Overcoming Common Challenges in Foundation Drilling Applications
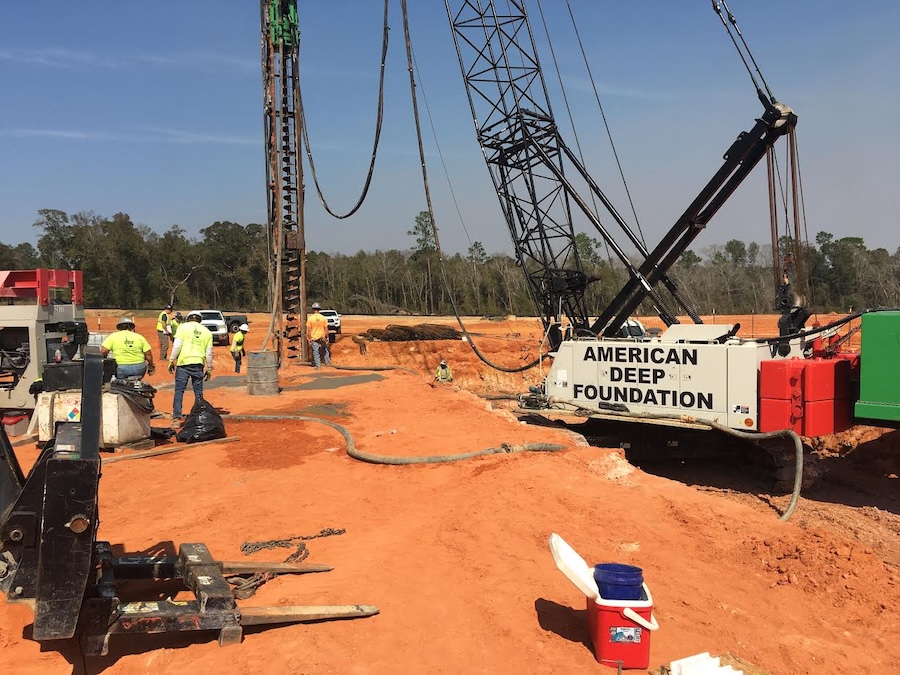
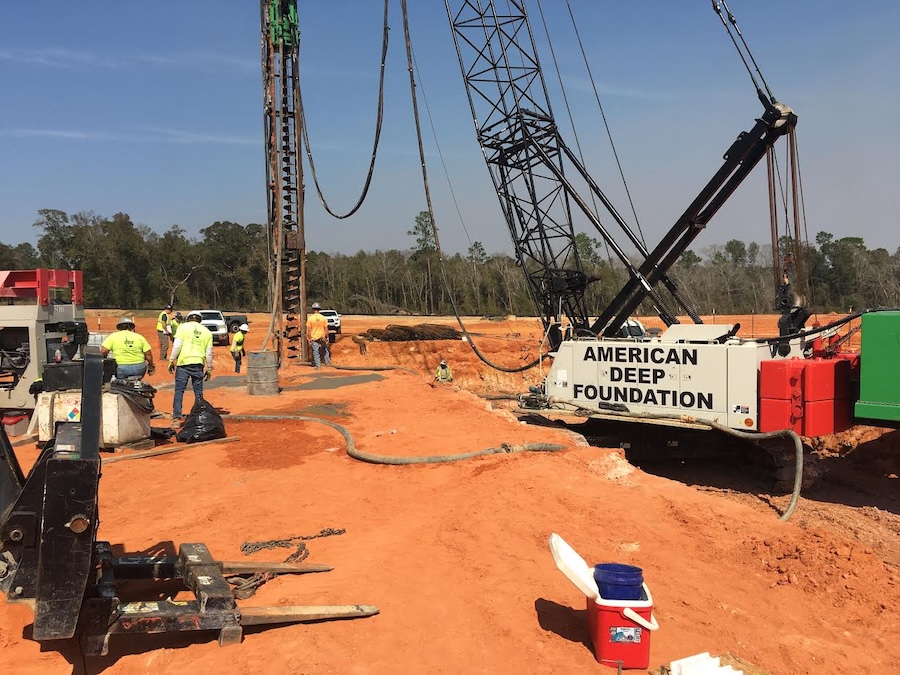
View the complete article here.
