Slurry Displacement Piles and Methods
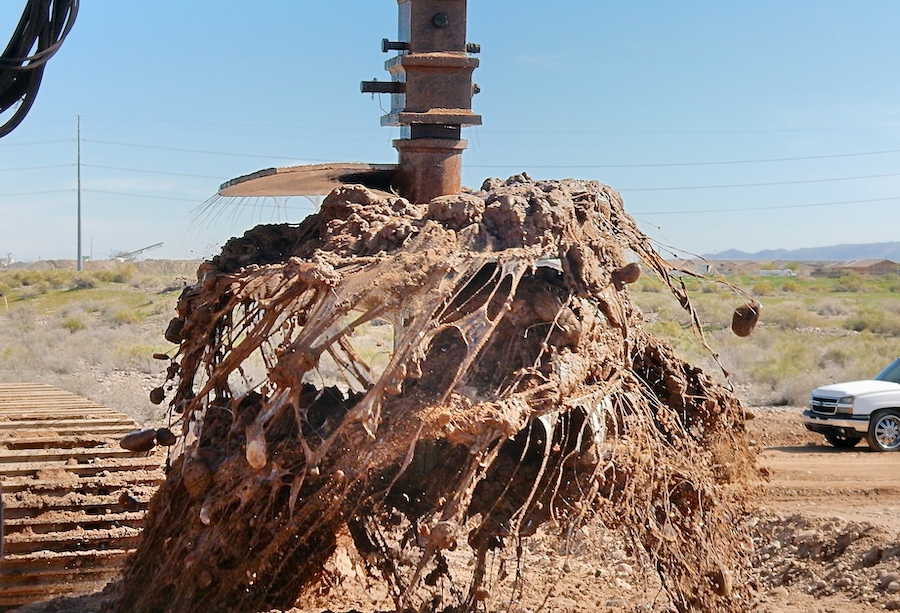
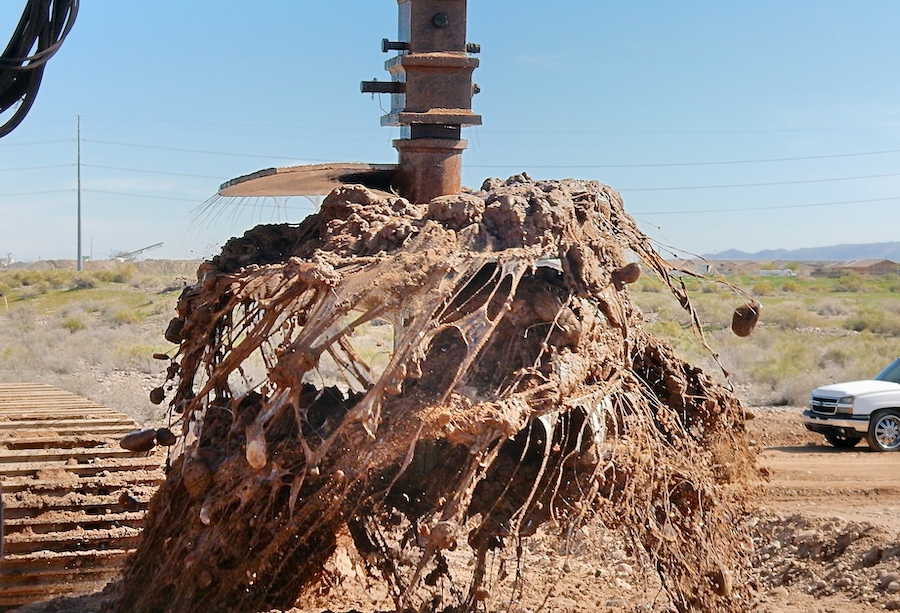
View the complete article here.
When unstable ground formations or groundwater are encountered or anticipated during installation of a Cast-In-Drilled-Hole (CIDH) pile, a contractor has a few options to prevent caving. They can use a casing to stabilize the drilled hole, remove the water from the drilled hole, or use the slurry displacement method. In this article we discuss the use of slurry displacement piles and methods.
What is a Slurry Displacement Pile?
Slurry displacement is a method to form a drilled hole by displacing the soil instead of extracting it. Drilling fluid – or slurry – is introduced into the hole as it is being drilled. The concrete is placed under the slurry using a rigid delivery tube. As the concrete is being poured it displaces the slurry.
