From Pile Driving to Superstructure: Mastering Dock Construction
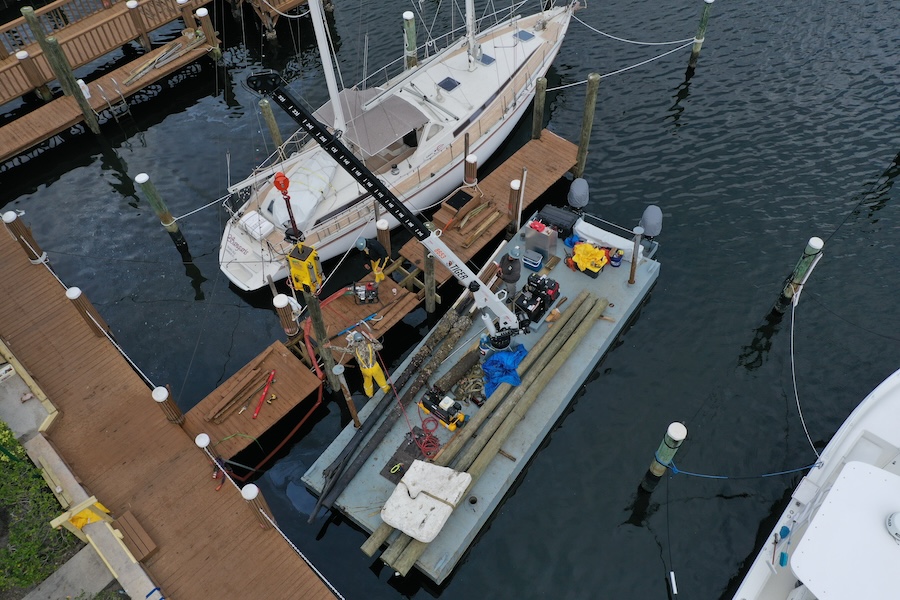
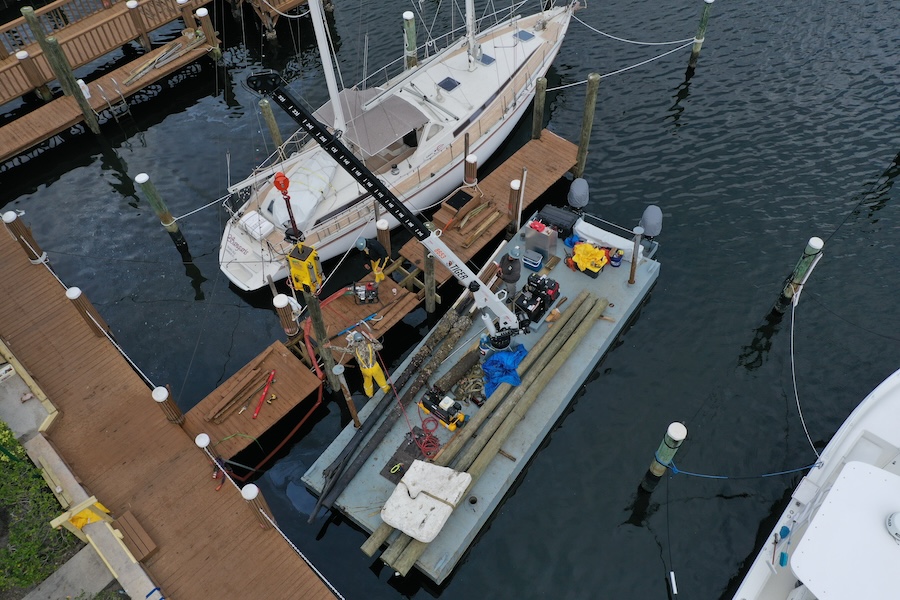
View the complete article here.
Building a dock in a marine environment involves precise engineering, time-tested construction techniques, and a thorough understanding of local conditions. This guide provides an in-depth look at every stage of the process, from choosing between fixed and floating designs to integrating robust foundation systems and superstructure components. It also explores the critical roles of pile driving, pre-construction planning, and long-term maintenance strategies to ensure durability and safety. Whether you’re a marine contractor or a pile driving specialist, this guide offers practical insights and expert recommendations to help you execute successful dock projects.
