Types of Sheet Pile
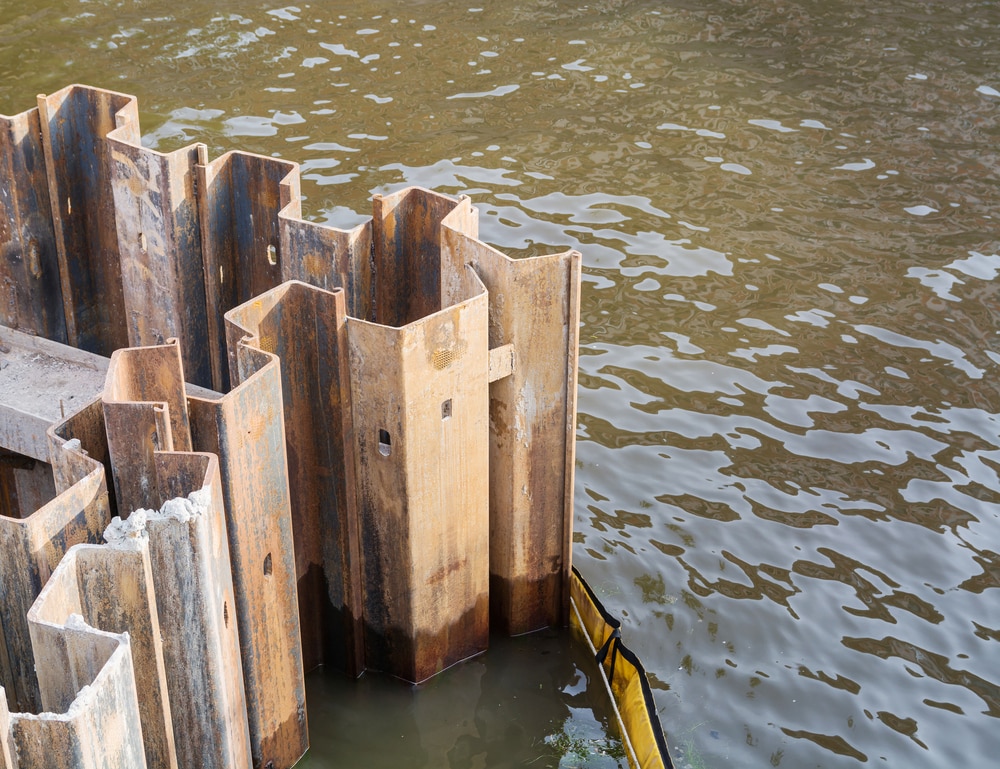
The term sheet piling refers to any retaining wall type that is a) installed into the ground by driving or pushing, rather than pouring or injection, and b) is of relatively thin cross-section and low weight so that the weight of the wall does not assist in the wall’s stability.
The modern sheet piling industry is a little more than 100 years old with perhaps the most important changes in type and selection of products occurring since the early 1970’s. Sheet piling have been used in a wide variety of applications, especially marine bulkheads and retaining walls where space is limited. In addition to these, a special type of retaining wall is the cellular cofferdam, which are used extensively for both temporary and permanent structures.
Sheet piling are made in a number of materials. The material chosen depends upon a number of factors including both strength and environmental requirements. The designer must consider the possibility of material deterioration and its effect on the structural integrity of the system. Most permanent structures are constructed of steel or concrete. Concrete is capable of providing a long service life under normal circumstances but has relatively high initial costs when compared to steel sheet piling. They are more difficult to install than steel piling. Long-term field observations indicate that steel sheet piling provides a long service life when properly designed. Permanent installations should allow for subsequent installation of cathodic protection before excessive corrosion occurs.
