Pile Driving Basics, Common Problems, and Solutions
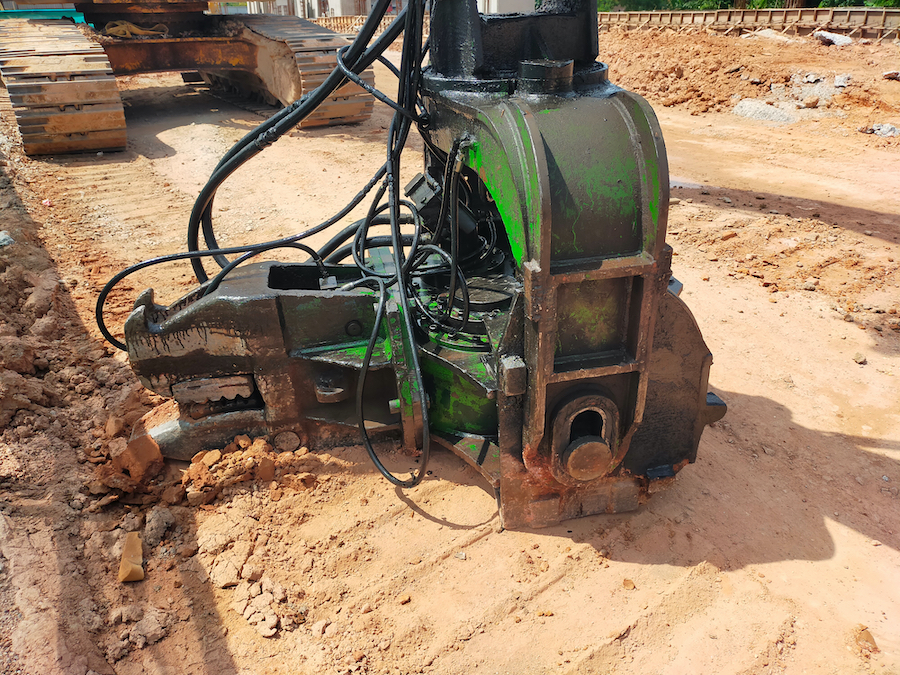
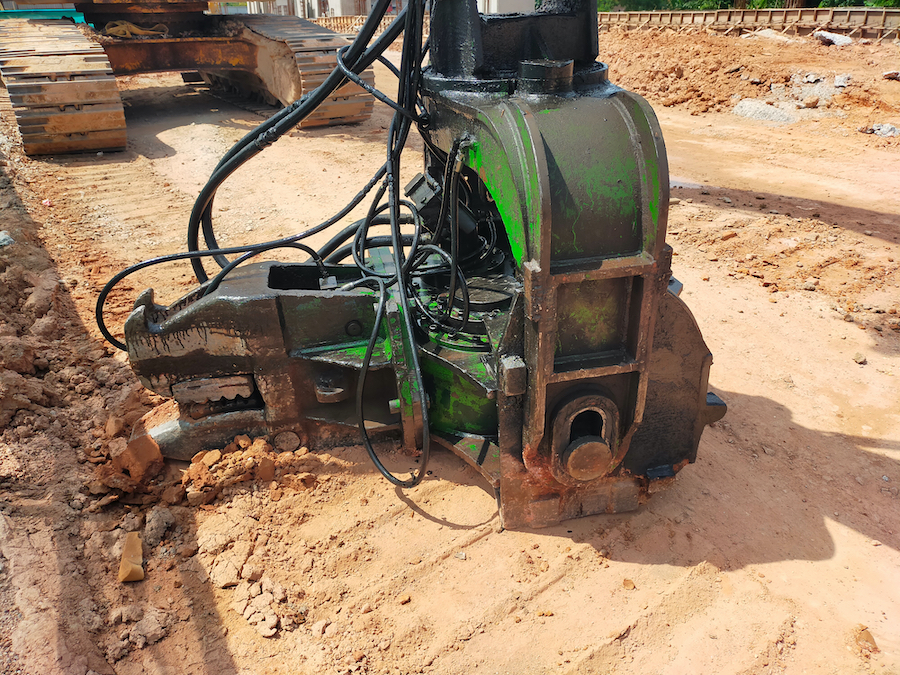
View the complete article here.
