Ductile Iron Piles Support Norfolk Southern Mill Shop Renovation in Portsmouth, OH
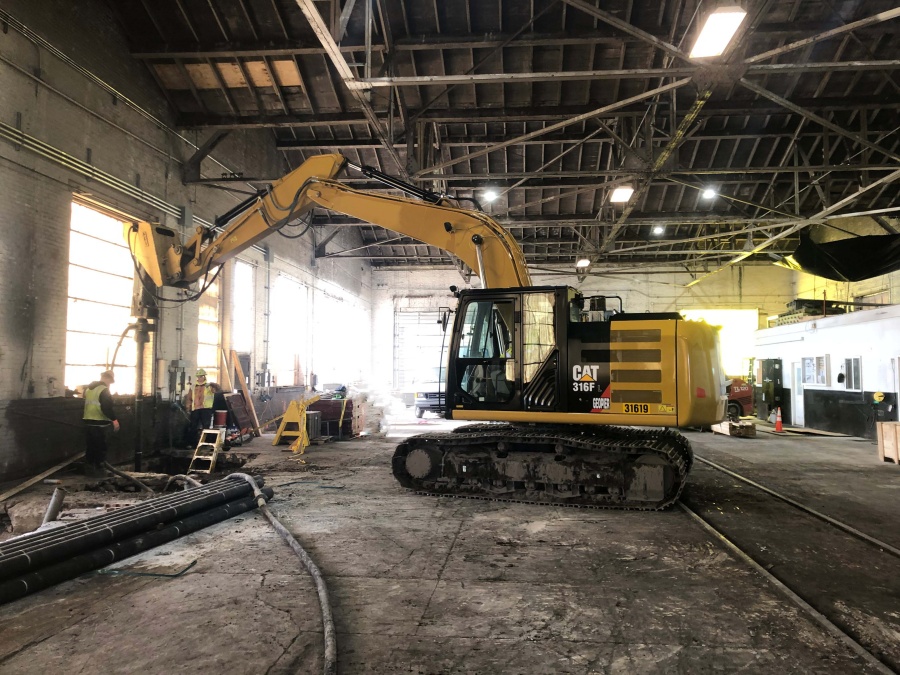
Expansions for manufacturing, warehousing, and distribution facilities were on the rise even before the Pandemic. The tremendous surge in demand continues to drive the need for renovation and expansion projects. Unfortunately, deep foundation options in the geotechnical toolbox for these types of projects are often limited. Piling solutions including helical piles and micropiles are typically recommended for support of new foundations and slabs. Yet project teams are often on the look out for alternative solutions to achieve higher capacity (and fewer) helical piles or a faster and less costly foundation system than drilled micropiles.
One such project involved the construction of a new crane system at the Norfolk Southern Mill Shop in Portsmouth, Ohio. The new 20-ton crane rail system was 48-ft wide and designed to run 180 feet through the shop interior. The new crane was planned within an area of the existing facility with only 20 feet of overhead clearance. Plans required a total of 16 new foundations to support the crane structure.
Initial recommendations for foundation support provided by Urban Engineers, the geotechnical engineer, included micropiles and augercast piles with compression capacities of 25 tons. The project team, investigating additional cost-effective piling options, approached DuroTerra about a Ductile Iron Pile solution. Ductile Iron Piles have been used in Europe for four decades to
provide an alternative to traditional foundations and are fast becoming the desired solution for foundation support in overhead restricted areas and many other challenging sites across the U.S.
Ground conditions consisted of 7 feet of sand fill underlain by soft to stiff silt and clay to a depth of about 40 feet followed by medium dense to very dense sand. Groundwater was encountered near 40 feet at the top of the sand. DuroTerra developed a friction pile solution consisting of exterior grouted Ductile Iron Piles installed through the upper silt and clay to terminate in the sand to develop working capacities of up to 25 tons (compression), 5 kips (tension) and 2 kips (lateral).
The foundation plan developed by project structural engineer, L.A. Gates Company, included isolated foundations requiring a group of three piles to maintain rotational stability. A Series 118/9.0 Ductile Iron Pile section (118 mm outer diameter with 9 mm wall thickness) was designed with a 220 mm oversized grout shoe to produce an 8-inch diameter grouted displacement pile to provide a cost-effective alternative to the micropile and augercast options. A 10-ft long, #6 Grade 75 threadbar was inserted into the pile to resist the minor tension loads and to hold the bearing and tension plates.
Peterson Contractors, Inc. performed the Ductile Iron Pile installations at the site using a mobile CAT 316 excavator with a CAT H120 hydraulic hammer. The 5 meter (16.4 ft) pile sections were cut in half to work within the limited overhead condition. During the test pile installation, driving resistance (rate of advancement) substantially increased below depths of 35 feet. The test pile achieved “set” of less than 1 inch of movement in 50 seconds at a depth of 47 feet indicating a competent bearing condition on the very dense sand. Results of the full-scale load test showed 0.16 inches of deflection at 47 kips (100%) and 0.51 inches at (200%) to verify the performance of the alternative approach.
Production piles proceeded during the interim between test pile installation and full-scale load testing to help accelerate the pile scope of work. Only 2 of the 3 piles were installed at each location initially to reduce the risk of pile cap geometry changes if the test results were unanticipated. Once the successful test was performed, the remainder of the piles in each group were installed. All piles were installed in similar fashion as the load test and achieved dense driving and set in the dense sand. A total of 48 piles were installed to depths of about 45 feet in 3 working days.
The use of low vibration, driven Ductile Iron Piles provided substantial reduction in time for the piling scope of work compared with the more traditional piling systems and reduced the overall foundation costs while still delivering a pile that met the design requirements.