INTERVIEW: CMI
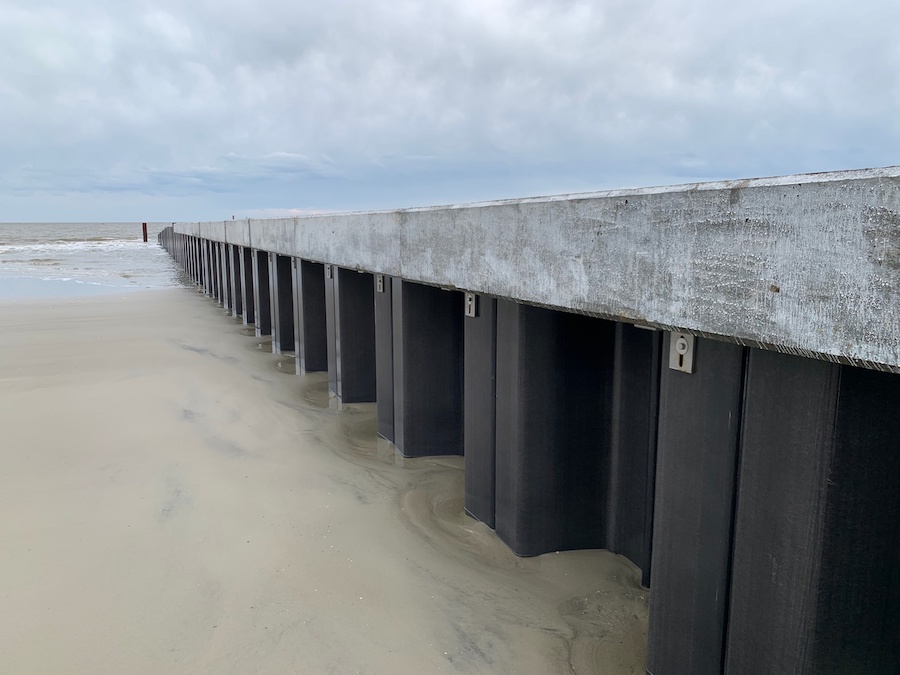
Pile Buck’s interview with CMI, the leading manufacturer and fabricator of engineered products providing solutions for marine walls, flood-levee protection, water control, chemical containment, soil stabilization, groundwater cut-off, aluminum bridges, gangways, docks and industrial access applications.
PB: It appears that CMI offers a variety of products for the marine construction industry. What are your most popular products and the application(s) they are used for?
CMI:
- (ShoreGuard®, UltraComposite™ and AlumiGuard™) Synthetic-Sustainable Sheet Pile (Vinyl, RFP and Aluminum) for Seawalls, Bulkheads, Floodwalls, Trip walls etc.
- (GatorDock®, GatorAccess™, GatorBridge®, Mantle Industries) Aluminum Docks, Marine Access, Gangways, Pedestrian Bridges for Commercial HOA, Marinas, Parks & Recreation etc.
- (Lumberock®, Bear Board) HDPE Plastic Decking for Docks, Marine Access, Boardwalks, Seawall Caps, Trails etc.
- (TimberGuard®) Polyethylene Encapsulated Marine Grade Pole Piles and Dimensional Lumber for Seawall/Bulkhead Structures, Fixed Pier and Floating Docks etc.
CMI: ShoreGuard® VSP is environmentally friendly, sustainable and readily available with short lead times via regional distribution and direct shipments by being 100% “Made in America”. ShoreGuard is ideally suited for all types of water and soil management applications: Seawalls, Bulkheads, Floodwalls, Trip walls, Retaining Walls, Cut-off & Containment, Weirs, Wave Breaks, Dams etc.
PB: What other type of sheet piling options do you offer?
