Why Use Casing Oscillators for Challenging Ground Conditions?
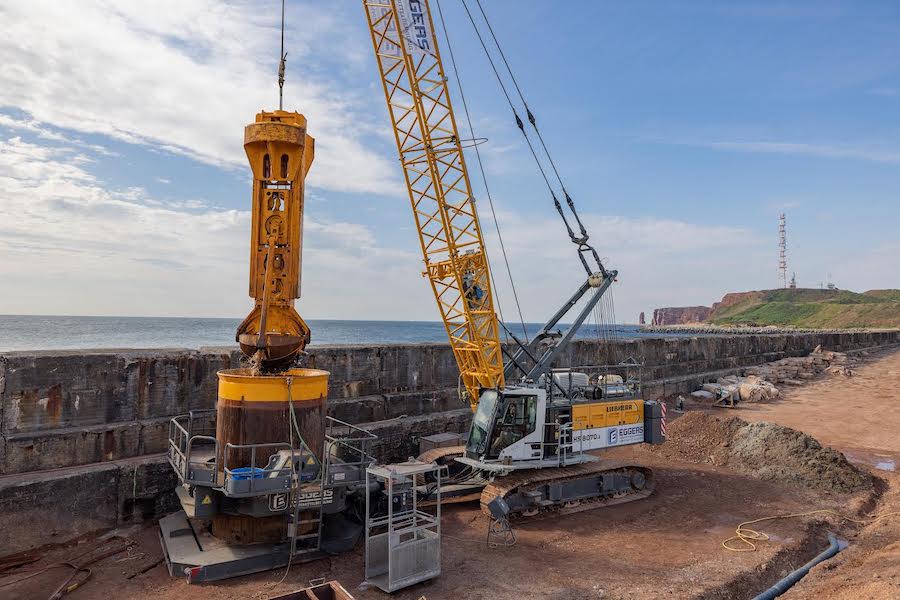
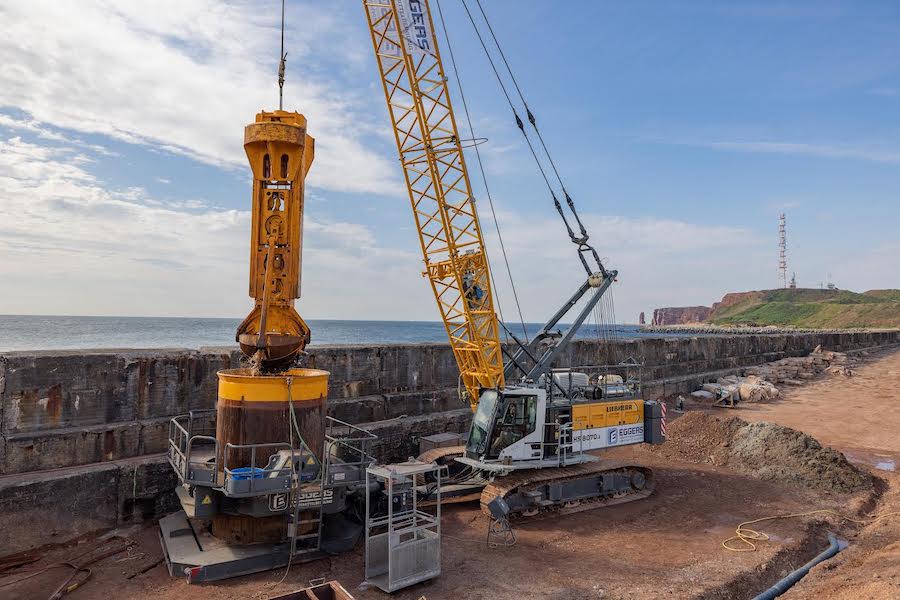
View the complete article here.
Traditionally, rotary drilling has been—and still remains in many cases—the go-to method for many foundation projects. While effective in many contexts, this method has its limitations—limitations in which the casing oscillator offers solutions. Instead of relying on hammering or vibration, casing oscillators use rotational force to drive the casing into the ground—allowing for precision even in the most challenging terrains.
What are Casing Oscillators?
At its core, a casing oscillator is a mechanical device designed to facilitate the drilling process. Unlike traditional methods that apply vertical force, a casing oscillator provides rotational force to the casing. This allows it to bore into the earth with a twisting motion, cutting through obstructions and dense layers more efficiently.
The mechanics are fairly straightforward: the oscillator is mounted onto a crane or a dedicated rig. Once activated, it grips onto a casing—a large, tubular structure—and rotates it. This rotation, combined with downward force, enables the casing to penetrate the ground—with the oscillatory motion easing its passage through challenging terrains.
Key Aspects of Casing Oscillator Equipment
Casing oscillators come with a range of features tailored to specific tasks.
Size & Type
From compact oscillators suited for smaller urban projects to massive units designed for large-scale undertakings, there’s a spectrum of sizes and types. The choice depends on factors like borehole diameter, depth, and the project’s overall scale.
Control Systems
Modern casing oscillators come equipped with state-of-the-art control systems. These technological advancements enhance the precision of drilling, ensuring the oscillator adheres to the designated path. Moreover, many of these systems have in-built safety features—reducing the risk of operational hazards.