Slurry Evolution
The slurry displacement method for drilled shafts has evolved over the years. Their use began in Texas after World War II. Unfortunately, mineral drilling slurries were not controlled or standardized in any way. This resulted in CIDH piles that presented problems later on. In the 1970s methods of preparing drilling slurries were improved. By the 1980s the use of synthetic slurries increased because processed clay mineral slurries were considered environmentally hazardous and difficult to dispose of.
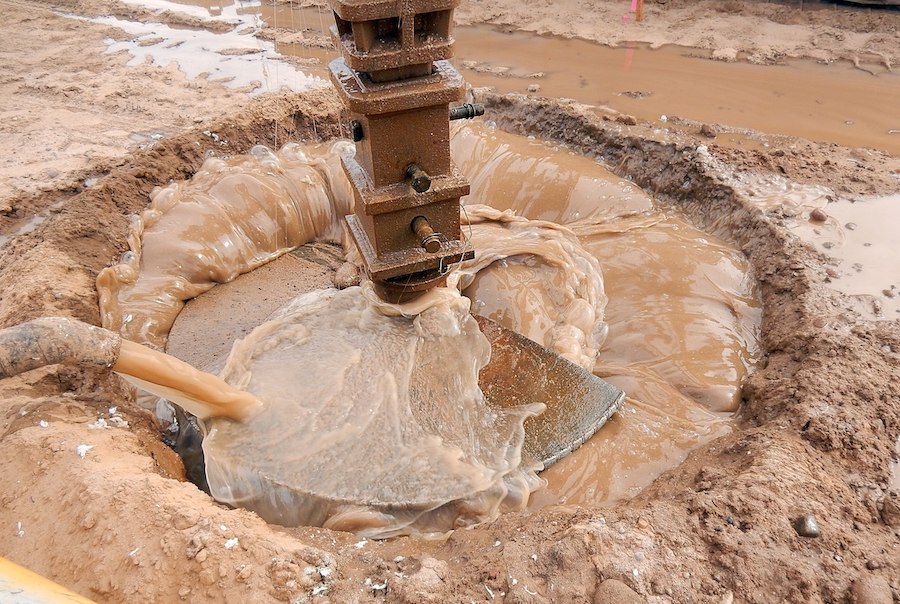
How Slurry Displacement Works
Slurry Introduction
Slurry is introduced at the same time the hole is being drilled. In cases where groundwater or caving materials are encountered during drilling, the slurry is placed into the drilled hole. The slurry is kept at least 10 feet above the piezometric head as drilling continues.
Cleaning the Slurry
During the drilling operation, soil cuttings get mixed in with the slurry. This must be removed either by cleaning the drilling slurry or allowing time for the soil cuttings to settle. The settled material can then be removed with a cleanout bucket. It will sometimes require multiple passes with the cleaning bucket as the action of the bucket itself can contaminate the slurry. Cleaning of the soil cuttings can also be done using a pump or airlift. When the cleaning is completed, the slurry must be tested. Testing allows the slurry’s properties to be controlled during drilling in order to stabilize the drilled hole.
Placing the Cage
Next, the pile bar reinforcement cage is placed. Before the concrete is placed, the slurry is retested, and the bottom of the hole is recleaned using a pump or airlift. Starting at the bottom of the drilled hole, concrete is placed using a rigid tremie tube or rigid pump tube delivery system.
Concrete Placement
The tip of the delivery tube is kept minimally 10 feet below the head of concrete as it rises. As the concrete is placed, the drilling slurry is displaced by pumping it away from the drilled hole. At this point the slurry is either prepared for reuse or is disposed of. When the head of concrete reaches the top of the pile it is wasted until all settled material or drilling slurry are removed. In some cases the contaminated concrete is mucked out after placement – or chipped out later.
Hydrostatic Pressure
Slurries are able to keep excavations open through positive hydrostatic pressure. This requires a pressure transfer medium. In other words, something the hydrostatic pressure can push against. Deposited filter cake of clay solids on permeable formations provides the transfer medium for mineral slurries. With synthetic slurries, the zone of viscous permeation surrounding the excavation is the transfer mechanism.
Filter Cake
Solid-laden slurries, such as mineral slurries, have a “filter cake” that temporarily provides stabilization to the sides of the drilled hole prior to concrete placement. However, it is not meant to remain in place. The filter cake must be thin enough for the column of concrete to scrape it off the sides as it rises up through the drilled hole. Filter cake left behind can reduce the pile’s skin friction capability. That’s why it is important that excess filter cake be removed before concrete placement. Although there are several variables that impact the thickness of the filter cake, two are key: ground formation and time. Generally, permeable granular ground formations like sands result in thicker filter cake. Typically the longer the slurry is present in the drilled hole, the more the filter cake will build up along the sides. In some cases the excess filter cake must be removed before the concrete can be placed.
