Ferry Terminals and Small Craft Berthing Facilities – Manual Part 2
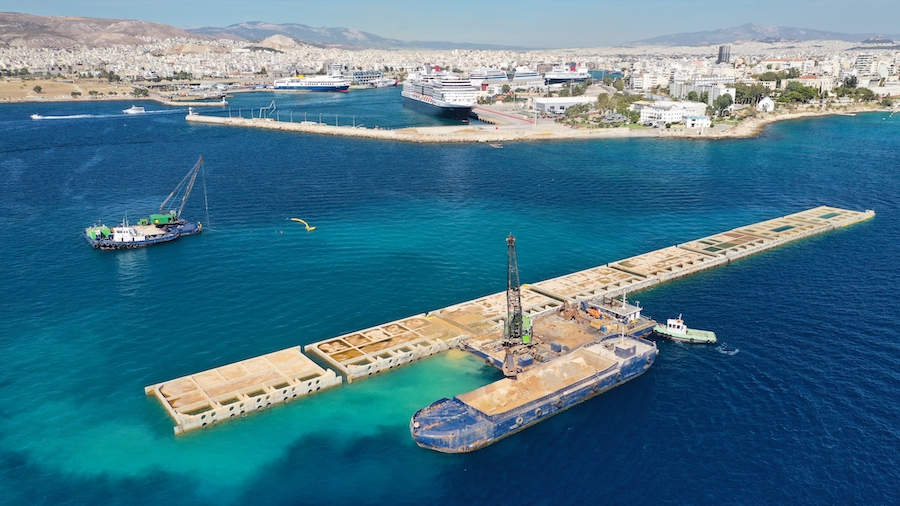
View the complete article here.
Designing Entrance Criteria and Protective Structures
Entrance channels and other protective structures play an important role in the functionality of a small craft berthing facility; without proper placement and construction, the facility will not be useful.
That is why contractors must carefully evaluate a number of issues, in consultation with specialists, in planning entrance channels and other protective structures.
When determining the placement of the entrance to the facility, the natural water depths and the character of the waves approaching the harbor should be considered. A contractor should analyze littoral drift, wave generation and refraction. Plus, a hydrographic survey to determine proper placement should be conducted.
The channel should be placed as close to the natural channel alignment as possible. If bends are necessary, they should be placed as close to the natural channel alignment as possible.
Breakwaters are often constructed to prevent or reduce wave energy transmission into the facility. This is done to provide more sheltered conditions for the facility and to protect the harbor entrance.
Contractors should obtain and evaluate a variety of data in determining where to place breakwaters, including:
- degree of protection intended in the lee of the structure
- wave runup, hydrographic and topographic surveys of the site
- degree of permissible overtopping
- hydraulic model analysis for the wave-basin space
- shape and roughness or armor material
- degree of permeability permissible
The breakwater should be positioned approximately normal to the primary direction of the wave approach, as close to the shore as possible. It should not encroach on the water area that is needed for an entrance and fairway during normal and peak boat traffic conditions.