Durability
Given the demanding environments in which they operate, casing oscillators are built for resilience. Their design considerations account for abrasive terrains, hard rocks, and other challenging conditions. High-grade materials and meticulous manufacturing processes ensure they can withstand the rigors of foundation drilling.
Selecting the right casing oscillator equipment requires a comprehensive understanding of the project’s demands and the available features. With advancements in technology and design, modern oscillators are more equipped than ever to address the multifaceted challenges of foundation construction.
Procedure for Using Casing Oscillators
Deep foundation projects employing casing oscillators are methodically planned and executed, ensuring precision and safety at every step.
- Site assessment and planning: Before initiating any drilling—a thorough ground survey is conducted to understand the soil’s composition, identify any potential obstructions, and evaluate groundwater conditions. Based on these findings, the most suitable casing oscillator equipment is selected—ensuring it’s aptly equipped to handle the project’s specific challenges.
- Setting up: Once on-site, the oscillator is carefully mounted onto a crane or a dedicated rig. The entire system is checked for stability and operational readiness. This setup phase is crucial as a well-prepared oscillator ensures efficient and safe drilling.
- Initiating drilling: With everything in place, drilling begins. The oscillator grips the casing and applies rotational force, causing the casing to bore into the ground. The oscillator’s unique twisting motion aids in navigating through dense layers and obstructions.
- Continuous monitoring: During drilling, constant monitoring is imperative. Sensors and visual checks ensure the drill progresses correctly, and immediate action is taken if any anomalies or challenges arise. This real-time vigilance is crucial to maintain the borehole’s integrity and safeguard against potential issues.
- Extraction of soil: As the drilling progresses, the displaced soil within the casing needs to be periodically removed. Various methods, like clamshell buckets or augers, are used to extract the soil—ensuring the borehole remains clean and preventing any blockages.
- Completion: Upon reaching the desired depth, drilling is halted. At this stage, the project’s requirements determine the next steps—which might include introducing reinforcing bars, pouring concrete, or other foundational elements.
- Retrieval: If the project demands it, post-completion, the casing is carefully removed from the borehole. This is done by reversing the oscillator’s rotation and gently extracting the casing, ensuring no damage to the freshly drilled hole or the casing itself.
Each phase of the process requires meticulous attention to detail, reinforcing the importance of expertise and experience when employing casing oscillators in foundation construction.
Why Casing Oscillators for Challenging Ground Conditions?
In the demanding world of foundation construction, the ground beneath our feet is far from uniform. From dense rock layers to waterlogged soils, the challenges can be varied and formidable.
Penetrating Dense Strata and Obstructions
The unpredictable nature of the earth means that often, drillers encounter hard strata or unexpected obstructions like boulders. Casing oscillators, with their powerful rotational force, can navigate through these challenging terrains effectively. Their twisting motion allows them to cut through dense material, making the process smoother and more efficient.
Minimized Vibration
Vibrations during drilling can be more than just a nuisance. In urban areas or near sensitive structures, excessive vibrations can lead to structural damage or even legal complications. Casing oscillators, due to their rotational approach, produce less vibration compared to other methods.
Stability in Loose Soils
In areas with loose or unconsolidated soils, traditional drilling can pose the risk of the borehole collapsing. The design of casing oscillators allows for simultaneous drilling and casing. This means as the hole is drilled, the casing is also installed, providing immediate support and preventing soil collapse. It’s a two-in-one solution that ensures safety and efficiency.
Controlling Groundwater Intrusion
Groundwater can be another significant challenge during foundation construction. In areas with high water tables, there’s a risk of water seeping into the borehole—which can compromise its integrity. Casing oscillators, with their sealed design, can create a watertight seal—effectively preventing groundwater intrusion. This ensures that the foundation remains robust and the worksite stays safe.
However, there are drawbacks to consider…
While casing oscillators excel in challenging terrains, they come with higher initial costs and require specialized training compared to traditional drilling. Their design can sometimes limit depth reach and mobility, and in straightforward terrains, they may be slower than conventional methods. In addition, the oscillator’s continuous rotation in abrasive conditions can lead to quicker wear-and-tear, potentially raising maintenance costs.
Conclusion
While casing oscillators do come with their own set of drawbacks—like higher initial costs and the need for specific training—it’s imperative to weigh these against their unmatched efficiency in challenging terrains—especially in dense strata, urban areas, and places with high water tables. For projects where precision, safety, and minimized disturbance are paramount—casing oscillators prove to be a worthy contender in the array of foundation construction techniques.
View the complete article here.
What are casing oscillators and how do they differ from traditional drilling methods?
Casing oscillators are mechanical devices that use rotational force, as opposed to vertical force, for drilling, allowing for efficient penetration through challenging terrains compared to traditional methods.
What challenges do casing oscillators address in foundation construction, especially in challenging terrains?
Casing oscillators effectively address challenges such as penetrating dense strata and obstructions, minimizing vibration in urban areas, providing stability in loose soils, and controlling groundwater intrusion during foundation construction in varied and challenging terrains.