P-834 SEAWOLF Class Service Pier Extension
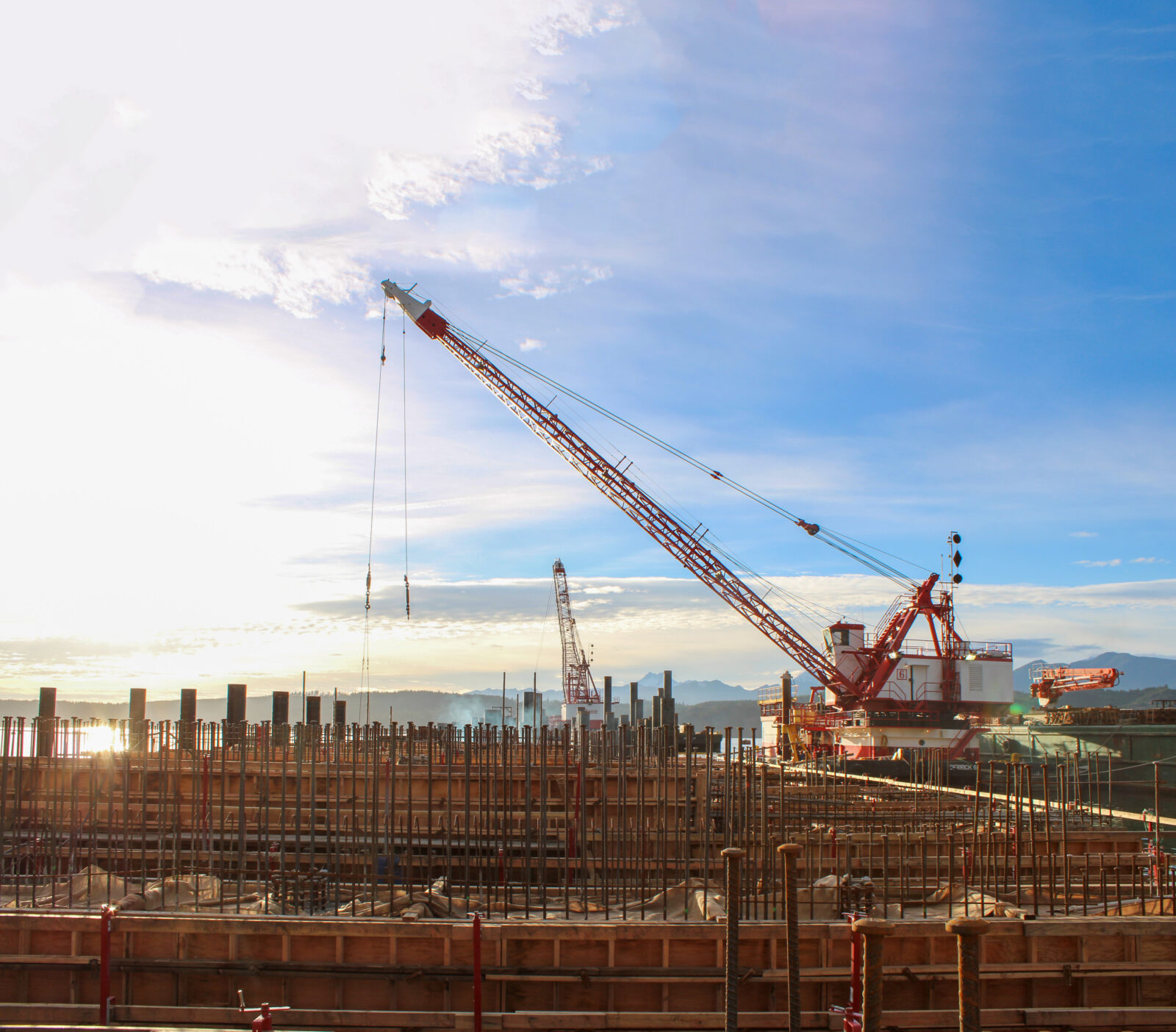
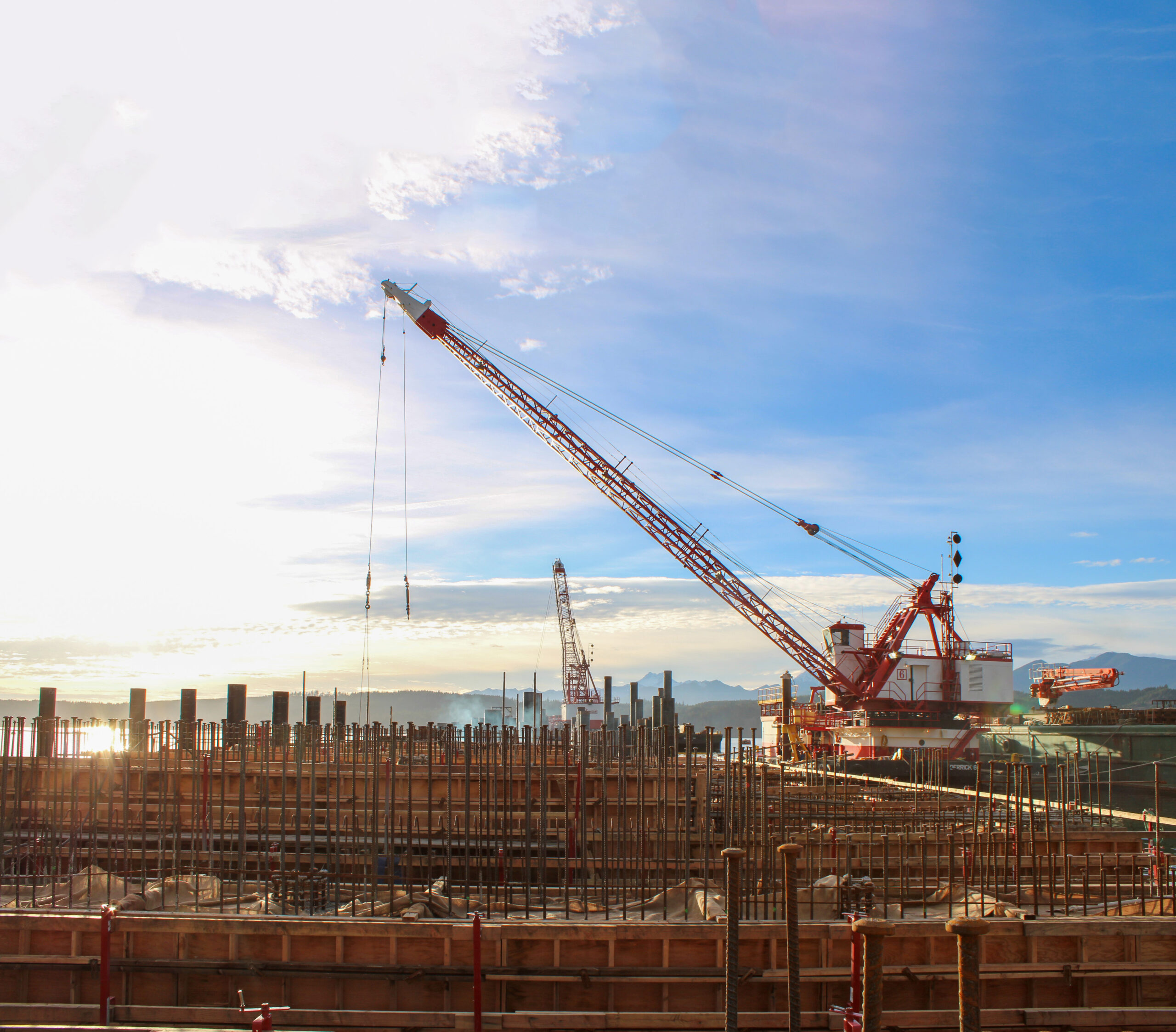
by J. Anthony Tedpahogo – Manson Copywriter
This Fall, Manson completed the P-834 SEAWOLF Class Service Pier Extension project at Naval Base Kitsap-Bangor (NBK) in Silverdale, WA. The three-year $91.6 million-dollar project for Naval Facilities Engineering Command (NAVFAC) Northwest, involved the demolition and construction of a 520 ft. by 68 ft. general purpose submarine berthing pier extension, two concrete floating camels, an upland parking lot, utility installations, a new air compressor building, existing pier building modifications, a small craft float, wave break. A new portal crane will also be added in 2023.
