Thoughts on Manufacturing Steel Sheet Pile
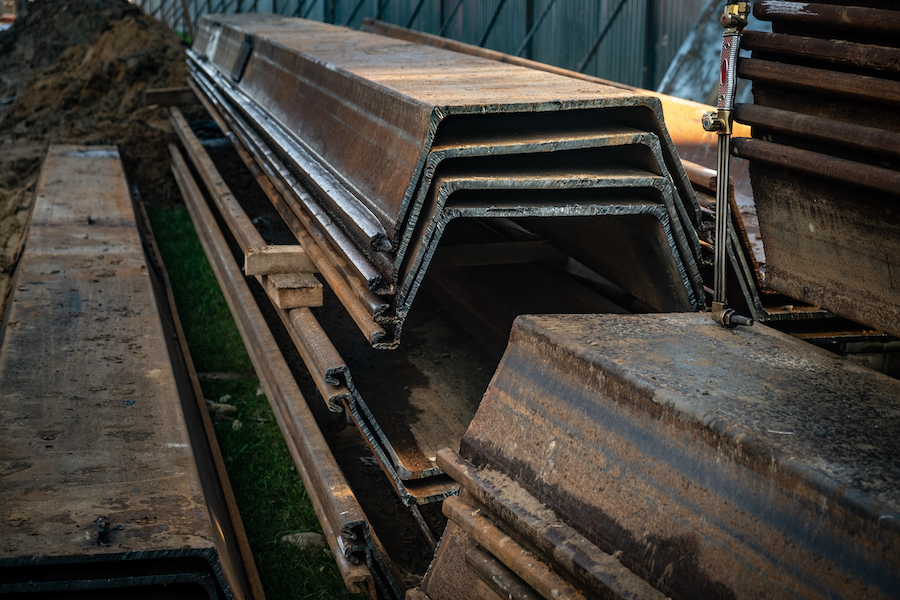
View the complete article here.
by Lee Wilczynski
A couple of weeks ago, I started researching how many manufacturers of steel sheet pile there are in the world. The following is a short summary and some thoughts on steel sheet pile.
In Luxembourg, ArcelorMittal produces the AZ sheet pile line, various U-shape sheets, and flat web sheets, along with other steel products. Their mill in Poland makes hot rolled U-shape sheets, and they have a cold rolling production facility in France.
In Dortmund, Germany, Salzgitter Hoesch had a mill that closed, and later, that same production line was reassembled in China. Currently, the Z-shape Hoesch sheets are made in conjunction with a Chinese mill called Jinxi.
Anshan is another Chinese mill that makes the hot rolled Z-shape and U-shape sheets. Anshan’s sheet pile ZZ (Double Z) series includes a wide range of different sections.
In the United Arab Emirates, Emirates Steel makes the ESZ sheet pile line.
In Belgium, Meever and Meever has set up a cold rolled production line.
In the Czech Republic, Vitkovice is a mill making U-shape sheets. Their sheets are referred to as “VL.”
In Korea and Russia, there are mills that make hot rolled U-shape sheets. They’re more compact and therefore heavier than the typical U-shape sheet made in Europe.
In Japan, there is a mill that makes hot rolled flat sheets “Nippon Steel.”
In China, there are also numerous cold rolled sheet pile production lines. Other countries make cold rolled sheet pile besides China.
In the US, Gerdau and Nucor make hot rolled sheet piles. Both manufacturers make Z-shape and flat sheet piles. And cold formed steel sheet pile is manufactured by Skyline, Shoreline, Samuel Roll Form Group, and Steel Piling USA.
This list is not complete, and there are other sheet pile mills around the world as well. Every major continent has some kind of hot rolled or cold formed mill rolling steel sheet pile.
This information made me think about many steel sheet pile issues. For example, Z-shaped vs. U-shaped and hot rolled vs. cold formed. Why are so many people around the world still using U-shaped pile?
It seems like the more compact shape of U piles would hold up better in difficult driving and repeated pulling and driving for temporary use. And I have had experience with hot rolled U-shaped sheet piles when the contractors were amazed at how watertight they were. Maybe we should consider U shape for applications where difficult driving is anticipated. The popularity of Z pile over U shape also can be explained by cost. Z sheets are wider, and Z sheets fit in a template more easily. Also, Z piles usually have more consistent wall thickness, and Z sheets are easier to stack up as pairs. Generally, you can purchase higher section modulus pile with lesser weight and save money.
Then we come back to hot rolled vs. cold formed. Why won’t the Corps of Engineers (USMC) design more projects with cold formed? There are millions of dollars of future Marine Corps projects coming out in the future, especially with the infusion of money that will come for infrastructure repairs.
There are few, if any, reports on cold formed pile structures failing. The most damaging report was presented by an engineer who was paid by the hot rolled industry to denigrate cold formed pile. Most people don’t know his original calculations were based on laboratory analysis of an obsolete pile, and the original thesis was to compare shape, not properties. The hot rolled industry was successful with this mumble jumble to set back the cold-formed industry by at least 15 years. This engineer also came up with calculations warning the engineering sector about coming failures due to transverse stresses. Again, if present, transverse stresses are recognizable and can be addressed with sound engineering principles.
So why won’t the Corp of Engineers design more with cold formed to keep costs competitive? Is it political? I don’t know.
And getting back to compact sheet pile, I have always thought PZ-27 was one of the best piles available for reuse because of the compact design and the ability to hold up well. What will happen when the only producer decides to stop rolling it? Maybe we will have to start using thicker .500” for reuse?
There are two hot rolled and six or seven cold formed steel sheet pile mills in the US. And worldwide, the ratio is about the same, with about three times more cold form mills than hot rolled.
View the complete article here.
What are the key aspects to consider in the manufacturing of steel sheet pile?
When manufacturing steel sheet pile, factors such as the type of steel, the grade, the manufacturing method, the shape and size of the pile, and the corrosion resistance are of crucial importance. The manufacturing process involves choosing the right type of steel and following a detailed process to form the shape and size of the pile. The process should also ensure that the pile has adequate corrosion resistance for its intended application.
How can steel sheet pile be manufactured sustainably?
Sustainable manufacturing of steel sheet pile involves the use of energy-efficient processes, recycling and reusing materials wherever possible, and minimizing waste. It also involves sourcing materials responsibly and ensuring that the manufacturing process has the least possible impact on the environment. Sustainable practices can also extend to the life cycle of the product, with considerations for recyclability at the end of its useful life.