Construction Site Dewatering: Techniques and Solutions
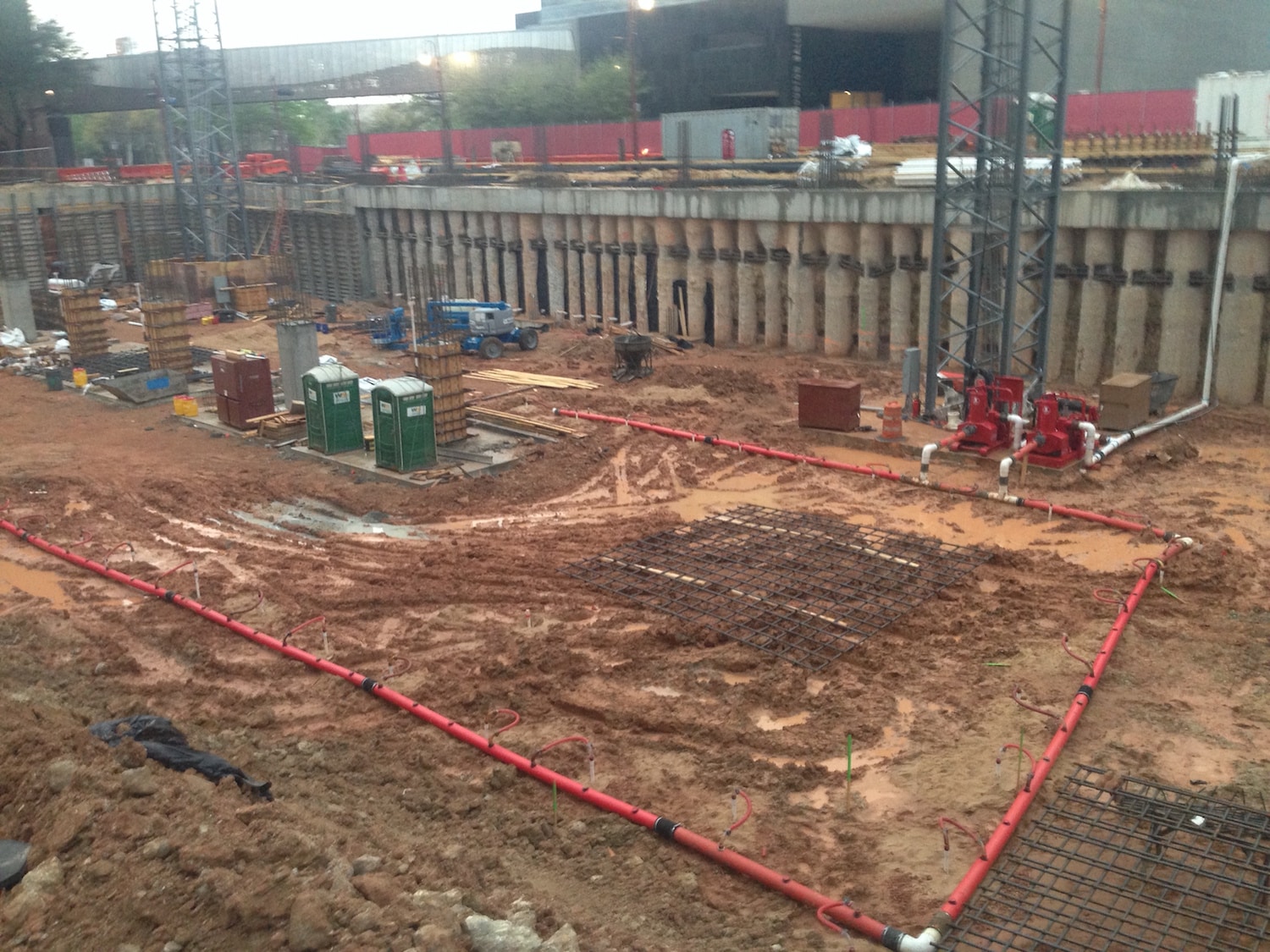
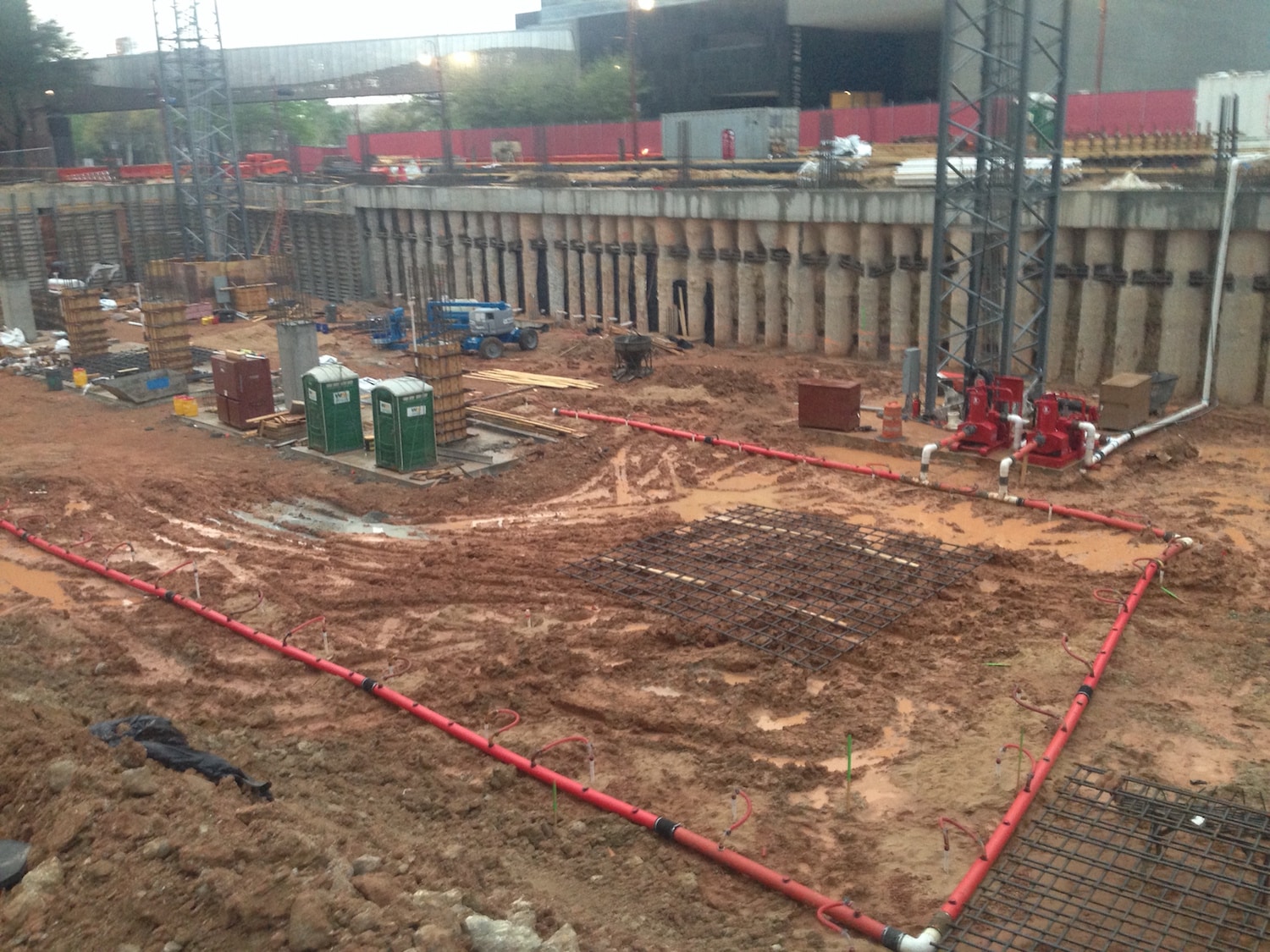
Lyric Center Garage Addition, Houston, TX
Wellpoint Dewatering System
General Contractor: Gilbane Building Company
2016-2017 Dewatering was completed and system was removed
It is not uncommon for water to accumulate at construction sites, whether from preoccupation or non-storm water. In order to begin construction operations, it is generally necessary to remove this water in a process known as dewatering. In general, dewatering is a multi-step process involving storing water, pumping the water, treating it, and discharging it that may require the provision of permits, depending on your state. Construction dewatering is typically done before excavation, and is often necessary in order to keep a project on schedule and to maintain a safe workplace. Dewatering will also prevent leakage of water and sand and help to avoid upheaval failure. Proper dewatering is necessary to avoid erosion or other hazards.