Overview of Dock Construction
Dock construction is a multifaceted process that combines robust engineering principles with innovative construction techniques to create structures capable of withstanding the harsh marine environment.
Types of Docks
When considering dock design, it’s essential to evaluate whether a fixed structure anchored to the seabed or a floating platform adaptable to changing water levels best suits the project’s environmental conditions and operational requirements.
Fixed docks: Fixed docks are anchored securely to the seabed, typically using robust foundations such as driven or drilled pile systems. This design ensures that the dock remains in a constant position—providing stability and reliability for operations that require a permanent, unmoving structure. Fixed docks are ideal in locations with minimal tidal variations or where long-term, high-load capacities are necessary.
Floating docks: Floating docks, often referred to as pontoon docks, rely on buoyant platforms that rise and fall with the tides. These docks are usually secured by cables or chains and can be repositioned or adjusted more readily than fixed docks. Their flexibility makes them particularly suitable for environments with significant tidal ranges or where temporary or seasonal configurations are desired.
When planning dock construction, it’s important to recognize that the intended application—whether it’s for commercial shipping, industrial operations, or recreational use—dictates specific design considerations, materials, and performance standards tailored to each unique environment.
Commercial docks: Designed to support heavy shipping and cargo operations—commercial docks prioritize load-bearing strength, efficient cargo handling, and integration with transportation networks. Their construction often involves reinforced materials and advanced engineering techniques to accommodate continuous, high-volume use.
Industrial docks: While industrial docks share many similarities with commercial docks—they are tailored to support the specific needs of manufacturing, storage, or processing facilities. This may include specialized equipment for handling bulk materials or provisions for on-site processing activities.
Recreational docks: Recreational docks focus on accessibility, aesthetics, and user comfort. They are constructed to support leisure activities such as fishing, boating, or waterfront dining. Although they might not require the same heavy-duty structural specifications as commercial or industrial docks, attention to durability and safety in the marine environment remains paramount.
Key Components of a Dock Structure
The foundation is the critical underpinning of any dock structure, providing the necessary stability and support for the entire system. In marine construction, pile systems are the most prevalent foundation solution.
Pile systems: Piles are long, slender columns driven deep into the seabed to transfer the weight of the dock to more stable soil or rock layers below. The selection of pile material—whether steel, concrete, or timber—depends on the specific site conditions, expected loads, and environmental factors. Proper installation is essential—as the integrity of the pile system directly influences the dock’s ability to withstand dynamic forces such as waves, currents, and operational impacts.
The superstructure of a dock comprises all components that rise above the waterline and directly interact with users and vessels.
Decking: The deck forms the working platform of the dock and must be engineered to handle heavy loads, resist corrosion, and offer durability against constant exposure to saltwater and fluctuating weather conditions. Material choices and construction methods are selected to balance performance with cost efficiency.
Fenders: Fenders protect both the dock and approaching vessels from damage during berthing. They absorb and distribute the energy generated when a vessel makes contact with the dock, thereby preventing costly repairs and ensuring operational safety.
Mooring systems: Mooring systems are critical for securing vessels to the dock. These systems are designed to accommodate various sizes and types of vessels while providing the flexibility to adapt to changing sea conditions. Effective mooring solutions enhance safety and operational efficiency by ensuring a secure and stable connection between the vessel and the dock.
The Role of Pile Driving in Dock Construction
Foundation installation: The process involves driving piles into the seabed to create a stable, load-bearing foundation capable of supporting the superstructure above. Precision in the installation process is vital—as the alignment, depth, and spacing of each pile directly affect the overall integrity and performance of the dock.
Load distribution: Properly installed piles ensure that the forces generated by waves, currents, and operational loads are effectively transferred to the ground. This load distribution minimizes the risk of structural failure and prolongs the dock’s lifespan by preventing uneven settlement or damage.
