Drilling in and Near Embankment Dams and Foundations – Part II
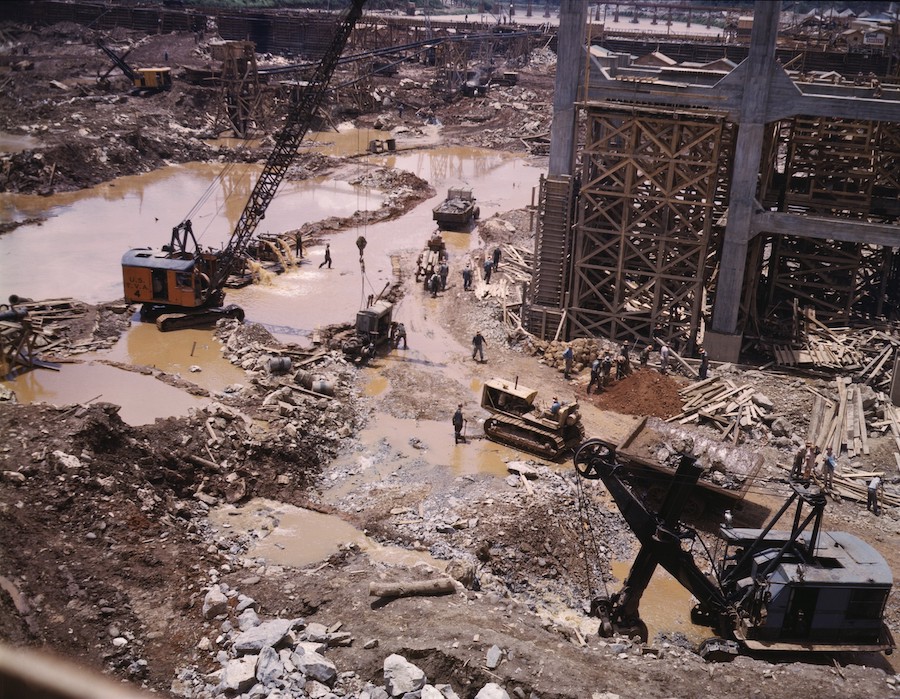
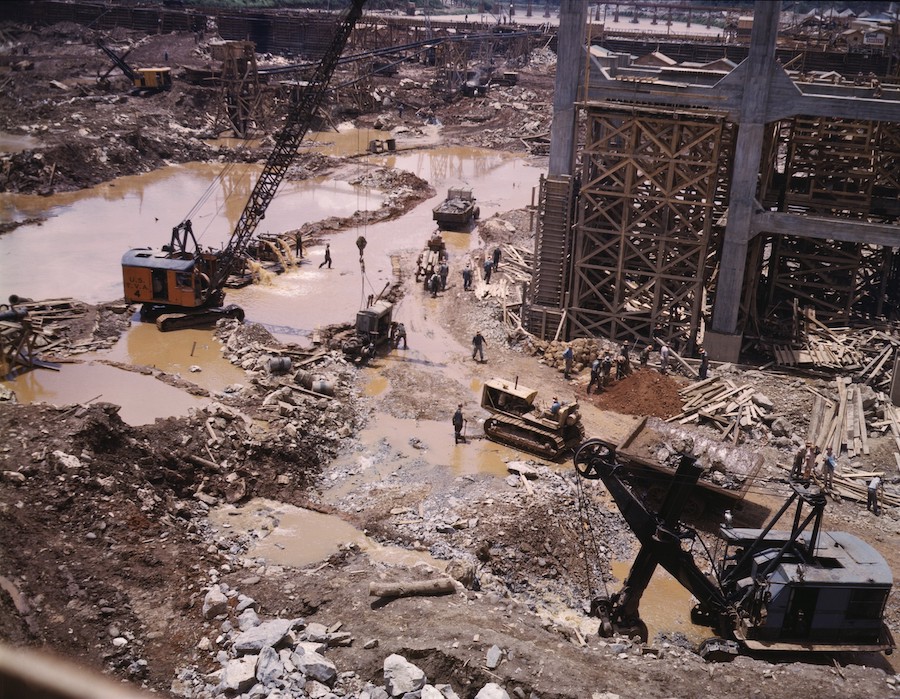
View the complete article here.
Part 1 of this article series covered important information about how to prevent damage to embankments, foundations, and structures when drilling in the area. In Part 2 of this series, we are taking a closer look at additional steps that should be considered for the safety and efficacy of the project – including topics such as hole completion, the selection of drilling personnel, and other considerations for drilling. This information is sourced from the FERC drilling guidelines handbook.
