Pile Driving Equipment Selection and Penetration Limitations
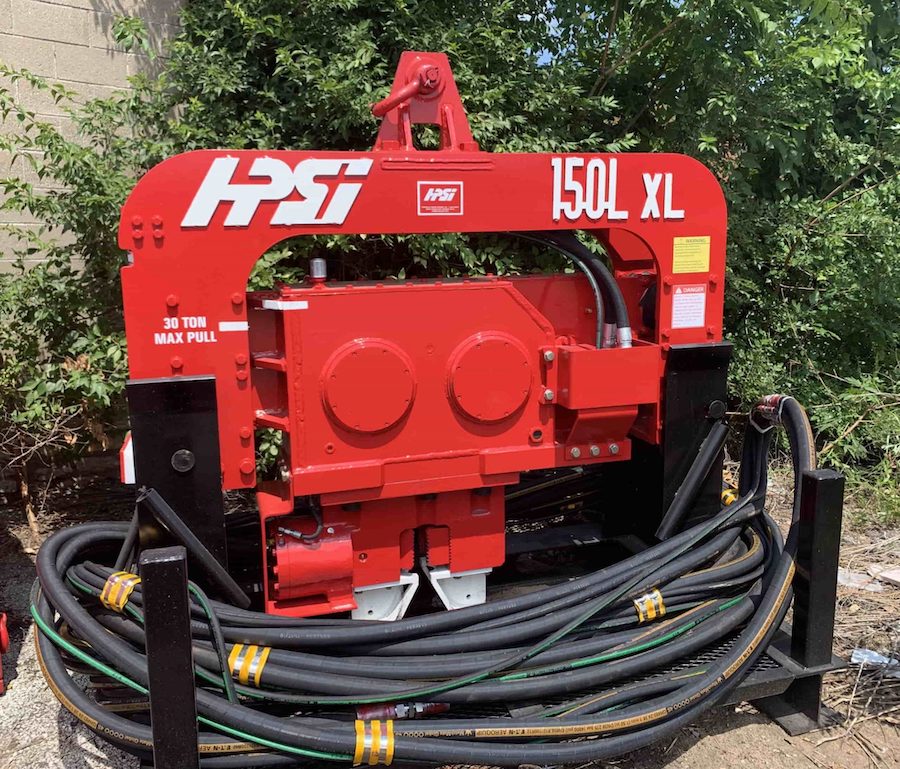
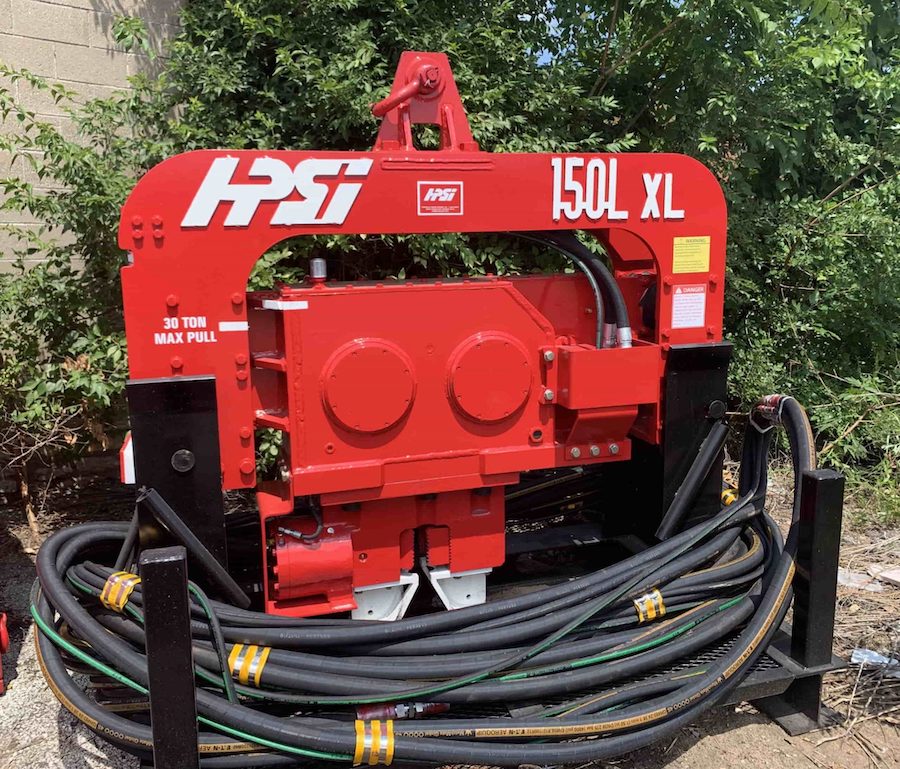
View the complete article here.
The Evolution of Pile Driving Equipment
Pile driving equipment has evolved significantly over the years—from simple hand-held hammers—to modern hydraulic and vibratory hammers that are capable of driving piles faster, deeper, and more efficiently.
Some of the key developments include…
Early pile driving involved manual labor and hand-held hammers, which were used to drive wooden piles into the ground.
In the late 1800s, steam-powered hammers were developed that used steam pressure to drive the pile.
In the early 1900s, diesel-powered hammers were developed—which provided greater driving force and improved efficiency.
In the 1950s, hydraulic hammers were introduced—which use hydraulic pressure to drive the pile and can be more precise and efficient than earlier hammer types.
In the 1960s, vibratory hammers were developed. Using a vibratory action to drive the pile into the ground, vibratory hammers can be especially useful in soils that have a high resistance to driving, or in situations where noise and vibration levels need to be minimized.