Coordination and expertise: Pile driving demands close collaboration between design engineers and pile driving contractors. The selection of the appropriate pile type and the precise execution of the driving process require both technical expertise and practical experience, ensuring that the dock is built to withstand both expected and unforeseen stresses.
Pre-Construction Planning and Site Assessment
Successful dock construction begins long before the first pile is driven. A comprehensive pre-construction phase lays the foundation for a project that is not only structurally sound but also compliant with environmental and regulatory standards.
Feasibility Studies and Site Surveys
Geotechnical investigations and hydrodynamic studies: Understanding the physical characteristics of the construction site is paramount. Geotechnical investigations assess the soil composition, load-bearing capacity, and other critical factors that influence foundation design. In parallel—hydrodynamic studies analyze water movement, tidal patterns, and wave dynamics.
Environmental assessments: Environmental assessments play a key role in identifying and mitigating the potential impact of construction activities on local ecosystems. These assessments evaluate factors like water quality, marine habitats, and shoreline integrity—ensuring that the project minimizes ecological disruption.
Regulatory Permitting and Compliance
Local, state, and federal regulations: Dock construction projects are subject to a wide array of regulations that govern everything from zoning and coastal management to construction standards and safety protocols. Early and thorough review of these regulations helps to identify all necessary permits and approvals, reducing the risk of delays or costly modifications during construction. Contractors must work closely with regulatory agencies to ensure that every aspect of the project adheres to the relevant legal frameworks.
Environmental impact mitigation: In addition to meeting regulatory standards, projects often require specific measures to mitigate environmental impacts. These might include implementing noise reduction strategies during pile driving, using spill containment systems, or establishing habitat restoration initiatives. Proactive environmental impact mitigation not only protects local ecosystems but also fosters positive relationships with regulatory bodies and the community.
Stakeholder Engagement and Project Financing
Stakeholder engagement: Engaging stakeholders—including local community leaders, environmental groups, and regulatory agencies—ensures that diverse perspectives are considered in the planning process. Early dialogue helps to identify potential concerns and build consensus around project goals and methodologies. This collaborative approach can lead to innovative solutions and smoother regulatory approvals.