1. WOOD
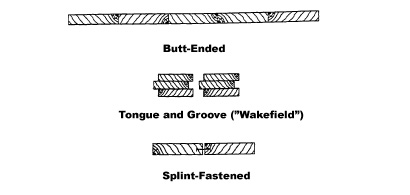
Thousands of years ago, timber logs were placed or pounded into the earth to act as retaining walls or crude dams. Rows of logs were sometimes paralleled and the centre filled with earth to make a stronger wall. Logs were probably lashed together with rope, and a strong back added to combine the logs into a wall. Eventually, it was found that sawn, shaped logs fit together better with less loss of fill through the joints. This lead to the first manufactured sheet pilings having a positive interlocking mechanism between each sheet. Timber sheet piles called “Wakefield” piles were fabricated of three flat wooden pieces. The centre section was offset from the outer sections thus forming a groove and a tongue for joining adjacent piles. A variation of this system was a single timber section in which the groove and tongue were cut to shape. Wakefield type sheet piling is still being used today (see Figure 1.) Many wood sheet pile walls follow the “Navy Wall” design concept, where loads are transferred to round timber master piles and standard dimensional lumber is used for the sheeting.
The interlocking systems devised for timber or concrete sheet piling have been based on the tongue and groove concept. This method serves to keep the wall aligned while providing a longer path against infiltration with more potential contact points than a simple butt joint. The efficiency of such joints depends on good installation practice but the long-term effectiveness is often in jeopardy due to impact from waves or from settlement. The development of filter cloth membrane material for the lining the backside of these walls has reduced the need for more positive interlocks on walls made of these products. As a consequence, many shallow timber bulkheads are built with regular dimension lumber.Timber sheet piling continues to enjoy an important position, in the industry providing relatively inexpensive bulkheads for homes, commercial property and marinas. Timber sheeting is also used extensively in retainment work for shallow trenches and land cofferdams where water intrusion is not a factor.
2. STEEL SHEET PILING
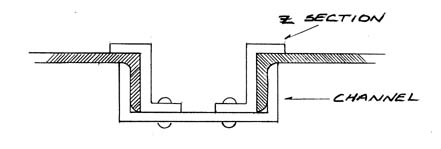
Metal sheet piling was a natural advancement in the evolution of this product as we entered the “Iron Age” in the mid-1800’s. Cast iron was used to make some crude sections, but these were not successful due to lack of ductility. Toward the end of the century, Bessemer steel was developed and mills began hot-rolling I-beams, channels and angles,
among other structural shapes. Freistadt-type piling appeared about 1890, fabricated from a rolled channel section as shown in Figure 2. Z-bars riveted to the web provided a groove into which the flange of a channel could slide, thus forming a crude but innovative interlock. A “Universal” type sheet piling introduced in Great Britain about 1895 utilized hot-rolled I-beams and special clips to join the flanges of the I-beams together. The efficiency of this wall was low because the I-beams were aligned in the weak structural direction.
2.1. LARSSEN SHAPES
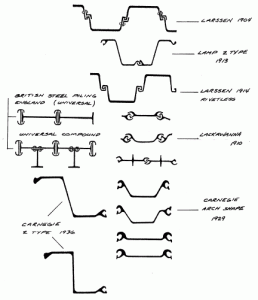
Inventors were striving to develop a sheet piling that would contain interlocks rolled into the beam during the manufacturing process, rather than attached afterwards by riveting. Gregson (USA) patented a bulb and jaw interlock in 1899, however this still resulted in production of a flat section with relatively small section modulus. Trygve Larssen obtained a German patent in 1904 for a deep, hot rolled section that greatly increased the strength and efficiency of steel walls and represented a major advancement. Larssen’s piling wall assumed a “wave shape” when assembled and all subsequent developments for efficient sheet pile walls are based on this concept. Larssen’s section still contained a partially fabricated interlock and it was not until 1914, that a rivetless Larssen interlock appeared in Germany.
In the United States, Lackawanna Steel Co. (later acquired by Bethlehem Steel Corp.) was a flat sheet piling shape and several arched types with rolled, integral interlocks as early as 1910.Carnegie Steel Co. (U.S. Steel Corp.) offered three flat sections with rolled-on interlocks and one fabricated section. By 1929, Carnegie’s catalogue illustrated four deep-arch, two shallow-arch and two straight sections. Some of these and other historical sections of sheet piling are shownin Figure 3.
