The New BAUER eBG 33 – The Drilling Rig for An Electrical Future
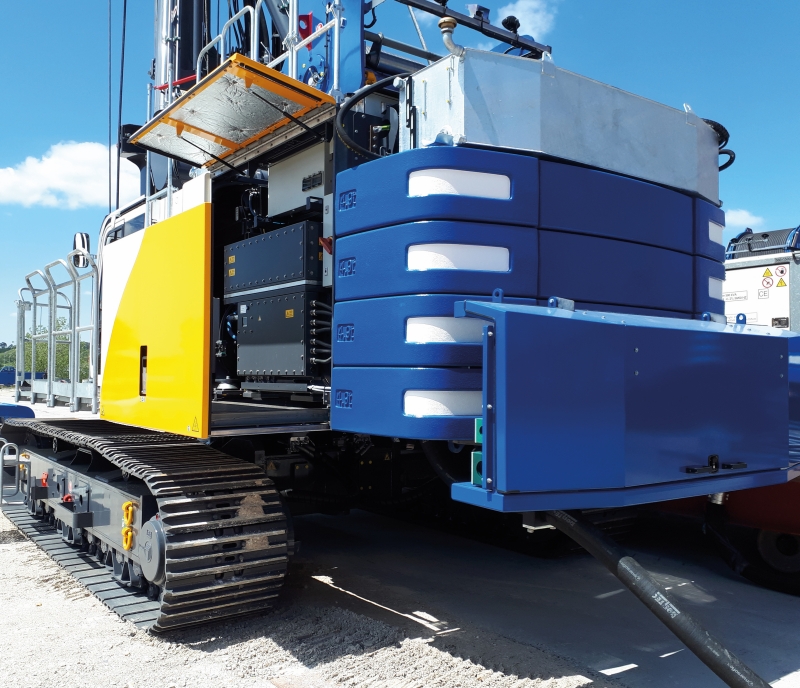
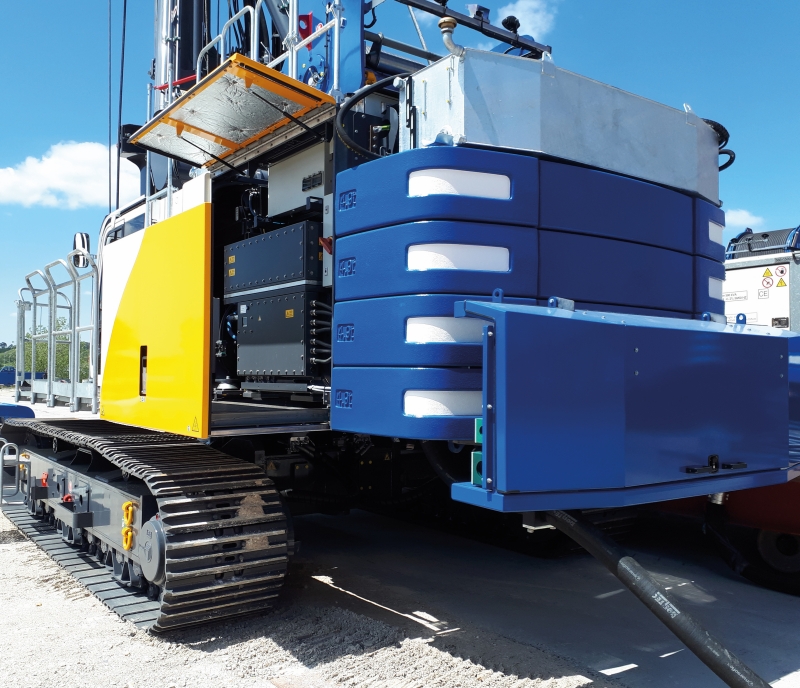
Schrobenhausen, Germany – What started as an idea is now reality: At this year’s in- house exhibition with the slogan “BAU ERLEBEN,” BAUER Maschinen GmbH is presenting the new eBG – the first electric drilling rig manufactured by Bauer. The equipment relies on electrical power instead of a diesel engine, so it does not require any fossil fuels, and operates extremely quietly, making it perfect for use in cities. “We have been working with electrification for some time now,” explains Christian Heinecker, Head of the Drilling Equipment division at BAUER Maschinen GmbH. “In the past, however, this was tailored to specific customer requests or projects.”