Project financing: Securing project financing is equally critical. Detailed feasibility studies and clear regulatory compliance plans form the backbone of any funding proposal. By demonstrating a solid understanding of both the technical challenges and the regulatory landscape, contractors can build investor confidence. Sound financial planning ensures that the project is well-resourced, reducing the likelihood of delays due to funding shortfalls and allowing for flexibility in managing unforeseen challenges.
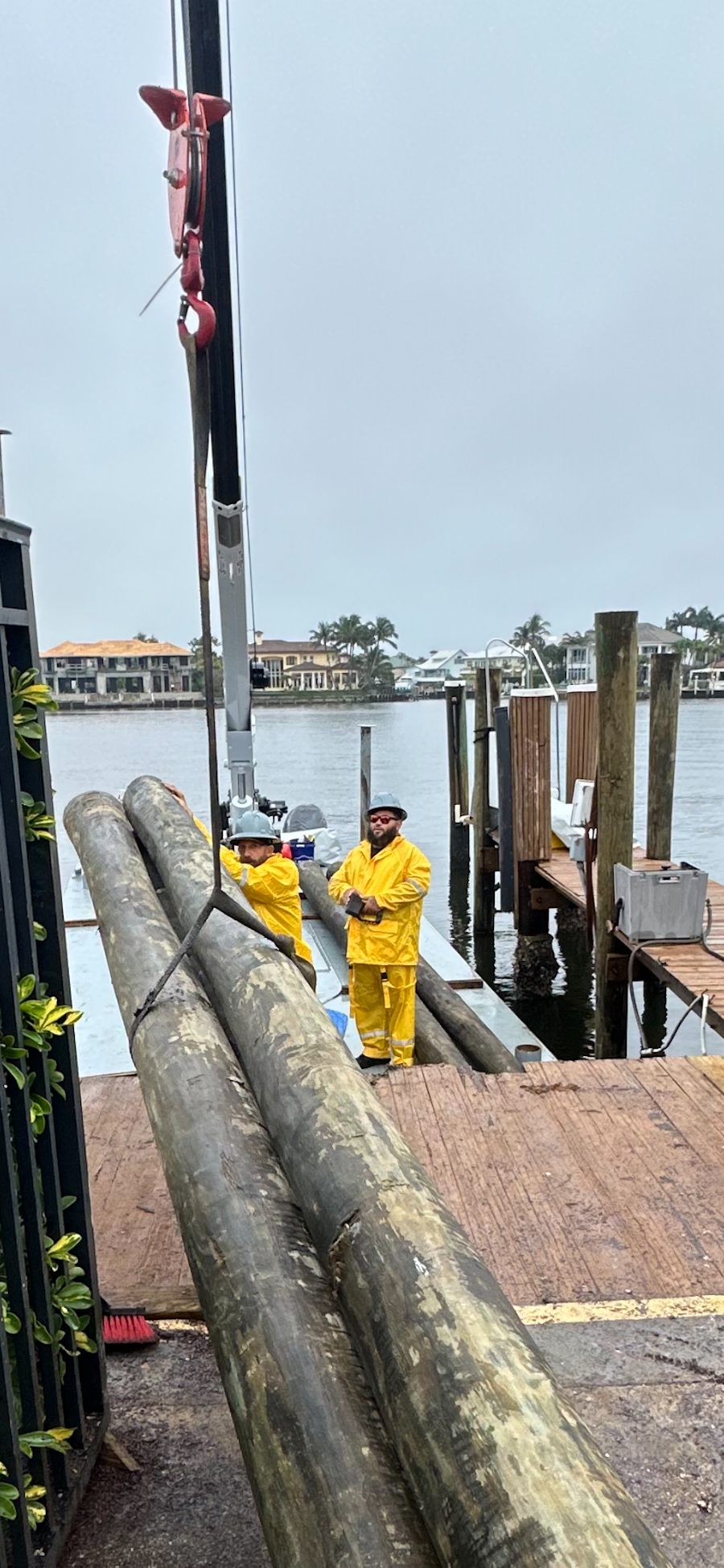
Design and Engineering Considerations
The design and engineering phase establishes the critical parameters that ensure structural integrity, durability, and safety in challenging marine environments.
Structural Design Principles
A comprehensive load analysis is fundamental in designing a dock that stands the test of time. Engineers must evaluate both static loads, the constant forces exerted by the dock’s own weight and fixed installations—and dynamic loads, which include transient forces from waves, operational activities, and moving vehicles. By understanding these varied load scenarios, engineers can determine the necessary strength and resilience of the structure—ensuring that every component performs reliably under both predictable and unexpected conditions.
Marine environments introduce unique challenges that require specialized design considerations. Dock structures must be robust enough to withstand the relentless impact of waves, the continuous push of currents, and the cyclical forces of tides. Designers employ advanced simulation tools to model these marine forces—enabling them to optimize the dock’s shape, orientation, and damping features. This proactive approach not only minimizes potential damage but also enhances the dock’s overall performance and longevity in the face of relentless environmental pressures.
Foundation Design
A stable foundation is the cornerstone of any dock, and selecting the appropriate pile system is crucial. Engineers assess various criteria when choosing piles, including:
- Material: Options such as steel, concrete, or timber each offer distinct benefits and limitations in terms of strength, durability, and corrosion resistance.
- Type: Whether to use driven piles, drilled (bored) piles, or a hybrid system depends on site-specific factors and the anticipated loads.
- Configuration: The arrangement and spacing of the piles directly influence the load distribution and overall stability of the dock. A carefully engineered configuration ensures that the forces from the superstructure are effectively transferred to the underlying seabed.
The effectiveness of any pile system is intrinsically linked to the characteristics of the underlying soil or seabed. Detailed geotechnical studies are conducted to determine soil composition, density, and variability—which are critical in predicting how the piles will perform under load. A mismatch between pile type and soil conditions can lead to uneven settlement or structural failures. Thus, the foundation design must be tailored to the specific geotechnical profile of the project site—ensuring optimal performance and long-term stability.
