Template Systems for Pile Driving Applications 101
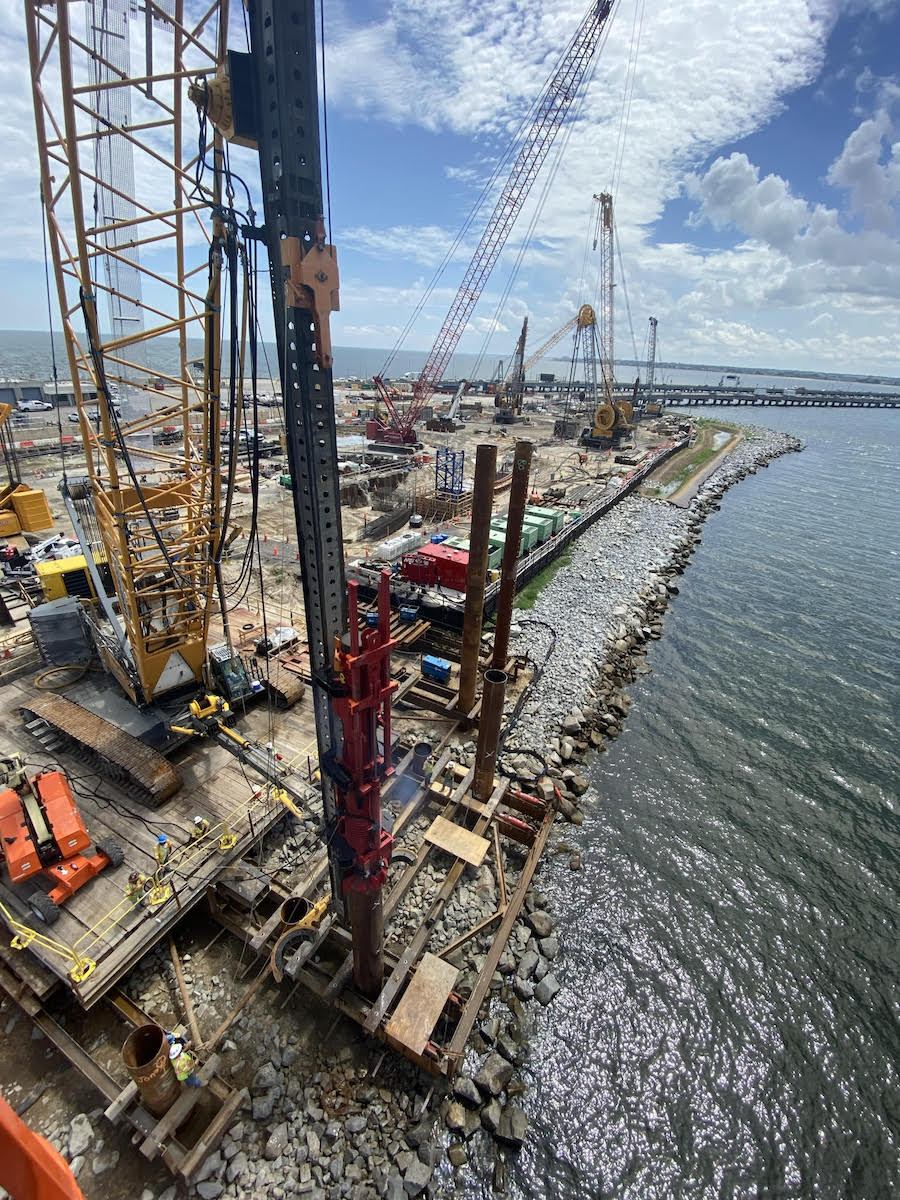
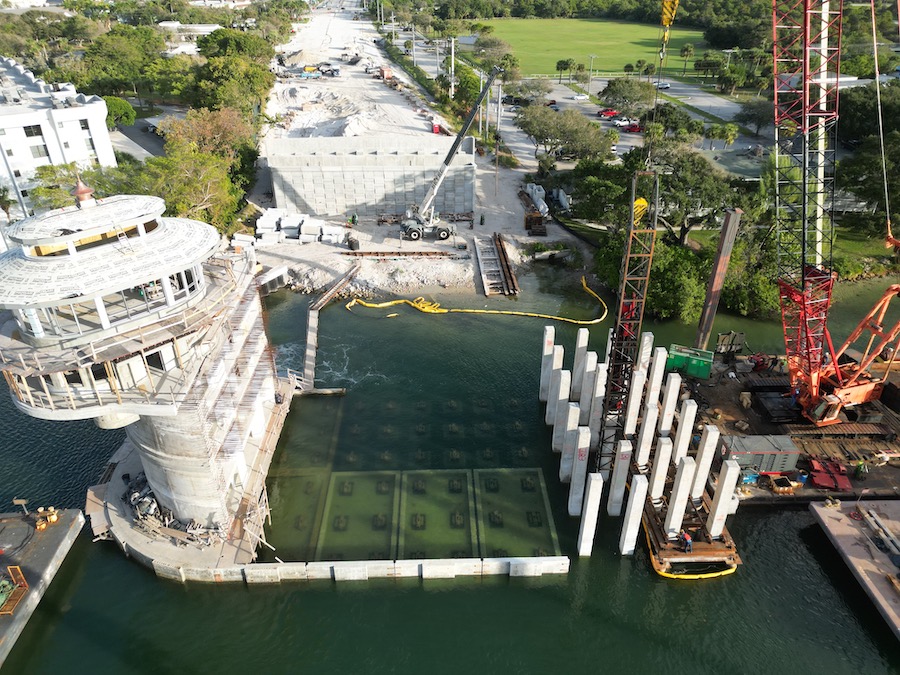
View the complete article here.
The significance of precision in pile installation cannot be overstated. Each pile must be placed at a specific location and driven to a precise depth at a particular angle to guarantee that the load is supported correctly. Deviations from the planned alignment or depth is likely to cause challenges to the issue of workmanship and quality.
For this reason, pile driving template systems are highly recommended to ensure accuracy and efficiency. Modern circular cell cofferdams with flat sheet pile construction, in particular, demand a pre-engineered template system. To form a perfect circle and have the ability to position an exact number of sheets in the diameter requires precision.
Designed to provide guidance and control for the placement and driving of piles, template systems ensure that each pile is accurately positioned according to the architectural plans and specifications. The use of a template system is especially vital in conditions where environmental factors, such as underwater currents or difficult terrain, make precision challenging.
Are template systems utilized in 100% of pile driving operations? No. As a matter-of-fact, it’s common knowledge in the pile driving industry that template systems are not used as often as they used to be—most likely because of lack of attention to quality, as well as impatience. This unfortunate trend compelled us to write this guide—a guide that hopes to inspire a new generation of contractors and engineers to create sturdy, reliable foundations with the use of template systems.
