Geotechnical Engineering Risk Management
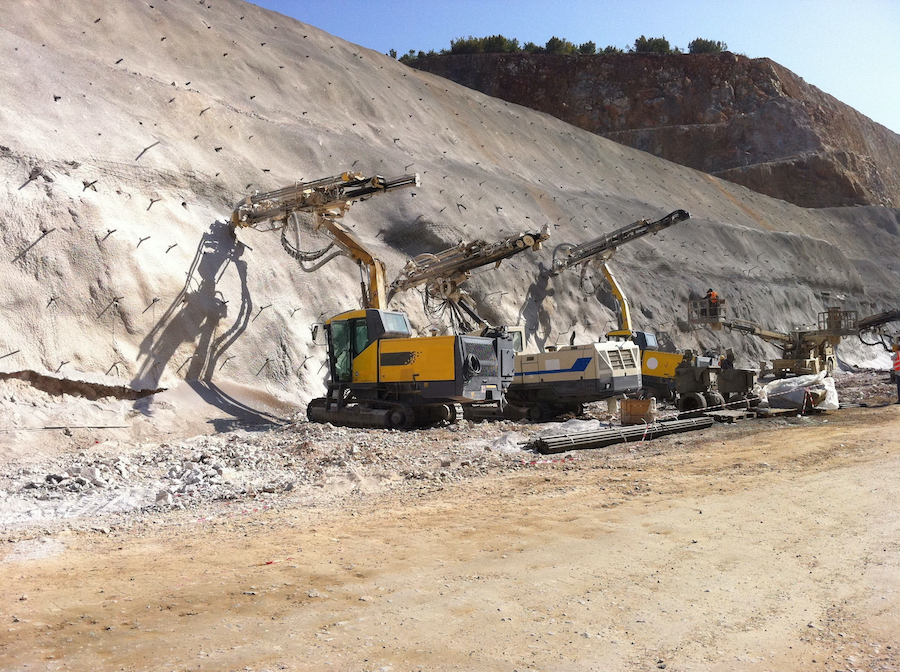
View the complete article here.
Poor risk management in geotechnical engineering projects has real-world consequences. It’s important to identify and manage risks in all aspects of a construction project. However, geotechnical engineering related to the foundation and support of a structure requires particular attention. Risk management planning for construction projects involving pile driving or foundation drilling is challenging because the soil underneath a worker’s feet can literally shift. In this article we discuss geotechnical engineering risk management in general and use examples in pile driving and foundation drilling to illustrate some key concepts.
Value of Risk Management
The value of risk management is not always appreciated by the whole project team. This, in and of itself, is a risk to manage. On some construction projects, geotechnical engineering risk management is either not implemented properly or plans are created and just filed away. A preliminary geotechnical investigation of the site will not likely detect rock or other obstructions three feet or more below the ground. It is not uncommon for cement piles to crack. However, preparing for these types of common risks is possible. Identifying and mitigating likely risks to save money, life, and limb is the value of risk management.
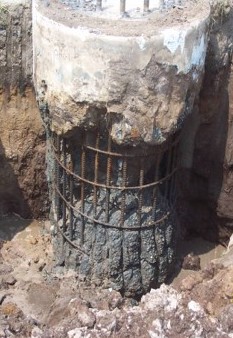
Project Size
Project size impacts the scope of risk management – not the need. For example, a foundation drilling project may involve only one structure such as building a small residential home in a flood zone. Geotechnical engineering is still involved and a risk management plan should be established. You will perform the same risk assessment and risk mitigation planning steps – on a smaller scale.
Audience-Appropriate
Your geotechnical engineering risk management report may have lots of pages and pretty charts, but the goal is to get team members to read it. In the same way most reports have an executive summary, you’ll want to tailor parts of the report to the various sub teams. This could be in the form of handouts and / or brief workshops to review the risks, communication, action, and safety plans that are within the purview of each sub team.
Key Geotechnical Engineering Risk Management Steps
Risk Identification
The geotechnical engineers and other subject matter experts develop a list of potential hazards. There are typical geotechnical engineering risks that can be used as a checklist to help guide the discussion of project risks.
Risk Assessment
Not every potential risk is likely to happen or may have little impact to the project cost or timeline if it does. In this step the geotechnical engineering team and subject matter experts determine the likelihood and impact of each risk.
