Mastering the Hard Rock: Effective Drilling Techniques and Technologies
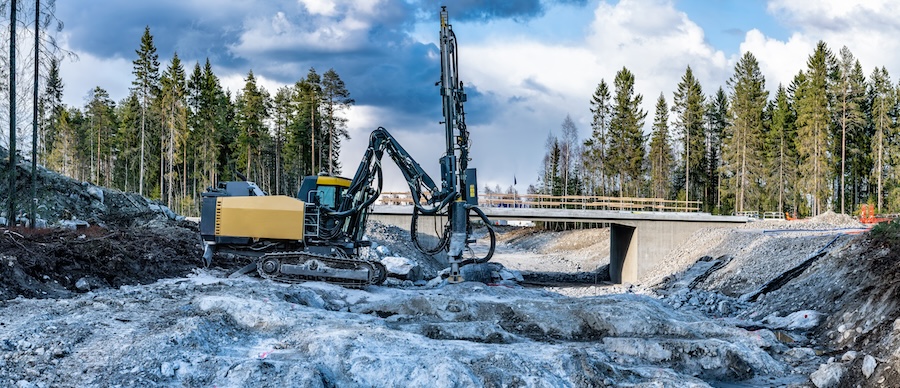
View the complete article here.
This guide is tailored for deep foundations contractors tasked with the demanding challenge of drilling in hard rock conditions. It discusses essential techniques and technologies required to navigate the complexities of various rock formations encountered in foundation work—such as granite, basalt, and limestone.
Understanding Hard Rock Conditions
When it comes to foundation drilling applications, encountering hard rock formations is not uncommon. These formations present unique challenges and necessitate specific strategies and tools for effective drilling.
Types of Rock Formations Commonly Encountered
Known for its hardness and density, granite is a common igneous rock encountered in foundation drilling. Its crystalline structure can significantly slow down drilling processes.
Another type of igneous rock, basalt is even harder than granite and is characterized by its fine-grained structure. It is commonly found in volcanic regions and poses a challenge due to its abrasive properties.
This sedimentary rock varies in hardness but can be particularly challenging when it is compact. Limestone may contain cavities or voids which can complicate drilling operations.
Typically softer than igneous rocks, sandstone is sedimentary and can range from soft to very hard. Its drillability largely depends on the cementing material and the size of the sand grains.
Metamorphic in origin, slate can be prone to cleavage and splitting—making it tricky to drill through without the right equipment.
Physical Properties Affecting Drilling Operations
The hardness of the rock determines the type of drill bits required. Harder rocks like granite and basalt may require diamond or carbide-tipped drill bits to efficiently penetrate the material.
Rocks with high fracture toughness are more resistant to cracking under stress, which can influence the choice of drilling technique and equipment.
The elastic properties of the rock affect how energy is absorbed during drilling, while brittleness indicates how easily the rock can fracture. Understanding these properties helps in selecting the appropriate drilling parameters to minimize equipment wear-and-tear.
Porosity and permeability influence how fluids used in drilling operations interact with the rock. Highly porous rocks can lead to higher fluid consumption, affecting the overall cost and efficiency of the drilling project.
Drilling Techniques for Hard Rock
Drilling through hard rock is a formidable challenge in foundation construction, demanding the use of specialized techniques and equipment to achieve effective results.
Traditional Rotary Drilling vs. Down-the-Hole (DTH) Hammer Drilling
Traditional rotary drilling involves a drill bit attached to a rotating drill pipe. As the bit rotates, it cuts through the rock, and the debris is typically removed by flushing water or air through the drill pipe. While effective in softer materials, traditional rotary drilling can be slow and less efficient in hard rock due to the high strength and abrasiveness of materials like granite or quartzite.
Down-the-hole (DTH) hammer drilling is particularly suited for hard rock and involves a hammer mechanism at the drill bit end which provides additional percussive force to break the rock, combined with the rotary action. This technique allows for rapid drilling in hard rock, with the hammer action effectively fracturing the rock into small chips—which are then evacuated by compressed air blown down the drill pipe. DTH drilling is more efficient than traditional rotary drilling in hard rock conditions due to its dual action of percussion and rotation.