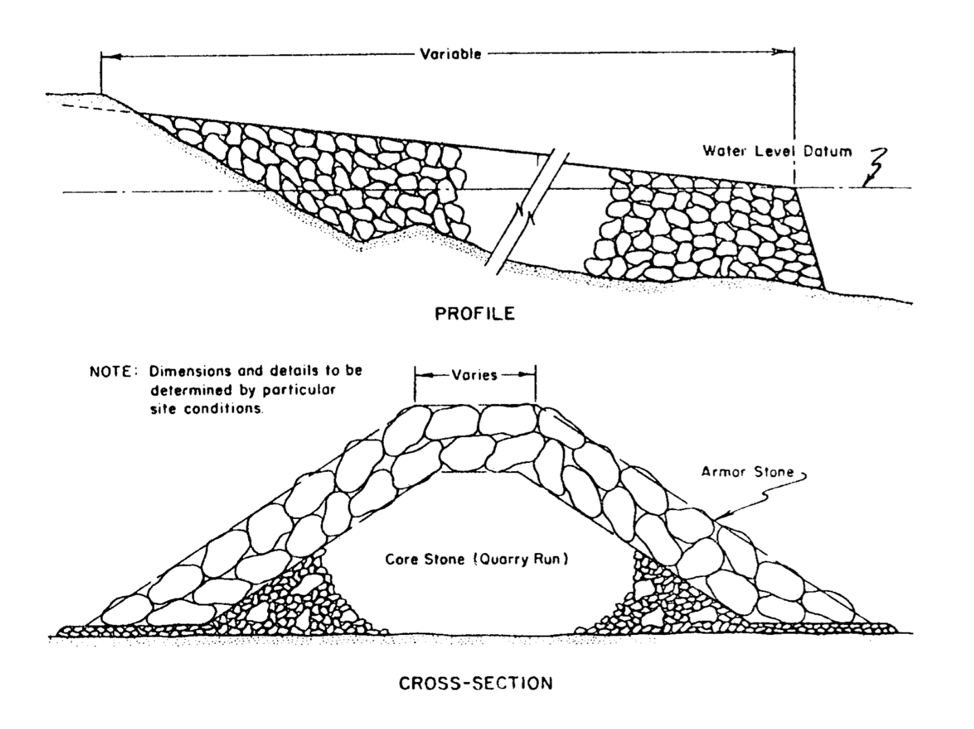
Protective Structures
Groins may be used to reduce the loss of material out of an area, build or widen a beach by trapping littoral drift, reduce the rate of longshore transport, prevent accretion in a downdraft area or stabilize a beach subject to excessive storms.
There are numerous types of groins, including timber, steel, concrete, rubble-mound and asphalt groins.
Jetties are structures that extend into the water. They are typically used to prevent or reduce shoaling of the channel by littoral material, direct or confine tidal flow into the channel, protect the entrance channel from wave action and cross currents, and stabilize the inlet location.
There are two primary jetty types to consider: rubble-mound structures and sheet pile structures.
Wave and surge dissipators are used to reduce turbulence in the boat basin that is caused by wave energy and surge. They can be built in a number of ways, such as by creating a non-uniform array of large stones, placed on top of a flat slope facing the outer entrance at the first turn in the entrance channel.
Alternatively, a wave-absorption beach can be made, recessed in the elbow in the first bend in the channel. Finally, a wave reflector can be made to reflect the waves back towards the first leg of the entrance channel.
Bank protection structures can be used to protect banks from waves and currents in the channel. This can be done be placing rubble on a filter layer, or by using sheet pile or by constructing a pour-in-place concrete wall at the top and a revetted concrete slope from the toe of the wall to the channel bottom.
River protection can be constructed to berth boats directly in a river. These methods may include a shallow basin excavated into the riverbank, or a current deflector placed upstream.
A current deflector is built as a pile-dike fence, which is then inclined downstream. Heavy beams for horizontal members in the area of surface-level fluctuation will then fend off floating debris.
Finally, floating wave attenuators can reduce moderate waves to reduce their impact. There are a number of types of floating wave attenuators, including:
- chained log booms, which are mainly used on rivers and small lakes; floating breakwaters, made out of modular polyolefin pontoon units
- worn-out rubber tires secured together
- air-filled mattress at the surface or suspended below the surface
- thin membrane on the surface
- random arrangements of horizontal pipes
- series of vertical diaphragms
- solid structures with void patterns.
Each of these floating wave attenuators is designed to break up wave motion.
