Underwater Drilled Shaft Testing: Techniques, Challenges, and Best Practices
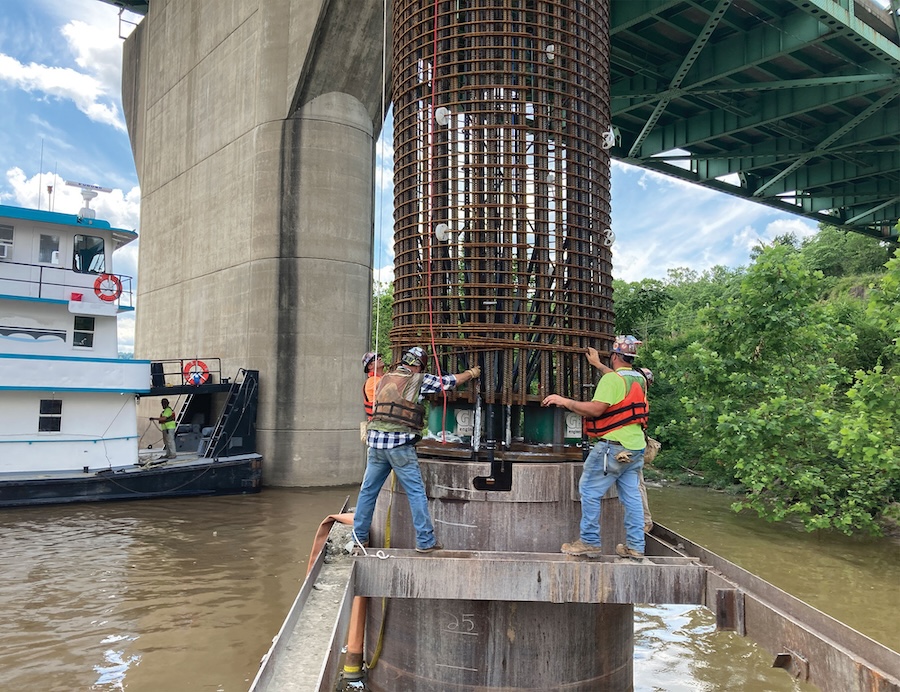
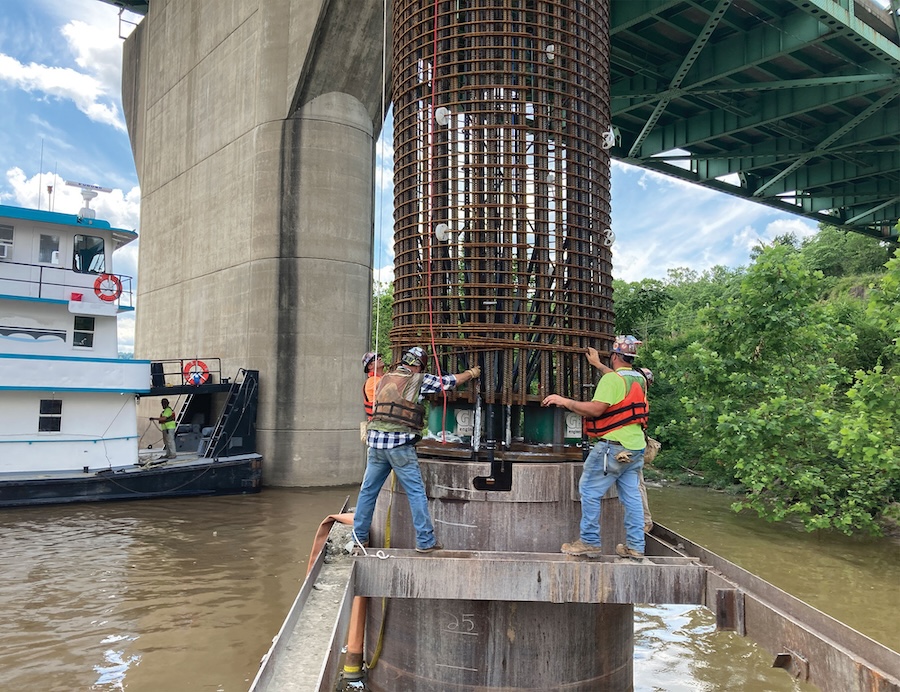
View the complete article here.
Underwater drilled shafts play a vital role in supporting marine infrastructure—such as bridges, piers, and offshore structures. Ensuring their integrity and load-bearing capacity is crucial for the safety and longevity of these projects. While drilled shaft testing is routine in land-based projects, conducting these tests underwater presents unique challenges and requires specialized techniques. In this guide—we’ll explore the different methods used for testing underwater drilled shafts, the challenges involved, and best practices for achieving accurate and reliable results.
Importance of Testing Underwater Drilled Shafts
Drilled shafts transfer loads from structures to stable soil or rock formations deep below the surface. In marine construction, these shafts are submerged—making them more susceptible to environmental factors such as water currents, corrosion, and the impact of aquatic life. To avoid structural failures, it is crucial to conduct thorough load testing of drilled shafts in these conditions.
Methods of Testing Underwater Drilled Shafts
Several techniques are used to assess the load-bearing capacity and integrity of drilled shafts, even when they are submerged. The most common methods include…
1. Static Load Testing
Static load testing is one of the most reliable methods for determining the capacity of a drilled shaft. This involves applying a static load to the shaft and measuring its deflection. For underwater shafts, specialized equipment is used to apply the load and monitor the results from the surface. The shaft is subjected to increasing loads until the point of failure or until the desired capacity is confirmed.
While static load testing provides highly accurate data, it can be expensive and logistically complex for underwater applications. It often requires large cranes or barges to position the testing apparatus above the shaft.
