Overcoming Brownfield Challenges with Ductile Iron Piles
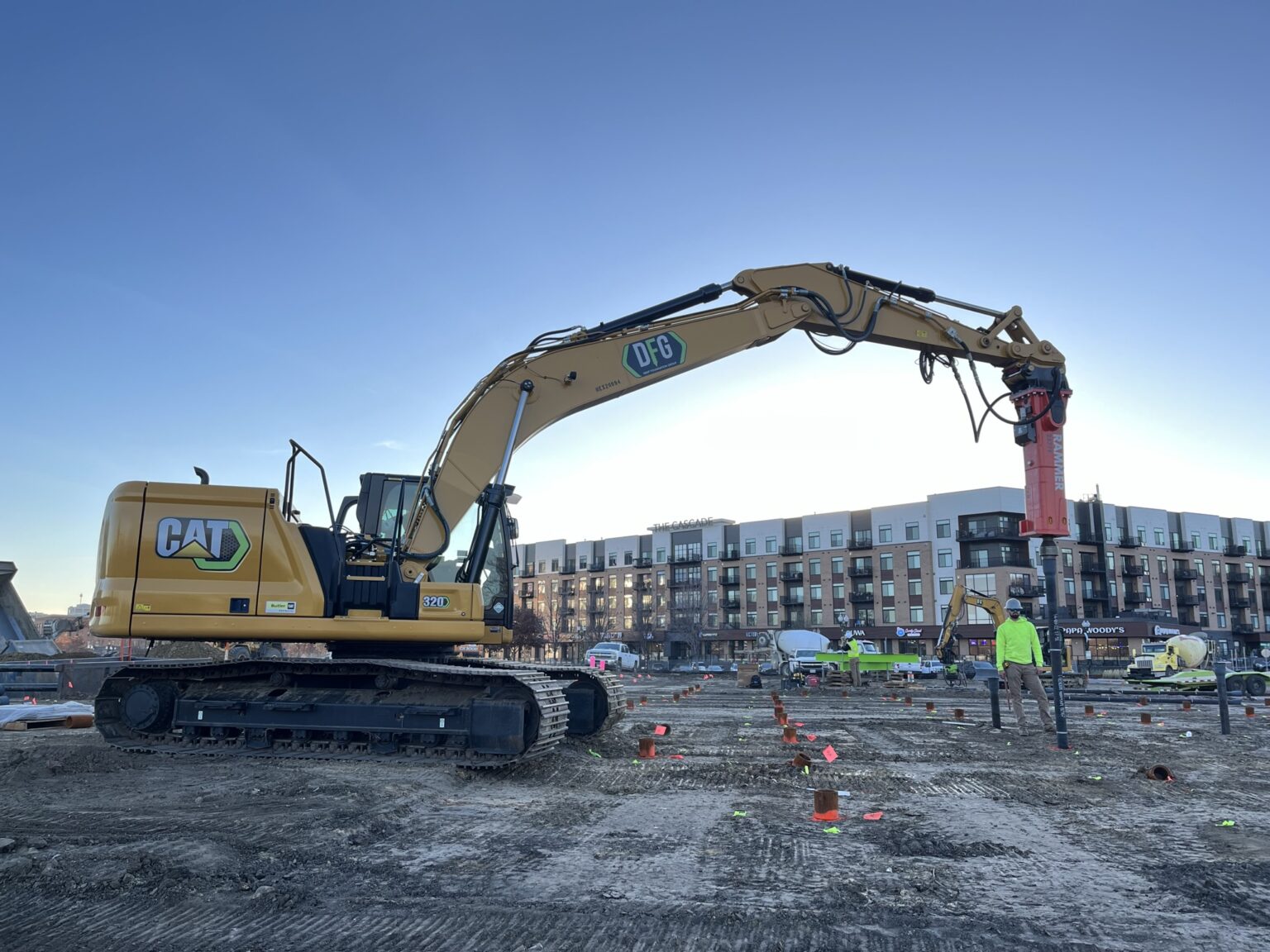
Ductile Iron Piles by DuroTerra™ provided an economical deep foundation solution to transfer loads through the debris fill without generating spoils.
Project Description
Construction of the new $18.5 million year-round recreation facility included a 14,000 square foot outdoor ice skating ribbon, a warming house, splash pad, dog park and inclusive playground. Foundations for the single-story, warming house consisted of a series of grade beams supporting a structural slab. Pile loads ranged from 5 to 45 kips.
Geotechnical Conditions
The site previously operated as railyard maintenance facility and then a scrap metal salvage yard. A major Brownfield remediation project was completed at the site by 2004 to remove soil contamination. Currently, the ground conditions consist of highly-variable, debris fill extending between 7 and 14 feet below ground surface. The fill was predominantly clay with construction debris. In some locations, a topsoil layer was encountered below the fill. Sioux Quartzite bedrock was encountered below the fill and topsoil.
Project Challenges
- Provide an economical deep foundation solution to transfer loads through the debris fill without generating spoils.
- Achieve pile capacities while limiting installation risk.
Advantages
- Rapid installation with mobile equipment
- Adaptable to variable bedrock elevations
- Simple, low-vibration installation
- Driven system reduces risk compared with helical piles spin-out
Design and Construction Solution
As a former Brownfield site with uncontrolled and contaminated debris fill, the single-story warming hut required foundation support to reduce the potential for settlement. Ground improvement using aggregate piers was considered for the project but ruled out due to the contamination concerns and potential for water migration into contaminated soils. Helical piles would also present challenges with penetrating the debris fill and likely spinning-out when transitioning between the variable fill and hard rock. Driven Ductile Iron Piles were ultimately specified to address these issues.
Ductile Iron Piles were designed to provide compression capacities up to 45 kips by penetrating the fill and topsoil and achieving set on the underlying bedrock. A total of 114 piles were specified for support of the series of grade beams supporting a structural slab. Series 118/9.0 Ductile Iron Piles consisting of a 118 mm (4.65 in) OD with a 9 mm (0.35 in) wall thickness were selected. This material size provided more than enough capacity even after considering possible corrosion rates from the contaminated fill.
Deep Foundation Group (DFG) was the specialty foundation contractor selected to perform the work. With winter weather closing in, speed of installation was critical for the project. DFG mobilized to the site in mid-November. On the first day, a test pile was installed to terminate on rock at 13 feet. Since the pile size has more than sufficient structural capacity without interior grout, the load test was immediately set-up and performed. Results of the test confirmed the design capacity with deflections of only 0.12 inches and 0.20 inches at the 100% and 200% design loads, respectively.
Once the load test showed acceptable results, DFG proceeded to install production piles. A total of 114 production piles were installed in only 1.5 days. With lengths ranging from about 10 ft to more than 25 ft, the crew averaged over 1,000 LF/day. The piles were then grouted on the interior and a bearing plate attached to the top. Total installation time including full-scale load testing was only 3 days for the system.
Project Team Members
DIP Design/Build Partner: Deep Foundation Group
Geotechnical Engineer: Geotek Engineering & Testing Services, Inc.
General Contractor: Lloyd Companies
Structural Engineer: RISE Structural Associates Inc.