Assessment and Corrosion Repair of Damaged Concrete Structures In the Persian Gulf Region
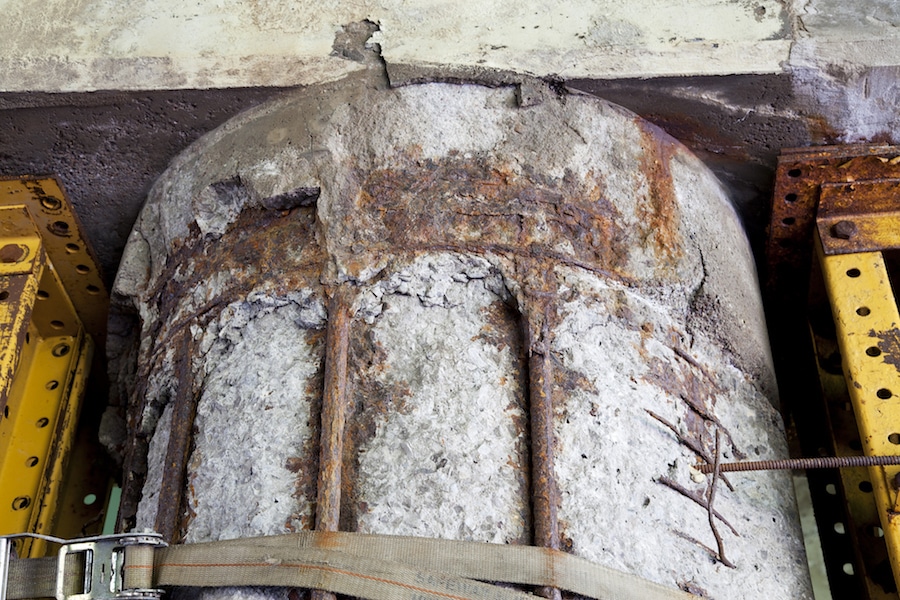
by Mobasher B., Shekarchi M. and Tadayon M. H.
Abstract
Corrosion of reinforcement has a damaging effect on the resilience of concrete structures. Corrosion is attributed to penetration of chloride and the reduction of pH of the concrete matrix due to carbonation, which decreases the passivity of steel reinforcement, whereby the active corrosion process begins.
Concrete structure reinforcement corrosion accounts for over half a percent of the GDP of most developed countries, a fact meriting the importance of evaluation and repair methodologies. The widespread use of reinforced concrete in infrastructure necessitates viable evaluation of corrosion damage.
The Persian Gulf is among the most corrosive areas in the world because of its exceptionally high water salinity and unique humid and hot weather. For these reasons and more, reinforcement corrosion is becoming a major problem in the Persian Gulf region. This paper discusses a case study, evaluates existing structures and suggests measures to limit corrosion of existing concrete structures as well as repair methods.
Introduction
Worldwide consumption of cement and concrete amounts to a staggering 10 billion tons per year. The commercial value of this quantity exceeds $600 billion. Arguably, such immense investment could translate to long-term performance, but there are some significant durability issues where civil infrastructure systems are concerned, such as low tensile strength, corrosion of concrete materials, chemical attack and brittleness. A key challenge for all affected parties is therefore to research and develop new applications using cement-based materials that are durable, strong, flexible, robust, and economically feasible in view of the ever-rising demand.
Transport and Durability Features
Durability is directly affected by chemical species’ resistance to transport throughout the porous system, which has multiple components. The relevant transport features of aggressive media are characterized by the interaction of competing mechanisms of sorption, ionic and gas diffusion and gas and liquid permeability [[i], [ii]] Deterioration is accelerated by early-age cracks caused by restrained shrinkage and desiccation. Plastic shrinkage occurs mainly due to the high rate of evaporation through the pore structure of concrete [[iii], [iv], [v]], even though it has also been attributed to several driving forces such as thermal dilation, differential settlement and deformation that occurs autogenously.
To a great extent, transport features and properties are affected by the connectivity and degree of capillary porosity in the microstructure [[vi]]. The analysis of diffusivity and pore structure is contingent on different variables and can be analyzed under various scales, which range from macrostructure to nanostructure.
Some of the main characteristics at the basis of transport mechanism analysis are coefficients of gas permeability Kg (m2), gas diffusivity Dg (m2/s), water permeability Kw (m2), ionic diffusivity Di (m2/s) and moisture diffusivity Dm (m2/s)[6].