While construction site dewatering can be both timely and expensive, it is often necessary on construction sites to reduce or remove groundwater. This article will discuss various techniques and solutions for construction site dewatering. Where permits are mentioned, they will be specific to the state of California; however, you should check with your local authority before beginning any dewatering operations to ensure that you are in full compliance with all applicable rules and regulations.
The Regulation of Dewatering Operations
Dewatering operations are regulated by federal and state law. Federal regulations, including those issued by the Environmental Protection Agency (EPA), require that contractors that plan to discharge construction site water or stormwater to obtain a National Pollutant Discharge Elimination System (NPDES) permit. In most states, including California, the EPA has delegated the authority for issuing these permits to the state. In California, as in many other states, there are additional requirements for obtaining permits to discharge construction site waters. This is due to how California defines waters subject to its jurisdiction; while the EPA only regulates “Waters of the United States,” California regulates discharges to both surface waters and groundwater, which means that discharges of water onto land are also regulated. While each state’s permitting system varies, contractors will likely find that their state also regulates the discharge of construction site water and stormwater onto land as well as into water.
The reason that the dewatering process is so heavily regulated by both the federal and state government is simple: untreated water removed from construction sites during dewatering operations may contain certain pollutants that could negatively impact local natural water courses or storm drainage systems. Federal and state regulations are in place to prevent this from occurring.
There are a number of potential pollutants that are potentially present in construction site water, as defined by the Clean Water Act and the Porter-Cologne Act. For purposes of construction site dewatering, these pollutants fall into three main categories: sediments, pH, and other pollutants. Sediments are a common pollutant found on construction sites, and are often visible in the water itself. Sediment concentration in water is generally monitored as turbidity, total suspended solids, or suspended sediment concentration. The removal of sediments is generally required for most dewatering operations. Similarly, pH — the acid level of the water — is also typically monitored in dewatering operations. High pH readings are typically a result of concrete or grouting operations near a dewatering operation. Unlike sediment, pH is not a visible pollutant. Other pollutants may include a wide range of items based on the use of the construction site of adjacent land, such as nitrogen and phosphate from fertilizers, oil, grease, solvents, copper, lead, concrete sealants, welding waste and blasting grit. Depending on the type of contaminant, other pollutants may or may not be visible.
Regardless of the type of pollutant in the water, if water on a construction site contains a pollutant, then discharge of the non-storm water can only occur after testing shows that either the pollutant was either not detected or it was detected below a certain trigger value. This type of testing is typically done at certified laboratories.
Typically, discharge of stormwater — accumulated precipitation — is less heavily regulated than the discharge of non-storm water, such as water used during construction activities. The permitting process for the discharge of non-storm water will depend on the type of water at issue and whether or not it contains a contaminant, as discussed above.
There are a variety of options for dewatering a construction site, based on factors such as the type of water present, the presence of pollutants in the water, the volume of water, and the general conditions of the construction site itself. Understanding the process of dewatering is critical to choosing the appropriate option, which may include managing collected water within the site itself, discharging water to adjacent land by agreement, use of water at a facility owned by others, discharge or water to a storm drainage system, or discharge or water to a sanitary sewer system. Determining which dewatering process is correct for a particular construction site requires careful consideration of a number of elements.
Step 1: Assessing Water Quality and Determining Discharge Parameters
The first and perhaps most important step in the construction site dewatering process is determining the quality of the water at the site. Each potential option for discharging or managing the water at the construction site has distinct water quality requirements. For example, water discharged to sanitary sewer systems may not require pretreatment, even if it contains some level of pollutants. That same water will likely require treatment prior to discharge to a storm drain system.
To assess water quality of dewatering discharge, the suggested procedure begins with using a water quality assessment form, such as the Water Quality and Discharge Parameters Assessment Form[1] from the California Department of Transportation. Your state may have its own water quality assessment form that will guide you through the process of determining the quality of water on site.
