of all topside bollards, bitts, cleats, capstans, utility covers, as well as any under deck utilities and fittings should be shown on the CADD drawings. A legend should be created to represent such things as the:
- Degree of deterioration of individual structural members
- Level of inspection given to designated portions of a facility
- Shape of individual piles
- Type of materials
- Condition of bollards and bitts
Pile plans should be prepared for piers showing the lengths, widths, and spacing of bents. The plans must also include the numbering system used in the inspection and in the report, and these must be correlated with existing drawings of the facility. Also include design live load data on all pile plans, if available. Load testing of the pier decking, if heavy equipment or vehicles are driven onto the pier, should be considered.
Particular attention should be paid to mooring hardware as it relates to safe mooring of naval vessels during heavy weather. A more thorough treatment of this topic is contained in UFC 4-150-08, Inspection of Mooring Hardware.
5-3.3.1 Developing Inspection Plan
Once the information about the facility structure and environment has been collected, an inspection plan is developed. The plan should be based on the inspection objective and the level of inspection required to meet that objective. It is important to select enough inspection areas per structural member. The written plan should be similar to a statement of work (SOW) specifying the sampling criteria, tasks, schedules, equipment to be used, and any additional responsibilities. The inspection plan must be prepared by a qualified engineer who is familiar with the structure.
The plan must specify that a qualified diver supervised by a qualified engineering diver should conduct the underwater inspections and an experienced engineer must perform the structural assessment of the entire pier.
5-3.4 Equipment and Tools
5-3.4.1 Surface Cleaning Tools
To perform a Level II and Level III inspection, the marine growth on the structure must be removed. How this is done depends on the surface support available. For small sample areas, wire brushes, probes, and scrapers may be adequate. For larger areas or more detailed inspections underwater, a hydraulic grinder with barnacle buster attachment, or high-pressure water jet gun, may be used. Take care to prevent damage to pile wraps or coatings and to the preservative-treated layers of timber or deteriorating surfaces of concrete.
5-3.4.2 Inspection Tools
Inspection tools and equipment include:
5-3.4.2.1 Hand-Held Tools
- Portable flashlight, ruler, and tape measure for documenting areas
- Small or large hammers or pick-axes for performing soundings of the structural member
- Calipers and scales for determining thickness of steel flanges, webs, and plates, or diameters of piling
- Increment borer and T-handles for extracting core samples from timbers
- Chipping tools for prodding the surface of the concrete to determine the depth of deterioration.
5-3.4.2.2 Mechanical Devices
Mechanical devices including a Schmidt test hammer for measuring concrete surface hardness and rotary coring equipment for taking core samples from concrete structures.
5-3.4.2.3 Electrical Equipment
This includes electrical equipment, such as an underwater voltmeter for determining the level of cathodic protection on steel structures and underwater sonic and ultrasonic equipment for detecting voids in concrete and thickness of structural steel. It also includes underwater magnetic particle testing to locate and define surface discontinuities in magnetic materials. Figure 5-2 shows typical equipment applications used in underwater inspections.
5.3.4.3 Recording Tools
Recording tools and equipment are required to provide a complete documentation of the condition of the structure. Simple tools such as a clipboard, forms, and cassette recorder for above water inspections; or Plexiglas® slate and grease pencil for underwater inspection, provide the basic documentation tools. More in-depth documentation may be obtained with above water or underwater photography using either colored still-frame cameras, colored video, or closed-circuit television. The latter may be very valuable in expediting major underwater inspections. For underwater inspections in turbid water, a clear-water box may be fitted to the lens of the photographic or video equipment to improve visibility between the lens and surface to be inspected.
5-3.5 Preparing Inspection Documentation
For the information to be useful, documentation must be clear and concise. Inspectors should maintain daily logs of inspection details including measurement data, locations of observation, and water depths, if relative. Fill out inspection forms as the inspection progresses, and complete the reports soon after the inspection has been finished. Standard forms and report formats facilitate the documentation procedure and are essential for comparing the results of the present inspection with past and future inspections. Figure 5-3 is a standard form that may be used for reporting the condition of piles; Figure 5-4 is an explanation of the condition ratings for concrete piles used on the form; and Figure 5-5 is an explanation of the condition ratings for timber piles. Steel pile inspection results are usually recorded in terms of remaining metal thickness.
When appropriate, visual inspection should be documented with still photography and closed-circuit television. Still photography provides the necessary high definition required for detailed analysis, while video provides a continuous view of the inspection. All photographs should be numbered and labeled with a brief description of the subject. A slate or other designation identifying the subject should appear in the photograph. Video tapes should be provided with a title and lead-in describing what is on the tape. The description should include the inspection method used, the nature and size of the structure being inspected, and any other pertinent information.
View the complete article here
Why is planning important in waterfront facility inspections?
Planning is crucial in waterfront facility inspections as it helps to identify the specific components that need inspection and establish the inspection frequency. A well-planned inspection will consider the type, age, and usage of the facility, local environmental conditions, and past maintenance records to prioritize inspection activities and allocate resources effectively.
What steps are involved in planning a waterfront facility inspection?
Planning a waterfront facility inspection involves several steps. Firstly, one must conduct a thorough review of the facility's documentation including construction plans, previous inspection reports, and maintenance records. Then, an inspection plan should be created that outlines the inspection's scope, methodology, and frequency. This plan should also include contingency measures in case of unexpected findings during the inspection.