In-Situ Testing and Sampling
While the actual advancement of the boring is the most common hazard that causes hydraulic fracturing, other supporting activities can also have an impact on the disturbance or performance of the structure. When the drill rods, casing, or drill steel are raised or lowered too quickly, then it can affect either positive or negative fluid pressures.
If hydraulic pressures are applied through a static head or pressure-induced head for in-situ testing, it could possibly cause excessive hydraulic pressures that cause hydraulic fracturing. These testing and sampling methods can be an important part of the project, but it is essential to evaluate the potential risk. Consider using the Engineering Geology Field Manual published by the Bureau of Reclamations as a reference to determine the right hydraulic fluid pressures that should be used.
Hole Completion
When the project comes to completion, all penetrations and boreholes need to be sealed. It’s not acceptable to simply backfill the hole with the drill cuttings. Specific methods need to be followed to ensure the structure of the embankment or foundation in the future.
If the penetrations occurred in the impervious portions of the foundation and embankment dam, then the backfill should be completed using tremie-placed cement-bentonite grout. An alternative method is to use bentonite chips or pellets, but only by approval based on the project. The grout used needs to have strength greater than or equal to the rock or soil. Also, it is important to consider groundwater aquifers to prevent leakage and cross-contamination. Boreholes should be backfilled using gravity grouting techniques.
In zones with low confining stress, boring penetration could induce hydraulic fracturing due to gravity pressure alone. When these borings are grouted, then measures need to be taken to grout backfill in all stages to allow time for the grout to set between stages.
Regarding pervious portions of the dam (such as filters, drainage features, etc.), a tremie placement of granular materials should be used for backfill in the borehole. These materials need to be sized to allow drainage, while reducing the risk of migration through the foundation materials or previous embankment.
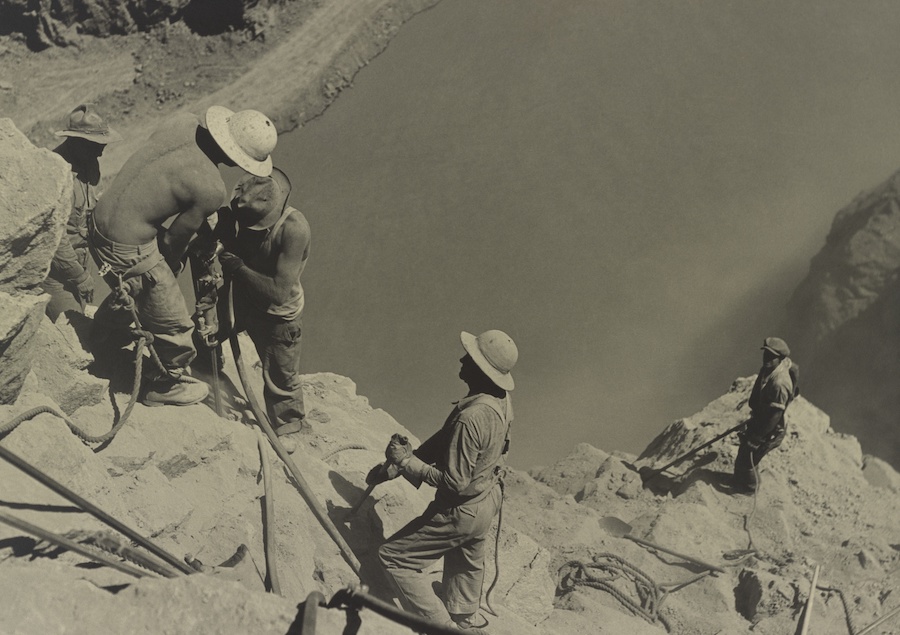
Photo credit: Everett Historical
General Guidelines for Borehole Completion
There isn’t much documentation for borehole completion. But you can follow general recommendations and guidelines to determine the intervals that should be used for backfilling material and the volume of materials needed. Pay attention to how the calculated volume of material compares to the volumes actually used. If the material volumes are significantly lower or higher than the calculations, then it could be an indication of a change in conditions.
Follow these general guidelines for borehole completion:
- High Solids Bentonite Grout: One acceptable method for embankment dam borehole completion is to use tremie grouting with high solids bentonite. The mix should yield between 20 to 30% solids. The casing should be pulled incrementally and correspond with stage up tremie grouting methods to ensure the stability of the hole wall. The best possible placement can be achieved by injecting the bentonite slurry through a tremie pipe.
- Neat Cement Grout: The best results with this method involve a mix created using 5 to 7 gallons of water for every 94 lb. sack of cement (Type I or Type II Portland). If high water content is used, it can result in excessive cracking, shrinkage, and bleed water. Other compounds, such as powdered bentonite, can be used to improve pumping ease and reduce cracking and shrinkage. Carboxylic acid and calcium chloride can be used to manage set times, but don’t overlook how these additives impact shrinkage factor. Just like the bentonite grout listed above, the same method should be used to pull the casing incrementally, with the grout injected through a tremie pipe.
