Pile Splicing: Fundamentals, Methods, Equipment, and Quality Control
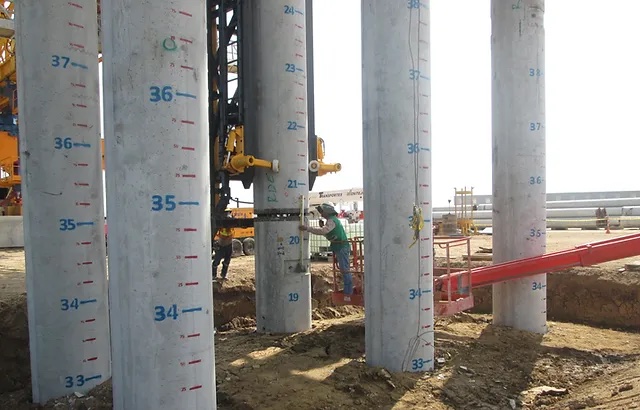
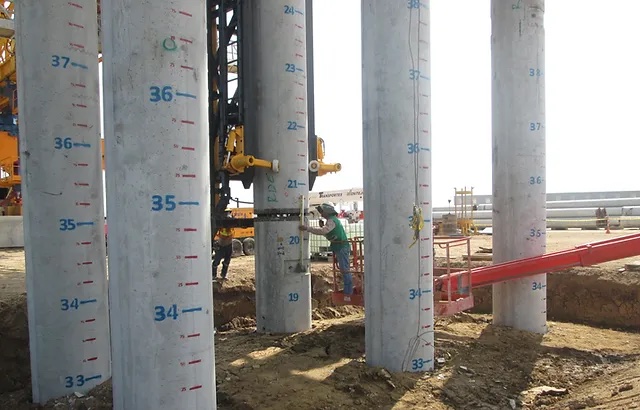
View the complete article here.
Introduction
Pile splicing is an indispensable technique that enables the installation of deep foundations where single-piece piles cannot be used due to various limitations. This guide will explore the fundamentals of pile splicing—outlining the essential considerations and methods that contractors must navigate to extend pile lengths and ensure structural soundness.
Fundamentals of Pile Splicing
Pile splicing is a critical procedure, enabling the extension of piles beyond their initial lengths to meet the structural requirements of various construction projects.
To recap, there are two main types of piles used in construction: end-bearing piles, which transfer load through the pile tip into a solid soil layer—and friction piles, which transfer load along the pile’s length through skin friction between the pile surface and the surrounding soil. The choice between these types depends on the soil characteristics and the project requirements.
Key Reasons for Splicing Piles
Pile splicing is necessitated by several factors:
- Length limitations: The maximum length of prefabricated piles is often constrained by manufacturing, handling, and transportation capabilities. Splicing allows for the extension of these piles to required depths that single-length piles cannot achieve.
- Transportation issues: Transporting very long piles can be logistically challenging and expensive, especially through urban areas or over long distances. Splicing enables the transportation of shorter segments that can be assembled on-site.
- Site conditions: Site-specific conditions such as limited headroom under bridges or inside buildings may restrict the length of pile that can be driven. Splicing shorter segments in situ allows for the construction of deep foundations in these constrained environments.
Overview of the Different Methods of Pile Splicing
Pile splicing methods vary depending on the type of pile material, the required strength of the splice, and the project’s specific requirements. The most common techniques include:
Primarily used for steel piles, butt welding involves aligning the ends of two pile segments and welding them together across their entire circumference. This method provides a strong and durable connection capable of bearing significant loads.
A specialized form of welding used for splicing piles, where heat generated by mechanical friction between the contacting surfaces is used to forge the piles together. Friction welding is less common and typically applied in specific conditions where traditional welding is not feasible.
Mechanical fasteners uses bolts, screws, or other mechanical fasteners to join pile segments. It is often used for temporary structures or where welding is not suitable. Mechanical fasteners provide the advantage of being relatively quick and easy to install but may not offer the same strength as welded splices.
For concrete and some types of steel piles, sleeve or coupler splicing involves sliding a sleeve over the joint between two pile segments and filling the space with concrete or welding it in place for steel piles. This method is effective for aligning and securing the pile segments, ensuring a continuous load path.
