Drilling in the Construction of a Particle Accelerator in Darmstadt, Germany
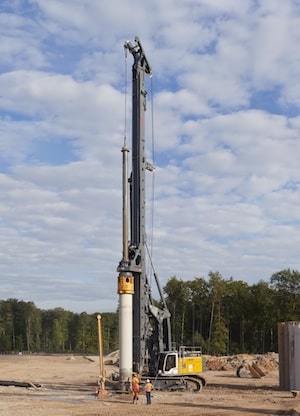
The first two Liebherr LB 44-510 rotary drilling rigs are being employed in the construction of a particle accelerator in Darmstadt, Germany. First presented at the Bauma 2013, the LB 44-510 rotary drilling rig is the latest development in Liebherr’s range of deep foundation products and expands the tried and proven LB series of rotary drilling rigs at the upper end of the scale.
The LB 44-510 has a torque of 510 kNm, making it the largest and most powerful rotary drilling rig currently in operation in Germany. In Kelly drilling applications, it is configured for drilling diameters of up to 3 m and depths of up to 92 m. The drilling rig weighs some 170 tonnes and is powered by a V8 diesel engine offering 505 kW (677 hp) and complying with the emissions standard stage IIIB / tier 4i.
Two LB 44-510 rotary drilling rigs are being employed on the construction site, which covers a total area of 200,000 m2, to stabilise the subsurface with cast-in-place drilled piles. These operations form the basis for the construction of the international particle accelerator FAIR (Facility for Antiproton and Ion Research). 35,000 tonnes of steel and 600,000 m³ of concrete are to be used in this construction project.
The lead contractor is the “FAIR Bohrpfähle” joint venture, comprising Züblin Spezialtiefbau GmbH (engineering management) and Max Bögl GmbH & Co. KG (commercial management).
Besides other drilling equipment, each company has provided an LB 44-510 to the joint venture to realise the extraordinary construction project.
Highly productive kelly drilling application for great depths
In total, some 1,400 foundation piles with a length between 40 and 62 m have been set in the ground since March 2013. To this end, the first series production unit of the LB 44-510 was delivered in August. Since mid-September, another LB 44-510 has been on the site, working in kelly drilling application.
All drilled piles are installed down to the final depth completely cased. That means that during the drilling process, the excavated material is removed under the protection of an advancing casing. Because of the high groundwater level and the partially unstable ground, a water load is needed throughout the pile manufacturing process to stabilise the bottom of the boreholes.
A drill bucket is used to loosen and remove the drill cuttings. The efficiency of the rotary drilling rigs working in the rotary drilling method means that the boreholes can be excavated down to the final depth completely cased, without the need for a casing oscillator. This procedure can be realised for the depth needed in Darmstadt with the LB 44-510. Thanks to the high torque and enormous pull force of the LB 44-510, there is no need for the machine units to be changed after the drilling process.
In the past, two duty cycle crawler cranes with casing oscillator were required to reinforce the piles and for concreting, in order to reliably guarantee the necessary torque and pull force when extracting the casing during concreting work. The LB 44-510 provides for substantially greater productivity when installing piles down to great depths.
Apart from the great drilling depths needed in the construction of FAIR, which are extraordinary for cased drillings, working in a drinking water protection zone also meant special requirements when preparing the piles. To this end, around 30 piles are fitted with sophisticated measuring equipment for monitoring the forces on the piles and any subsidence.
Quick set-up, easy transportation
Despite its impressive size, the 170-tonne LB 44-510 rotary drilling rig does not need much time for its set-up. As the leader can be folded back for transportation with all hydraulic hoses connected, no disassembly is required when moving between two jobsites. Subsequently, the LB 44-510 can quickly be set up using the quick assembly system – this process barely requires more time than for smaller machines. On the FAIR construction site, the two LB 44-510 units were ready for operation in just six hours.
Another benefit is that the machine is straightforward to transport. If required it can be disassembled so that no single unit weighs more than 40 tonnes. That means that it can be transported throughout the world without any problems.
The basic concept of the machine follows two tried and proven principles. This includes a large operating area thanks to parallel kinematics. Another aspect concerns the direct assembly of all winches on the leader, which on the one hand allows for a direct view from the operator’s cab to the main winch, and on the other hand ensures that the ropes do not move while the leader is being adjusted. Secondly, the undercarriage has long crawlers, increasing stability and guaranteeing a small swing radius which can only just be matched by the smaller units of the LB series.
The innovative BAT rotary drive of the new LB 44-510 offers a torque of 510 kNm. The main advantages of the hydraulic drive manufactured by Liebherr are automated torque adjustment, continuous speed optimisation and four electronically adjustable speed ranges. Further advantages of this rotary drive are its simple structure, its low maintenance requirements and, above all, its exceptional efficiency.
Besides the described application with the kelly bar, the LB 44-510 is also suitable for drilling processes employing a double rotary head, continuous flight auger and full displacement tool. The powerful rope crowd system with a pull force of approx. 56 t allows the entire length of the leader to be utilised. This provides the operator with maximum performance and reliability even on the most difficult soils and under extreme operating conditions.
Major research institution with far-reaching scientific ambitions
After its planned completion in 2018, the FAIR particle accelerator will be one of the largest research facilities in the world. Some 3,000 researchers from around 50 countries will then use FAIR for their scientific projects. For example, it is planned to use this major research institution to investigate how the universe developed from the big bang to the present day, and to decode the building blocks of matter.
Besides basic research, FAIR should also help to develop new medicinal therapeutic and diagnostic procedures, energy-efficient high-performance computers and new materials, for example for use in interplanetary space travel.
The new facilities are being built directly adjacent to the GSI Helmholtzzentrum für Schwerionenforschung (Helmholz Center for Heavy Ion Research), whose existing accelerator will be used as an injector for FAIR. Extremely intensive high-precision beams of antiprotons and ions from the entire range of elements can be generated on FAIR. These can be used by scientists for researching rarely observed particle collision products.