A Novel Solution for Restoration of Deteriorated Piles
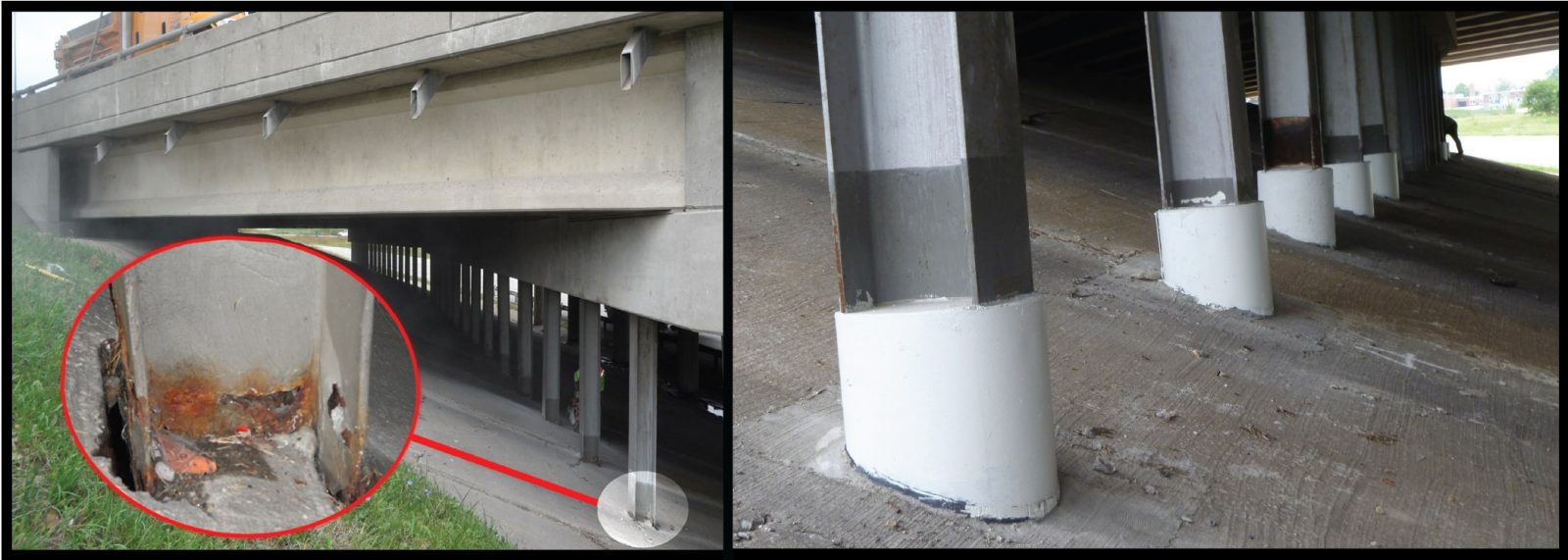
Many bridges constructed in Missouri over the last 70 years utilize exposed steel H piles as part of their substructure. From time to time these exposed pilings corrode for various reasons, such as a shift in a stream channel that allows water flow directly around the piling, repetitive cycles of condensation at a connection to concrete, or in the case of four bridges recently repaired with fiber reinforced polymer (FRP), drainage from the deck onto concrete slope protection allowing anti-icing chlorides around some of the piling. The damage is typically concentrated at the base of the pile above and below the soil. In the case of water crossings, corrosion is most severe at the splash zone, which extends a few feet above and below water level.
A total of 49 piles near the edges of four bridges in St. Louis at the I-70 and I-270 interchange were severely corroded, with the section loss of the piling to be repaired varying from 20 to 80 percent. The four structures are five span bridges that carry I-270 traffic and two of the intermediate bents are constructed of exposed H piling. The H piling bents allow for expansion between the cap and the deck while the other two intermediate bents on these bridges are constructed of concrete columns that are integral with the deck. The H piling bents had 26 to 32 10 x 42 steel piles that are located behind barrier wall on a 3:1 concrete slope with limited overhead space, so all work had to be performed by hand. The pile lengths in place varied between 30 and 46 ft. Damage, caused by polluted rain run-off, was concentrated over a one-ft high section at the base of the piles.