Evaluation of the State of Existing Structures and the Quality of Concrete
The first and most significant step when devising a strategy for the repair of a reinforced concrete structure is adequate evaluation of its quality and condition. The following measurements are generally used:
Visual Examination – Careful visual examination is the initial and most important qualitative concrete assessment. This type of inspection is very feasible for the recognition of the type of deterioration and damage and the respective causes. It enables an estimate of the required measurements for additional investigation and repair planning.
Non-destructive Tests – There are a number of quantitative non-destructive tests for reinforced concrete quality assessment. Some of them may be chosen to assess a structure depending on its access, type, life cycle expectancy, importance, extent of damage and environmental conditions.
Destructive Tests – There are a few destructive or semi-destructive test approaches for assessment of reinforced concrete condition. These tests generally yield more exact results based on specific controlling parameters of interest than quantitative non-destructive tests, but are also more time-consuming and expensive [15].
Below is a list of some available destructive and non-destructive tests which can be carried out:
– Bulk absorption of Concrete (ASTM C642)
– Resistance of concrete to chloride ion penetration (AASHTO T259)
– Chloride content and diffusion coefficient (ASTM C114, C1152, C1218)
– Rapid Chloride Penetration Test or RCPT (ASTM C1202)
– Carbonation depth determination (RILEM CPC-18)
– Compressive strength (ASTM C42)
– Gravimetric steel weight loss due to corrosion (ASTM G1)
– Corrosion rate by GalvaPulse®
The ohmic resistance of concrete is being used more and more often as an indirect measure of concrete characteristics such as chloride ion diffusivity and permeability to the fluids, both of which demonstrate positive correlation with the degree of resistance of the concrete to the repercussions of severe environments such as those of the Persian Gulf, where the temperature can reach 50 degrees Celsius, humidity is as high as 95% and water salinity is about 39 g/L. These conditions of the environment intensify deterioration mechanisms [[i]]. The concrete ohmic resistance may also offer useful information regarding the risk of steel fiber corrosion in concrete. There seems to be a linear relationship between the conductivity of a steel rebar embedded into concrete and intensity of corrosion according to RILEM TC 154-EMC [[ii]].
Deteriorated reinforced concrete structures can be rehabilitated and repaired in one of several ways. The exact way depends on the degree of deterioration, the conditions of the environment and the availability of rehabilitation and repair products.
One also needs to keep in mind the skill level of the workforce used to carry out the repair procedure. Common available repair options include removing and cleaning up delaminated and spalled concrete and replacing it with an overlay patch, installing cathodic protection to protect the steel reinforcement from further corrosion or removing all the contaminated chloride or carbonated concrete and patching it with an overlay [4].
Reinforced Concrete Corrosion
The most important factors that determine the corrosion rate are oxygen content, concrete ohmic resistance, pH, relative humidity and temperature. Most frequently, concrete begins to corrode due to chloride ion from concrete ingredients. Occasionally the reason may involve de-icing salts or saline seawater [15].
The main causes of corrosion in conventionally reinforced concrete involve resistance of the reinforcing system to the stresses resulting from expansion of the reaction products of corrosion process and the consequences of this, such as concrete cracking and delamination. These are accounted for by chloride-induced corrosion and also such caused by carbonation, leading to the reduction of pH of the concrete matrix. Depassivation of steel reinforcement in concrete occurs at chloride threshold levels of approx. 0.15% and 0.6% by weight of cement (ACI 318, Norwegian Code NS3474)[[iii]]. A study on steel FRC specimens exposed to marine tidal cycles showed these did not corrode at all at Cl– concentration over 2% (by weight of cement) of low carbon steel and galvanized steel fibers embedded in the matrix [[iv]] [[v]].
Mechanical performance was evaluated using the wedge-splitting tests before and after exposure of the pre-cracked cubes to the various environments [[vi]]. This study showed that sensors bridging the crack demonstrated high electrochemical impedance comparable to that of those placed in the sound non-carbonated concrete. This impedance was higher than 1 M-ohm under all the exposure conditions except wetting in NaCl, showing absolutely negligible corrosion. This is consistent with the microscopic analysis. The depth of carbonation is normally quite small even for specimens dried in the CO2 environment – just 1 to 2 mm. It is most likely that the determining factor is the type of concrete.
