Drilled Shaft Foundation Safety: The Aldridge Story of Success
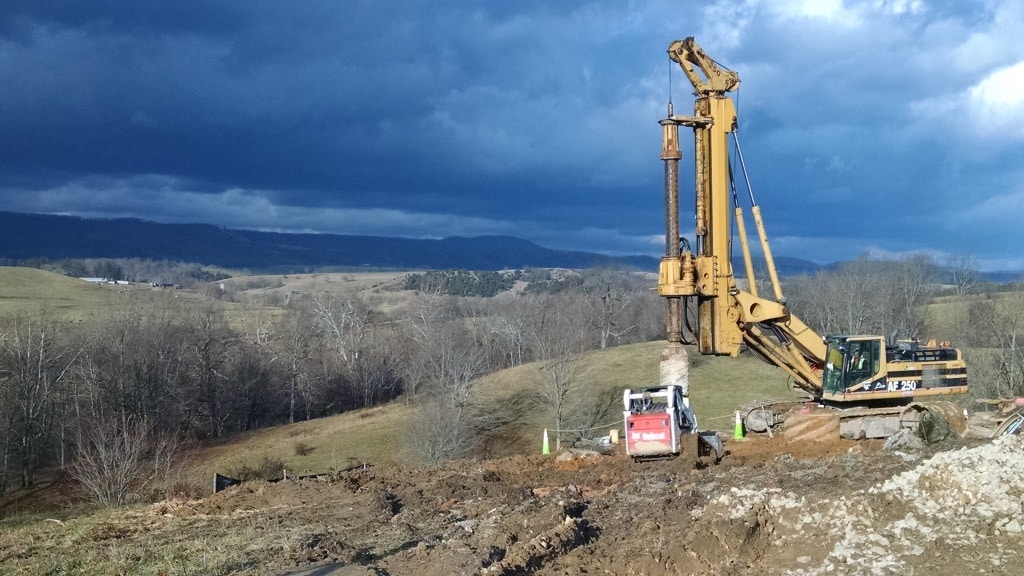
According to the Bureau of Labor Statistics, between 4,500 and 5,000 fatal injuries occur each year in the workplace; with approximately 20 percent of those fatal injuries occurring in the construction industry. By investigating these fatal injuries, the Occupational Safety and Health Administration (OSHA) has identified falls, being struck by heavy construction equipment, and electrocutions as the hazards that are most likely to contribute to workplace fatalities in construction industry. In the area of drilled shaft foundation construction, these hazards are present each and every day.
It could be argued that drilled shaft foundation construction is one of the most hazardous types of construction work performed. For any company to succeed in safely performing this type of work, two things must exist. One: the company must be committed to safety; and two: the company must have a comprehensive and progressive safety and health program. In the field of drilled shaft foundation safety, there is one company continually recognized as a leader – Aldridge.
Aldridge can attribute much of its success in foundation safety to the following elements:
- Pre-task hazard analysis program
- Site ownership
- Safety Absolutes
- Enforcement
- Training
Pre Task Hazardous Analysis Program
Before any worksite task can begin, a thorough pre-task hazard analysis must be performed. It is the policy of Aldridge that the pre-task hazard analysis, known as the Daily Task Analysis (DTA), be performed, documented on paper, reviewed with, and signed by, all crew members involved in the task. The DTA verifies that all crew members have been made aware of the task to be performed and the hazards associated with the task. Further, if additional personnel, such as managers, inspectors, visitors, material delivery, etc. must enter the worksite, an Aldridge crew member at the worksite will ensure the DTA has been reviewed with, and signed by, all personnel prior to entering. The review and signature of the DTA by all personnel prior to entering the worksite are vital for site control, and more importantly: Site Ownership.
Site Ownership
Site ownership is an important aspect of the Aldridge safety and health program as it is necessary for federal (OSHA) and legal (civil) liability. Beyond the legal aspects however, Aldridge has found that site ownership encourages crew members to accept responsibility for their actions and empowers them to act on that ownership to ensure that they and/or their co-workers are not put at additional risk while performing their tasks.
The Safety Absolutes (as listed below) are safe work policies and practices that are of the highest priority at Aldridge. They are selected for focus because serious physical harm, even death, is a likely outcome when these policies and practices are violated.
“Everyone at Aldridge has a duty to themselves and to their co-workers to be constantly aware of potentially hazardous conditions. When hazardous conditions are noted, proper action must be taken to eliminate the hazard.”
- Fall Protection
- Excavation Safety
- Confined Space
- Energized Electrical Hazard
- Willful or Repeated Violations
In addition:
When employees knowingly commit violations of Aldridge safe work policies, practices, and procedures, these employees not only put themselves at risk for injury, they also put their coworkers at the same level of risk for injury.
It is for this reason that “Willful and Repeated Violation” was added as fifth Safety Absolutes. Creation of the Safety Absolutes and its ensuing campaign was designed to keep a constant focus on these critical safety elements. As part of the campaign, a Safety Absolutes handbook containing the Aldridge policies and work practices on each of the Safety Absolutes was created and provided to every employee. Also; in an effort to maintain the focus, a review of one of the elements of the Safety Absolutes is performed by all crews once a month.
Enforcement
As with any successful safety and health program, accountability through enforcement is critical to its success. For example: If a Safety Absolutes violation is observed during work activities, or is determined to have occurred as a result of an incident investigation, details of the Safety Absolutes violation is immediately sent to the Aldridge Director of Safety for review. The Director of Safety will then forward the violation to the Safety Absolutes Review Committee for further evaluation.
The Safety Absolutes Review Committee is committed to creating an incident and injury free workplace to bring attention to company policy and to foster learning and improvement. However, when deemed necessary, violations evaluated by the Safety Absolutes Review Committee may include disciplinary actions up to and including termination. Based on the circumstances of the violation, an employee’s immediate supervisor may also decide to impose disciplinary actions for a Safety Absolutes violation.
Training
A safety and health program cannot be successful unless the workers for which it is intended to protect are trained in the elements of the program. At Aldridge, training is achieved in three ways; new hire orientation; Green Hardhat Program; and formal training.
Every new employee to Aldridge receives new hire orientation prior to his or her initial job assignment. The new hire orientation, conducted on the first day of employment, not only provides the employee with a thorough explanation of the safety and health program, but also prepares the employee with the ability to recognize, and safely avoid worksite hazards associated with tasks to be performed.
New hire orientation is also designed to strongly emphasize emergency response, incident reporting, the importance of the Daily Task Analysis (DTA), and the Aldridge commitment to maintaining an Incident and Injury Free (IIF) culture.
New hire orientation also includes a review of, and enrollment in, the Aldridge Green Hard Hat Program.
Upon completion of the new hire orientation, the employee is issued a green hard hat and is enrolled in the Aldridge training program known as the Green Hard Hat Program.
Wearing the green hard hat designates the employee as an employee in training, and enrollment in the Green Hard Hat Program will ensure the employee receives the necessary training, and develops the necessary skills, to be a safe and productive worker in drilled shaft foundation work.