Integration of Pile Driving Specifications
Coordination between design engineers and pile driving contractors: The integration of design and execution is essential for the successful implementation of a dock’s foundation. Close collaboration between design engineers and pile driving contractors ensures that the theoretical specifications developed during the design phase are achievable in the field. This cooperative effort facilitates real-time adjustments during installation, ensuring that the practical aspects of pile driving—such as installation depth, orientation, and load transfer—align precisely with the design intent.
Tolerances and alignment for optimal load transfer: Precision in pile installation is non-negotiable when it comes to effective load transfer. Strict tolerances in pile placement and alignment are maintained to ensure that each pile functions as intended. Any deviation from the planned specifications can result in uneven load distribution, which might compromise the dock’s structural integrity. By employing advanced monitoring techniques and quality control measures, contractors can verify that each pile is installed within the prescribed tolerances—ensuring a robust connection between the dock superstructure and its foundation.
Material Selection and Construction Techniques
Selecting the right materials and construction methods is crucial for ensuring that dock structures are both durable and efficient.
Pile Materials
Steel piles: Steel piles are renowned for their exceptional strength and durability, making them ideal for high-load applications in aggressive marine environments. Their high tensile capacity and resistance to dynamic forces allow them to effectively transfer both static and dynamic loads. Additionally, modern coatings and cathodic protection systems help mitigate corrosion—ensuring a long service life.
Concrete piles: Concrete piles are a popular alternative, offering excellent compressive strength and resistance to the harsh marine environment. They provide a robust foundation, especially in conditions where corrosion of steel may be a concern. Precast or cast-in-place concrete piles can be engineered to meet specific load and environmental requirements, with reinforcement options available to further enhance their structural performance.
Timber piles (when applicable): Timber piles, while less common in high-load or long-term installations, still have their place in certain scenarios. They are often used for temporary structures, smaller recreational docks, or in locations where local material availability and cost are primary considerations. When properly treated and maintained, timber piles can perform adequately—though they generally require more frequent inspections and maintenance compared to steel or concrete options.
Pile Types and Installation Methods
Driven piles: Driven piles are installed by using impact hammers or vibratory drivers to force the pile into the ground. This method provides immediate load-bearing capacity and is especially effective in soils with favorable compaction characteristics. Driven piles often result in a denser surrounding soil profile, which can enhance overall stability.
Drilled (bored) piles: Drilled or bored piles involve the removal of a core of material to create a hole that is subsequently filled with reinforced concrete. This method is preferable in areas where noise, vibration, or environmental concerns make driving operations less desirable. Drilled piles allow for precise placement and can be optimized for sites with challenging soil conditions.
Considerations for selection based on site conditions: Choosing between driven and drilled piles depends on several factors—including soil composition, environmental impact, noise and vibration constraints, and the specific load requirements of the dock. For instance, sites with highly variable soil conditions or sensitive marine ecosystems may benefit from the controlled installation of drilled piles—while more robust soil profiles might favor the efficiency of driven piles.
Advances in Construction Equipment and Techniques
Modern technology continues to revolutionize dock construction—offering improved efficiency, precision, and environmental stewardship.
Modern pile driving machinery and monitoring systems: Recent advancements in pile driving equipment include the integration of computer-controlled systems that monitor driving parameters in real time. These systems ensure that each pile is installed with optimal force and precision, minimizing deviations from the design specifications. Remote monitoring technologies enable continuous oversight, providing critical data on pile integrity and performance and allowing for immediate adjustments if necessary.
Innovative methods to reduce vibration and noise: Environmental considerations are increasingly important in marine construction. To mitigate the impact of vibration and noise on surrounding marine life and nearby communities, innovative techniques have been developed. These include:
- Silent pile driving systems: Utilizing alternative energy sources or advanced hydraulic mechanisms, these systems significantly reduce the acoustic footprint of pile driving operations.