In recent years, computerized control systems—such as pile driving analyzers—have been developed that allow for greater precision and control over the driving process, as well as real-time monitoring and data collection.
Overview of the Driving System
A pile driving system is defined as a set of equipment and components that are used to install piles into the ground to support structures or other loads.
The typical pile driving system consists of the following:
- The pile: The structural element that is driven into the ground to support a load.
- Hammer: The device that delivers an impact to the pile to drive it into the ground.
- Leads: A framework or guide system that is used to position and guide the hammer and pile during driving.
- Cushion: A protective object that is placed between the hammer and the pile to help protect both from damage during driving.
- Helmet: A steel cap or shoe that is attached to the pile to help distribute the impact forces of the hammer during driving.
- Power source: A source of power—such as a diesel engine or compressor—that is used to operate the hammer.
- Control system: A system of valves and controls that is used to regulate the flow of power and control the operation of the hammer.
- Monitoring equipment: Sensors and instruments that are used to monitor and measure the driving process—such as pile penetration, blow count, and vibration levels.
- Rigging and lifting equipment: Equipment used to position, lift, and move the pile and hammer—such as cranes, winches, and hoists.
- Personal protective equipment (PPE): Safety equipment—such as hard hats, earplugs, and safety glasses—that is worn by workers to protect them from potential hazards during the driving process.
It’s important to note that all of these components of the driving system have an effect on the performance of the hammer and how the hammer transfers its energy to a pile.
Pile Hammer Selection
When selecting a pile hammer, the following must be considered…
The pile type and properties of the pile being driven—such as material, shape, size, and length. For example, steel piles may require a different type of hammer than concrete piles due to their different properties and behavior during driving.
Soil conditions. The soil type, density, and other properties at the site where the pile is being driven. For example, if the soil at the site is hard and dense, it may require a pile hammer with a higher driving force to achieve the desired pile penetration rate. In contrast, if the soil is loose or soft, a hammer with a lower driving force may be more appropriate to avoid damaging the pile or the surrounding soil.
The driving method being used—such as impact, vibratory, or press-in. For example, if the site is in an urban area where minimizing noise and vibrations is a priority, a vibratory hammer may be used for pile driving—as it generates less noise and vibrations than an impact hammer.
The required driving force refers to the amount of energy needed to drive the pile to the desired depth and achieve the necessary bearing capacity. This can be influenced by a variety of factors—such as the soil conditions, pile properties, and the desired pile capacity—and can differ significantly depending on the specific project requirements.
Energy efficiency—or the efficiency of the hammer in terms of energy consumption and output. For example—in most cases—a hydraulic hammer may be more energy efficient than a diesel hammer, as it uses hydraulic pressure to deliver energy to the pile, rather than relying on combustion.
Access and mobility. The ease of transportation, setup, and operation of the hammer at the site—including factors such as size, weight, and power requirements. For example—if the site is located in a remote or inaccessible area—a smaller, more compact hammer may be used. In contrast—if the site is easily accessible—a larger hammer may be used, which can achieve higher driving forces and possible greater efficiency.
The level of noise and vibration generated by the hammer during driving, and whether it meets regulatory requirements or project specifications. Factors such as hammer type, driving method, and soil conditions can impact the level of noise and vibration generated.
Cost and availability. Of course—the cost of the hammer, availability of spare parts and service, and other factors related to procurement and maintenance should all be considered. For example—if the project is on a tight budget, a used or rental hammer may be a more cost-effective option than purchasing a new hammer.
All of these factors should be carefully considered during hammer selection. This is just a simple list, with minimal information. You can find more detailed information at the Pile Buck store.
Penetration Limitations
In order to monitor the pile driving process and ensure that the pile is driven to the appropriate depth and capacity, the rate of penetration—defined as the number of blows delivered by the hammer per unit length of pile penetration—is a crucial element that cannot be overlooked.
During pile driving, blow counts are recorded in the field on a per-foot basis until the pile approaches a designated tip elevation or the end of driving. At that point, the blow count is typically recorded for each inch of penetration. This information is then used to determine the relative capacity attained during driving and to prevent overdriving, which can cause structural damage to the pile. Overdriving occurs when the pile is driven too far into the ground, resulting in permanent deformation or damage to the pile structure.
Limiting penetration rates are specified to prevent overdriving and provide guidance for determining the relative capacity attained during driving. These rates are the maximum allowable number of blows per unit length of pile penetration. Limiting penetration rates may be impacted by the type and properties of the pile, soil conditions, and the driving method being used.
Pile tip damage due to very difficult driving—commonly referred to as refusal—can occur when the pile encounters an obstruction or a hard bearing stratum prior to reaching the indicated tip elevation. Keep in mind that damage like this may not be easily detectable—so it is essential to specify the criteria needed to determine limiting rates to prevent overdriving and maintain the pile’s structural integrity.
View the complete article here.
What factors should be considered in pile driving equipment selection?
In pile driving equipment selection, factors to consider include soil conditions, pile type and material, required penetration depth, load-bearing capacity, and accessibility of the site. Selecting the right equipment ensures efficient pile installation and long-term stability of the foundation.
What are the penetration limitations in pile driving?
Penetration limitations in pile driving are influenced by factors such as soil conditions, pile material and size, and the driving system used. Issues like denser soil layers, high pore water pressure, and soil plug formation can limit penetration, making it difficult to reach the desired depth or load-bearing capacity.