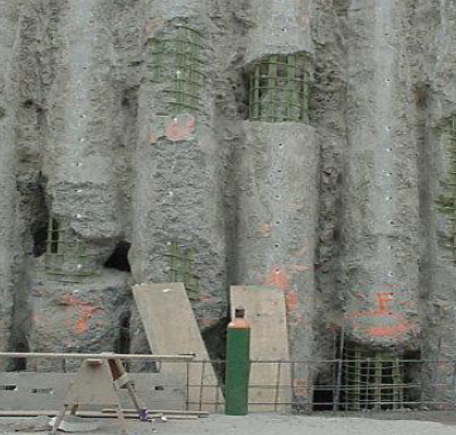
Risk Management
Risk management includes determining who is responsible for managing each risk and the action they should take. An obvious and sometimes overlooked aspect of risk management is communicating with the person or group you have assigned a risk to manage.
Risk Evaluation
A process by which the probability and impact of a risk are quantified. Decisions are based on the scoring of each risk. For example, some risks are so high that the project may not proceed. Or a risk may be so low that it will be monitored but have little no impact on the project budget, timeline, or safety.
Common Geotechnical Risks
There are common risks associated with certain geotechnical engineering projects. For example, a July 2010 document published by the Federation of Piling Specialists lists several risks related to pile driving projects including:
- Flighting of soils during pile installation can cause damage to surrounding structures.
- Working near a major highway can result in debris falling onto the roadway.
- Over reliance on pile end bearings in variable/layered rocks may cause excessive pile settlement.
Using existing hazards lists can save time in the risk identification process.
Quantifying Risk Impact
The impact of geotechnical engineering risks can be evaluated qualitatively or quantitatively. Risk evaluation early in project conception depends mostly on qualitative measures. There just isn’t enough data to determine the impact of a risk in terms of cost and time.
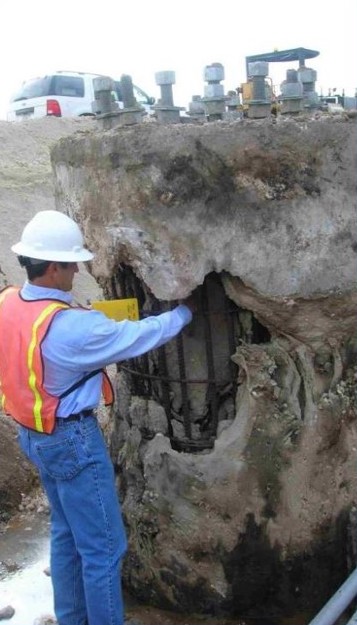
Qualitative
Qualitative risk impact evaluation is subjective. It depends on the assessment of experienced geotechnical engineers and subject matter experts. Risks are ranked generally as high, medium, or low in likelihood and impact based on the initial site investigation, historical data, and other preliminary information.
Quantitative
Quantitative risk impact assessment begins at the end of the preliminary engineering phase but prior to the start of the design phase. (As the risk assessment can influence design decisions.) Now there is enough data to estimate the cost associated with a risk’s impact. However, quantitative analysis is time-consuming and not necessary on smaller projects. An organization will determine, for example, that projects over some dollar amount should include a quantitative risk impact analysis.
Scoring
Each risk is given a probability and an impact score, typically a scale from 1 to 5 in the qualitative method and a percentage and dollar amount in quantitative method. A risk’s score is calculated by multiplying probability by impact. The final score categorizes the risk as low, medium, or high. Some project teams prefer a finer scale, such as very low, low, medium, high, and very high. In the final project plan, a risk register is used to track risks quantitatively assessed as high to very high.
Risk Management Response
When the risk identification process is completed, there are four options for handling each risk:
Avoid: Remove the risk by, for example, changing the design.
Transfer: Some risks can be reduced or eliminated by transferring the risk responsibility to another entity who can best handle it.
Mitigate: Reduce the likelihood that the risk will occur – or reduce the impact to a level that avoids project failure.
Accept: In some cases there is no choice but to accept the risk and develop a more robust contingency plan – and contingency budget.
Balancing Act
Often any risk management response increases either the direct budget or contingency budget. You can take the “it’s only a problem for the winner” approach. Estimate on the low side and deal with cost overruns later. Or the “better safe than sorry” approach that pads the budget so much that you price yourself out of the running. That’s where reviewing past projects can help you find a realistic middle road. You should have historical project data to help you better estimate future projects. The projects don’t have to match in every detail. A foundation drilling project for a skyscraper in the city can still inform your risk management planning for a small office building in the suburbs.