The water quality assessment form will require you to complete a questionnaire based on whether the accumulated water is precipitation or non-storm water. Generally, the assessment will ask the contractor to determine if there is any reason to believe that the water has been contaminated by non-visible pollutants. For example, if the water is located in an area where there is known contamination or if the water has come into contact with construction activities or materials, then it may have non-visible pollutants. Next, the form will likely ask the contractor to assess the water for visible pollutants such as an oily sheen, floating foam, unusual color or a murky appearance. Finally, the form will question if the water has an unusual odor.
If any of the questions regarding water quality have been answered in the affirmative, then further testing may need to be done to confirm the presence of pollutants. Otherwise, the form can be submitted to the resident engineer for approval, and the approved forms can be filed with the appropriate authorities. The dewatering plan can then move forward to the next phase.
In many localities, construction site dewatering operations are limited based on the flow rate, daily volume, total volume and the duration of the process. Given the regulations governing construction site dewatering operations, it is important for contractors to estimate discharge parameters. This estimate is part of the Water Quality and Discharge Parameters Assessment Form, discussed above, and will be part of many states’ and localities’ permitting requirements as well.
Discharge parameters will be based on a number of factors, including the pump size and flow rate. An estimate can be formed by first determining whether the discharge is from groundwater, accumulated precipitation, a cofferdam/diversion, or other source. All sources of water, including multiple sources on one site, should be included. Next, estimate the total quantity of water, the number of hours the pump will be run each day, and the proposed discharge rate for each daily discharge event, including whether the discharge will be intermittent or continuous. The depth and flow of the water is a particularly important consideration, particularly if you are working on a cofferdam project. Consulting U.S. Geological Survey (USGS) gauges can help you determine fluctuations in river levels and determine the best time for a project involving construction site dewatering. Additional considerations should include the pH and turbidity of the discharge water compared to the receiving water and the expected duration of the dewatering operation.
Once the discharge parameters estimate form has been completed, it should be submitted to the resident engineer for approval, and then filed with the appropriate local authorities.
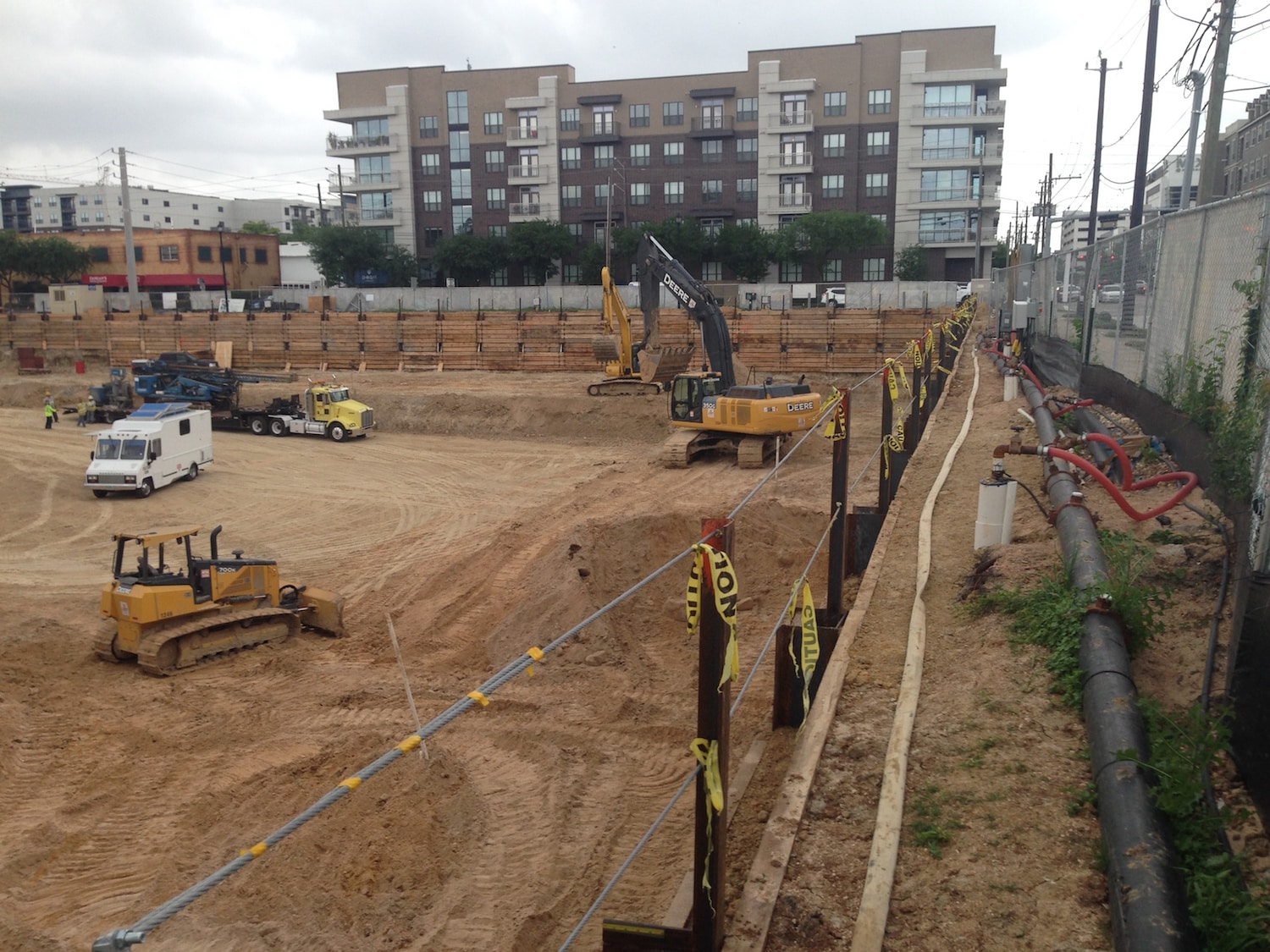
Pearl Residences Midtown, Houston, TX
Deep Well Dewatering System
General Contractor: Morgan Group
2017 Dewatering system in operation
Step 2: Obtaining Permits
