‘Serviceable’ 316 Stainless Metering Valves a Game-changer for Marine Lubrication Systems
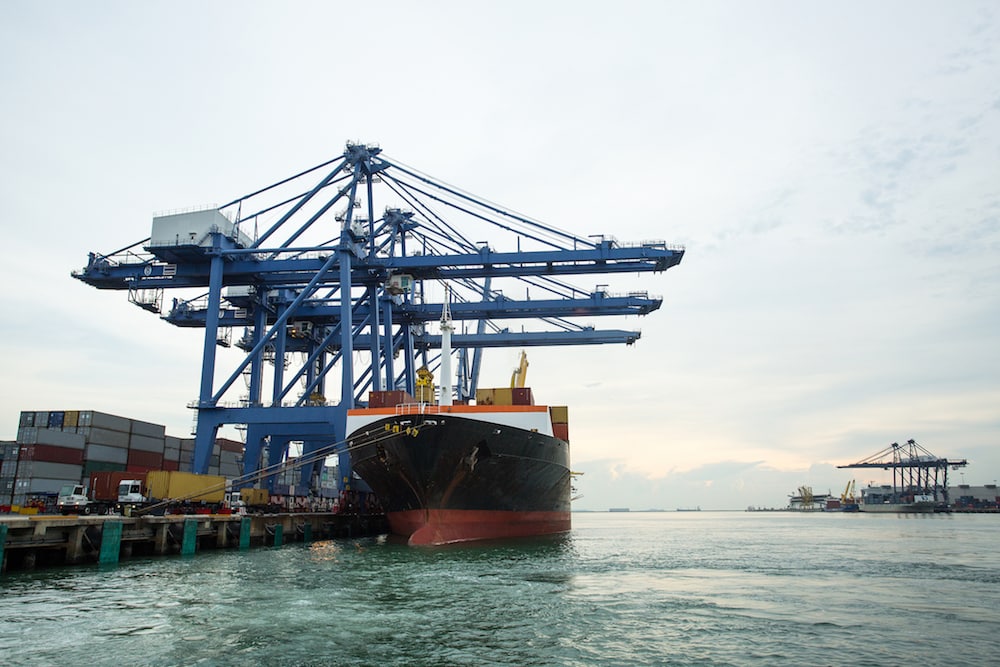
Protecting automatic lubrication system with metering valves made of corrosion-proof stainless steel offers significant advantages over epoxy-encapsulated models.
The proper functioning of lubrication systems is of critical importance to commercial and military vessels, ensuring the reliable operation of dozens of vital mechanisms and systems. Propeller shafts and thrusters, steering gears, deck cranes, winches, and turrets – virtually any gear that is supported by bearing components such as rollers, spines, gears, ball bearings or other moving parts – is dependent upon lubrication to fend off the destructive forces of corrosion.
Unfortunately, many automated lubrication systems, which are the preferred solution to regulating and dispensing the necessary lubrication to bearing points, are also subject to caustic corrosion. One solution to protecting against that – encapsulating lubrication system metering valves in epoxy – can result in long-term equipment servicing problems. The better solution may be to use costly, yet more economical, stainless steel.
Corrosion presents one of the greatest challenges to marine vessels, particularly corrosion by seawater and salt air, which is exacerbated by warm air and high humidity. According to the most recent NACE (National Association of Corrosion Engineers) study, the annual cost of corrosion for the U.S. shipping industry is in excess of $2.5 billion, including the costs of maintenance, repairs and downtime.
For example, in December of 2015, the $316 million USS Milwaukee, one of the U.S. Navy’s newest Freedom-class littoral combat ships, had to be towed to port less than three weeks after it was launched. The vessel had effectively lost its propulsion system due to metal filings in its lubrication oil system, a problem that could cost over a million dollars and months of time to repair.
Because corrosion by seawater – aqueous corrosion – is an electrochemical process, most metals and alloys are subject to various degrees of destructive corrosion, pitting, erosion or cavitation – except for 316 stainless steel.
Protecting the lubrication system
State-of-the-art lubrication systems are automated, providing grease or oil to many bearing points onboard a ship. These systems eliminate the cost and hazards of manually dispensing lubricants, and also ensure longer bearing wear life.
There are several different types of automated lubrication systems, but a typical system consists of controller/timer, pump with reservoir, supply line, metering valves and feed lines.
Whatever the design, the heart of the automated lubrication system is the metering valve that dispenses oil or grease in controlled proportions to each connected lube point at precise intervals.
Many of today’s most common marine automatic lubrication applications require large series progressive metering valves. These valves are assembled from inlet, piston, and end sections. Each piston section dispenses an engineered amount of lubricant to the bearing point(s), to which it is connected. These large series progressive metering valves are generally only available in plated carbon steel, which will not offer optimum life in high corrosion applications.
To protect these large carbon steel series progressive metering valves from aqueous corrosion, a prominent manufacturer of lubrication system components instructs its distributors to encapsulate the valve body in epoxy material, which is impervious to the corrosive effects of seawater and salt air.
Unfortunately, these epoxy-encapsulated valves are virtually impervious to maintenance as well. When a piston section of the valve ultimately fails, the complete unit is rendered unusable because it is so impossible for shipboard maintenance personnel to disassemble the epoxy encapsulated valve assembly, replace the one piston section.
“The inability to service sections of epoxy-encapsulated metering valve assemblies is a costly predicament,” says Richard Hanley, president of Lubrication Scientifics, LLC (Irvine, CA), a manufacturer of automated lubrication systems. “If it is an eight-section valve, the cost to the customer is approximately $30,000. So, if a section goes bad, the user has to discard one $30,000 valve and replace it with another $30,000 valve.”
Hanley adds that if the metering valve assembly were not encapsulated in epoxy, it would be a simple procedure to replace a faulty valve section for a cost of approximately $2,500.00.
To avoid the high costs of replacing epoxy-encapsulated metering valves, Lubrication Scientifics recently introduced a line of marine lubrication systems that features a metering valve constructed of 316 stainless steel.
The 316 stainless advantage
Hanley says the reason his company decided to use 316 stainless due to that material’s long-term resistance to corrosion.
Grade 316 stainless is austenitic chromium-nickel steel that contains corrosion-resistant molybdenum, which is highly resistant to pitting and crevice corrosion in seawater environments. Crevice protection is particularly significant for metering valves composed of sections that are sandwiched together so that they may be serviced individually.
Lubrication Scientifics has been supplying 316 stainless lubrication system metering valves for use on offshore oil and gas drilling rigs for a number of years, and corrosion problems have been nonexistent.
According to Hanley, other manufacturers of automatic lubrication systems claim they can provide lubrication metering valves out of 303 or 316 stainless steel. However, in many cases those special orders take several months to fill. He says his company is totally committed to making stainless steel metering valves for many different applications, and keeps a large supply of 316 stainless on hand for fast delivery.
Lubrication Scientifics makes three types of system and components available in 303 and 316 stainless steel – single line parallel, dual-line parallel and single-line progressive – most of which are available within days rather than months.