At its heart, development of the new eBG is a component of “Zero Emission”. This encompasses various spheres of activity such as sustainability, recycling, energy, CO2 footprint and noise emissions. The electrical operation of drilling rigs is therefore simply the logical next step towards climate neutrality.
Previously, electrification of Bauer equipment has only been applied in specific cases such as the Dive Drill, a drilling rig operated from ships for underwater drilling in which electrically driven hydraulic power packs were installed, or in the area of deep drilling technology with the electrically driven Top Drive. “Electrification has entered our standard portfolio in the form of individual products as well as deep drilling technology,” says Christian Heinecker. The first duty-cycle crane with an electric motor was presented at Bauma 2019 in Munich: the BAUER MC 96, with a trench cutter that is suitable for urban construction as well as for the construction of subway shafts.
The new eBG 33 falls in the mid-range segment of the drilling rig series with a drive power of more than 400 kW, which puts it on the same scale as a BG 28 to BG 36 and thus within the range of 280 to 390 kNm torque. As a result, it covers a very wide range of applications on site. Apart from classical Kelly drilling, the eBG 33 can be used for high-performance methods, for example soil mixing techniques such as cutter soil mixing (CSM) or double-head system drilling. It is even possible to attach a Bauer trench cutter.
In preparation for development of the electric drilling rig, analysis has revealed that the average diesel consumption is significantly higher for the BG 28 and larger equipment when compared to smaller equipment types. This is because this type of drilling rig is also used for high-performance methods roughly a third of the time, in addition to frequent Kelly drilling. “And this is exactly where we focused,” says Christian Heinecker. “In fact, our analysis also demonstrated that specifically in this range, the operating costs could be enormously reduced for the long-term operation of an eBG compared to a diesel-operated drilling rig.”
To deliver the same capacity as a conventional Bauer BG with a diesel engine, the eBG 33 was developed using a direct power supply solution. The reason: The currently available battery systems would not be able to manage the capacity in this size class. Accordingly, the preparatory work on site must be planned over a number of months to ensure that the power supply is also provided. Using the eBG is thus primarily advantageous on large-scale and long running construction sites, since the overall benefits, such as significantly reduced operating costs, can be fully exploited over the longer period of time.
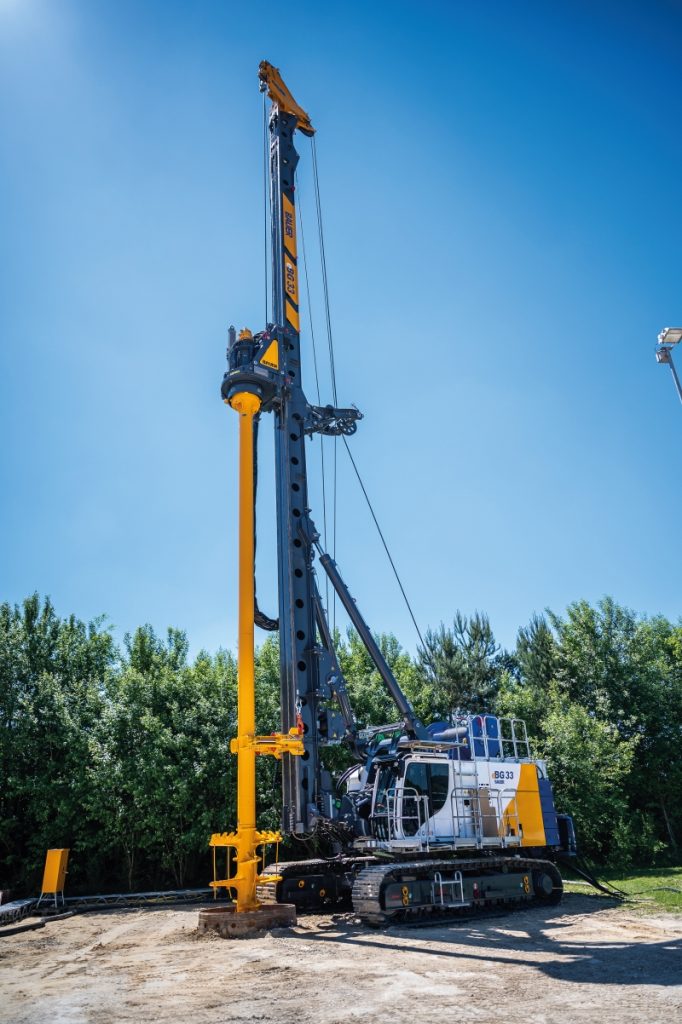
From the outside, the eBG does not look any different from its “relatives” except for the color. It’s a different story on the inside: An electric engine was installed instead of the diesel engine and the power distribution is located where the tank would be. A transformer supplies various voltages for the electric control components. The engine requires a full 690 volts, while 400 volts are required for air conditioning and heating. In addition, a 230 V socket provides the option of plugging in additional attachment parts on site, such as percussion tools. The on-board controls require 24 volts as usual.