As discussed above, the type of permit that you will need will vary based on your location, the type of water you are dealing with, and the dewatering operation that you are undertaking. Contractors should be aware of the specific requirements in their area, particularly as it relates to the specific requirements for turbidity (level of sediments in the water), pollutants other than sediments, pH levels and other requirements, such as testing and evaluations. Having a complete understanding of these considerations will assist in the timing and planning of construction site dewatering projects.
Step 3: Treating Water Containing Sediment
Sediment is the most common pollutant in water found on construction sites. When sediment is visible in water, a sediment treatment option may be considered prior to starting the construction site dewatering operation. The amount of sediment removal required will depend on factors such as the dewatering process chosen and the permits in place. For example, if the water is being kept on-site for use on the construction project, a high degree of sediment removal may be necessary in order to ensure proper functioning of water trucks. If the water is being discharged to a storm drain, then a similarly high level of sediment may also need to be removed in order to comply with federal or state law or with disposal permits.
The appropriate sediment treatment option will depend on several considerations. First, look to the type of sediment present in the water. The size of the particles will likely be determinative of the options available; the finer the particle, the more advanced the technology will need to be in order to effectively remove the sediment. Second, consider the site conditions when determining which sediment treatment option to utilize. The slope and accessibility of a construction site may limit choices when it comes to sediment treatment, particularly when it comes to the effectiveness of pumps and other equipment. Third, think about the volume of water present at the site. Manufacturers specify the maximum flow rate that can be treated for sediment removal; if a particular site has a large quantity of water, multiple systems may be required. Finally, cost and availability should be considered as part of the overall calculation.
Option 1: Desilting Basin
For large to some fine-sized particles, a desilting basin may be an effective choice. A desilting basin is a temporary basin with a controlled release structure that is formed by excavation to stop water runoff, and permit sediment to settle out before being discharged. This option can hold large volumes of sediment, and can filter particles ranging from gravel to silt. However, they require a large surface area and are ineffective in removing colloidal particles. Maintenance is required for safety and other requirements. It is a relatively low cost option, at $15 per square foot.
Option 2: Sediment Trap
For large to medium-sized particles, such as sand and gravel, a sediment trap is a cost-effective choice. Sediment traps are temporary containment areas that permit sediment to settle out during infiltration or before discharge through a stabilized spillway. As with desilting basins, sediment traps require a large surface area, and are only effective for the removal of large and medium size particles. Maintenance is required for these traps, which cost approximately $15 per square foot to construct. Sediment traps can be built in confined areas.