Missouri DOT (MoDOT) determined that it would be sufficient to repair a two-ft high length of the pile in the corroded area. A section of the concrete slab about 2.5 ft by 2.5 ft was cut and removed to expose the pile. The corroded area was cleaned by sandblasting. As added protection, a corrosion-inhibiting paint was used to coat the repair area of the steel pile.
PileMedic™ was selected for the repair. PileMedic (QuakeWrap, Inc., www.quakewrap.com) is a new form of FRP that for certain applications offers great advantages over the earlier generation wet layup system. PileMedic allows transfer of a great portion of the activity from the construction site to the manufacturing plant. This results in higher quality products that can be installed much faster in the field and with significantly less manpower. It also allows certain unique solutions that are impossible to implement with the wet layup system. PileMedic is manufactured by impregnating rolls of carbon or glass fabric with resin and pressing them together under heat and pressure to produce strong thin laminates. The laminates have tensile strength in excess of 150,000 psi and are produced in a continuous process in sheets up to five ft wide by 300 ft long. The large laminate sheets are coiled and packaged in a box for easy shipment; they can be cut to any width and length in the field with ordinary scissors. With a thickness below 0.025 in., the thin laminates are flexible enough to create a cylindrical shell as small as eight in. in diameter in the field. There is no upper limit for the diameter of the shell for such applications. By wrapping and epoxy bonding the laminate around itself, a multi-layer strong shell can be quickly created around the pile that can be filled with grout or resin. The product is compatible for repair or strengthening of structural elements made with wood, concrete, and steel.
A piece of the product two ft wide by nine ft long was used for each pile. A special two-component epoxy was mixed in the field and applied to about a two-ft by five-ft ft section of the laminate. The mixed epoxy has a paste-like consistency and is applied with a trowel to a thickness of 30 to 40 mil. The laminate is then wrapped loosely around the pile to create a two-ply shell. The nine-ft length of the laminate allows creation of a two-ply 16-in. diameter shell with eight in. of overlap beyond the starting point.
At this stage, before the epoxy cures, ratchet straps must be used to hold the shell in a cylindrical shape and to maintain the diameter of the shell. The shell can be moved up or down to be centered about the damaged portion of the pile. In this project the soil below the slab formed the seal at the bottom of the shell.
The annular space between the shell and the pile was filled with a high-strength non-shrink cementitious grout. The grout was mixed in a five-gal pail with a hand-held jiffy mixer and required no special heavy equipment. Consolidation of the grout was completed with a small vibrator and the top of the grout was finished with a trowel. Before the grout sets, the hydrostatic pressure from the grout pushes the inner layer of the shell outward against the outer layer and forces the two plies of the laminate to be tightly pressed against each other. After several hours, the ratchet straps are removed and if desired the exterior of the shell can be painted. The entire repair operation excluding the painting was completed in about two hours.
If desired, steel reinforcing bars can be also positioned in the annular space before the placement of grout. This will provide significant flexural capacity to the column. In those cases, a taller jacket may be required to ensure that there is sufficient development length for the steel to develop its full capacity.
The laminates described offer several advantages over conventional methods and materials used for repair of piles. From a structural behavior point of view, the combination of high tensile strength of the laminates and the creation of a seamless shell results in a tube that offers very high confining pressure for the grout and the pile. From a construction point of view, the laminates can be made into an ellipse or a cylinder of any diameter in the field; this eliminates time and expense of ordering customized jackets in advance, reduces the amount of excavation required, and speeds up the repair process. Similarly shipping and storage costs are reduced. The laminates also serve as a moisture barrier and protect the grout and steel column from future deterioration. Even in cases where reinforcing steel is placed within the annular space, there is no need to provide substantial concrete cover for the reinforcing bars. This, combined with the fact that the jackets are not supplied in pre-made sizes, allows construction of snug-fitting jackets in the field that minimize the volume of grout needed for repair.