2.2. Z-TYPE SHAPES
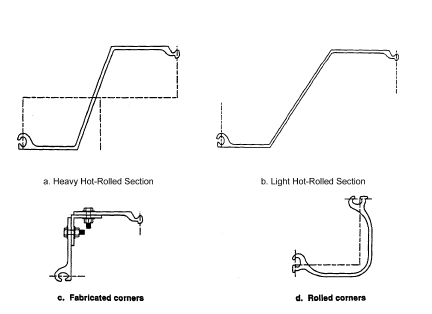
Z-shaped piles followed the Larssen concept for a wave-shaped profile but with the added advantage that the interlocks are formed on the outer elements of the section. The extra metalis put to best use, since it is well out from the neutral axis of the wall. Larssen interlocks are located on the neutral axis. Surprisingly, Z-shaped piles were produced in Europe as early as 1911. The Ransome profile looked very much like some of today’s lightweight Z-shapes. The deeper Lamp Z-pile introduced about 1913, resembles a modern ball and socket Z-type pile.
In Europe, Z-type shapes fell from favour when the Larssen U-types were developed. Two Z-shapes were introduced in the United States in the 1930’s and became quite popular. PZ-38 and PZ-32 offered wider and deeper sections than any of the arch shaped shapes then available. Z-shaped piles obtained some impetus in the U.S. from the long-standing controversy regarding the actual moment-resisting properties of U and Arch shaped sections.
Z-shaped piles interlock on the wall extremities and provide a solid web connecting the two flanges. When the PZ-27 section was introduced in the 1940’s, its section modulus of 30.2 in3/ft was almost three times that published for the arch section with the identical weight per square foot of wall. This section subsequently became the all-time most popular sheet piling section in history. Z-type shapes are now produced with section modulii ranging from 8.6 to about 85 in3/foot of wall.
The Z-type piling is predominantly used in retaining and floodwall applications where bending strength governs the design and no deflection (swing) between sheets is required. Most producers do not guarantee any swing although some can generally be attained or area can be built by providing some bent pieces in the run. Turns in the wall alignment can be made with standard bent or fabricated corners. Typical configurations are shown in Figure 4.
Z-piles are not used in applications when interlock strength is required such as filled cells. These sheets would tend to stretch and flatten in these cases. No minimum interlock strength is offered for this reason. When interlock tension is the primary consideration for design, an arched or straight web piling should be used.
2.3. STRAIGHT WEB SECTIONS
Flat profile sections were originally produced only because of mill rolling limitations. Competition and customer demand prompted the expansion into structurally efficient sheet piling. It was discovered that these flat profiles had strength in tension that was advantageous for building circular, filled structures from sheet piling. About 1908 a large cellular cofferdam was built on the Black Rock River in Buffalo N.Y. in order to de-water the site for a new lock. This concept was progressively expanded to include circular and diaphragm-shaped cells for piers and breakwaters that might have formerly been built of timber cribs or masonry.
The use of large diameter, cellular cofferdams was given a special impetus in the 1930’s when the Tennessee Valley Authority began a series of hydro dams and navigation locks on that river system in the south-eastern United States. Not only did TVA engineers develop new design methods for designing these large structures, they developed better ways of installing and maintaining them.
Flat sheets have little strength to resist bending, but do have very strong interlocks to resist “hoop” stress. These piles are used almost exclusively for building large, filled cellular structures. Flat sheets must provide some ability to “swing” between sheets so that a circle can be closed. Most manufacturers will guarantee a minimum swing of 8 to 10 degrees between adjacent sheets for standard lengths of piling. For overly long pieces, these warranties must generally be negotiated.
Most flat sheet piling has been used to construct temporary cellular cofferdams. After the initial use, the sheets are pulled and used in other portions of the project or perhaps sold for another project elsewhere. Other flat sheets are used in permanent structures such as breakwaters, earth containment sites, piers and other applications. Cellular cofferdams are discussed in more detail in 1.2.1.4.