Option 3: Weir Tank
For sediments as small as .05 mm, a weir tank separates water and waste through the use of weirs. Multiple tanks can be used in parallel to achieve a high rate of flow. Weir tanks can remove trash, some settleable solids, some visible oil and grease, and fine sand. Removal is dependent on flow rate, with improved results on slower flows. Weir tanks are a simple solution, and fairly inexpensive to rent ($55 — 70 per day). The tanks require a level surface and enough space to set up, and often require an additional method of sediment or pollutant removal to achieve optimal water quality.
Option 4: Dewatering Tank
Depending on the type of filtering fabric used, a dewatering tank can remove fine particles as small as .025 mm in size. This makes dewatering tanks an excellent choice for removing smaller particles. In a dewatering tank, water enters the tank through the top, goes through a mesh fabric filer and then is discharged through the bottom of the tank. The filer removes trash, sediments and some metals and oil. It requires level ground, and costs about $70 to 90 per day for a tank.
Option 5: Gravity Bag Filter
For removing sediments and some metals, a gravity bag filter (also known as a dewatering bag) is a rectangular bag that can collect sand, silt and other fine sediments. Water that needs to be treated is pumped into one side of the bag and then seeps through the bottom or sides of the bag. The sediments that escape from the bag are then captured by a secondary barrier, such as a rock filter bed or straw bale barrier. The bag can last for three days to three weeks, and costs from $170 to $300 per bag, depending on size. The bag works efficiently, although it requires the installation of a secondary filter. It must also be monitored continuously to prevent ripping, tearing or overfilling of the secondary barrier.
For a final treatment of water, a sand-media particulate filter can help to remove particles as small as .01 mm, with an efficiency rate of up to 95%. Water that is recirculated through a second unit can result in removal of particles to sizes as small as .005 mm or smaller. This makes a sand-media particulate filter an excellent choice as the last step after water has been treated with other options. A sand-media particulate filter requires a level, compacted surface, along with backwash tanks with clean water. This type of filter is expensive, with a cost of up to $1,700 to $6,200 per month per unit.
Option 7: Pressurized Bag Filter
Pressurized bag filters can removed particles as small as .002 microns with up to 99% removal efficiency, depending on the type of filter selected. They can also remove hydrocarbons with oil absorbent bags. Water flows through a pressurized bag filter, is discharged through a distribution header, and then flows into an additional treatment unit. A variety of filters and cartridges are available for this type of sediment treatment option. Pressurized bag filters require a level, compacted surface, and are expensive to rent, at approximately $2,800 per month. Pressurized bag filters are often used in combination with cartridge filters.
Option 8: Cartridge Filter
For removing small particles to less than .002 mm, hydrocarbons, and other sediment, cartridge filters are often used as a secondary level of treatment. They utilize a series of individual cartridges as part of a larger filtering unit, often in combination with pressurized bag filters. The cartridges are often made of media such as paper, polypropylene, nylon and cellulose to remove a variety of contaminants from water. As with pressurized bag filters, renting a cartridge filter unit is pricey, typically costing between $1,200 to $4,700 per month.
Option 9: Active Treatment Systems
An active treatment system is any one of a number of conventional treatment technologies that can be utilized on construction sites with sediment that is difficult to remove from suspension, severely impaired receiving waters, or sites with small disturbed waters. The system uses either a coagulant or a flocculent for the treatment or water for turbidity reduction. When necessary, pH adjustment or filters may be included in the process. The exact system will vary based on the quality of the water to be discharged and the receiving water requirements. These systems can be complex to design, and expensive to implement. They can be used only for accumulated precipitation, and may require preliminary treatment or post-treatment to remove chemical residue.
Who regulates dewatering operations?
Dewatering operations are regulated by federal and state law. Federal regulations, including those issued by the Environmental Protection Agency (EPA), require that contractors that plan to discharge construction site water or stormwater to obtain a National Pollutant Discharge Elimination System (NPDES) permit.
What is a dewatering operation?
In order to begin construction operations, it is generally necessary to remove this water in a process known as dewatering. In general, dewatering is a multi-step process involving storing water, pumping the water, treating it, and discharging it that may require the provision of permits, depending on your state.