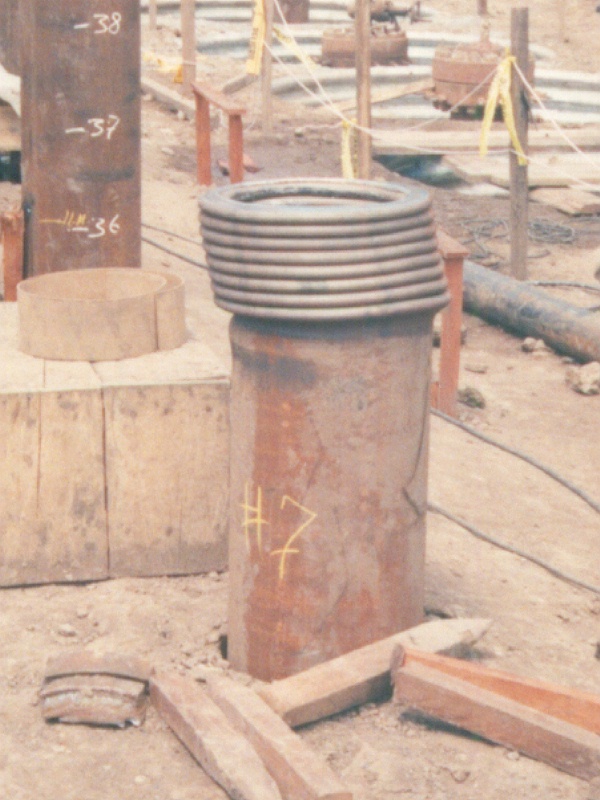
Geotechnical Engineering Project Documents
In a pile driving project, for example, much research and testing are completed before the first pile is driven. These geotechnical engineering project documents are a critical part of the risk management process.
Risk Management Integration
Geotechnical engineering risk management is only one part of the overall risk management plan. You will need to coordinate with those responsible for managing other project risks. An integrated risk management plan should be developed. Or at least touchpoints should be identified and coordinated. All or most geotechnical engineering risks identified will be retired from the risk register after the pile driving or foundation drilling phase of the project is complete. Time and dollar contingencies can be assigned to other project risks.
Communication
A geotechnical engineering project involves many stakeholders. Why, when, and how stakeholders communicate with each other is critical to the success of the project. Lack of communication is often the root cause of failure. Yet some projects lack a robust communication plan — if it’s discussed at all. Part of the risk management plan must include a review of the communication plan. The stakeholders — and the relationship between them — should first be identified.
- Stakeholder Identification. Includes information such as department or sub team, title, job description, and project activities, and name of person assigned. Remember to update personnel changes as sometimes employees leave or are transferred.
- Stakeholder Relationships. On large, complex projects, it is best to have a single point of contact (and back up contact) for each sub team.
- Stakeholder Communication Process. Determine in advance how and when stakeholders will communicate, including emergency procedures.
- Communication Risks. Historical project data can offer insight into past communication problems and how to mitigate them.
Post-Mortem
Most geotechnical engineering projects are ultimately successful. But all have challenges that were met and overcome. Performing a post-mortem review at the completion of every project can increase the likelihood of success for future geotechnical engineering projects. It can also lead to innovation as knowing how risks were handled or avoided may reveal opportunities for new products or processes. It is just as important to document what went well. In this way you will know which methods and processes should be continued.
Conclusion
Key project decisions are based on the geotechnical engineering risk management assessment. Risk mitigation can be handled in the pre-design phase to reduce costs and increase the likelihood the project will succeed on time and on budget. Working with and communicating risks to project stakeholders are important aspects of risk mitigation. Identifying and managing geotechnical engineering risks can literally save lives during construction.
View the complete article here.
Why is risk management crucial in geotechnical engineering projects, especially in foundation drilling and pile driving?
Effective risk management is vital to identify and address potential hazards, ensuring the safety, budget, and timely completion of geotechnical engineering projects, particularly those involving foundation drilling and pile driving.
How can geotechnical engineers assess and manage risks during a project, and what are the key steps involved in the process?
Geotechnical engineers follow key steps, including risk identification, assessment, management, evaluation, and response, using qualitative and quantitative measures to ensure a comprehensive risk management plan for construction projects.