Success in Steep Conditions with Liebherr Crawler Cranes
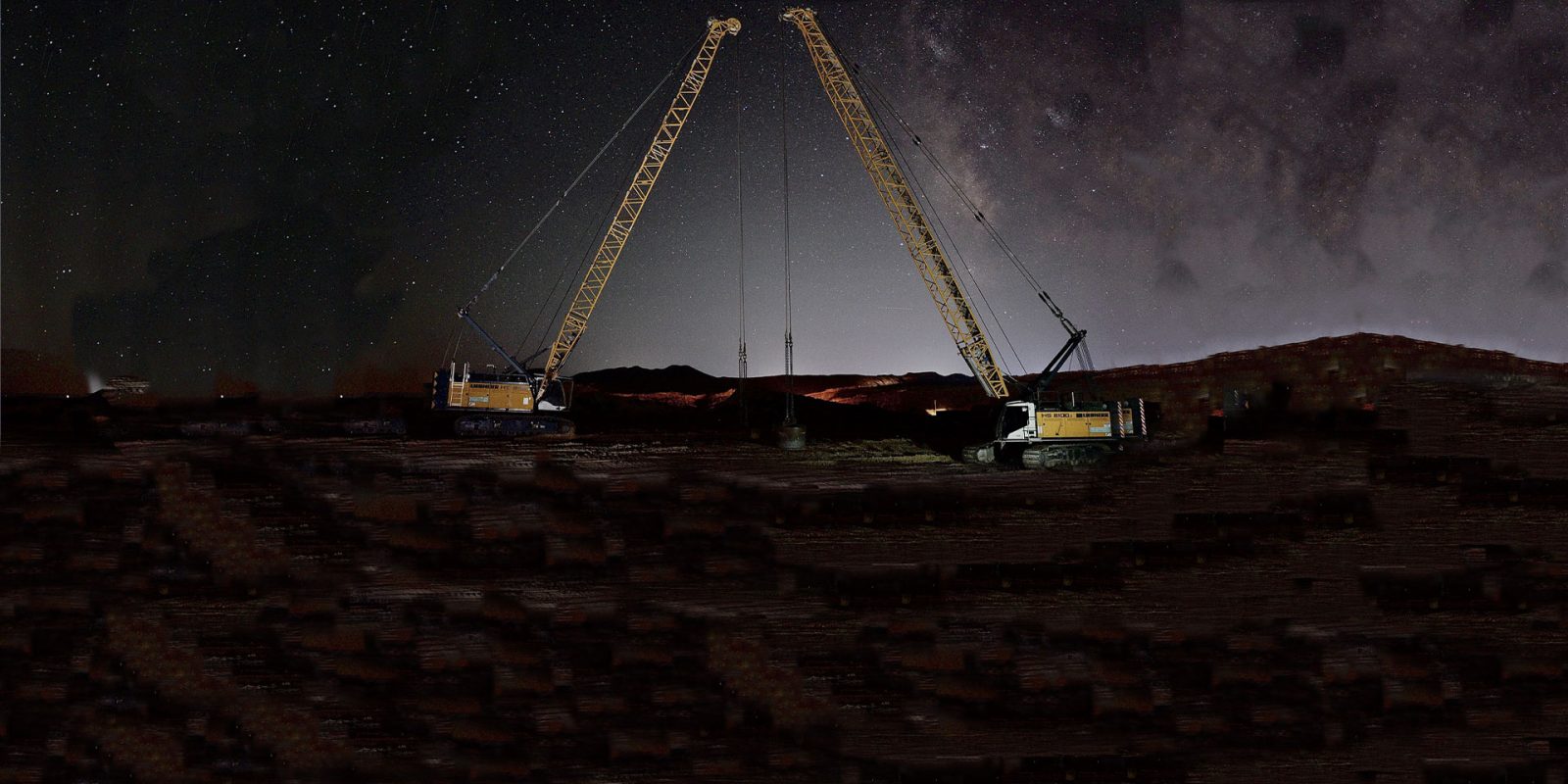
With the help of two Liebherr HS 8100 HD duty cycle crawler cranes, Densification, Inc. completed an extensive dynamic compaction program to provide a solid foundation for a safer stretch of highway along the US Route 191 corridor.
Founded in 1994, Densification, Inc. strives to provide property owners and developers with a cost-effective solution when encountering poor quality soil or fill during construction. Through the years they have become a premier dynamic compaction contractor, performing jobs across the United States and the Caribbean.
