ShibataFenderTeam Delivers Four Parallel Motion Fenders for the Refurbishment of Thunderer Jetty, UK
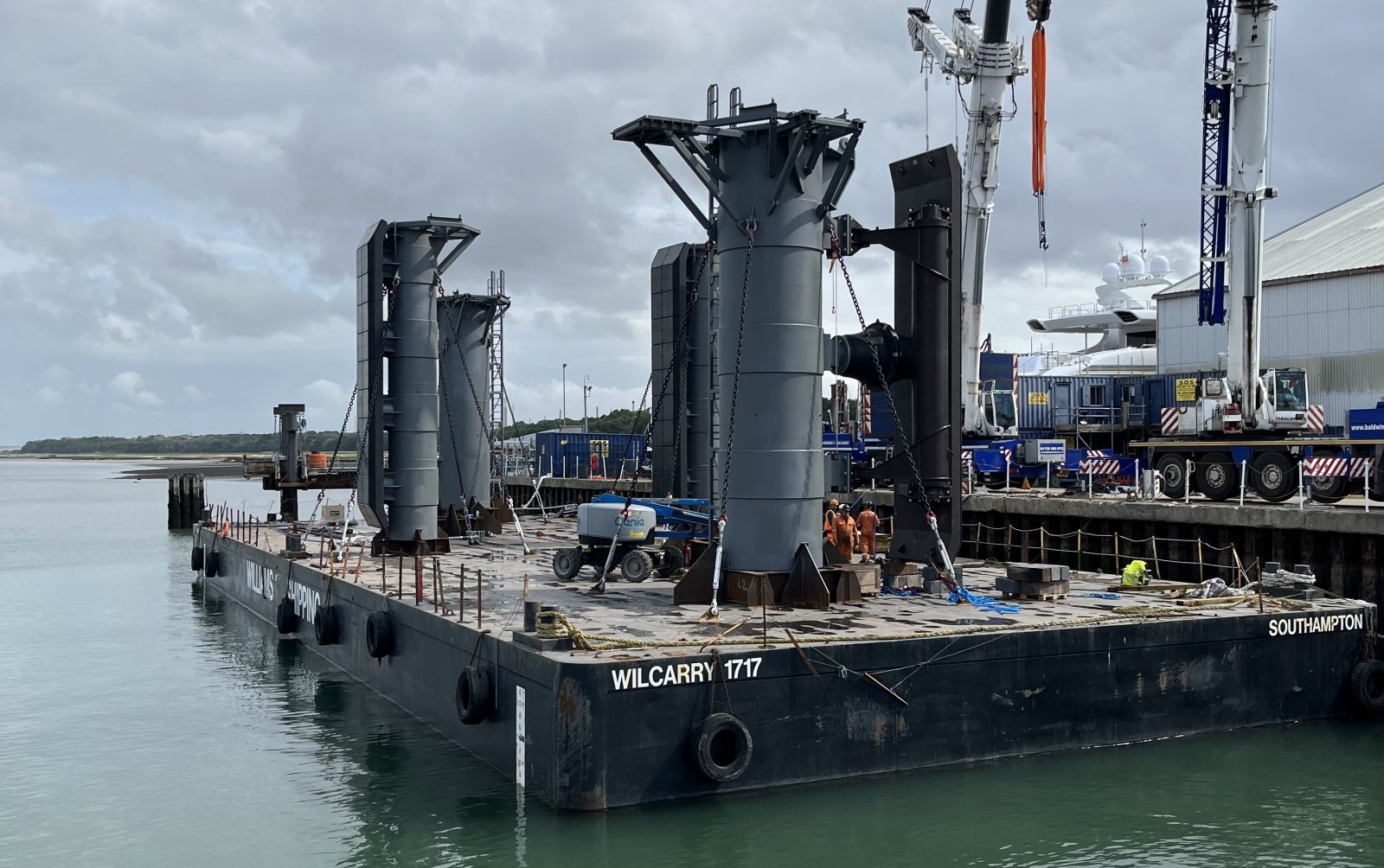
Originally built in the early 1900s, Thunderer Jetty is located on the banks of the Thames in Dagenham,East London, an area with long-established historic industrial character. After years of minor renovations, it is now undergoing a complete refurbishment of the existing berth structure, including the construction of a replacement jetty approach, breasting dolphins, mooring dolphins and a new loading platform.
Due to the structure’s nature and the variety of vessel sizes berthing at the jetty, the consulting company responsible for the design of the project was seeking a solution that would result in very low hull pressures and avoid any possible double-point contacts with the vessel. Working in close collaboration with them, SFT’s in-house engineering team wisely advised selecting PMF fenders, a proposal that was eventually adopted for the final design.
SFT delivered 4 sets of Parallel Motion Fenders, each of them consisting of two cone fenders SPC 1100 mounted back-to-back in order to allow for twice the energy absorption and large closed box steel panels (2250 x 9930 mm). The project scope also included two more Fender Panels (2100 x 9930 mm) and eight sets of Bollards with various capacities.
The installation of the solution posed a twofold challenge. Firstly, there was the need to execute the works in various phases, while ensuring the terminal remained operational throughout the project. Secondly, there was the complexity of working with these large PMFs. For the former, the SFT sales and logistics teams worked thoroughly to meet the demanding schedule; for the latter, the contractor decided to assemble and install the fenders onto the dolphin’ heads at a steel construction facility in the South of England and ship them out from there to the job site along the river.
This refurbishment project at Thunderer Jetty – used for storage services for fuel, biobased feedstock, and renewables – has extended the facility’s lifespan by an additional 40 years and upgraded it to meet the latest safety and environmental standards. We at the SFT Group are proud to have contributed to both goals.