CMI:
CMI® produces Fiberglass Reinforced Polymer (FRP) called UltraComposite™
CMI also produces Aluminum Sheet Piling called AlumiGuard™
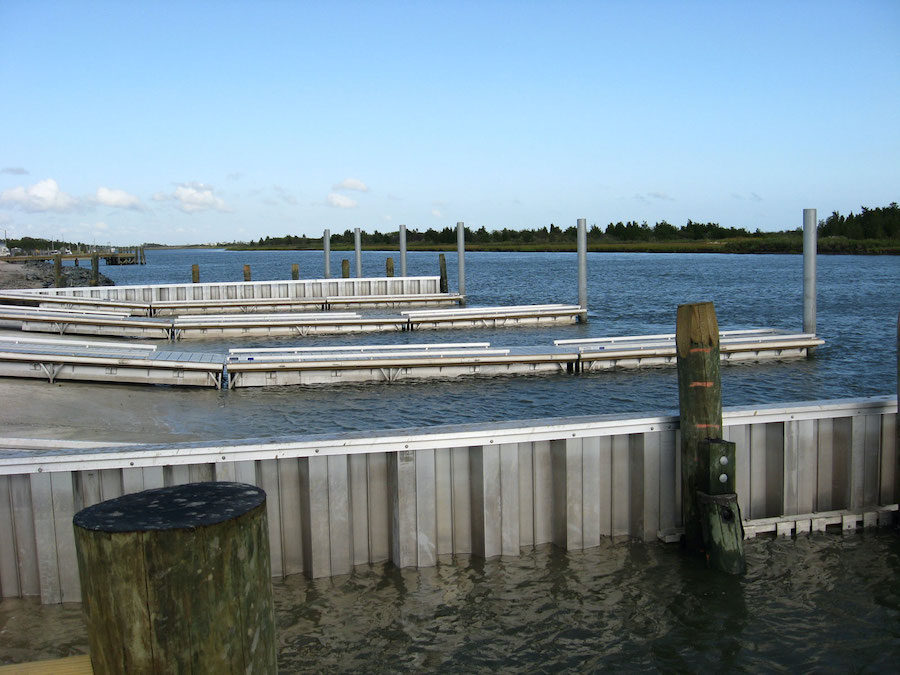
PB: How about installation equipment? How are your products typically installed?
CMI:
CMI sheet piles are installed with a variety of vibratory hammer equipment, driving helmets, mandrels and pre-trenching.
CMI produces and leases proprietary pile driving assist equipment called a PileClaw® that is engineered specifically for specific sheet pile profiles and is offered on a by-project or application type basis based on working with the design and construction teams’ needs.
PB: In addition, a lot of PB readers deal with timber piling on a regular basis. Tell us about the advantages of TimberGuard®.
CMI: TimberGuard® is an industry leading environmentally friendly and sustainable product technology that is constructed with CCA 0.8 and 2.5 Pressure Treated Lumber that is encapsulated in Polyethylene. TimberGuard meets New Jersey’s Administrative Code on Coastal Zone Management Rules regarding “Non-polluting materials.” identified as plastic, natural cedar or other untreated wood, polymer-coated, pressure-treated wood, concrete, steel or other inert products. Creosote and pressure-treated lumber – that is, treated with preservatives such as CCA-C. ACZA, CC, and ACQ – which is susceptible to leaching is not considered “non-polluting material.”
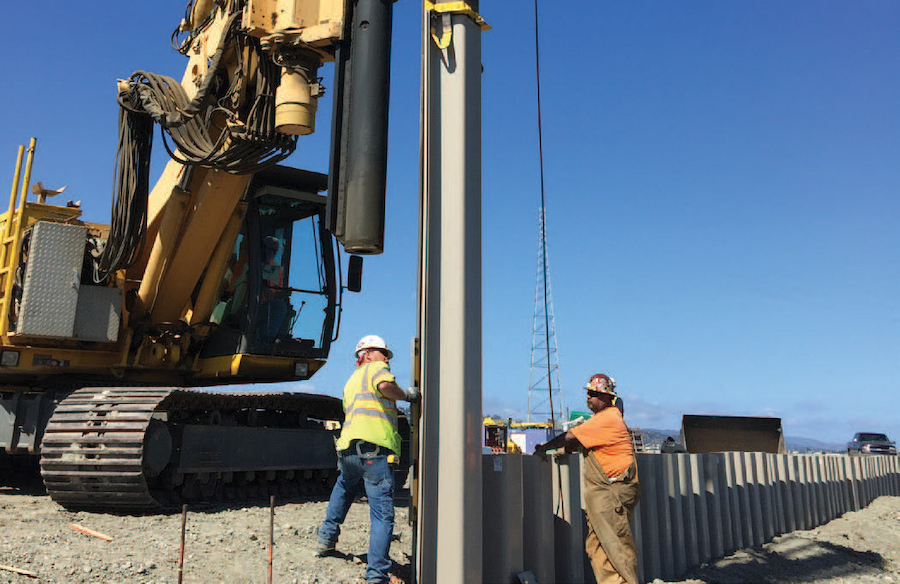
PB: Based on your experience with clients over the years, do any particular projects stick out? Any unusual obstacles?
CMI: We has been fortunate to have been selected for many of the most challenging water, soil management and marine access projects built of the past 40 plus years built by the leading construction teams in the world. We have also been fortunate to provide aesthetically pleasing long-term protection on tens of thousands of residential, water-facing properties all over America.
PB: Is there a common pattern of obstacles that your clients face? Do you have any general suggestions for marine contractors out there?
CMI:
- Access to capable contractors
- Optimal product selection
- Pre-construction planning
We have developed design assist and pre-construction services aimed at helping owners and engineers analyze their projects, select optimal products that are engineered for their applications and then connect them with leading marine contractors. We strive to add value by being a resource for all the construction team constituents.