Pile driving is a critical part of the construction process. Vertical columns made of various materials (wood, concrete, steel, or a combination) are driven into un-excavated soil. The piles are a type of deep foundation used to hold up large structures – often bridges. In this article we discuss pile driving basics, the common problems encountered, and potential solutions.
Early Pile Driving
Early pile driving was done by hand. The energy required to drive a pile was created by the weight of the ram falling through the gravity field. In the twentieth century, greater driving force was achieved by using air- or steam-powered machines to accelerate the ram’s downward action. Many of today’s pile driving hammers are powered by diesel or hydraulic systems.
Piling Use
Softer soils are best for using piling. Most of the load capacity is generated from skin friction. To support heavy loads, they are grouped under footings.

Anatomy of a Pile Driver
At a high level, a pile driving system has four main parts: lead, hammer cushion, helmet, and pile cushion. Each part has a role in transferring energy to the pile which in turn impacts hammer performance. Read more at our glossary.
Lead
The pile driver lead is a supporting framework that guides the pile and hammer. They are categorized by how they attach to the pile driver – hanging, fixed, or swinging. Leads keep the piling and hammer aligned.
Hammer Cushion
A hammer cushion, typically made of man-made materials, is placed between the striker plate and helmet.
Helmet
The helmet is a temporary steel cap placed on top of the pile used to, as much as possible, protect the head during driving.
Pile Cushion
A pile cushion is typically made of wood. It is placed between the helmet and the pile.
Types of Pile Drivers
There are several types of pile drivers, including:
Vibratory Hammer
Vibratory hammers cut soil rather than drive piles using a spinning technique and counter-weight system. They are powered by hydraulic motors. A crane or excavator lifts the hammer. Hydraulic clamps attach it to the pile. They drive piles faster and their operation is (comparatively) quieter.
Diesel Impact Hammer
This drop hammer uses a two-stroke diesel engine. The ram is raised then released and allowed to free-fall. When it hits the pile, the energy drives it back up. It will keep going until it runs out of fuel or is manually stopped.
Double Acting Air/Steam Hammer
These hammers increase the blow rate with a shorter stroke. Active pressure accelerates the ram during the down stroke. This type of hammer greatly increased the speed with which piles could be driven.
Hydraulic Impact Hammer
A hydraulic hammer incorporates the use of an external energy source to lift the hammer to the top of its stroke. For the single acting hydraulic hammer, the free-falling piston develops the actual energy induced into the pile–much the same power stroke as a drop hammer or a single acting air/steam hammer.
Pile Foundation Design
The design of a pile foundation is highly dependent on the soil the piles are driven into. Other factors include the material of the piles, the expected load, and the level of use anticipated.
Keep in mind that driving the piles alters how the soil around it will behave. As well, soil – particularly in a large area – can vary greatly. Determining the right design is difficult. The planning process must include extensive and careful soil testing. Testing and evaluation should continue during construction.
Pile Driving Problems and Solutions
The challenging aspect of dealing with soil presents a variety of problems that can be anticipated. The project’s risk mitigation plan can consider likely issues to be encountered. Solutions can be included in contingency planning – avoiding cost overruns.
Drive Pile Blow Count Issues
Blow counts are calculated in advance. If the blow count is different in the field, there’s likely a problem. Here are common issues and solutions related to blow count:
Increased Blows Needed to Drive Pile
The number of blows needed to drive the pile to the required depth is calculated in advance. It is based on the soil and the driving system. If it is taking a lot more blows to drive the pile than planned, there is an issue with the soil and / or the driving system.
First ensure that the driving system is matched to the pile type. (Something that should be done before the work is started.) If they are matched, make sure the driving system operation conforms to the equipment manufacturer’s guidelines. Driving system problems can be related to low hammer efficiency or cushion that is too soft. The soil could have greater strength, higher damping ration, or larger soil quakes than initial testing anticipated.