- Bentonite Chips or Pellets: This method can be acceptable, but certain conditions need to be met for it to have a favorable outcome. If there is a chance that the water in the hole could slow the bentonite fall, then chips or pellets shouldn’t be used. Even if the hole is dry, there must be enough annular space, so the bentonite can fall to the bottom of the borehole without the risk of bridging. Both solid bentonite and grout should always be placed through a tremie pipe.
- Instrument Installations: Special completions are required, depending on the instruments being placed. Piezometers require the placement of sand packs in the influence zone, followed by a bentonite seal (often consisting of bentonite pellets) above the sand pack. This method prevents the contamination of the sand pack from the sealing materials. When the seal is placed, sufficient time is required to allow it to hydrate – usually 1 to 2 hours. Another option is to install piezometers in fully-grouted holes. In this case, it is recommended to only place 1 piezometer in a hollow stem auger (4-inches), with a maximum of 2 instruments in a single boring. Additional considerations are required for the placement of other instruments, such as geophysical casing, slope inclinometer casing, etc.
Selection of Drilling Personnel
Due to the risk associated with dam drilling, it is essential that these tasks are only performed by qualified and experienced personnel. The most important positions to pay attention to include the lead drill rig operator, as well as the geologist or engineer holding the responsibility as the on-site representative for overseeing the safety of the dam throughout the drilling program. All drilling activities should only be conducted with a qualified engineering geologist or geotechnical engineer there to oversee the operations. This qualification must include a combination of training, education and experience, based on the hazard level of the dam.
Drill rig operators should have at least 5 years of experience using the equipment, as described in the drilling program. If the drilling plan requires specific drilling techniques, such as drilling in the vicinity of the dam or within an embankment dam (among others), the operators should have demonstrated experience with embankment dam drilling.
The integrity of the structure and safety of those involved always take priority over secondary issues such as budget and schedule. If structure or safety is at risk, then the necessary means should be implemented to remediate the problem.
Other Considerations for Dam Drilling
Here are a few other considerations that need to be addressed for every project:
- Emergency Communications: A thorough review of the Emergency Action Plan (EAP) must occur before the dam is investigated or drilled, as determined for FERC-regulated dams. This EAP includes contact information for the key individuals who need to be informed of the proposed activities.
- Monitoring: Continuous inspection and monitoring should occur through all drilling operations, appropriate to the instrumentation and procedures of the dam site. This monitoring needs to evaluate the potential impact of drilling activity, as well as the detection of unanticipated changes that might occur in process.
- Reporting: Potential damage or real damage related to drilling and the associated activities must always be reported. In the incident that there is a sudden loss of drill media, drilling should stop immediately to stop the loss of drill fluid. The reason for the loss needs to be determined. The FERC should be notified immediately if it is identified that hydraulic fracturing occurred.
- Remediation/Construction Drilling Activities: Drilling activities performed during remediation or construction phases shouldn’t be overlooked. There are many situations where the dam required remediation after the filling of the reservoir, due to damage that occurred to the foundation or embankment. If there is a concern, then the drilling methods need to be reviewed by a team formed for this purpose.
- Exemptions: Certain situations may be exempted from the standard requirements to prepare a drilling plan. For example, if drilling is needed for immediate emergency measures, then there might not be enough time to obtain the acceptances and reviews or design the drilling plans. While emergency drilling can be expedited, it should always follow the guidelines listed.