Diamond Core Drilling and Its Effectiveness in Hard Rock
Diamond core drilling employs a drill bit embedded with industrial diamonds, which is one of the hardest materials available. Diamond core drilling is highly effective in hard rock, allowing for precise cuts and the extraction of a core sample. The hardness of the diamonds allows the bit to grind through tough rock, making it ideal for exploratory drilling where core samples are needed for geological analysis.
Diamond core drilling is highly regarded for its precision and ability to drill at great depths with minimal deviation. Its effectiveness in hard rock is unmatched by most other drilling methods, making it a preferred choice for mineral exploration and geotechnical investigations where accurate core samples are critical. However, it is generally more expensive than other methods due to the cost of diamond bits and the slower rate of penetration in extremely hard formations.
Equipment Adaptations
Drilling in hard rock conditions requires specialized equipment that can withstand the extreme stress and abrasion of the environment.
Modifications and Equipment Adaptations
Drilling in hard rock can generate significant vibrations and stress on equipment. Reinforced frames and mountings help absorb these forces, reducing the risk of structural failure.
The intense friction generated during hard rock drilling can lead to overheating of equipment. Advanced cooling systems, such as enhanced fluid circulation systems, are crucial to prevent overheating and prolong the life of drill bits and machinery.
Standard drill pipes can bend or break under the extreme torque and rotational forces of hard rock drilling. Using heavy-duty drill pipes made from strengthened materials like reinforced steel ensures durability and resilience.
Innovations in Drill Bits and Hammers
Tungsten carbide is a material often used in drill bits for hard rock due to its exceptional hardness and wear resistance. Recent innovations have improved the bonding of carbide tips on the drill bits, enhancing their longevity and effectiveness.
Utilizing small industrial diamonds, these drill bits offer superior performance in the hardest rock formations. Innovations in diamond bonding technologies have significantly increased their durability and drilling speed.
The latest DTH (Down-The-Hole) hammers feature improved air cycle efficiency, reducing fuel consumption while increasing penetration rates. They are designed to handle larger diameter bits and deeper drilling applications, making them ideal for hard rock conditions.
Advanced sensors and automation technologies are being integrated into drilling equipment, allowing for real-time adjustments in drilling parameters based on changing rock conditions. These smart technologies enhance drilling accuracy, efficiency, and safety.
Challenges and Solutions
Drilling in hard rock presents a unique set of challenges that can significantly impact the efficiency and cost-effectiveness of construction and mining projects.
Common Problems
Drilling in hard rock can cause rapid wear-and-tear on drill bits due to the abrasive nature of the rock formations. This wear can lead to frequent bit changes and increased project costs.
Hard rock formations often result in slower drilling rates. This slowdown can be due to several factors, including inappropriate drilling techniques or equipment not suited for the rock type.
The harsh conditions of hard rock drilling put extra stress on drilling equipment, leading to more frequent breakdowns and maintenance issues—potentially causing significant project delays.
Solutions and Expert Advice
Use drill bits designed specifically for hard rock, such as diamond-impregnated or carbide-tipped bits. Innovations in bit design continue to improve their lifespan and effectiveness in cutting through tough rock.
Optimize drilling parameters such as the rotation speed, torque, and drilling pressure based on the rock type and conditions. Real-time monitoring systems can adjust these parameters automatically to optimize drilling efficiency and minimize bit wear.
Implement a rigorous maintenance schedule for all drilling equipment. Regular inspections can identify wear and potential failures before they lead to breakdowns. Using predictive maintenance technologies can also help in forecasting equipment failures.
Ensure that drilling operators are trained in the latest techniques and fully understand how to adjust equipment settings based on real-time feedback and rock conditions. Skilled operators can significantly enhance drilling efficiency and equipment longevity.
Consider using advanced drilling techniques like DTH hammer drilling or rotary-percussive methods, which may offer better performance in specific types of hard rock. Each technique has its strengths and may be more suitable depending on the geological conditions.
View the complete article here.
What is the best drilling method for hard rock?
Down-the-hole (DTH) hammer drilling is highly effective for hard rock due to its percussive and rotary action.
What type of drill bits work best in hard rock conditions?
Diamond or carbide-tipped drill bits are ideal for hard rock drilling due to their durability and hardness.