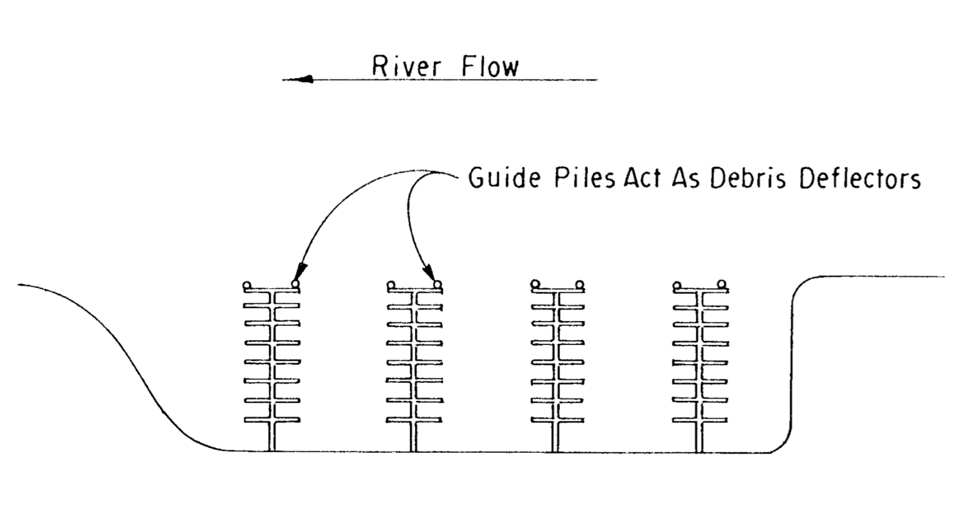
Designing Support Facilities
Beyond the berthing, harbor, entrance channel and perimeter of the small craft berthing facility, a contractor must also plan for the various structures that support the facility itself.
This includes all of the various buildings and utilities that are necessary to run the harbor, from firefighting equipment to fuel docks to launching ramps.
Safety should be a top priority in constructing a small craft berthing facility. To that end, contractors should make sure that the appropriate utilities are provided for, including water, electrical and sanitary systems.
In addition, an intercom system should be installed, with speakers located along the harbor so that every slip and support facility can hear announcements.
A central telephone switchboard in the administration should also be included.
Firefighting equipment, such as chemical firefight equipment (if warranted) and fire-alarm boxes, should be placed along the main walk and at convenient locations on or near the piers.
Locker boxes should also be provided for gear and structural storage along the piers.
Fuel docks should be built in a manner that supports the fuel pumps and in locations that are accessible to the buried tanks ashore.
Floating systems must have flexible fuel lines that lead to the fixed lines that are installed in the docks.
Quick-disconnect devices should be provided at the high point in each fuel line to prevent siphoning of the storage tank contents into the basin in the event of a line break.
Pump out stations should be placed on or near the fuel docks so that these two tasks can be accomplished successively. However, the pump out station should not be located too close in proximity to the fuel pumps.
Each dock or slip should have a full set of cleats for mooring lines, along with fenders to break the impact of moored or drifting boats against the dock.
Cleats are typically made of galvanized or non-corroding metal alloys, or of hardwood.
Launching hoists, elevators and ways are also necessary items that must be included in a small craft berthing facility.
The most common types that are used to transfer crafts between land and water include davits, forklift trucks, jib-boom cranes, lift slips, marine railways, mobile cranes, overhead rail launchers, stiff-leg derricks, straddle-truck boat hoists and vertical-lift platforms.
Forklift trucks are well-suited for small craft berthing facilities with relatively little water level fluctuations, while vertical-lift platforms are mainly used for large crafts (over 25 tons).
Launching ramps are typically built with slopes between 12 and 15 percent.
The ramp surface should generally be paved down to an elevation of three feet below extreme low water to make sure that trailers are not backed over the lower end.
An administration building should generally include enough space for a reception office, a record board to display the graphical layout of the facility, record files, offices for the manager, communication center for incoming and outgoing calls and the address system, restroom facilities, and supplemental facilities such as storage rooms, break rooms and meeting rooms.
Dry storage is also a necessary component of a small craft berthing facility, for lack of sufficient space in protected waters, or to simply keep boats dry when not in use. Generally, dry storage is limited to crafts that are less than two tons.
Depending on the project requirements, other structures to consider are a maintenance and storage yard, a boat repair facility, a hardware supply store, transient housing facilities, road and walkway system, and perimeter fencing.
Contractors should also make allowances for appropriate signage, such as welcome signs, directional signs, and signs noting regulations.