Preparing for SEAWOLF
This critical defense infrastructure project—which started in Spring 2020—began with the mobilization of Manson and subcontractor personnel to NBK. They logged timber to clear the way for the laydown area. Manson crews worked with civil subcontractor Tunista Construction, LLC to complete the site preparation work, which allowed Manson to store heavy equipment and tools for the project. Over the next two summers, the laydown area was transformed into a permanent parking lot supporting Naval operations at the new pier.
In the Fall of 2020, when it was time to begin pile driving operations for the construction of the pier extension, Skyline Steel provided and delivered the steel pipe piles—measuring 36 in. diameter, ranging from 97 ft. to 174 ft., and weighing up to 65,000 lbs.— to Manson’s Seattle Yard. Due to the long length of the piles, truck deliveries utilizing steer cars could only occur at night with mandatory police escort. The Seattle Yard Crane was used to load out the piles onto Manson barges for transport to the project site.
For pile driving operations, Manson derrick barge SCANDIA was equipped with a fixed spotter and hanging leads to eliminate the need for a template. A second set of offshore leads, commissioned by Manson’s Equipment group, allowed the crew to quickly swap between an APE 400 vibratory hammer and a D-100 impact hammer during the driving operation. Permit and environmental requirements provided limitations and conditions on which type of hammer could be utilized throughout the driving, so it was critical that the process of swapping the hammer was efficient. A rotating fleet consisting of the M50, M58, and M64 flat barges fed the piledriving operation, keeping a steady supply of piles moving from Seattle to NBK.
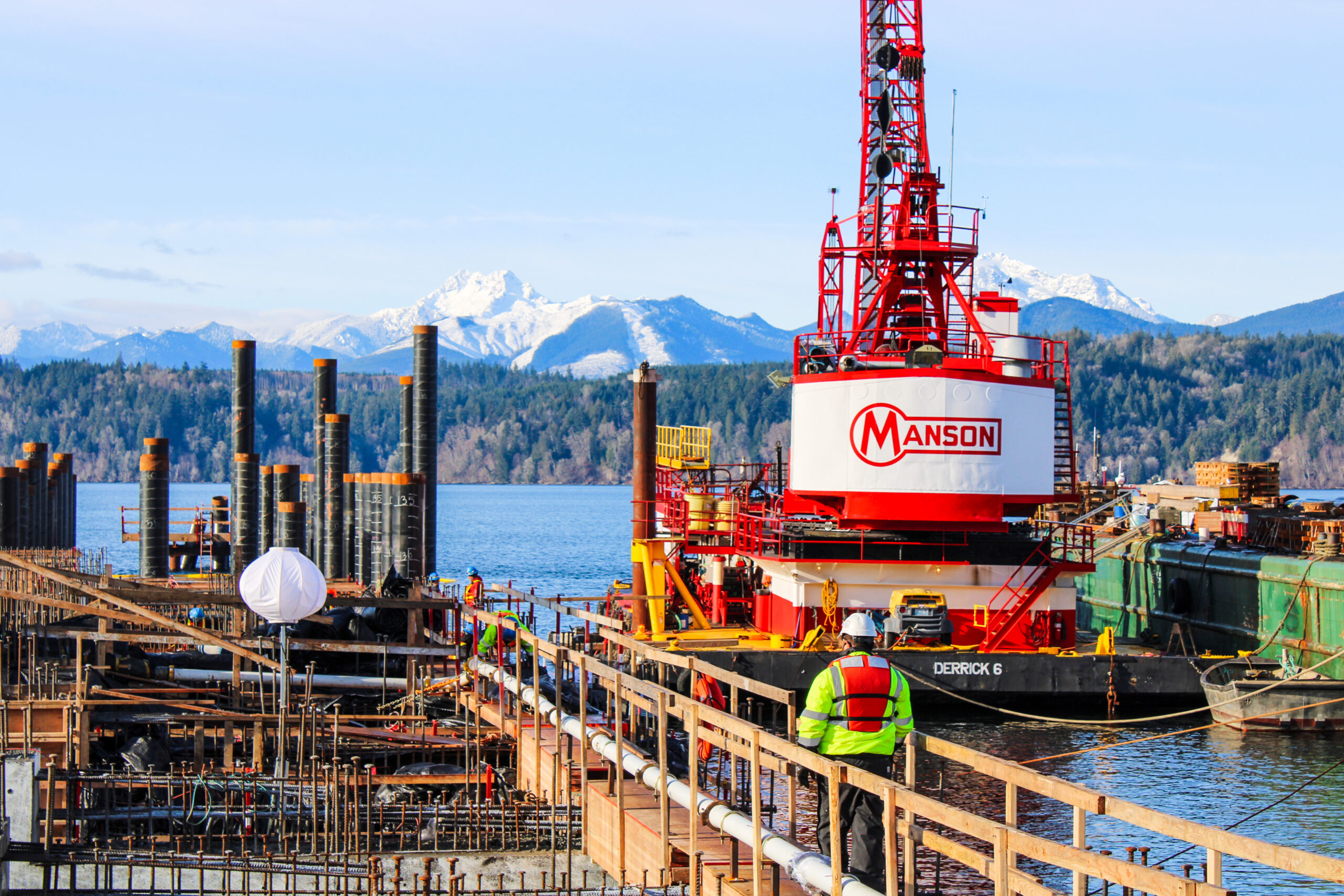
Challenges at SEAWOLF
