Molex Teams with Pile Dynamics to Transform Structural Foundation Testing
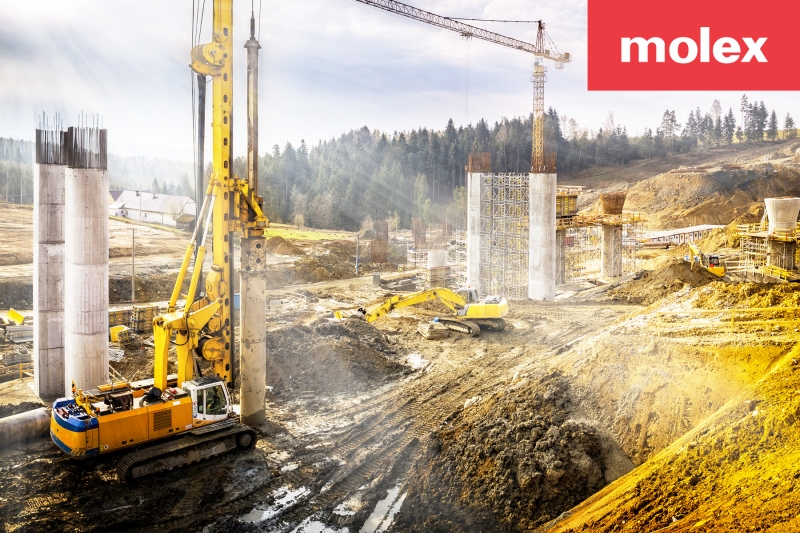
- Seamless collaboration facilitates continuous product innovations and quality improvements to elevate industry testing standards
- Shared quality commitment drives rapid delivery of industry-leading dynamic foundation testing solutions amid supply chain constraints
- Molex’s proven connectivity, cabling, and manufacturing automation enable PDI to handle one million product orders as business doubles year-over-year
LISLE, IL – Molex, a global electronics leader, and connectivity innovator, today announced a highly successful collaboration with Pile Dynamics Inc. (PDI), the largest manufacturer of deep foundation testing equipment in the world. Together, the companies are using the latest innovations in connectors, cables and sensors to revolutionize the traditional quality testing of the foundations supporting massive infrastructures, such as bridges, skyscrapers and stadiums, without fault or failure.
Based in Cleveland, PDI develops quality assurance and testing equipment to assess the integrity of deep foundation structures on land and in water. Over the past half-century, PDI’s products have been used on jobsites in more than 100 countries, earning its flagship Pile Driving Analyzer® (PDA) a reputation as the gold standard in high-strain, dynamic load-testing and pile-driving monitoring. Through its commitment to quality and innovation, PDI delivers accurate results in real time, in sharp contrast to traditional testing methods, which can take up to 10 days.
“Our patented method is much faster, more comprehensive and can be completed at half the cost of other testing methods,” explained George Piscsalko, president of Pile Dynamics Inc. “All our data is stored in the cloud, so no site visits are needed, which further reduces time, cost and carbon footprint. As PDI continued to add sophisticated technologies and sensors to its solutions, it became apparent we needed to team with a more progressive, proactive connectivity solutions provider like Molex that could solve problems and really help move our business forward.”
Shared Commitment to Quality and Innovation
Initially, Molex’s drop-in connector enabled PDI to address reliability and availability issues with an existing supplier, which then set the stage for a deeper level of collaboration. “What was most interesting to us was PDI’s clear position as a disruptor in this industry,” added Daniel Koch, senior product manager, Global Consumer & Commercial Solutions Division, Molex. “They use technology and electronics in a way this industry has not seen before.”
PDI leverages Molex’s extensive experience in highly demanding automotive, consumer electronics, healthcare and data center environments to address rigorous performance requirements. For example, Molex eliminated the need for manual intervention while testing splice connectors installed hundreds of feet underwater, which lets construction crews perform testing in less time and at much lower risk. Additionally, Molex incorporates sensors directly into PDI’s Thermal Wire® cable to speed and simplify production of the company’s leading-edge Thermal Integrity Profiler (TIP™). In doing so, PDI can evaluate concrete quality both within and outside a rebar cage while delivering secure cloud-based testing results instantaneously.
Meeting Record Demand Amid Supply Chain Constraints
Molex has developed automation solutions to accelerate the production of custom cable assemblies, which enables PDI to build prototypes faster while expediting novel product designs featuring new and different technologies. Molex’s cable assemblies assist in the early prototype process, concept design and development phases, focusing on reducing time-to-market while providing best-in-class preproduction support, quality checks and cost-reduction support. Furthermore, Molex’s industry-certified manufacturing plants support design manufacturing from early production to high-volume, fully automated assembly.
During the COVID-19 pandemic, Molex stepped up to help PDI ensure a steady flow of raw materials to scale production by aligning experts in global supply chain management, procurement and logistics. Thanks to a reliable supply chain and industry-leading connectivity innovations, PDI expects to double its business year-over-year with a 2023 sales pipeline of about two-to-three times bigger than current levels. “To us, Molex is more than a vendor,” says George W. Piscsalko, production manager at PDI. “They’re an integral part of our business, bringing solutions to the table we really value and delivering them not only on time, but often ahead of schedule.”