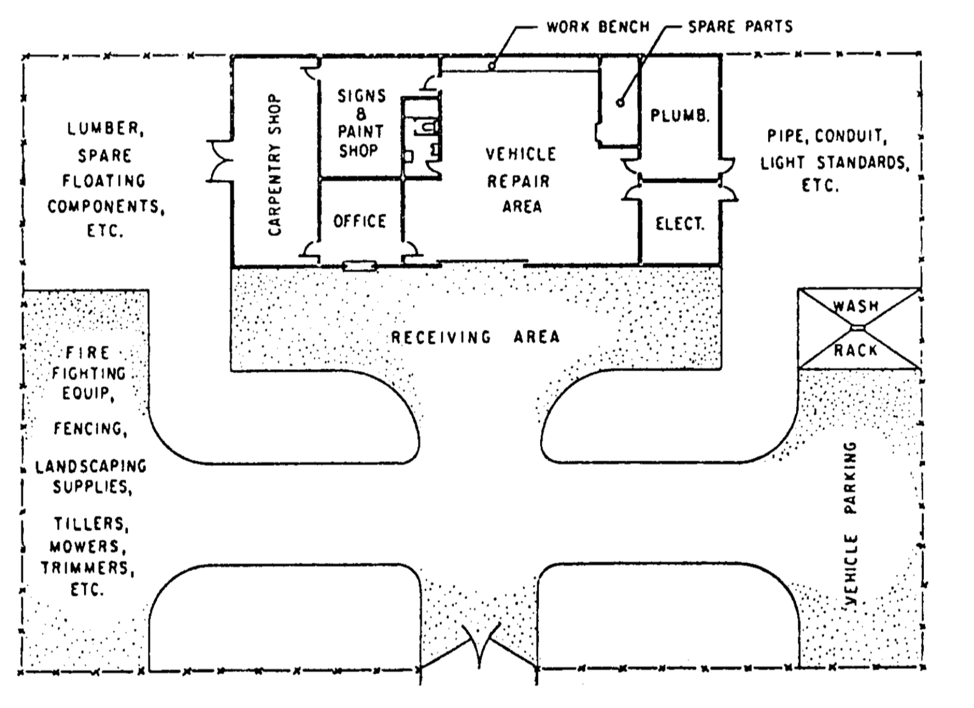
Environmental Factors and Protection
As with any construction project, contractors must carefully design a small craft berthing facility to withstand weather extremes that are typical for a given area. Based on the location of the facility, this may include snow, ice, hurricanes, floods, or tornadoes.
For snowy areas, protective measures must be taken to counteract the weight of snow on floating pier systems and the roofs of floating sheds. Boats berthed in the open during winter months can be fitted with tarpaulins, fitted canvas or reinforced plastic covers for protection.
To protect against submergence, boats can be removed to dry storage before winter. This may include placed on cradles on land, with larger boats being covered and smaller boats being stored keel up to allow for shedding of snow and rain.
In areas where ice is a problem, ice formation can damage boats and facility structures. Forced convection of water through a bubbler system can push warmer water to the surface, preventing the formation of ice sheets.
Otherwise, piles can be driven in deeply to allow them to develop withdrawal resistance to the ice.
Breakwaters and jetties also can provide ice-impact protections, along with deflecting booms.
Hurricanes can cause tremendous damage to facilities and boats. Pile guides and cable or chain anchorage systems for floating docks can accommodate fluctuating water levels and resist lateral wind forces.
Decking, roofs and other parts of the docks can be fastened down, and hurricane shutters can be used to protect the buildings.
Flood damage is common. Floods can often result in debris accumulation and collision of floating objects. This can be rectified by providing a training wall to protect against debris and shoaling.
