How to Minimize Downtime of Foundation Equipment
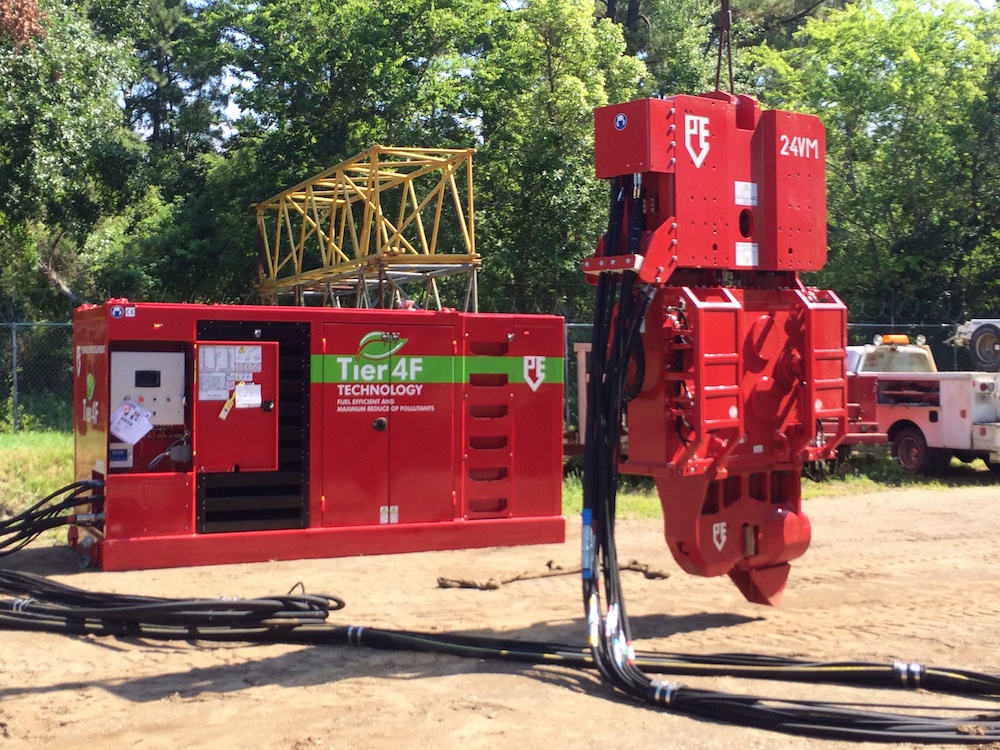
by Walter Haberl
It goes without saying that foundation equipment has a lot to endure. Outdoor job sites can include various challenges like difficult soil conditions. Even when working with a local repair company, regular service check ups or replacement of parts cannot always prevent a vibratory hammer or power pack to break down. This can bring a lot of disadvantages in time, money and energy.
Not only expensive repair costs can be expected, but also serious downtime. The piece of equipment cannot be replaced one by one in short time. On top of that, the downtime brings along a high risk of penalty fees. When the deadline of the project is not realized, an increasing amount of contractors receive a penalty for the extra project time they need. The price tag of this delay is significant. Furthermore, a lot of people work on the job site. Their wages need to be paid, too. Last but not least, extra equipment that is rented to complete the job, such as cranes, suffer from downtime as well.
Looking at the fact that the time between bidding and winning a construction project can be a matter of just a few weeks, downtime is something you want to avoid at all times. So especially when working in tough working conditions, the need of an excellent shape of the equipment is high.
Save time, money and a lot of energy in the long run
Experience taught us the life cycle of equipment can be extended significantly with a maintenance check up. Yes, a check up often means replacement of parts and other repair costs, but we’ve learned from customers who used our machines for years that it saves a lot of money in the long run. Thanks to the check up, equipment can be used for a longer period of time and customers experience a lot less downtime.
The check up can be organized in multiple ways
It can mean a service engineer of Dieseko Group travels to your job site, but we also make sure our dealers are trained to provide local service. Even companies with their own maintenance service can have training from service engineers of Dieseko Group how to use, check and repair the foundation equipment. After the training, they receive a certificate. When a new piece of equipment is bought, we can also put it into service at your job site.
The biggest difference with normal maintenance and repair is that these maintenance check ups are not based on individual incidents. Check up of the foundation equipment – even when the piece of equipment is working properly at that moment – can prevent downtime in the future. This way, we have saved our customers a lot of money, time and energy!
Dieseko Group and our local dealers are always open to enter a discussion on how the maintenance of foundation equipment at your job site(s) can be organized.
Construction company MJ Eriksson coped with expensive repairs and serious downtime in the past.
MJ Eriksson A/S, headquartered in Copenhagen (Denmark) realized they could save a lot of time, money and energy if they could find a way to organize this in a different way. But how? Read this in the new case study.