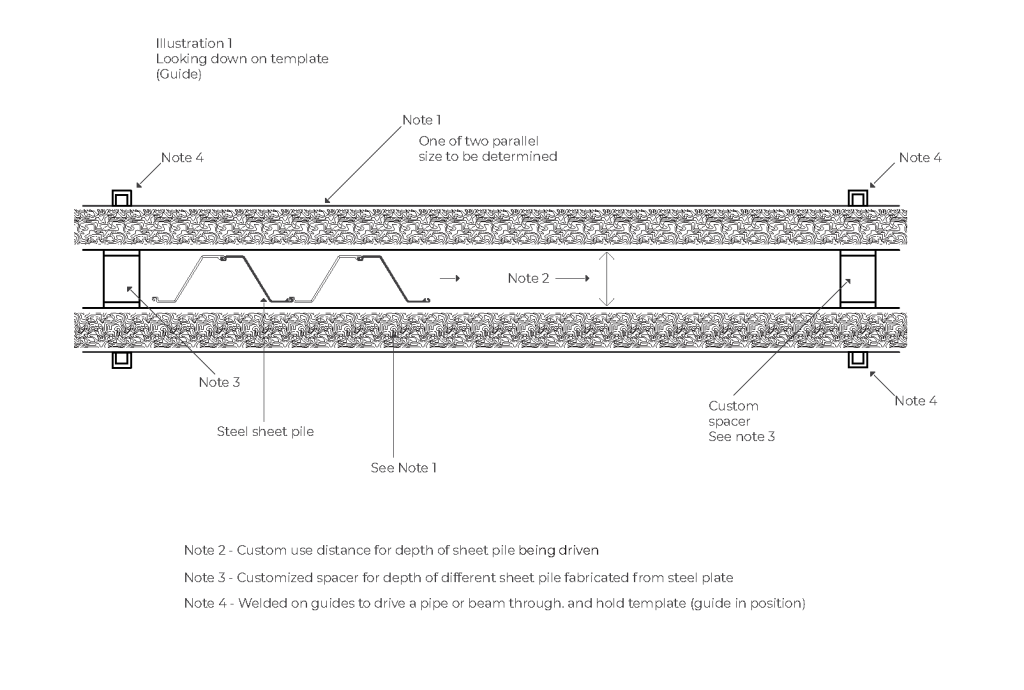
Understanding Pile Driving Template Systems
Understanding the primary types of template systems, as well as the different components contained with each, is essential before working with template systems.
Types of Pile Driving Template Systems
Template systems come in various configurations, each suited for different conditions and project requirements.
Fixed templates are commonly used in onshore applications where the driving surface is stable. They are anchored firmly to the ground or a solid base, providing a rigid guide for pile installation.
Used for marine or offshore projects, floating templates are designed to be adaptable to water movements while maintaining the pile’s position. They are often part of a larger floating platform or vessel.
Offering flexibility in construction, modular templates can be assembled in various configurations to accommodate different pile arrangements and project scales. Their adaptability also allows for efficient transport and reconfiguration as needed.
Components of a Typical Pile Driving Template
A typical pile driving template includes several key components:
- Guiding frame: This is the main structure that provides the template’s shape and stability. It ensures that piles are held in the correct spatial orientation.
- Positioning elements: These include clamps, sleeves, or guides that hold the pile in place within the template—ensuring that it does not deviate from its intended path during driving.
- Alignment mechanisms: These may involve lasers, GPS, or other survey equipment that assists in aligning the template precisely according to the construction plan.
- Adjustment features: These are systems that allow the template to be moved and adjusted to accommodate different pile positions or to correct for any misalignments during the driving process.
Modern template systems boast digital interfaces that seamlessly synchronize with construction management platforms, offering real-time progress tracking and enhanced record-keeping. Customizable to the core, these systems can be tailored to meet the unique demands of each project—accommodating a range of pile sizes and environmental conditions. Furthermore, modern template systems incorporate advanced safety features—including automated gripping and release mechanisms that minimize the need for manual intervention.