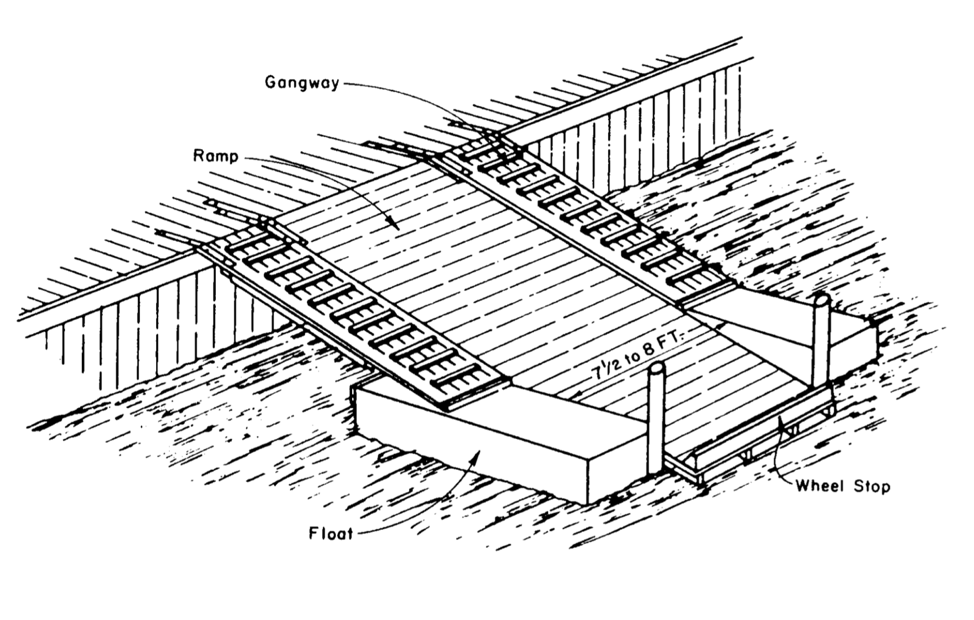
Summary of Common Design Problems
There are a number of problems that commonly occur at small craft berthing facility. These can be anticipated and planned for by a skilled contractor.
Ice is a significant issue in cold regions, with free-floating cake ice being one of the greatest causes of damage. If ice formation is anticipated and when feasible, piles should be driven butt down.
For floating piers, forced convection or bubbler systems are highly effective in preventing ice from forming.
Corrosion is also a common issue in small craft berthing facilities. Low level lighting systems may fail, water values may be corroded, and untreated wood decks may disintegrate as a result of seawater. The solution is to use the appropriate products for the environment.
Fuel dispensing creates another issue, with many facilities encountering issues fueling boats at extreme low water levels at fixed pier stations. They may have trouble with the reliability of their fuel line connections to floating pier stations.
Floating pier systems can create problems due to the difficulty of adjusting chain or cable anchorages during water level fluctuations, as well as the tendency of these piers to drift beyond the desired limits. In addition, the time and difficulty in removing and storing floating piers for winter can be an issue.
Shoaling is another major issue for many small craft harbor facilities, as maintenance, including dredging, is time-consuming and difficult.
Finally, enforcing speed limits to reduce boat wake can be a challenge.
Degaussing and Deperming Facilities
For some projects, it may be necessary to install degaussing and deperming facilities.
Degaussing is the process in which a craft is equipped with a cable to neutralize its magnetic polarity through electricity. This is done to protect it against magnetic mines, and to approximate the effect of a nonmagnetic ship or boat.
Continuous application of current is required to maintain a degaussed condition.
Deperming consists of removing the permanent magnetic characteristics of a craft using powerful demagnetizing coils.
While it would be unusual to need these facilities at an average small craft berthing facility, if they are required, it will mean providing certain items. This includes special electric power and strategic work areas to obtain measurements.
View the complete article here.
How should contractors determine the placement of entrance channels in a small craft berthing facility?
Contractors should consider natural water depths, wave characteristics, littoral drift, and conduct hydrographic surveys to ensure proper placement.
What are some common environmental factors to consider when designing a small craft berthing facility?
Environmental factors include snow, ice, hurricanes, floods, and tornadoes; protective measures range from tarpaulins for snow to bubbler systems for ice prevention.