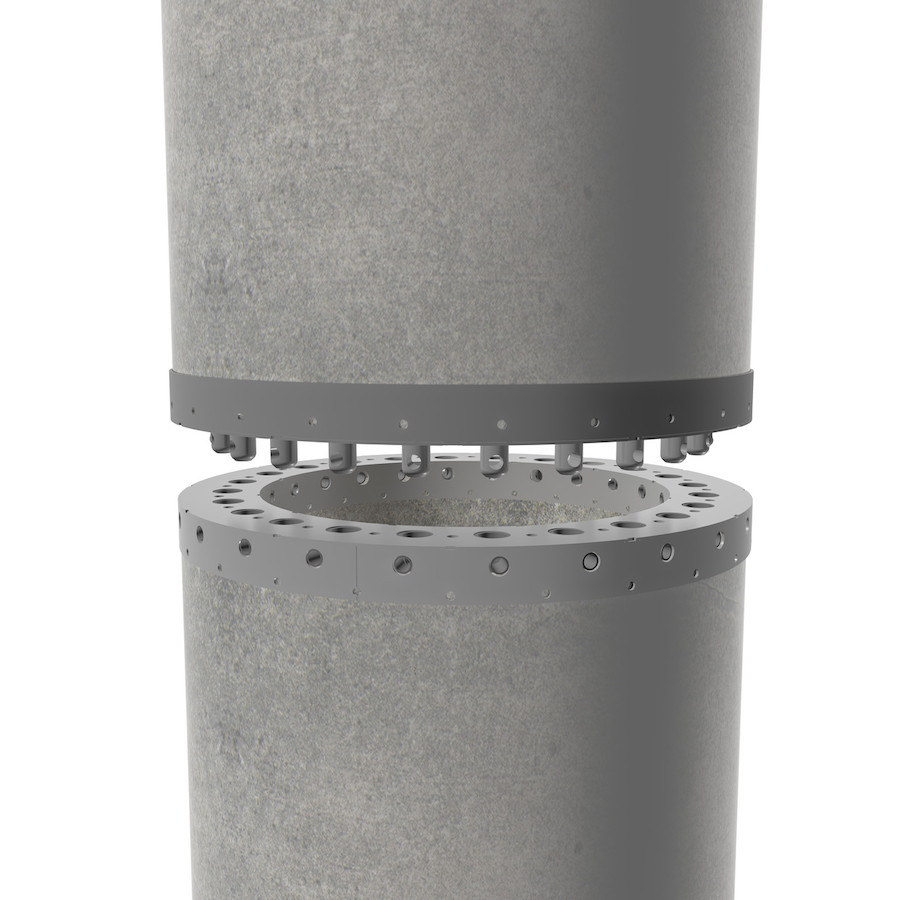
Technical Aspects of Pile Splicing
The technical aspects of pile splicing involve a deep understanding of the procedures, materials, and quality control measures that are critical to the structural integrity of deep foundations.
Detailed Explanation of the Most Common Pile Splicing Techniques
The two most common techniques for pile splicing are welding and mechanical splicing. Each has its procedures, applications, and material considerations—which are pivotal in ensuring the stability and longevity of the splice.
Welding: Procedures, Equipment, and Safety Measures
Welding is a widely used method of splicing steel piles due to its ability to create a continuous, monolithic structure. The procedure typically involves:
- Preparing the pile ends: The ends of the piles to be spliced must be clean—free from rust and cut square to each other.
- Alignment: The pile segments are carefully aligned to ensure the axis is continuous and the weld will be strong across the entire circumference.
- Welding process: A full penetration butt weld is commonly employed. This involves the use of a beveled joint design to allow the weld to fully penetrate the thickness of the pile.
- Testing: Upon completion—non-destructive testing methods, such as ultrasonic testing, are used to verify the integrity of the weld.
The equipment required for welding includes welding machines, electrodes, grinders for preparing the weld surfaces, and various tools for aligning and securing the piles. Safety measures are paramount during welding—including the use of personal protective equipment, fire prevention measures, and trained personnel to handle the equipment and execute the weld.
Mechanical Splices: Types, Applications, and Installation Process
Mechanical splicing involves connecting pile segments using various types of fasteners or couplers. The types include:
- Bolted splices: These utilize high-strength bolts and may involve the use of splice plates or sleeves.
- Screwed splices: These involve screw connections that can be tightened to hold the pile segments together.
- Pressed splices: This type utilizes hydraulic jacks to press-fit endplates or sleeves onto pile ends.
The applications for mechanical splices are diverse, ranging from temporary works to permanent installations where welding is impractical. The installation process involves aligning the pile segments, attaching the mechanical connectors, and securing them according to the manufacturer’s specifications.
Material Considerations: Steel, Concrete, and Composite Piles
The choice of splicing method is often dictated by the type of pile material:
- Steel piles: Typically spliced by welding, but can also be joined using mechanical splices.
- Concrete piles: Often joined using dowel bars and grout, or with pre-fabricated splicing components.
- Composite piles: Splicing can involve a combination of techniques suitable for the materials involved, such as a fiberglass sleeve with adhesive for FRP (Fiber-Reinforced Polymer) piles.
Quality Control and Assurance in Pile Splicing Processes
Quality control and assurance are essential to ensure that the splicing process is performed correctly. This includes:
- Certification of welders and operators: Personnel must be qualified to the relevant standards.
- Inspection: Continuous inspection during the splicing process to ensure compliance with design specifications.
- Testing: Post-splicing testing to verify the structural integrity of the splice.