Foundation drilling sometimes comes with a unique set of challenges that can disrupt timelines, inflate budgets, and compromise safety. From difficult ground conditions to equipment failures and environmental concerns—successful execution requires preparation, the right tools, and a skilled team. This guide highlights the most common challenges in foundation drilling and pairs them with effective solutions and expert tips to help contractors navigate their next project.
Challenge 1: Difficult Soil and Rock Conditions
Foundation drilling often involves varied and unpredictable ground conditions, including:
- Hard rock: Drilling through granite, basalt, or other hard materials can quickly wear down tools, reduce efficiency, and risk overheating equipment.
- Soft clay: Clay can clog machinery and tools, slowing down operations.
- Sandy soils: Loose, shifting sands can cause borehole instability and collapse.
Solutions
- Specialized drill bits and tools: Use rock augers or core barrels for hard rock and anti-clogging clay tools for soft soils. In sandy conditions, stabilize the borehole using casing or drilling fluids like bentonite or polymers.
- Advanced rig technology: Equip rigs with high-torque hydraulic systems and real-time monitoring sensors to adapt to changing ground conditions efficiently.
Challenge 2: Water Table Interference
High water tables or groundwater ingress can destabilize borehole walls and disrupt operations, especially in coastal or flood-prone areas.
Solutions
- Dewatering systems: Install pumps to lower the water table around the drilling site, ensuring a stable and dry environment.
- Drilling fluids: Use bentonite or polymer-based fluids to create a barrier that prevents borehole collapse and improves drilling stability.
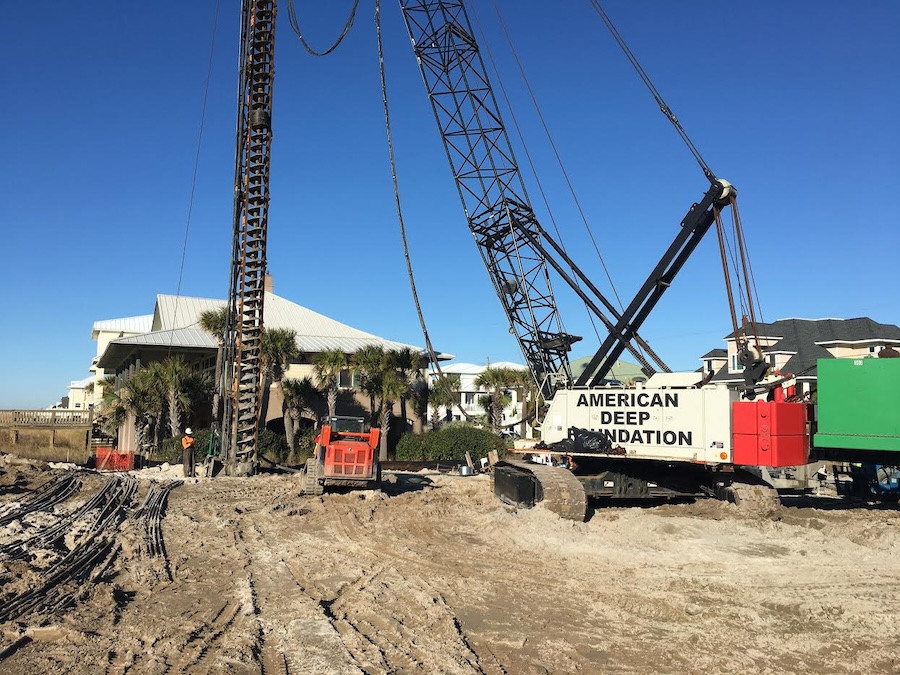
Challenge 3: Obstructions
Subsurface obstructions—such as buried debris, boulders, or utility lines—can halt progress unexpectedly and damage equipment.
Solutions
- Site surveys and scanning: Conduct thorough geotechnical surveys and use ground-penetrating radar (GPR) to identify potential obstacles before drilling begins.
- Specialized tools: Use rock breakers or excavation equipment to remove obstructions efficiently. In the case of utilities, plan alternative routes and coordinate with relevant authorities.