2.4. COLD FINISHED PILING
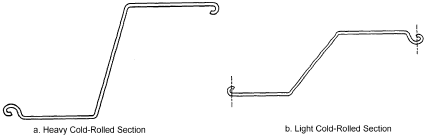
Since the early 1970’s another method of producing steel sheet piling has greatly expanded the availability and the selection of sections. This new method uses hot-rolled sheets in coil form, fed through a series of cold-rolling stands to form “Z” or “arch” shapes complete with a simple, hook-type interlock. This involves a relatively inexpensive capital expenditure compared to the hot-rolled product and has attracted a number of new producers.These steel pilings are shallow-depth sections, cold formed to a constant thick-ness of less than 0.25 inch and manufactured in accordance with ASTM A 857. Yield strength is dependent on the gauge thickness and varies between 25 and 36 kips per square inch (ksi). These sections have low-section moduli and very low moments of inertia in comparison to heavy-gauge Z-sections. Specialized coatings such as hot dip galvanized, zinc plated, and aluminized steel are available for improved corrosion resistance. Light-gauge piling should be considered for temporary or minor structures. Light-gauge piling can be considered for permanent construction when accompanied by a detailed corrosion investigation. Field tests should minimally include pH and resistivity measurements.
See Figure 5 for typical light-gauge sections.
2.5. HIGH MODULUS SECTIONS
There is a limited but regular demand for sheet piling with strength properties that exceed those available from standard products. These may be required for deep excavations, poor soil conditions, deeper dredge lines and other special conditions.
2.6. SHEET PILING NOMENCLATURE & IDENTIFICATION
U.S. producers of sheet piling standardized the identification of sheet piling sections so they could be specified without reference to a particular manufacturers product. The identification included a “P” (piling”) “Z” (type or shape) and “27” the weight, or PZ-27. Arch and flat shapeswere similarly described. Non-U.S. and cold-finishing producers have their own “in house” identification systems. There is now no universal nomenclature system. It is common practice recently to specify the bending moment to be satisfied which then allows the contractor considerable flexibility in his selection of a section and a supplier. This bending moment specification should not be used blindly, however, as many sheet pile designs (especially those using vinyl or pultruded fibreglass sheeting) are principally governed by deflection.
2.7. ORDERING SHEET PILING
Like other steel products, steel sheet piling may be ordered by reference to a standard specification. In the United States this standard is published by the American Society of Testing Materials (ASTM) 1916 Race Street, Philadelphia, PA 19103-1187. The basic ASTM Specification A-328 and others listed may be obtained by writing to the Society or visiting their website//www.astm.org.
This specification covers the steel making process, the chemistry requirements, the minimum yield and ultimate strength. Delivery is referenced in ASTM Specification A-6. The ASTM Specification does not cover interlock tolerances, straightness, interlock strength, nor does it cover rental or second hand material. These are between buyer and seller.
Other Specifications include:
- Canadian Specification CSA 44 W, CAST 44W/70
- British Specification BS4360 – Various Grades
- European Specification: ST SP 37; ST SP 45; ST SP 5.
While the annual consumption of sheet piling in this country rarely exceeds 250,000 U.S. tons, the number of producers and the availability of sections has increased dramatically in the last ten years. In 1960 there were two U.S. producers, each offering nine sheet piling sections. Today there are at least 14 U.S. and non-U.S. producers offering over 200 sections in this country. Competitive factors have generated development of new, wider, more-efficient sections. Large Z-shapes are now available for deep construction with section modulus of almost twice that previously available. A wall system has been developed using large H-sections combined with light Z-shapes that greatly increases the section modulus. Light weight “gauge” material is produced on the cold forming mills for economical shallow bulkheading and trench work.
Higher strength steels up to 60 ksi yield point have also been effectively used in sheet piling design. These grades offer the opportunity to save weight or to extend bending or interlock strengths beyond those of conventional grades. For those applications that require it, corrosion resistant steel can also be specified as well.
3. CONCRETE
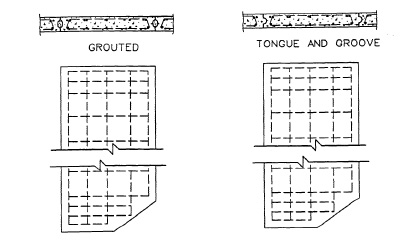
These piles are precast sheets 6 to 12 inches deep, 30 to 48 inches wide, and provided with tongue-and-groove or grouted joints. The grouted-type joint is cleaned and grouted after driving to provide a reasonably watertight wall. A bevel across the pile bottom, in the direction of pile progress, forces one pile against the other during installation. Concrete sheet piles are usually prestressed to facilitate handling and driving. Special corner and angle sections are typically made from reinforced concrete due to the limited number required. Concrete sheet piling can be advantageous for marine environments, streambeds with high abrasion, and where the sheet pile must support significant axial load. Past experience indicates this pile can induce settlement (due to its own weight) in soft foundation materials. In this case the watertightness of the wall will probably be lost. Typical concrete sections are shown in Figure 6. This type of piling may not be readily available in all localities.
