Waterfront Facility Inspection: Part IV – Synthetic Materials and Components, Quaywalls, and the Inspection Report
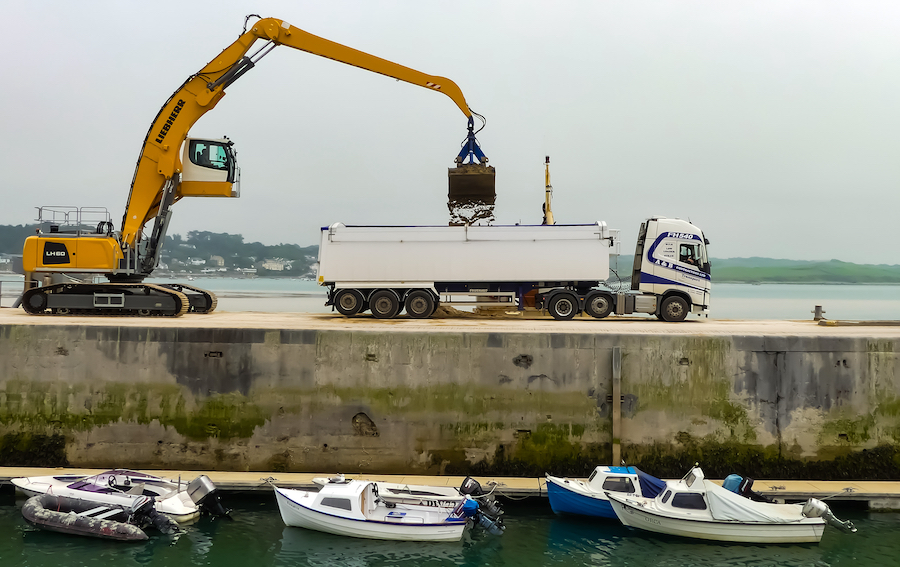
View the complete article here.
5-7 INSPECTION OF SYNTHETIC MATERIALS AND COMPONENTS
Inspection of synthetic materials and components is subdivided into the following three categories:
5-7.1 Structural Members
Structural members should be inspected annually. The inspection should detect:
- Cracked, worn, brittle, or deformed plastic railings, stanchions, gratings, light standards, or piping; loose or damaged fittings and connections; and exposed fiberglass.
- Cracked, worn, or deformed rubber resilient fender components, and/or loose or damaged fittings and connections.
Basic inspection procedures are the same as those outlined for timber or concrete structures.
5-7.2 Coatings, Patches and Jackets
Coatings, patches, and jackets should be inspected annually, or more frequently, depending on the failure rate of the application. The inspection should detect:
- Pits, cracks, scars, or abrasions in coatings.
- Cracked, loose, or dislodged epoxy patches.
- Punctures, brittleness, tears, rips, or abrasions in fabric, or unlocking of fabric seams in pile jackets.
Basic inspection procedures are the same as those outlined for timber, concrete, and steel structures.
5-7.3 Foam-Filled Fenders
Foam-filled fenders should be inspected more than normal pier inspections and should cover:
- Condition of the fender-to-pier connection hardware. Check for operability and signs of corrosion. Check to ensure that the fender is constrained horizontally so that it contacts the bearing surface for its full length. Ensure that the fender is free to vertically float with the tide and rotate around its long axis.
- Condition of the fender chain and tire net for net fenders. Check to see that the chain is symmetrical on the fender and that the end fittings are in good working order. Ensure that the chains are protected from the ship hull by the tires, and that the net is not loose.
- Condition of end fittings on netless fenders. Check to see that the fittings are in good working order, and corrosion is minimal. Check to see that the fender shell is not cracked or separated around end fittings.
- Condition of the fender elastomer shell. Check for cuts, tears, and punctures. Record the size and location of damage on a sketch.
- Measure or estimate the diameter of the fender at its smallest point to record permanent set.
Inspections will be done by walking the pier and using a small boat.
Record keeping for foam-filled fenders is very important. In this regard, the fenders should be treated as an item of high-cost equipment rather than an appurtenance to a fixed facility. Each fender should have a unique identification number with a history record that includes date of procurement, manufacturer, date of installation or when fender was put into service, and berth location if permanently installed.
5-8 INSPECTION OF QUAYWALLS
Quaywalls are an integral part of wharves and should be included when other pier components are inspected.
Deterioration of quaywalls is indicated by:
- Shifts in horizontal and vertical alignment of sheet piling.
- Damage or deterioration of the wood, concrete, or steel sheet piling.
- Wash-out of substrate under the sheet piling, particularly at the toe of the structure.
Alignment shifts can be detected by visual observation. A complete description of shifts and any apparent cause should be provided. Deterioration of wood is covered by the Paragraphs entitled, “Inspection of Timber Structures,” Inspection of Concrete Structures” and “Inspection of Steel Structures.” Wash-out may be detected by visual inspection in clear water at low tide. If not, then an underwater inspection is required. Figure 5-20 “Quaywall Surface and Underwater Inspection Checklist,” is a useful guide.
For each inspection, a report is prepared. The report includes facility plans with updated descriptions, such as: size and pile arrangement, an evaluation of the assessed conditions, and recommendations for further action. The report should provide enough technical detail to support the assessments and recommendations. The Paragraph entitled, “Planning for Inspection” provides guidance for preparing inspection documentation to be used in preparing the report.
NAVFAC MO-322, Inspection of Shore Facilities calls for a three-part inspection report package for shore facilities consisting of a: facility inspection checklist, facility condition summary report sheet, and facility condition detailed deficiency list. Forms for these three sections are shown in Chapter 4, Volume 1 of MO-322. They are, however, geared more for inspecting buildings and are not specifically designed for waterfront structures.
Since waterfront inspections are specialized, a report format such as the one presented in Table 5-7 would be more appropriate. This format is used by NFESC when conducting underwater inspections and assessments at Naval waterfront facilities.
View the complete article here.
What are Synthetic Materials and Components?
Synthetic materials and components in the context of waterfront facilities refer to man-made materials such as plastics, composites, and synthetics that are used in various structural elements like fenders, wales, and decking. These materials are favored for their durability, resistance to corrosion, and low maintenance requirements compared to traditional materials like wood, steel, or concrete.
What does a quay wall inspection report typically include?
A quay wall inspection report typically includes an assessment of the physical condition of the quay wall, details of any defects or issues identified, and recommendations for repairs or maintenance. The report would typically include details such as the location of the wall, a description of the wall, its construction and material details, the observed condition of various components, any signs of distress or failure, and any maintenance or repair recommendations.