At NBK, the SEAWOLF project team faced several challenges during the first phase of piledriving. The site contained a large amount of hard glacial till—sediment deposited from glaciers—that prevented crews from achieving design tip elevations. Manson’s project team collaborated daily with NAVFAC, and design engineering firm WSP USA, Inc. This included using as-built hammer blow count information to customize the appropriate final embedment depths and accommodate this geotechnical issue while maintaining the tight schedule.
While Manson crews were onsite performing pier demolition in preparation for pile driving, a group of harbor seals started to appear around the in-water work site. The project required that a team of professionally-trained marine mammal observers be present onsite during certain work activities – primarily while piledriving. At varying times, the SCANDIA crew had to halt piledriving operations when the seals were observed to be swimming around the jobsite. NAVFAC was able to work with the permit regulators to obtain permit clarifications which provided more flexibility for Manson crews to continue to piledriving, even when seals were within the work site.
Both the geotechnical and marine mammal challenges at NBK caused delays to Manson’s piledriving schedule. With a collaborative effort, the project team and SCANDIA crew finished their first season of piledriving before the in-water work window closed on January 15, 2021.
Constructing the Concrete Deck at SEAWOLF
This project was an extension of the existing pier structure, requiring extensive coordination with ongoing Naval operations to construct the concrete deck while the facility remained operational. The two piers—existing and new structure—connect at a narrow 50-ft. section and share the same existing access trestle. The new pier juts out at a 30-degree angle from the existing pier, so a connector bridge—known as a junction slab—was used to link the two structures together. All concrete and utility operations had to start at this complex and crowded junction slab before reaching other sections of the new pier.