4. LIGHT-GAUGE ALUMINUM
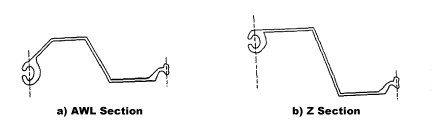
Aluminium sheet piling is available as interlocking corrugated sheets made from aluminium alloy 5052 or 6061. These sections have a relatively low-section modulus and moment of inertia necessitating tiebacks for most situations. A Z-type section is also available in a depth of 6 inches and a thickness of up to 0.25 inch. See Figure 7 for typical sections.
5. VINYL SHEET PILING
Vinyl sheet piling is a relatively new type of sheeting which can be applied in a wide variety of ways for seawalls and other applications of sheet piling. It is generally manufactured by continuous extrusion. The raw material, plastic resin compound, is melted and pushed through a die. This die shapes the plastic into the computer aided design cross section. The sheet is then cooled and cut to length. The sheets can be extruded to the length required for different retaining wall applications.
Vinyl sheeting comes in a number of configurations. The most common configuration is a Z-sheet type of configuration similar to those shown in Figure 4. Others are similar to aluminium sheeting shown in Figure 7. The individual sheets have interlocking male and female edges. The interlocking edges are extruded as part of the sheet to insure consistent strength throughout the retaining wall. As is the case with other sheeting, vinyl sheeting requires transition pieces such as corners and intersections. These are designed to interface properly with the other sheeting the manufacturer makes.
Vinyl sheeting is made of a modified polyvinyl chloride (PVC), which makes it suitable for most marine environments and not subject to leaching, corrosion or similar deterioration mechanisms. The technology that has brought us vinyl siding for homes, plastic automotive parts such as bumpers and dashboards, and durable home appliances, is now being utilized to produce a sheet piling for marine retaining walls, sea walls or bulkheads. The vinyl also includes a UV stabilizer to reduce deterioration due to sunlight.
Because vinyl sheet piling generally has a low modulus of elasticity and strength relative to metal sheet piling, deflection frequently becomes the governing factor in the design of the wall, and should be determined in the design process.
6. PULTRUDED FIBERGLASS SHEET PILING
Pultruded sheet piling is a section of piling that is manufactured by the continuous processing of raw materials by pulling resin-rich reinforcements through a heated steel die to form profiles of constant cross section of continuous length. The first reinforcement utilized in the profile arelong continuous glass fibres referred to as “roving”. Glass roving runs the length of the pultruded profile and gives the shape its “longitudinal strength”. To add multidirectional reinforcement, continuous glass “matting” is added. The roving and matting is now pulled through a resin bath where the glass fibres are saturated with a liquid thermosetting resin. This process is typically referred to as the “wet-out” process.
The coated fibres are now assembled to the proper shape by a forming guide and finally drawn through a heated (curing) die. Once exiting the die, the pultruded shape is cooled and the resulting high strength, reinforced composite sheet piling is cut to length.
Pultruded sheet piling is suitable for a wide variety of applications for light bulkheads. As is the case with vinyl sheeting, deflection is frequently the controlling factor in design, although the strength of the material is several times higher than vinyl.
What are the different materials used in sheet piling, and how does the choice of material impact construction projects?
Sheet piling can be made from various materials such as wood, steel, concrete, aluminum, vinyl, and fiberglass; the selection depends on factors like strength, environmental conditions, and project requirements.
How has the evolution of steel sheet piling shapes progressed, and what are the advantages of different shapes like Z-type, straight web sections, and cold-finished piling?
Steel sheet piling has evolved from early cast iron and Freistadt-type shapes to modern Z-type and straight web sections; each shape offers unique benefits, influencing factors like installation ease, bending strength, and interlock efficiency.