Slurry Quality Control
Sampling and testing of the drilling slurry are critical to quality control during the drilling of the hole and during concrete placement. This is primarily to ensure that no suspended material in the drilling slurry remains settled out while the concrete is being placed.
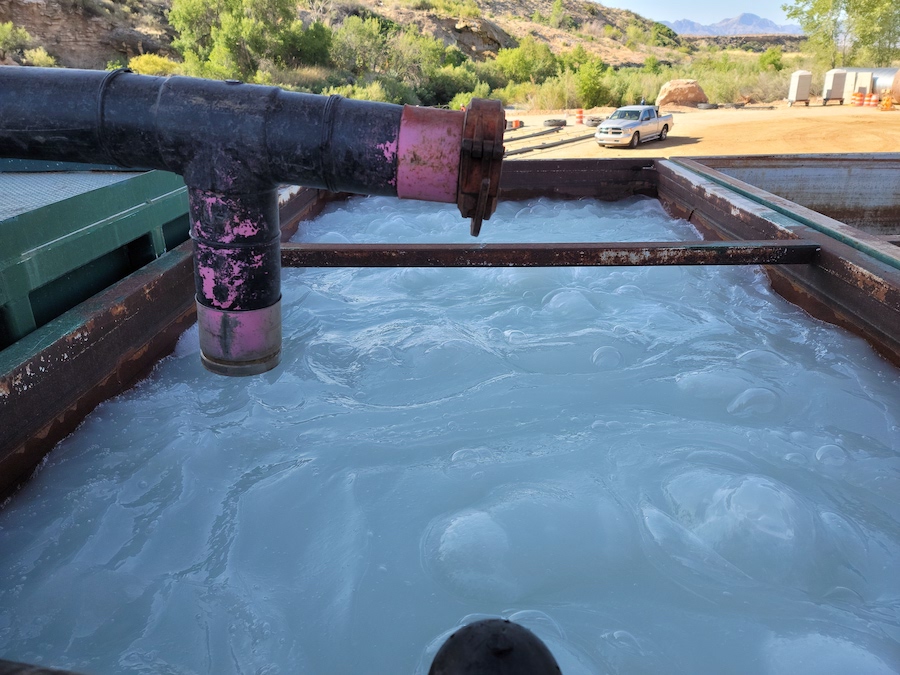
Types of Slurry
The type of slurry used depends on several factors. Budget constraints, contamination levels of the ground and groundwater, the temperature of the ground and air, and the ground formation type all must be taken into account.
Water
Water is often preferred as a drilling slurry wherever possible since it is cheap and often readily available. It also suspends sand and silt for typically under 30 minutes – allowing soil cuttings to settle to the bottom of the drilled hole quickly. Its use is only appropriate where ground formations are strong enough to resist deformation during drilling.
Mineral
Although many types of clay formations exist, most mineral slurries are processed from bentonite and attapulgite. The thickness of the filter cake can be reduced by removing soil solids, such as sand, from the mineral slurry. Mineral slurries must be agitated in the drilled hole to reduce the amount of filter cake that builds up on the sides. This type of slurry is an option for most ground formations.
Synthetic
Synthetic drilling slurries have been widely accepted in the construction industry since the 1980s. They are easier and less expensive to dispose of compared to mineral slurries. Synthetic slurries do not require physical cleaning. They are grouped by polymer type. The polymers are dry or emulsified. The three types of polymers are naturally occurring, semi-synthetic, and synthetic. Synthetic slurries, like mineral slurries, can be used for most ground formations. However, they are not recommended for soft or very soft cohesive soils.