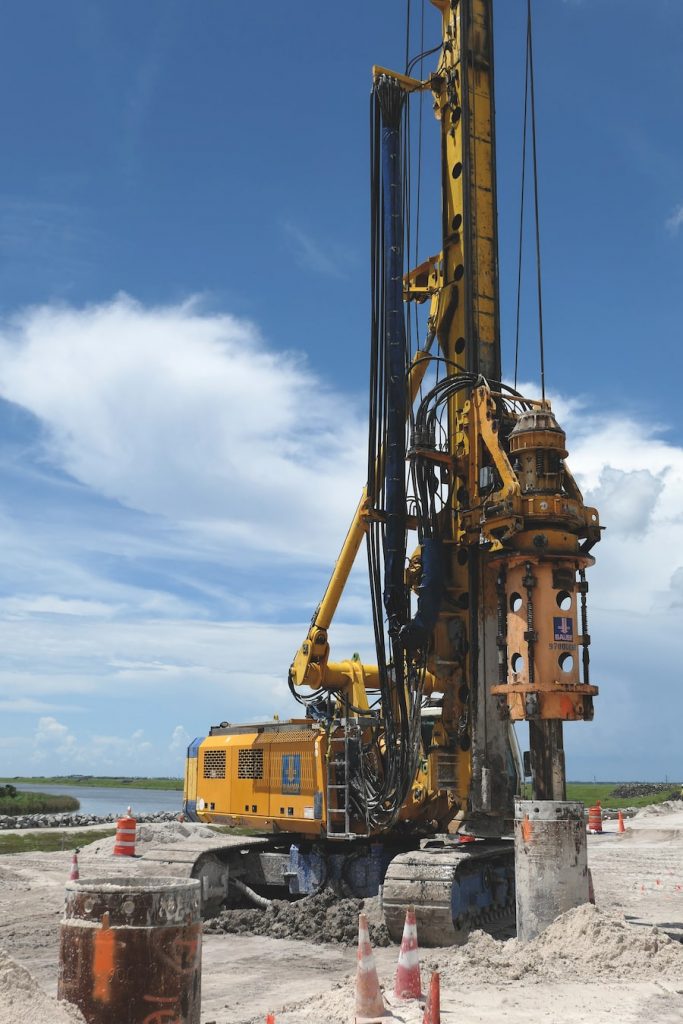
Evaluating Potential Risks
The proposed drilling needs to be evaluated to determine potential risks of the project, as well as the intended efforts to mitigate these risks. A variety of topics should be discussed, including the possibility of:
- Hydraulic fracturing of the embankment
- Seepage
- Instability
- Other potential dam safety issues
This risk evaluation must encompass the way drilling operations could potentially impact the dam, as well as the boreholes locations in relation to high-risk areas of the dam that are susceptible to hydraulic fracturing. A thorough evaluation of potential risks reduces the likelihood of encountering problems when drilling activities are occurring.
Other evaluations should be done regarding soil type, borehole completion, borehole abandonment, instrumentation installation, and emergency procedures. Focused attention needs to be placed on contingency plans and procedures that will be implemented to protect the dam from potential risks, including hydraulic fracturing.
Designing a Drilling Program Plan (DPP)
Every project that involves exploration drilling, remediation drilling, or instrument installation on or in proximity to an embankment plan must have an approved Drilling Program Plan (DPP). Experienced geotechnical engineers and/or engineering geologists should be involved in the preparation and review of the DPPs. These team members need to be familiar with subsurface exploration methods and techniques.
All subsurface information needs to be thoroughly understood and evaluated before a plan is developed for additional drilling. Existing subsurface information should be incorporated into essential section drawings and plans, outlining the proposed holes, depths, instrumentation, and target sample areas.
Additionally, the DPP needs to comply with site environmental restrictions and provisions, as well as good environmental practices. Sometimes, this process requires coordination with other outside agencies and DHAC.
Then, the FERC Regional Engineer must review and accept the DPP before the drilling begins. This review process may require extra coordination with other FERC staff, including the headquarters in Washington D.C. For the best results, the plan should be submitted at least 30 days before the target drilling date.
DPP requirement and guideline instructions can be obtained in full, but should always include:
- Name and description of the project.
- Purpose of the activity.
- Description of the proposed activity including location, depths, sampling intervals, testing, and instrument installation.
- Description of anticipated site conditions.
- Proposed methods, equipment, and processes.
- Identification of project personnel, as well as their resumes and details about experience and qualifications.
- Risk identification and mitigation plan.
- Communication plan, including names and phone numbers of key individuals.
- Overall schedule for the duration of activities.
Other reporting requirements to list in the DPP include logging, documentation, and the submission of applicable drilling data. Within 24 hours after the boring is backfilled, the field inspector’s boring log must be submitted to the FERC. Daily work logs and draft field boring logs should be submitted daily when reasonable.
The possibility is always present that changes will need to be made in the field as certain conditions are encountered. The DPP needs to outline how the deviations and changes will be coordinated and communicated with the DPP. If there are significant differences from the anticipated conditions, then it could be an indication of the possibility of a serious dam safety issue – and should be reported immediately.
View the complete article here.
Why is it important to consider proper hole completion at the end of project?
It is important to avoid any potential hazard or failure caused by improper completion of the borehole. Improper borehole completion leads to hydraulic fracture and total failure of nearby structures. Specific methods like tremie-place cement-bentonite grout, Bentonite chips, or Pellets should be used to backfill the hole.
What is a Drilling Program Plan (DPP)?
For any large and successful drilling operations, Top executives and engineers need to finalize Drilling Program Plan (DPP). It should include all subsurface information, drawing details, the outline of proposed drilling information/techniques, tool management, borehole location/details, and a sample/completion report. DPP serves as great tool for future and current project requirements and in case of discrepancies.