Abrupt Change in Bearing Piles Blow Count
When the blow count for a group of pilings changes abruptly – or decreases – use borings to check soil conditions. If there is no indication of a weathered profile above the bedrock, the pile toe is probably damaged. Inspect the inside of the pile for damage to the pile toe. If you are not able to do an internal inspection you will need to evaluate the problem using dynamic measurements. Or, you may have to extract the pile.
Slightly Lower Blow Count
There are two key reasons for a lower-than-anticipated blow count. Lower soil resistance or better hammer performance. You will need to do restrike testing in the case of lower soil resistance. This requires establishing the setup factor and driving to a lower capacity. Evaluate hammer performance and make adjustments, if needed.
Significantly Lower Blow Count
Where the blow count is much lower than anticipated, review the soil borings. If there is no indication of soft layers, the pile may be damaged below the grade. You should also evaluate tensile stresses along the pile and compressive stresses at the toe. Other causes may be a spliced pile, an obstruction, or the toe contact is uneven. Check for toe damage.
Piles Are Driving Deeper Than Estimated
Piles driving into the soil much deeper than original estimates may be due to lower soil resistance than anticipated. Or increased driving system performance. A restrike test is needed to determine changes in the soil strength. A structural engineer will determine if changes in the driving system or pile depth are required.
Shifting Piles
Unanticipated movement of piles is another indication of a problem that needs to be resolved before work continues.
Lateral Movement in Previous Driven Piles
If previously installed piles move laterally when new piles are driven, soil displacement is the likely culprit. However, the failure of soil in an adjacent slope could be the cause. Solutions include changing the sequence in which the piles are driven or redriving the installed piles. You can also reduce ground movement by predrilling the pile locations.
Piles Outside of Alignment Tolerance
Pile design takes into account a certain amount of alignment tolerance. It is based, in part, on the type of material the pile is made of. If piles move beyond this tolerance it likely is related to hammer-pile alignment control issues or soil conditions. There are several methods for adjusting hammer-pile alignment control. For example, you can use a template or pile gate. Using a pile gate guides the pile into the leader. There may also be an obstruction near the surface. Removing the obstruction will shift the soil and may reveal other soil issues beneath. An engineer will need to evaluate the soil and determine next steps.
Pile Obstructions
The solution to handling pile obstructions varies based on the depth of the obstruction. The obstruction may reveal contaminated soil.
Shallow Pile Obstructions
If you encounter shallow obstructions within three feet of working grade, you can likely just remove it without significant impact to the surrounding soil.
Deep Pile Obstructions
Excavations are often not a viable solution where the obstructions are located beyond three feet or below the water table. In this situation, pre-drilling of pile locations can be employed. Deep pile obstructions may require an engineer to provide a remedial design. Deep obstructions can reduce calculated bearing capacity. In this case, additional piles may be needed.
Concrete Piles
Concrete piles are subject to various kinds of cracking. The direction, location, and severity of the cracks provide clues to the cause. Common problems with concrete piles and solutions include:
Partial Cracks – Easy Pile Driving
Where easy pile driving causes partial horizontal cracks in a concrete pile, check the hammer-pile alignment. Another possible cause is a combined tension and bending that is too high.
Complete Horizontal Cracks – Easy Pile Driving
Where easy pile driving causes complete horizontal cracks in a concrete pile, calculated tension stresses may be off. If the tension stresses are too high, add cushioning or reduce the length of the hammer stroke. If too low, it may be related to poor hammer performance.
Complete Horizontal Cracks in Hard Driving
Complete horizontal cracks during hard driving require you to calculate tension stresses along the length of the pile. If they are high, you may need a heavier ram. If too low, quakes are likely higher than expected.
Using fiber optic sensors for pile monitoring allow you to measure stresses along the entire length of the pile during driving. This provides greater accuracy as compared to standard monitoring. Note that cracks discovered early may be repaired with epoxy. Otherwise, they may end up in the pile heap.