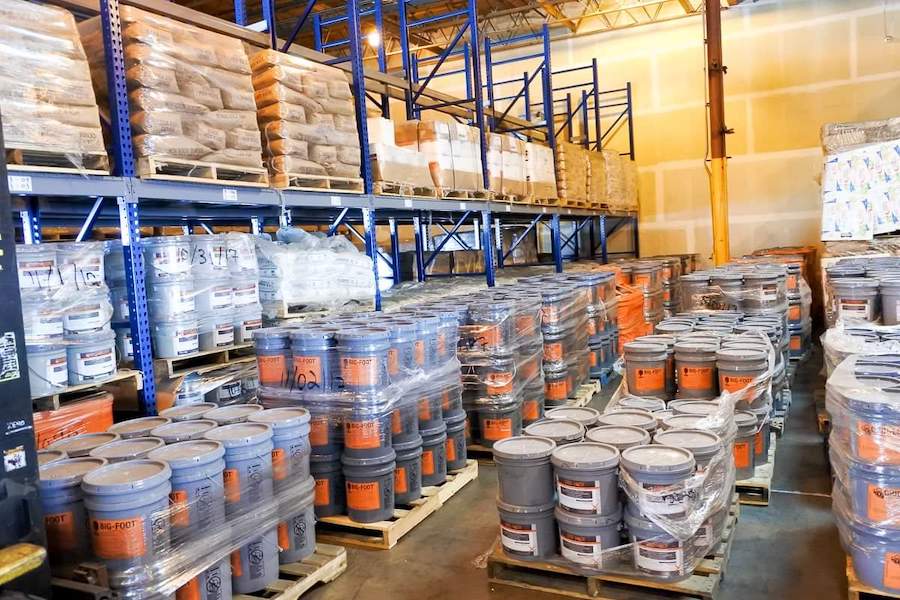
Physical Properties of Drilling Slurries
Parameters are set for physical properties of the drilling slurry that are part of the contract specification. They are density, sand content, pH, and viscosity.
Density
This is the weight of the solids held in suspension by the drilling slurry. Mineral slurries hold solids in suspension longer than synthetic slurries or water. So their allowable density value will be higher.
Sand Content
Again, mineral slurries hold sand particles and other solids in suspension longer than synthetic slurry or water. Thus the allowable sand content will be higher for mineral slurry.
pH Value
To fully hydrate the clay mineral and develop the proper viscosity, a mineral slurry must have the proper pH level. In the case of synthetic slurry not mixed with water of the proper pH level, they will exhibit no viscosity.
Viscosity
If the slurry is too thick – or viscous – it will cause the slurry to suspend more solids than allowable. In turn this affects density and sand content. That said, in loose ground formations like gravel, a higher viscosity may be needed to form a filter cake to stabilize the sides of the drilled hole.
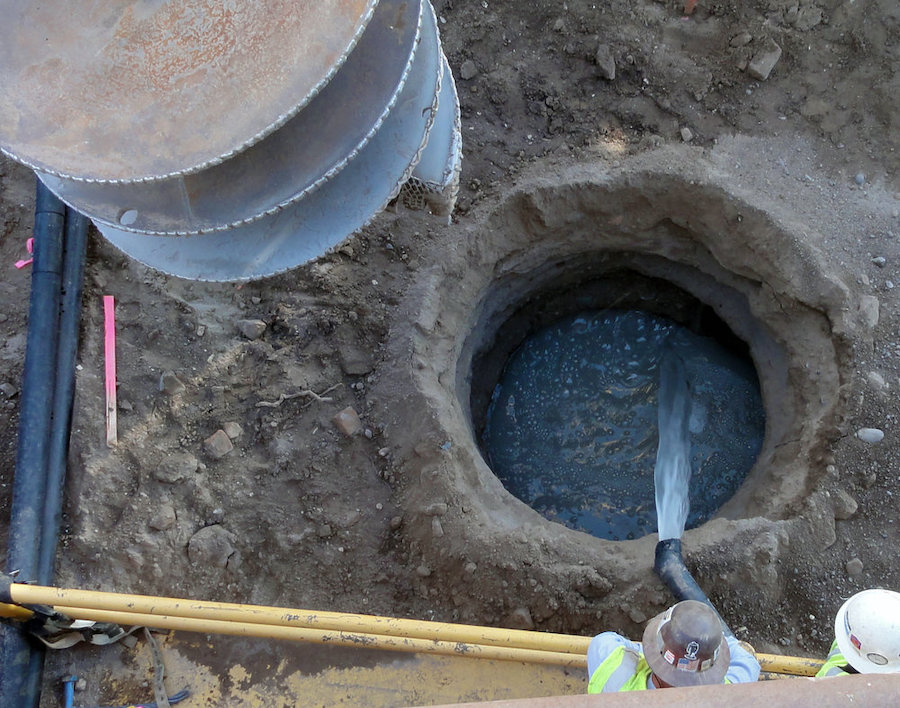
Chemical Additives
Chemical additives can be used to adjust the mineral slurry’s properties during drilling. For example, organic colloids like starch can reduce the filter cake thickness and increase its viscosity. Pyrophosphate acid lowers the slurry’s pH. Soda ash and sodium hydroxide can increase the pH as well as reduce water hardness. Other additives used include tannins and acrylates.