Dynamic compaction serves as an innovative and sustainable solution for soil densification and involves multi-ton weights being dropped repeatedly to create a shock wave that increases the density of the soil. Having completed over 1,000 projects since their founding, Densification has the expertise and equipment to properly supply effective soil densification to sites across the nation thanks to their extensive crane fleet including multiple Liebherr HS 8100 HD duty cycle crawler cranes. As one of the only companies in the US using these machines for this application, Densification has seen the versatility of these machines first-hand and found a trusted partner in Liebherr.
Robert Shaffer, Vice President of Densification, Inc. said, “part of our decision to purchase and use Liebherr HS 8100s HDs was based on Liebherr’s reputation for durable, dependable cranes.”
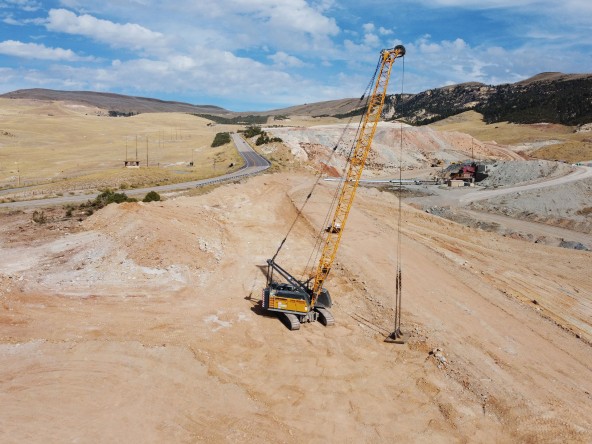
Realigning Rough Terrain
Frequent drivers along US Route 191 are familiar with the 2.6 mile stretch of switchbacks located just north of Vernal, UT. To improve this stretch of road and make it safer and more efficient for motorists and semi-trucks, the Utah Department of Transportation began the US-191 Realignment Project to provide standard horizontal curves, optimize grades and eliminate switchbacks for the highway.
The project began with the dynamic compaction of the uncontrolled embankment fill along the proposed realignment through an active sulfate mine through which the existing highway alignment traversed. Densification was brought in to perform dynamic compaction along the alignment, which was performed by two of their HS 8100 HD duty cycle crawler cranes working in tandem. The cranes utilized 18-ton (19.8 USt) weights dropped from a height of approximately 70-foot for the high energy work, and an 11-ton (12.1 USt) weight dropped from a 20-foot height to complete the final ironing pass.
For dynamic compaction, HS 8100 HD key features include Liebherr’s advanced control system that lifts the drop weight to a pre-defined height and releases it in free-fall mode using both winches simultaneously. The winches brake automatically to prevent damage to the wire ropes. This process is repeated until a preset number of drops or the desired compaction depth is achieved. Additionally, the operator’s cabin is equipped with armored glass to ensure the operator’s safety.
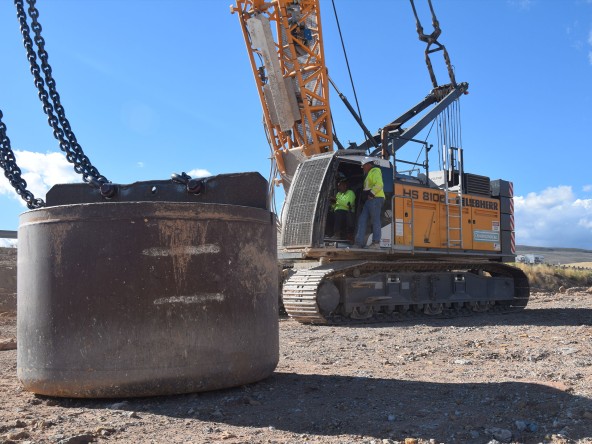
Your Partner in Planning
While this project was like the type of infrastructure projects Densification has been performing for decades, there was one variable that made this project different from all the others and that was the moderate slope of the site. From start to finish, there was a 500-foot elevation change that Densification had to accommodate for to safely operate their machines.
As a company that always strives to be a trusted partner for customers, Liebherr created a custom load chart for the project’s unique specifications. The custom load chart provided the operators with the proper load capacities to complete the job safely and efficiently.
“We’re confident in our ability to stay on schedule and provide our clients with the best dynamic compaction solutions possible due to our HS 8100 HDs consistent performance and durability,” notes Shaffer.