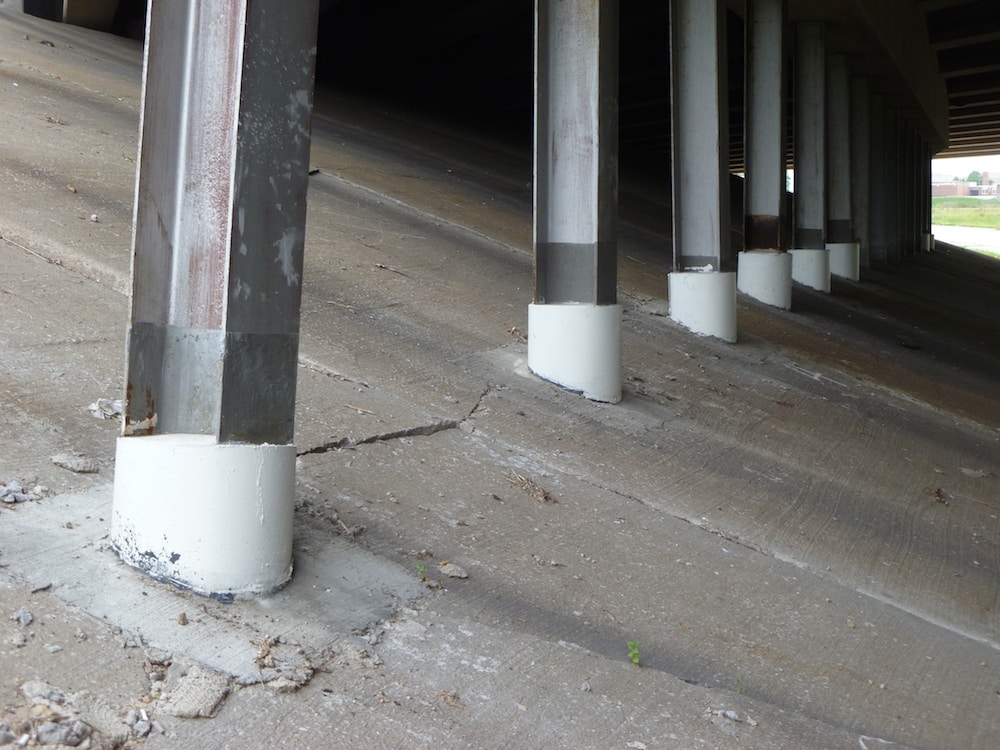
FRP laminates are non-metallic and will not corrode. They offer a long service life with little maintenance. With a special epoxy that cures under water, PileMedic can be used to repair piles in water. Likewise, the laminates are ideal for repair of deteriorated concrete or wooden piles and utility poles. In such applications, it is best to inject a low viscosity resin in the annular space. Such resins can be pressurized to penetrate into the voids and crevices of the concrete or wood for enhanced structural performance and elimination of decay from the environment and insects.
In the project described above, 2 months prior to the PileMedic™ repairs, routine inspections had lowered the substructure Condition Rating to poor (NBI rating of 4 on a 9 point scale). This meant these bridges were considered Structurally Deficient due to the number of piling with significant section loss. The FRP repairs were completed in just two weeks, improving all 4 bridges to a Satisfactory Condition Rating (NBI rating of 6). All of this was affordable enough to be funded with the region’s operations budget and happened on one of the busiest highways in Missouri without causing any delays or distractions to the traveling public.
Dr. Ehsani, PE, SE is Professor Emeritus of Civil Engineering at the University of Arizona and President of QuakeWrap, Inc. Mr. Croarkin, PE, is St. Louis District Bridge Engineer, MoDOT.