- Vibration dampening accessories: Modern equipment may incorporate vibration isolation pads or other dampening technologies that minimize the transmission of vibration to the surrounding environment.
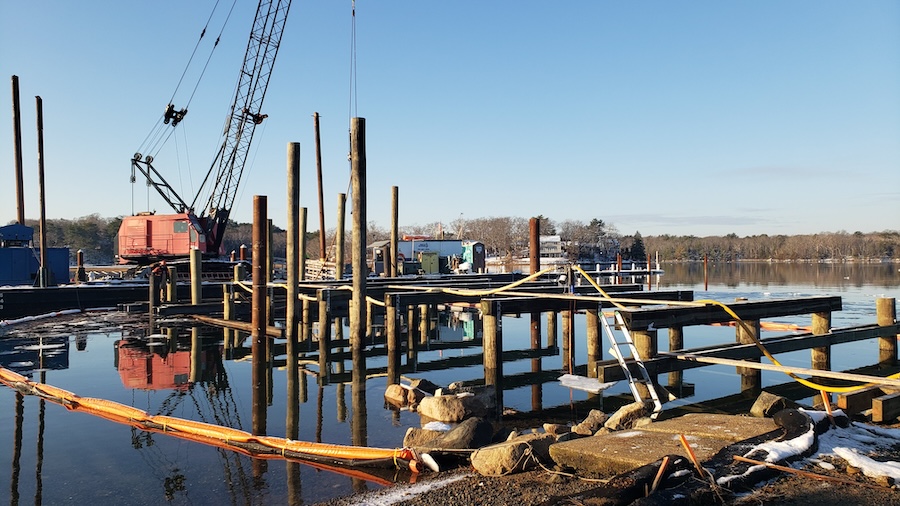
Pile Driving Operations
Effective pile driving operations are central to establishing a durable and stable dock foundation. This phase requires meticulous planning, precise execution, and stringent quality and safety protocols to ensure that every pile meets the performance standards necessary for long-term structural integrity.
Site Preparation for Pile Driving
Access and staging: Establishing secure and organized access routes for heavy machinery and personnel is crucial. This includes preparing staging areas where equipment can be assembled, maintained, and operated safely—ensuring that the worksite is organized and free from unnecessary hazards.
Environmental controls: Prior to pile driving, environmental controls must be put in place to mitigate any potential negative impacts on the surrounding marine ecosystem. This can involve setting up protective barriers, managing sediment dispersion, and scheduling operations to minimize disruptions during sensitive times for local wildlife.
Pile Driving Techniques and Equipment
Hammer selection and energy delivery: Choosing the right type of hammer—whether impact, vibratory, or hydraulic—is critical. The hammer must deliver the precise energy required to drive each pile to the designated depth without causing damage or undue vibration. The energy delivery system should be calibrated based on the pile material, size, and the specific soil conditions at the site.
Real-time monitoring and adjustments: Modern pile driving operations benefit from advanced monitoring systems that provide real-time data on driving progress—including penetration rates, energy absorption, and pile alignment. This continuous feedback loop allows operators to make immediate adjustments, ensuring that each pile is installed within the prescribed tolerances and achieves optimal load-bearing performance.
Quality Assurance and Testing
Integrity testing: Once piles are installed, integrity testing such as dynamic load testing and static load testing are conducted to verify that each pile can withstand the expected operational loads. These tests are critical for identifying any issues with pile installation, such as misalignment or insufficient embedment—and for confirming that the foundation will perform as designed under both static and dynamic conditions.
Documentation and reporting requirements: Detailed records of the pile driving process—including testing results, installation parameters, and any adjustments made during operations—must be maintained. This documentation serves as an essential reference for future maintenance, regulatory compliance, and quality audits—ensuring that the project meets all contractual and industry standards.
Safety Protocols During Pile Driving
Equipment safety: Regular inspections, maintenance, and calibration of pile driving machinery are essential to prevent mechanical failures that could lead to accidents. Safety features such as emergency stop controls, protective enclosures, and proper load monitoring systems should be standard on all equipment.