Spalling Near the Pile Head
When there is spalling (chipping or crumbling) near the pile head, you will need to determine pile head stress for the blow count observed as compared to allowable stresses. One cause for damage near the head of a concrete pile is insufficient pile cushioning. Adding pile cushioning is the solution to high stress. However, if your calculations indicate low stress, there are several potential causes. These include hammer performance and alignment issues, as well as poor pile quality.
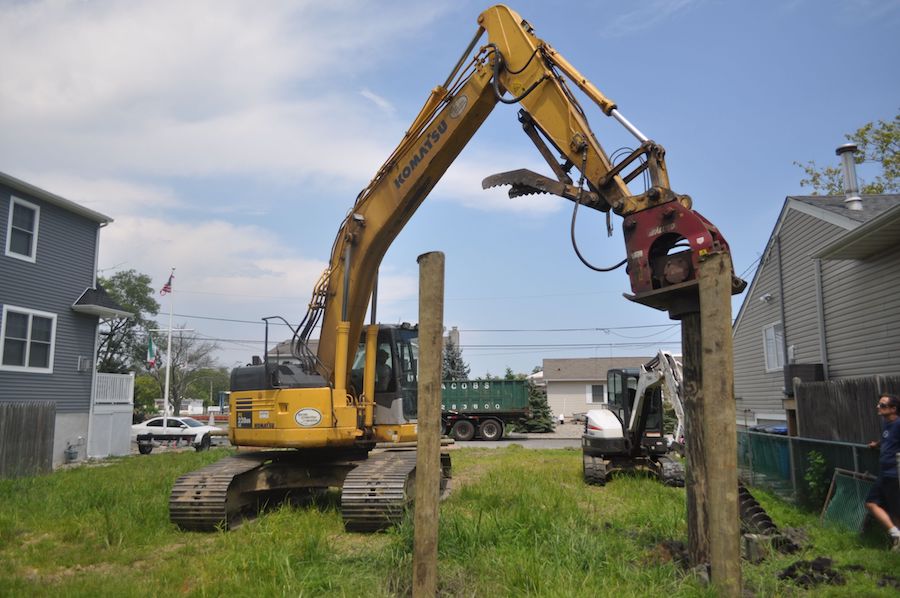
Steel and Timber Piles
There are several things that can cause a steel pile head to deform or the head of a timber pile to split or splinter. These include:
- Incorrect helmet size or shape
- Insufficient steel strength
- Uneven pile head
- Improper banding
You can use a metal point or boot to protect the timber pile. Use them with banding near the top of the pile to prevent splitting.
If you are still having an issue, calculate the stress on the pile head. Reduce the hammer stroke for low blow counts; increase for high blow counts. However, you may need to choose a different hammer – even a different pile type.
Hammer Issues
Sometimes the pile driving hammer is the cause of problems. One example is a when the field stroke of a diesel hammer is less than 90% of the calculated stroke. In this case, ram friction may be the cause. If the observed blow count is less than calculated, soil resistance is likely lower than originally estimated. If they are similar, use lower combustion pressure to align the hammer stroke.
Wave Analysis Data Issues
When using a wave analysis software program to predict pile behavior, you may run into data issues. If the specific hammer you are using is not listed when you are entering wave analysis data, use a hammer of the same type. It should have a similar energy rating and ram weight. You will need to modify its data to fit the application. In some cases, there is no hammer that matches the driving stress and resistance limits. It may be that the calculated stresses and blow counts are too high. One option is to increase material strength – or make design changes. Perform restrike or static load testing to confirm capacity.
Conclusion
Pile driving sounds simple – hammer columns into the ground. But it is a complex process that requires extensive testing and accurate calculation. Selecting the right pile material and equipment for the soil and load capacity depends upon it. There are several problems that can arise in the field. Preparation and contingency planning are the key to keeping a pile driving project on track and on budget.
View the complete article here.
What is pile cushion?
A pile cushion is typically made of wood. It is placed between the helmet and the pile.
What is a Vibratory Hammer?
Vibratory hammers cut soil rather than drive piles using a spinning technique and counter-weight system. They are powered by hydraulic motors. A crane or excavator lifts the hammer. Hydraulic clamps attach it to the pile. They drive piles faster and their operation is (comparatively) quieter.