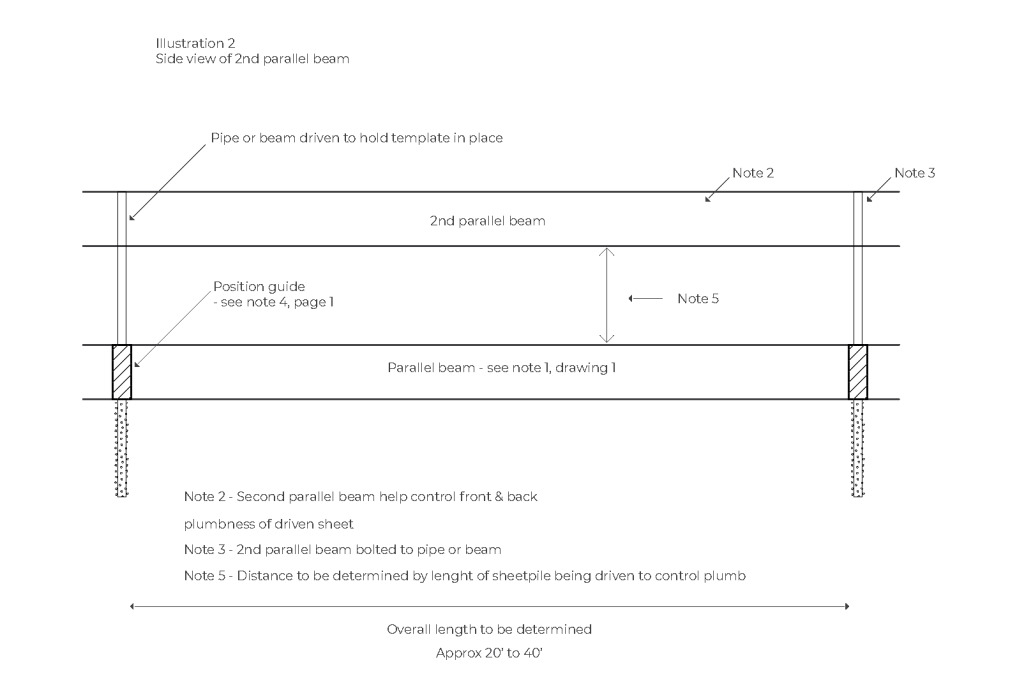
Preparation for Pile Driving Using Template Systems
The foundation of a successful pile driving operation lies in thorough preparation—which entails a meticulous site assessment, strategic planning, and the careful selection and setup of the template system.
Site Assessment and Planning
The initial phase involves a comprehensive site analysis to understand soil composition, environmental conditions, and spatial constraints. This data is critical in developing a detailed plan that outlines the pile driving sequence, locations, as well as any potential challenges that may arise during the operation.
Selection Based on Project Needs
Choosing the right template system hinges on the specific requirements of the project. Factors such as pile type, size, and the environmental context—whether onshore, offshore, or in a variable terrain—influence this decision. The objective is to match the template’s capabilities with the project’s demands to ensure efficiency and safety.
Logistics and Assembly
The final step before driving piles is the logistical coordination and assembly of the template system on-site. This process requires precision and attention to detail to ensure that the template is correctly positioned and securely anchored, ready for the piles to be driven. The assembly might also involve calibrating alignment mechanisms and testing adjustment features to confirm operational readiness.
The construction of the template system is a collaborative endeavor—with engineers meticulously designing the system to meet the project’s precise specifications, and contractors—likely specialized in foundational construction—bringing the plans to life on-site. This on-site collaboration ensures that the system not only aligns with the engineering requirements but is also pragmatically executable within the given environmental and project constraints.