Worker safety and training: Comprehensive training programs ensure that all crew members are well-versed in safe operating procedures, emergency response plans, and the specific hazards associated with pile driving. Personal protective equipment (PPE) must be provided and used at all times, and safety protocols should be rigorously enforced to prevent accidents and injuries.
Dock Superstructure Construction
The superstructure of a dock is the visible, functional component that interfaces directly with users and vessels. Its construction not only contributes to the aesthetic appeal of the dock but also ensures operational efficiency, safety, and durability.
Decking Systems and Materials
The decking forms the primary platform of the dock, providing a stable surface for operations and access. The selection of decking systems and materials is a critical decision that impacts the overall performance and longevity of the dock.
Precast concrete decking: Precast concrete components are manufactured offsite under controlled conditions and then transported to the construction site. This method offers high quality control, faster installation times, and consistent material properties—which are vital for ensuring a uniform and durable deck surface.
Cast-in-place decking: In contrast, cast-in-place decking is poured and cured directly at the construction site. This approach provides greater design flexibility, allowing for custom shapes and dimensions tailored to specific project needs. However, it requires meticulous onsite quality control to achieve comparable strength and durability.
Given the harsh marine environment, corrosion protection is a paramount consideration in decking construction. Protective measures such as corrosion-resistant coatings, sealants, and the use of reinforced materials help safeguard the decking against saltwater exposure, weathering, and mechanical wear. Proper corrosion protection extends the lifespan of the deck, reducing maintenance costs and ensuring a reliable operational platform over the long term.
Integration with Pile Foundations
Pile caps, beams, and connection details: The interface between the deck and the foundation is typically managed through pile caps and beams that distribute loads evenly across the supporting piles. Detailed engineering of these connection points is crucial—proper reinforcement, precise alignment, and secure bonding between elements ensure that the forces acting on the deck are effectively transferred to the pile system. This careful integration minimizes potential weak points and enhances the overall structural resilience of the dock.
Load distribution and flexibility: The design of the superstructure must accommodate not only static loads but also dynamic stresses caused by environmental forces and operational activities. Flexible design strategies, such as incorporating expansion joints or engineered load distribution systems, help manage these forces. By ensuring that loads are evenly dispersed across the pile foundation, the dock can better withstand variations in stress and avoid localized failures that might compromise the structure’s integrity.
Ancillary Structures and Installations
Beyond the primary decking and foundational integration, ancillary structures contribute significantly to the functionality and safety of the dock.
Fenders: Fenders act as protective buffers that absorb the impact when vessels make contact with the dock, preventing damage to both the structure and the vessels. They are designed to dissipate energy effectively and are positioned strategically along the dock’s perimeter.
Mooring systems: Mooring systems secure vessels to the dock, ensuring stability even in fluctuating environmental conditions. The design of these systems takes into account factors such as vessel size, tidal movements, and wave action—providing a reliable and flexible connection that accommodates various docking scenarios.
To enhance operational efficiency and ensure user safety—docks are often equipped with a range of ancillary installations, including:
- Lighting: Adequate lighting is essential for safe nighttime operations, enhancing visibility for both personnel and vessels. Energy-efficient lighting solutions not only improve safety but also contribute to sustainability goals.
- Signage: Clear and strategically placed signage provides critical information regarding navigation, safety protocols, and operational guidelines. Effective signage helps prevent accidents and streamlines daily operations.
- Safety features: Additional safety measures—such as handrails, non-slip surfaces, and emergency communication systems—are integrated into the dock design. These features ensure that the superstructure meets regulatory safety standards and provides a secure environment for all users.