Slurry Displacement Methods
There are two types of slurry displacement construction processes: static and circulation.
Static Process
In the process of slurry displacement the hole is drilled down to the piezometric level. The slurry is introduced and the cuttings are lifted from the hole.
Circulation Process
In the circulation process of slurry displacement the hole is drilled and the slurry level is maintained at the ground surface. Cuttings and sand are reintroduced down the hole after being circulated to the surface and cleaned.
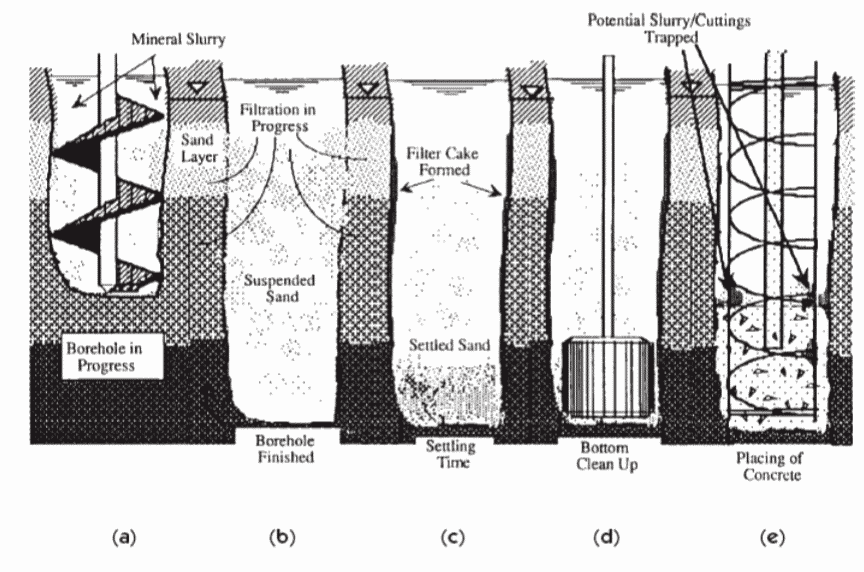
Slurry Testing Methods
There are four main testing methods used to ensure the slurry displacement piles are sound: external vibration, crosshold sonic logging, physical core inspection, and gamma-gamma logging.
External Vibration
External vibration measures stress wave propagations in the pile. Instrumentation is placed on the pile bar reinforcement cage prior to the concrete being placed. This slurry testing method requires expensive equipment and highly skilled operators.
Crosshold Sonic Logging
Crosshold sonic logging is an acoustical technique. Sender and receiver probes are lowered into inspection pipes. They measure the velocity of sonic waves through the concrete. If the concrete is sound the sonic wave is quickly received by the receiver probe. If it takes a long time, the concrete is defective.
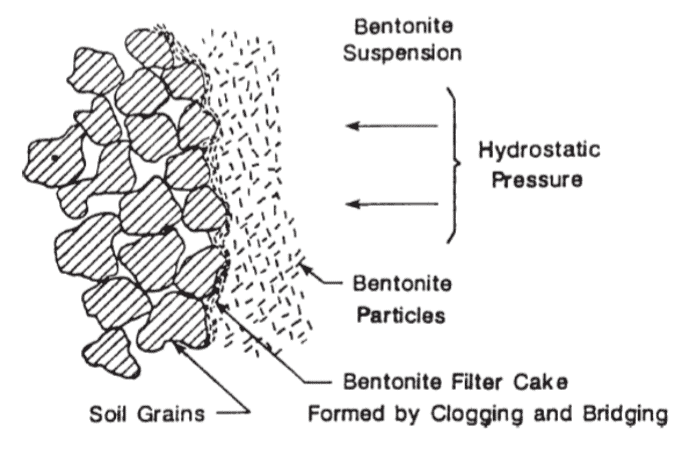
Physical Core Inspection
This testing method involves coring the pile for physical inspection. Unfortunately, though it is a conclusive method of testing, it is time consuming. And it is destructive to the pile.
Gamma-Gamma Logging (GGL)
GGL is a radiographic technique. PVC access tubes are attached to the reinforcing cage before installation. A low-level radioactive source at the probe tip and a shielded detector are used to assess the concrete’s density.