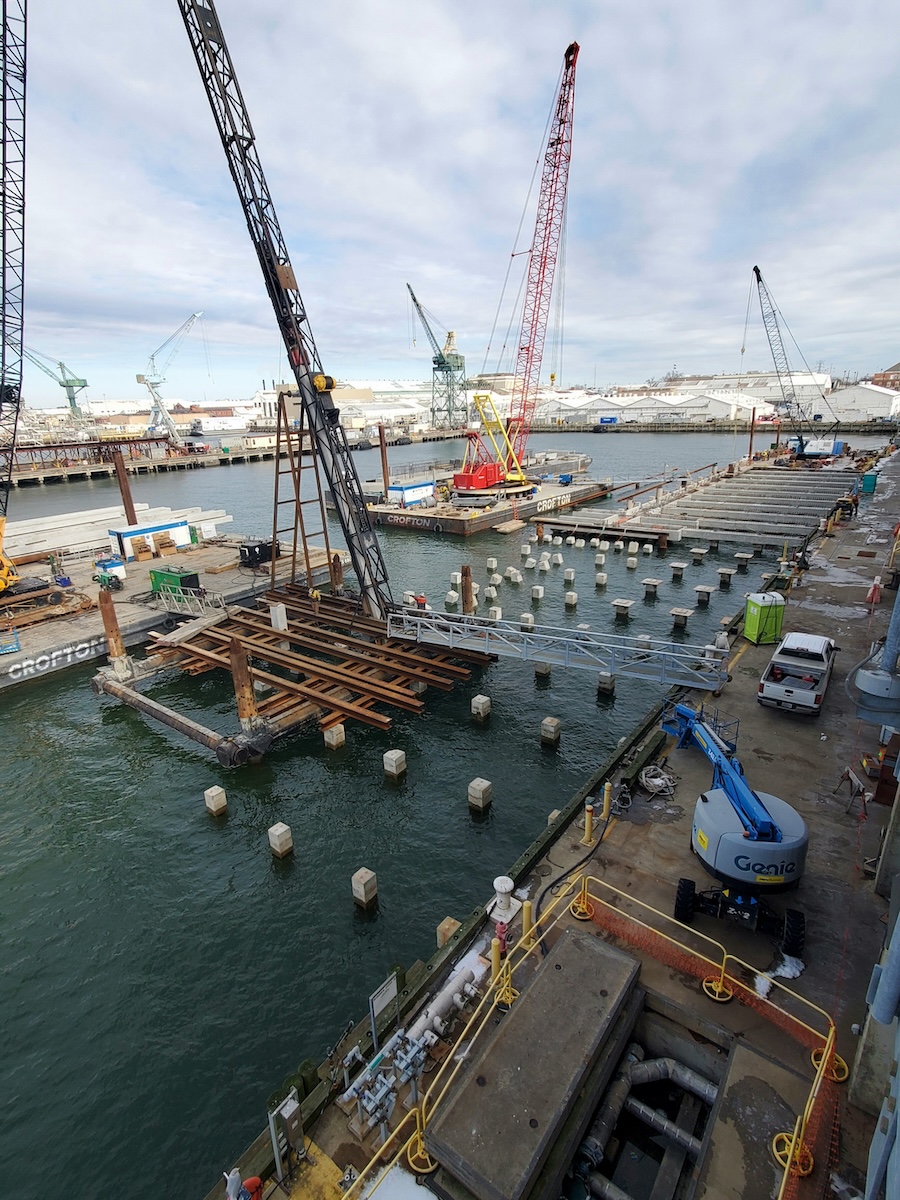
Operational Guidelines
Efficient and safe pile driving is contingent upon adhering to a set of operational guidelines that ensure the template system is utilized to its full potential.
Step-by-Step Guide to Using the Template System
Firstly, it is necessary to familiarize oneself with the template’s operating manual—if this should be available. Begin with a pre-use inspection, then follow the specific steps for securing the template system to the ground or platform. Place the pile within the guides of the template, ensuring it is vertical or at the required angle as per the engineering plans.
Aligning and Positioning the Piles
Accurate alignment is crucial. Use the template’s built-in alignment mechanisms, such as laser guides or GPS systems, to position the pile correctly. Double-check all measurements before commencing pile driving to ensure that each pile will be placed within the tolerances specified by the structural engineers.
Safety Protocols During Operation
Safety must be a top priority throughout the pile driving process. Establish a safety perimeter around the driving area, ensure all personnel are trained on emergency procedures, and confirm that all safety equipment—such as hard hats and high-visibility vests—are being used.
Monitoring and Adjustments During Pile Driving
Once pile driving begins, constant monitoring is crucial. Observe the behavior of the pile and the template for any signs of shifting or misalignment. Should any deviations occur, stop driving immediately and make the necessary adjustments. Keep a detailed log of the driving depth and any issues encountered for each pile, as this will aid in quality control and future reference.