2. Dynamic Load Testing
Dynamic load testing, typically performed using the PDA (Pile Driving Analyzer), is a more cost-effective and faster alternative to static load testing. It involves striking the shaft with a hammer or drop weight and measuring the resulting vibrations and shaft response. The test can be conducted on both the shaft’s tip and along its length to assess skin friction and end-bearing resistance.
In underwater environments, dynamic load testing is advantageous because it requires less heavy equipment and can be performed from a floating barge or a platform. However, the data obtained is often less precise compared to static testing—particularly in complex soil conditions.
3. Crosshole Sonic Logging (CSL)
Crosshole Sonic Logging is a method used to check the integrity of the concrete in drilled shafts. This non-destructive test involves placing access tubes within the shaft before it is poured. After the shaft has hardened, a sonic transmitter and receiver are lowered into the tubes to send sound waves through the concrete. Any inconsistencies in the wave transmission may indicate voids, cracks, or other defects in the shaft.
Underwater, CSL can be more challenging due to water interference—but with proper techniques, it can provide valuable insight into the condition of the drilled shaft.
4. Thermal Integrity Profiling (TIP)
Thermal Integrity Profiling measures the heat generated during the curing process of the concrete to assess the shaft’s integrity. For underwater shafts, this method can be used by placing thermal sensors in access tubes. TIP is particularly useful for identifying variations in shaft diameter or potential anomalies like necking or inclusions in the concrete.
This method is gaining popularity in marine construction because it provides continuous data along the length of the shaft and can be performed relatively quickly.
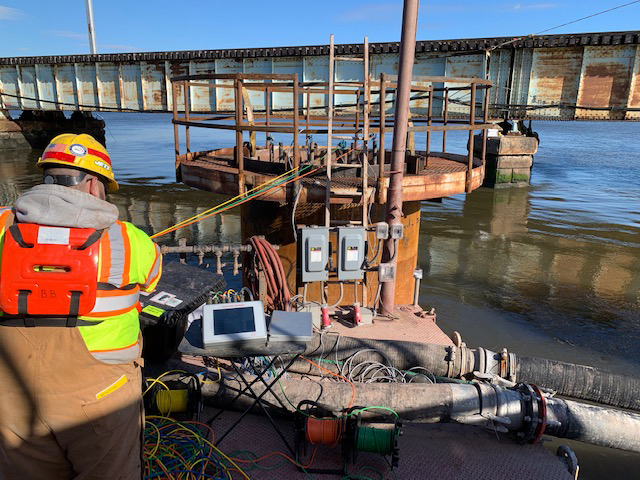
Challenges of Underwater Drilled Shaft Testing
Testing drilled shafts underwater comes with unique challenges that aren’t present in land-based testing. Some of the primary challenges include:
Access to the Test Site
Marine construction sites often require floating platforms or barges to access the drilled shafts. This can increase the complexity and cost of setting up testing equipment.
Environmental Conditions
Water currents, tidal changes, and sediment movement can impact both the drilled shaft and the accuracy of testing data. Careful planning is required to mitigate these factors.
Corrosion and Marine Life
Over time—underwater structures are exposed to corrosion, marine growth, and other environmental factors that can affect the shaft’s structural integrity. This necessitates more frequent testing and maintenance compared to land-based projects.
Visibility and Precision
Testing underwater often requires remote equipment and monitoring systems. Limited visibility, water pressure, and other factors make it more difficult to carry out visual inspections—so more reliance is placed on advanced technologies like sonic and thermal profiling.
Best Practices for Underwater Drilled Shaft Testing
Given the challenges mentioned, the following best practices can help ensure that testing of underwater drilled shafts is both accurate and efficient…
1. Use Specialized Equipment
Invest in testing equipment specifically designed for underwater use. This includes high-pressure-rated sonic or thermal profiling tools and heavy-duty dynamic load testing gear. Equipment designed for marine environments can better withstand the harsh conditions and provide more reliable results.
2. Plan for Environmental Conditions
Careful planning is essential for dealing with tides, currents, and weather conditions. Testing should be scheduled during calm periods, and engineers should account for any potential water movement that could affect the testing results. Monitoring the weather and tidal changes in advance can prevent delays or inaccuracies in data collection.
3. Collaborate with Marine Specialists
Working closely with marine construction specialists and divers experienced in underwater operations is key. They can assist in positioning equipment, navigating environmental challenges, and ensuring the tests are carried out safely and efficiently.
4. Conduct Regular Inspections
In addition to load testing, regularly inspecting the condition of drilled shafts is crucial in marine environments. Periodic testing should be scheduled to monitor the effects of corrosion, marine growth, and other potential threats to the shaft’s integrity.
5. Document and Analyze Data Thoroughly
Because underwater conditions can vary significantly, it’s important to thoroughly document each test and analyze the data in detail. Comparing results over time can help identify trends in shaft performance and guide maintenance schedules.
Final Thoughts
Testing drilled shafts underwater requires specialized techniques, advanced technology, and careful planning to account for the unique challenges of marine environments. By understanding the available testing methods—such as static load testing, dynamic load testing, Crosshole Sonic Logging, and Thermal Integrity Profiling—marine contractors can ensure that their underwater foundations are safe, reliable, and long-lasting.
View the complete article here.
What are the most common methods for testing underwater drilled shafts?
The most common methods include static load testing, dynamic load testing, Crosshole Sonic Logging (CSL), and Thermal Integrity Profiling (TIP).
What challenges are unique to testing underwater drilled shafts?
Challenges include access to the test site, environmental conditions such as currents and tides, corrosion, marine life, and limited visibility for precision during testing.