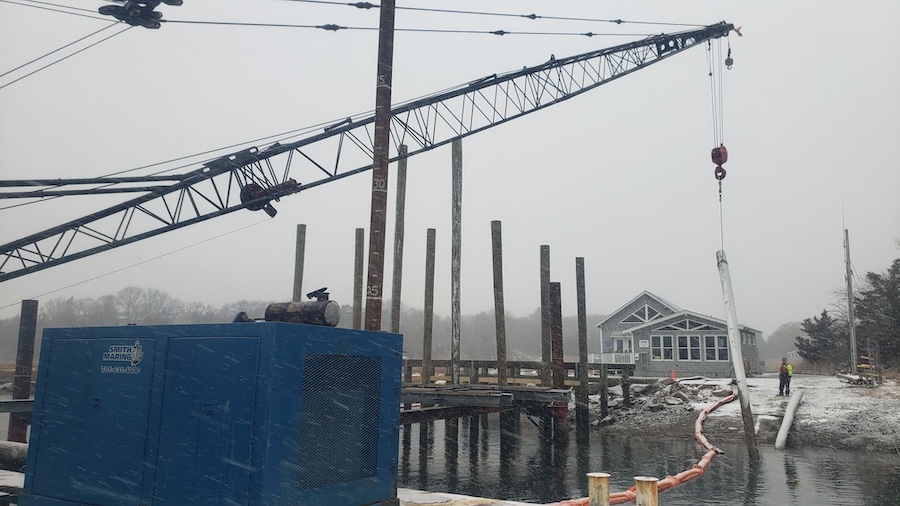
Maintenance, Repair, and Inspection
A robust maintenance, repair, and inspection program is essential to extend the service life of a dock and ensure its ongoing safety and functionality. Regular upkeep not only preserves the structural integrity of the dock but also mitigates costly repairs down the line.
Routine Maintenance Practices
Regular inspections and condition monitoring: Consistent inspections form the cornerstone of an effective maintenance program. Regular visual and technical inspections help identify early signs of wear, corrosion, or other forms of structural degradation. Condition monitoring systems, such as sensors and automated data logging, can track key performance indicators—alerting operators to potential issues before they escalate into significant problems. By scheduling frequent assessments—contractors can ensure that all components, from the decking to the pile foundations, remain in optimal condition.
Scheduled maintenance activities: Beyond inspections, planned maintenance activities are vital to the long-term health of the dock. These scheduled tasks might include cleaning, repainting with corrosion-resistant coatings, sealing cracks, and replacing worn components. A well-defined maintenance schedule not only helps in preventing deterioration but also minimizes disruptions to the dock’s operational use.
Repair Strategies
Addressing corrosion and structural degradation: Corrosion and structural degradation are common challenges in the marine environment. Repair strategies should focus on both immediate remediation and long-term prevention. This can involve removing corroded sections, applying protective coatings, and reinforcing vulnerable areas to restore structural integrity. Advanced diagnostic tools, such as ultrasonic testing or ground-penetrating radar, may be employed to assess the extent of degradation and guide targeted repair interventions.
Upgrades and retrofits for evolving requirements: As operational demands evolve and new technologies emerge, upgrading and retrofitting existing dock structures becomes increasingly important. These upgrades can include modernizing lighting and safety systems, enhancing load-bearing capacities, or incorporating sustainable materials that extend the dock’s service life.
Life-Cycle Cost Analysis
Budgeting for long-term durability and repairs: A thorough life-cycle cost analysis is a critical tool for managing the long-term financial health of a dock. This analysis takes into account not only the initial construction costs but also the anticipated expenses associated with routine maintenance, repairs, and potential upgrades over the dock’s lifespan. By forecasting these costs, project managers can allocate appropriate budgets and plan for future expenditures—ensuring that the dock remains operational without unexpected financial strain.
Sustainable practices and materials: Integrating sustainable practices and selecting eco-friendly materials contribute to both cost savings and environmental stewardship over the dock’s life cycle. Sustainable maintenance strategies might include the use of recycled materials, energy-efficient lighting, and corrosion inhibitors that have a lower environmental impact.
View the complete article here.
What’s the difference between fixed and floating docks?
Fixed docks are anchored to the seabed and stay in place, while floating docks rise and fall with the tides.
Why is pile driving important in dock construction?
Pile driving provides a stable foundation that transfers the dock’s loads into the ground, ensuring structural integrity.