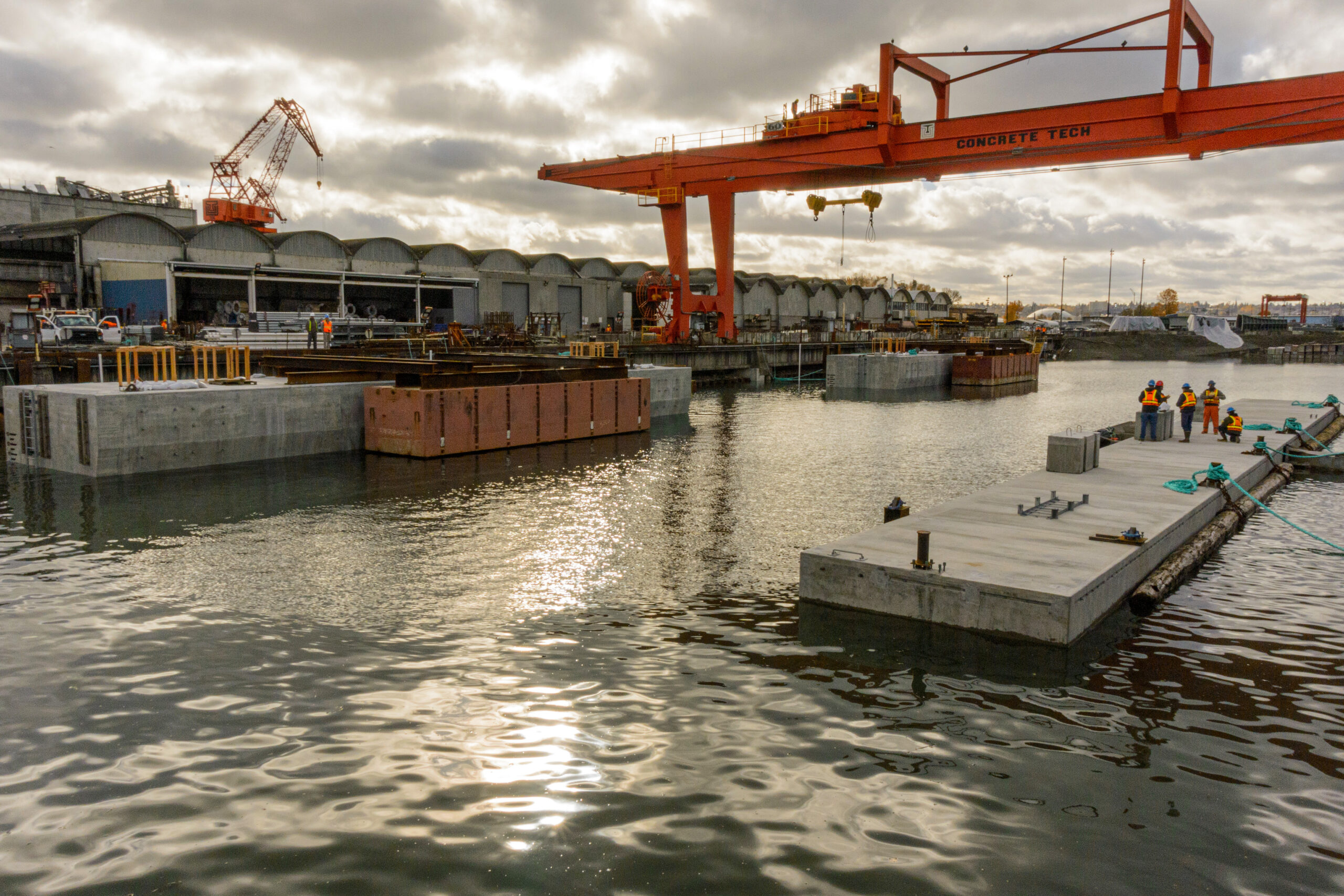
The new pier supports two modern submarines at a single berth, a pier-mounted portal crane, and an air compressor building that supports the adjacent existing service pier and operations facility. The pier contained mechanical trenches and electrical duct banks that were designed to run within the pier deck, creating very tight conditions for fitting in all the utility lines. Partnerships with mechanical & electrical subcontractors, Holmes Mechanical and Sturgeon Electric, allowed Manson to solve these challenges as a team in collaboration with the client.
Floating Camels
To berth the Navy’s state-of-the-art submarines, Manson installed two precast concrete floating camels to serve as the berthing structure, allowing submarines to dock at the pier. The camels are tapered to account for the submarine hull’s curvature and provide a safe and stable mooring setup designed to run up and down along driven guide piles throughout the tide cycle. The Navy has utilized steel-framed camels to berth submarines at their facilities. To increase the camel lifespans and decrease lifecycle costs, the Navy opted to use precast concrete for this pier. The camels were fabricated by Concrete Technology Corporation within their graving dock in Tacoma, WA. Casting in the graving dock allows the camel to be built in the “dry” and then floated out and towed to the jobsite after the graving dock has been re-flooded. Due to the non-uniform shape of the camels and natural instability of them until they are secured and trimmed and ballasted at the pier to sit level, the structures required supplemental floatation and careful handling from the moment they were launched in the graving dock. In addition, all the voids were filled with closed cell foam to mitigate against any future leaks.
The SEAWOLF project presented a variety of challenges, and Manson’s project team rose to the occasion. Through collaboration, partnership and innovation, the team worked diligently to successfully complete the work.