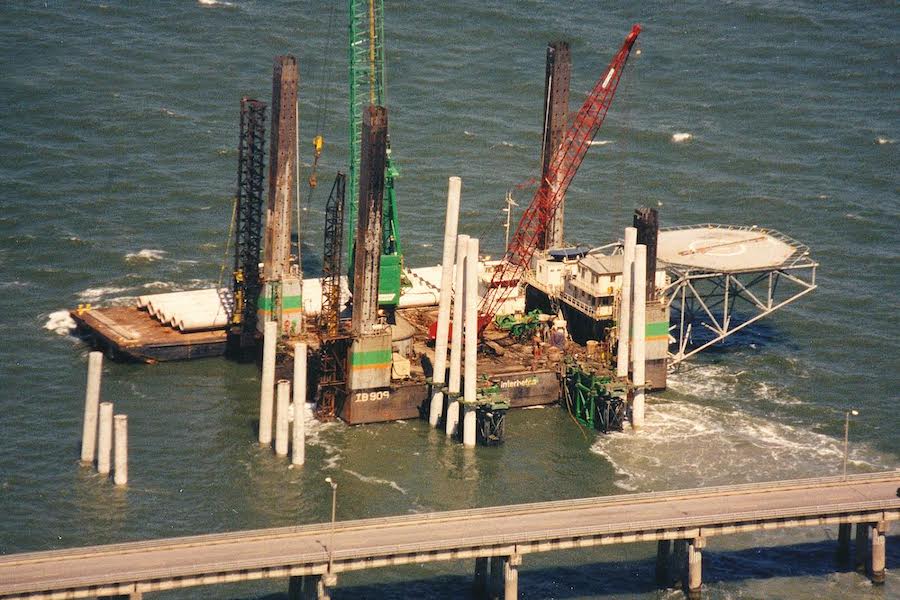
Troubleshooting and Common Challenges
The implementation of template systems, no matter how meticulous the planning, is not without its challenges. Contractors and engineers must be vigilant at identifying and addressing potential issues that can arise during pile driving operations.
Identifying and Addressing Common Issues
The most common issues include:
- Misalignment of piles
- Incorrect positioning due to unexpected subsurface conditions
- Equipment malfunctions
Addressing these problems requires careful attention to detail, as well as real-time adjustments. For instance, misalignment can be corrected through the use of onboard alignment tools and repositioning mechanisms that most modern templates are equipped with.
Maintenance and Problem-Solving During Operations
Regular maintenance is the key to prevent problems before they occur. This may involve routine checks of:
- Hydraulic systems
- Structural integrity of the template frame
- Efficiency of the positioning elements
When issues do arise, on-the-fly problem-solving is necessary. This will require a skilled crew that can quickly diagnose and rectify problems, ensuring minimal downtime and adherence to project schedules.
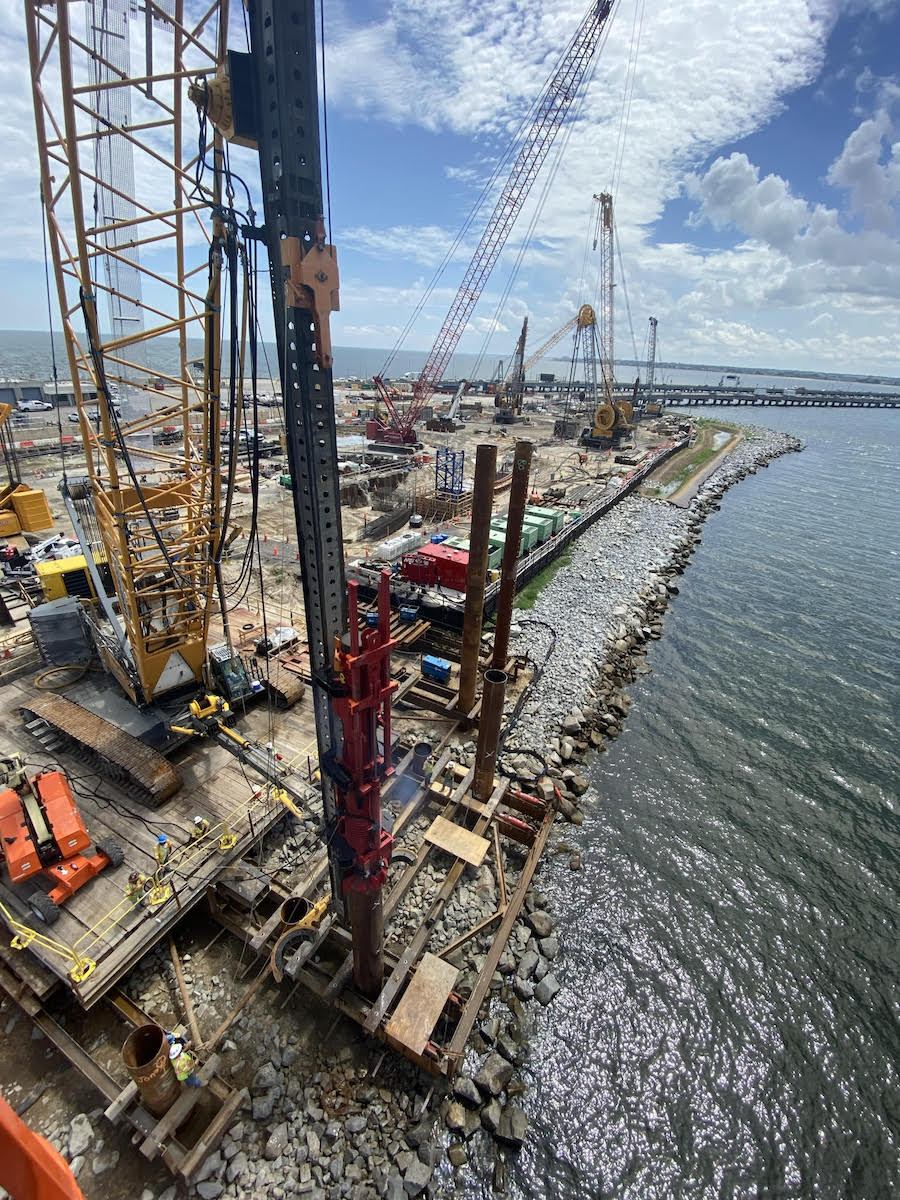
Case Studies
The utilization of template systems has been pivotal in several landmark construction projects across the world—each presenting unique challenges that demanded precise pile placement.
San Francisco-Oakland Bay Bridge (California, USA)
The floating template system utilized for the San Francisco-Oakland Bay Bridge was engineered to maintain stability and precision in the face of dynamic marine conditions—allowing the construction team to accurately position piles in depths that varied significantly. This undertaking was particularly important given the Bay Area’s vulnerability to earthquakes—requiring a foundation capable of withstanding substantial seismic forces, which was successfully achieved through the careful coordination of template-assisted pile driving.
Hong Kong-Zhuhai-Macao Bridge (China)