No decrease in strength was observed regardless of exposure conditions in plain concrete samples after 18 months of exposure. Specimens wetted in NaCl environment showed full chloride penetration: up to 3g Cl– /kg concrete.
Reinforcing Structures with Fiber as Corrosion Protection
Fiber reinforced concrete structures are subjected to carbonation and chloride penetration that could bring corrosion of steel fibers, resulting in structural deterioration and reduced durability. The concrete is penetrated by liquid or gas corrosive agents. The rate of carbonation penetration depends on the permeability of the concrete and slows with time, making the process a self-decelerating one. Carbonation begins on the concrete surface and develops inwards, whereby its rate declines. Research has shown that it stops when it reaches the high concentration of calcium hydroxide near a fiber. A fiber may start to corrode when it loses this protective passivation layer.
The chloride diffusion depends of the concrete pore structure and all the other aspects of structure, including presence of cracks [[i]].
Case Study: Evaluation and Rehabilitation of Damaged Jetty Structures
The case study presented here is a jetty structure on steel piles with a concrete deck and concrete beams as the pile cap (Figure 1). It was built in 1976 in Bandar-e Imam Port in the western region of the Persian Gulf and repaired in 1990, but had to be repaired again less than 7 years later.
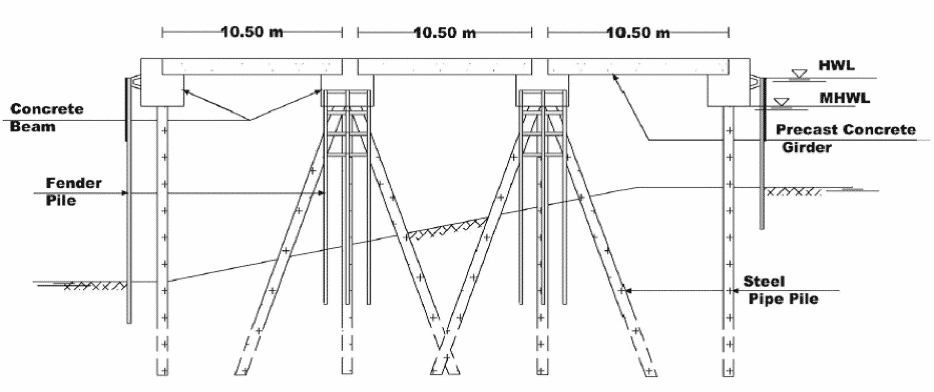
Both visual and NDT inspections were carried out as part of the condition studies of the jetty structure in this case. Visual inspections of the concrete beams showed spalling of concrete on both the repaired and substrate concrete and longitudinal cracks. The cracks were mostly located in the boundary areas and interface of repaired and substrate concrete, presenting evidence of the incipient anode effect, often observed after patch repair. Moreover, the reinforcements had corroded severely in some areas.
Both destructive and non-destructive tests were applied including ohmic resistance, bulk water absorption, chloride content, carbonation depth and half-cell potential. All in all, these tests showed that the repaired materials were of lower quality than substrate concrete, as they started to corrode soon afterwards. The study also showed that precast concrete performs better than the cast in place components, which may be due to control of ingredients leading to lower chloride content and better construction conditions (e.g. curing period) [1].
Conclusions
Corrosion affects edge areas to a greater extent because of the exposure to oxygen, chloride ion and moisture from two or more directions. Suitable concrete cover with sufficient thickness, using concrete materials of adequate quality, proper concrete mixture and stable construction, curing and maintenance are all crucial factors for the protection of concrete structures from reinforcement corrosion.
Corrosion of concrete structure reinforcements generates enormous repair and rehabilitation costs, particularly in the Persian Gulf region. The materials used to repair the corroded concrete should be mechanically, electrochemically and dimensionally compatible with the substrate. If they are not, the incipient anode effect and subsequent severe corrosion are inevitable.
Why is corrosion assessment crucial for concrete structures in the Persian Gulf region?
Corrosion assessment is vital due to the region's high water salinity and harsh weather conditions, impacting the resilience of concrete structures.
What are the key evaluation methods for the state of existing concrete structures and their quality?
The evaluation involves visual examination, non-destructive tests, and destructive tests, including ohmic resistance, bulk water absorption, chloride content, carbonation depth, and half-cell potential assessments.