Challenge 4: Equipment Breakdowns
Drilling rigs and tools are subject to intense stress, making them prone to wear-and-tear. Hydraulic failures, dull bits, and electrical malfunctions can lead to costly downtime.
Solutions
- Preventive maintenance: Establish a routine maintenance schedule to inspect hydraulic systems, drill bits, and electrical components.
- Real-time diagnostics: Use monitoring systems to detect potential failures early, allowing for timely repairs or replacements.
- Operator training: Ensure operators are skilled in identifying and addressing minor issues before they escalate.
Challenge 5: Environmental Concerns
Foundation drilling can impact the surrounding environment—potentially leading to noise pollution, vibrations, and potential contamination of soil or water.
Solutions
- Noise and vibration control: Install temporary soundproof barriers and vibration dampeners to minimize disruption to nearby structures and communities.
- Waste management: Properly handle and dispose of drilling fluids and cuttings to avoid contamination. Use biodegradable or eco-friendly fluids where possible.
- Compliance: Adhere to local regulations and environmental guidelines to avoid fines and maintain project integrity.
Tips for Success in Foundation Drilling Applications
Consider these tips to streamline your foundation drilling projects, overcome common challenges, and achieve optimal results efficiently and safely…
1. Plan Ahead: Conduct Comprehensive Site Surveys
Comprehensive site surveys are critical to understanding the subsurface conditions and potential challenges. Soil testing, groundwater analysis, and the use of tools like ground-penetrating radar can uncover issues before they become problems. Early planning minimizes delays, prevents costly surprises, and ensures the drilling strategy aligns with project requirements.
2. Invest in Advanced Technology
Modern rigs and tools offer features like GPS, automated controls, and hydraulic systems that improve precision and efficiency. These technologies adapt to varying soil conditions, reduce operator fatigue, and enhance safety. Investing in advanced equipment ensures projects stay on schedule and within budget, even in challenging environments.
3. Partner with Specialists
For complex projects, collaborating with experienced drilling contractors or service providers can make a significant difference. Specialists bring expertise in handling unique challenges and often have access to specialized equipment. This collaboration allows you to leverage their knowledge while focusing on other critical aspects of the project.
4. Emphasize Safety
Safety is paramount in foundation drilling, where risks include equipment failures and environmental hazards. Regular training for operators, daily safety checks, and adherence to regulatory guidelines are essential. By prioritizing safety—you protect your team, reduce liability risks, and maintain project timelines.
5. Prioritize Environmental Compliance
Drilling operations can have environmental impacts, such as noise pollution or soil contamination. Implement mitigation strategies, including noise barriers, vibration dampeners, and proper disposal of drilling fluids. Ensuring compliance with environmental regulations avoids fines and enhances your company’s reputation.
6. Focus on Communication and Coordination
Clear communication between stakeholders ensures smoother project execution. Regular updates, progress meetings, and effective use of project management tools help address challenges proactively. Good coordination minimizes missteps, especially in projects involving multiple contractors or regulatory bodies.
7. Optimize Equipment Utilization
Using the right equipment for each specific task ensures efficiency and reduces wear-and-tear. Monitor equipment usage closely and maintain backup machinery to avoid delays due to unexpected failures. Proper utilization maximizes productivity and extends the lifespan of your rigs and tools.
8. Build a Contingency Plan
Unexpected challenges are inevitable, so a well-thought-out contingency plan is crucial. Allocate additional time and budget for unforeseen issues and ensure backup suppliers or equipment are readily available. This preparedness allows you to address problems quickly without derailing the entire project.
9. Track and Analyze Performance
Monitoring key performance metrics, such as drilling speed and equipment wear, helps identify inefficiencies. Post-project reviews provide insights into what worked and what didn’t, enabling continuous improvement. Regular analysis ensures that future projects benefit from past experiences and lessons learned.
View the complete article here.
What are common challenges in foundation drilling?
Common challenges include difficult soil and rock conditions, water table interference, obstructions, equipment breakdowns, and environmental concerns.
How can foundation drilling projects be made more efficient?
Efficiency can be improved through comprehensive site surveys, advanced technology, skilled operators, and clear communication among stakeholders.