Starting with the transfer case, the structure of the eBG remains the same. The hydraulic system, control elements and software design are implemented in the established, conventional manner. The operator does not need to adapt because operating the equipment is the same as for all other Bauer BGs. The advantages of Bauer’s award-winning Energy Efficient Power (EEP) system are also fully available for the electrified eBG. The EEP system has been setting new standards for years now, especially in terms of emissions and diesel consumption. This concept also includes demand-specific, dynamic control of cooler speed and diesel engine speed as well as outstanding hydraulic efficiency thanks to large-scale hydraulic components. Another highlight is the operating method of the main winch: The EEP winch concept makes it possible to recover energy during retraction into the bore hole.
Cable guidance for a secure power supply poses a particular challenge. Once again, the idea comes from deep drilling technology: The solution is a power loop, a thick hose with a firm protective sheath inside of which a total of seven cables are laid.
At BAU ERLEBEN, the first eBG with a trailing cable is being presented. In this configuration, the equipment is primarily suited for soil mixing techniques where it operates in the same location for a considerable period of time. A model for Kelly drilling will be presented from mid-August. This machine needs to be able to move and rotate for alternating drilling and emptying operations. For that reason, this electric BG model is equipped with a patented cable guidance arm on the machine. “All in all, cable guidance will continue to pose certain challenges because every project has different requirements, and the solutions will be as diverse as the projects themselves,” remarks Christian Heinecker.
The eBG 33 is a novelty on the market in this form and capacity. “Development was possible due to close collaboration with our customers and above all due to the enormous dedication of our project team – we cannot thank them enough,” emphasizes Christian Heinecker. The team at Bauer Maschinen is thrilled that, with the eBG, one of the main pieces of equipment for specialist foundation engineering can now be operated completely CO2-free on site. The eBG can execute various methods for the construction of excavation pit walls as well as drilling large-diameter foundation piles. Even the execution of cut-off bases is conceivable.
“During project preparation, the total initial expenditure is higher, but the customer can reduce overall operating costs thanks to the highly efficient electric drive system,” summarizes Christian Heinecker. In addition, the total carbon footprint of a project is improved thanks to the CO2-optimized electric drive system as well as the option of using CO2-optimized construction methods. The implementation of many environmental initiatives and new regulations is thereby supported sustainably and with a view to the future.