The Hong Kong-Zhuhai-Macao Bridge project, a triumph of engineering, leveraged the versatility of template systems to address the varying geological challenges presented by the Pearl River Delta. These templates ensured that each pile was accurately positioned and driven to the required depth, a necessity for the longevity and safety of the bridge—which now withstands the heavy traffic and harsh weather conditions of the region.
Burj Khalifa (Dubai, UAE)
Another engineering marvel, the Burj Khalifa, required a pile driving template of unparalleled precision to counter the complexities of the Arabian Gulf’s sandy terrain. The custom design of the template system was pivotal in ensuring the correct placement and depth of each pile, forming a robust and stable foundation that supports the soaring structure.
Conclusion
Pile driving template systems are essential when it comes to the structural integrity and efficiency of any serious pile driving project. From site assessment and tailored selection to the implementation of operational guidelines and proactive troubleshooting, we hope this guide was able to convey the significance of template systems. The dedication to precision, underpinned by a deep understanding of template systems, is what allows contractors and engineers to build with confidence—securing the longevity and safety of infrastructure around the world.
View the complete article here.
What are the main types of template systems used in pile driving?
The main types of template systems used in pile driving are fixed templates, floating templates, and modular templates. Fixed templates are anchored to stable surfaces, floating templates adapt to water movements, and modular templates can be reconfigured for different project needs.
Why are template systems important in pile driving applications?
Template systems ensure precision in pile placement, which is crucial for structural integrity. They help maintain the correct alignment and depth of piles, especially in challenging environments, reducing the risk of misalignment and structural failures.