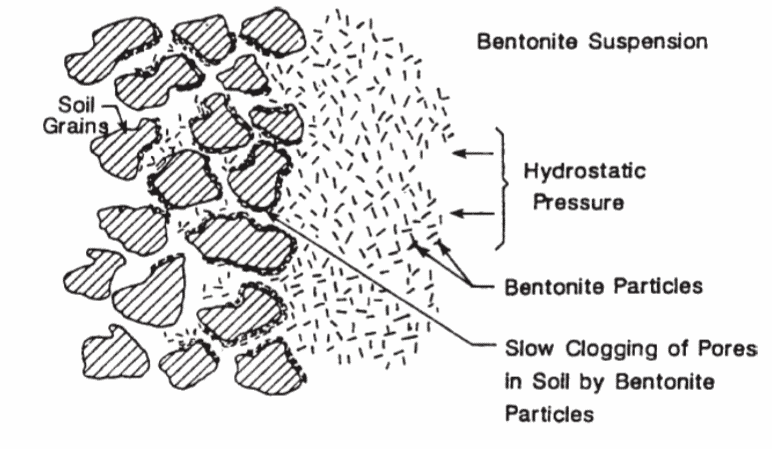
Defective Piles
There are three key reasons why piles constructed by the slurry displacement method are defective. They include settled materials, improper handling of the slurry, and poor mix design and placement.
Settled Materials
When mineral slurry is not properly cleaned and/or agitated, excessive amounts of settled material will be left at the bottom of the drilled hole. Synthetic slurry may not be given enough time for the materials to settle out. Or the synthetic slurry becomes contaminated from the encapsulation of clay particles.
Improper Drilling Slurry Handling
Mineral slurries will cause pile defects if they are not properly mixed or allowed to hydrate. Balls or clumps can form and attach themselves to the pile bar reinforcement cage. If the mineral slurry is left in the drilled hole for too long the filter cake will become too thick. If the concrete is dropped through the drilling slurry (mineral or synthetic) a chemical reaction may take place that undermines its integrity.
Mix Design and Placement
Poor mix design and / or placement can cause defects. For example, when there is not enough slurry-contaminated concrete wasted from the pile top during its placement. This results in a defective pile top.
Pile Mitigation Methodologies
There are four ways to mitigate defective CIDH piles:
- Unearth and Recast (Basic Repair).
- Pressure Grout (Grouting Repair).
- Structural Bridging.
- Supplement or Replacement.
Unearth and Recast (Basic Repair)
Basic repair involves removing all of the concrete that is within the defective zone of the pile. It is considered a simple repair when completed within five feet of the top of the pile. For repairs below five feet, the effect on the skin friction capacity of the pile must be assessed.
Pressure Grout (Grouting Repair)
There are three types of grouting procedures: permeation, replacement, and compaction.
Permeation Grouting
Permeation grouting repairs a defective pile by injecting a water-based, high-slump cement grout into the drilled shaft. However, water must be able to escape after the grout has been injected which is not always feasible when repairing a concrete defect. Permeation grouting is best used to handle “soft tip” anomalies.
Replacement Grouting
The purpose of replacement grouting is to fill voids using a low-slump, mortar-type mix. Contaminated concrete must be removed before replacement grouting. A common method used to remove deleterious material is high-pressure washing.
Compaction Grouting
With compaction grouting, the grout is inserted through an injection pipe and the pipe is slowly removed in lifts. This creates a column of grout bulbs that overlap and expand to displace the surrounding soils. The grouting improves the soil around the pile.
Structural Bridging
In structural bridging the center of the pile is cored and a structural steel section and / or rebar cage is installed. This type of repair increases the structural strength of the pile without having to completely remove the defect.
Supplement or Replacement
In cases where the defect is not repairable, the pile may be supplemented or replaced. Where sufficient space is available, supplemental piles may be placed to increase load-bearing capacity. Otherwise the pile may have to be replaced entirely.
Conclusion
Slurry displacement piles have been used since the 1940s. The type of drilling fluid used has evolved over time to include synthetic slurry. It is critical to test the properties of the slurry during the drilling operation to reduce the risk of pile defects. However, defective piles can be repaired in many cases. Slurry displacement piles are an effective way to install piles in unstable ground formations.
View the complete article here.
What is a slurry displacement pile?
Slurry displacement is a method to form a drilled hole by displacing the soil instead of extracting it. Drilling fluid – or slurry – is introduced into the hole as it is being drilled...
What is slurry?
A mixture of suspended solids and liquids. In cases where groundwater or caving materials are encountered during drilling, the slurry is placed into the drilled hole.