Challenges and Solutions in Aligning and Securing Pile Segments
Aligning and securing pile segments can present challenges, particularly when dealing with large or heavy pile segments or when working in difficult site conditions. Solutions include:
- Use of templates and guides: These assist in maintaining alignment during splicing.
- Stabilization structures: Temporary structures can hold piles in place during the splicing process.
- Adjustment mechanisms: Some splicing systems incorporate features to make fine adjustments to alignment easier.
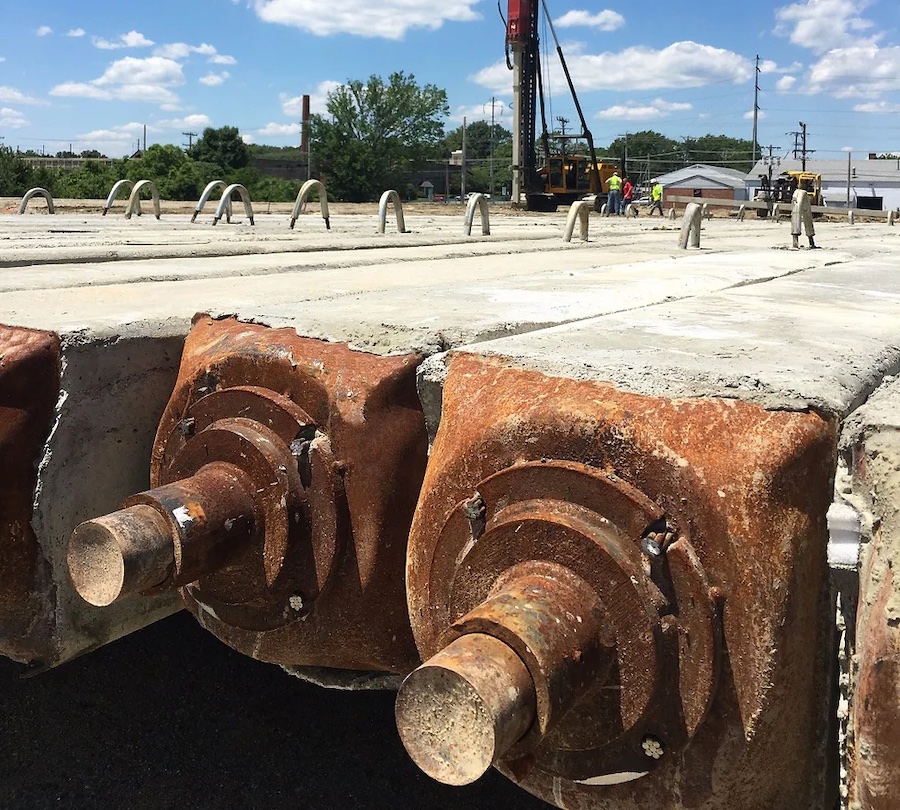
Practical Insights for Contractors
When it comes to pile splicing, contractors are likely to face a myriad of considerations that can impact the success and efficiency of their operations.
Best Practices in Planning and Executing Pile Splicing Operations
Effective planning and execution of pile splicing operations are critical to the project’s success. Here are some best practices to consider:
- Advance planning: Engage in thorough pre-planning—including a detailed review of the project specifications, pile design, and the splicing method.
- Coordination: Ensure clear communication and coordination among the design team, field personnel, and material suppliers.
- Equipment and materials: Confirm the availability of proper equipment and materials well ahead of the operation.
- Training: Provide specialized training for crew members to ensure they are adept at handling the specific splicing techniques required for the project.
- Trial assemblies: Perform trial assemblies when possible to anticipate and address potential alignment or connection issues.
Cost Considerations: Estimating and Managing Expenses Related to Pile Splicing
Cost management is a key concern in pile splicing operations. To manage costs effectively:
- Accurate estimation: Develop accurate cost estimates that account for all aspects of the splicing operation—including labor, materials, equipment, and contingencies.
- Efficiency: Optimize the splicing process for efficiency to minimize labor hours and equipment rental times.
- Bulk purchasing: Consider bulk purchasing or leasing of splice materials and equipment to reduce costs.
- Waste reduction: Implement practices to minimize waste of materials, such as precise cutting of pile segments and reuse of templates and guides.
Safety Guidelines for Pile Splicing on Construction Sites
Safety is paramount during pile splicing operations due to the heavy materials and high-risk activities involved. Safety guidelines include:
- Risk assessment: Conduct a thorough risk assessment specific to the pile splicing activities.
- Safety protocols: Develop and enforce strict safety protocols, including proper use of personal protective equipment (PPE) and safe handling procedures.
- Emergency plans: Prepare emergency response plans for incidents that could occur during splicing operations.
- Regular training: Hold regular safety training and briefings to keep safety front of mind for all workers involved in the splicing operation.
By adhering to these best practices, cost-saving strategies, safety guidelines, and legal requirements—contractors can execute pile splicing operations that are not only cost-effective and safe but also compliant with the stringent standards governing construction projects.