Dick Hartman: Failure Specialist and Cofferdam Expert
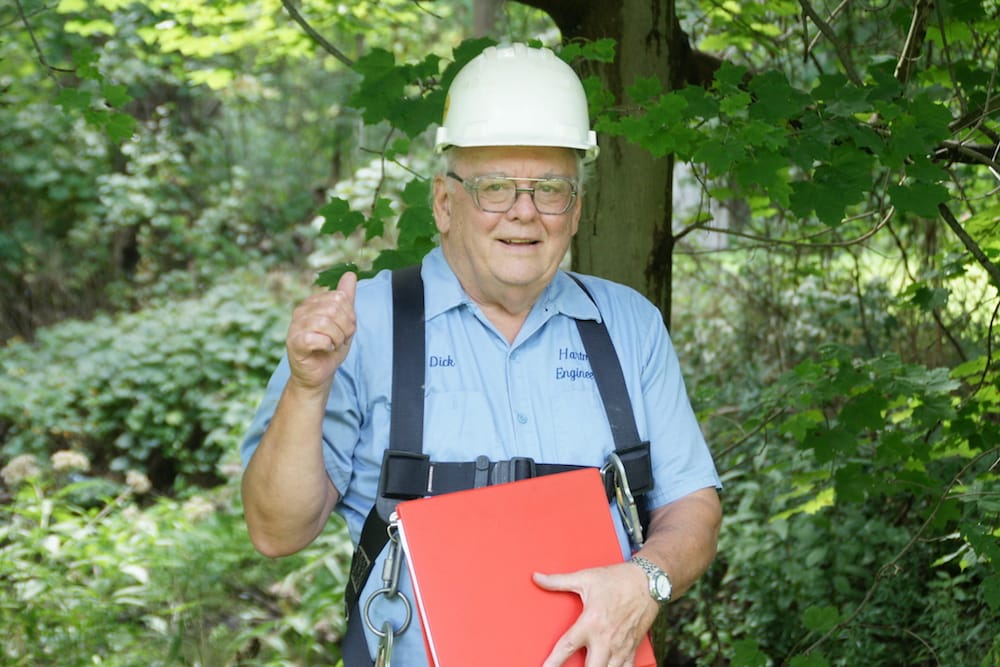
by Sarah Milstead
This summer, Pile Buck traveled to Clarence, New York on the outskirts of Buffalo to interview Dick Hartman, P.E., referenced in the industry as the number one cofferdam expert in the world.
PB: Dick, can you begin with some background of where you grew up?
Dick Hartman: I was born in Buffalo, New York and I grew up on the west side of Buffalo where we could walk in the park and go down by the Niagara River, go fishing. After 8th grade, my parents decided to move to the suburbs. I went to the Williamsville schools, where I ran track and cross-country.
In 1959 after high school, I went to the University of Buffalo [State University of New York at Buffalo] where I earned my bachelor of science in civil engineering [1965] then my master’s degree in 1966. I got married in 1965.
I went to Drexel [University in Philadelphia] in 1966 where I earned my Ph.D. in 1972. I started teaching at the community college in 1970 while I was still finishing my dissertation.
I started my engineering practice in 1966 and I was doing work for contractors I had worked with previously designing cofferdams for them and I had it in my mind that I would have a career both in teaching and consulting work. Then the consulting work just took off and I could only do one job so I chose the consulting track.
This choice was partly influenced by the fact that in 1972 tropical storm Agnes came through the eastern part of the country. I had graduated just 10 days previous to that and thought I was going to have the summer off. A hospital administrator called me and asked, “We have a river that’s flooded and it’s underneath the foundations of our hospital now, the soil is gone … can you help us?”
There was no soil under the hospital wing so I went there and worked with them. One of the hospital wings was lost, collapsed into the river. We were able to stop another wing from moving. I ended up working with them through the whole summer and that was a big start towards my consulting practice.
It was a big project for me for quite awhile. I got 10 days of vacation between getting my degree and that phone call!
I have two children, a son and daughter, who both live in Michigan.
That’s my bio!
PB: Let’s start with how you became interested in the field of engineering.
DH: I had it in my mind that I wanted to be a medical doctor. However, I was with my uncle, whom I looked up to, and he asked me what I was going to do when I finished high school. I replied I really didn’t know. He asked why don’t you become an engineer, they make a lot of money, so I said, ok … [laughter]. That was the decision path. If it had been anyone but that uncle I don’t know that I would have agreed to it.
PB: Would you like to talk a little about the two specialties your practice concentrates on, the design of retaining structures and the evaluation and repair of structures that are seriously damaged by foundation problems?
DH: I had summer jobs with construction companies and had never heard of a cofferdam before but they were having trouble with one. I did not get involved with the problem-solving, I was way too young for that, but I saw what the problems were.
As I got older, I realized that no one really focused on that [identifying the problems and solving] and I saw a need for it. When I was deciding how I was going to build my practice, I looked for areas where I wouldn’t be actively competing with other people, where it would be easier to get projects.
I saw that the more risk there was with a project, the less competition there was. So I decided I would work towards trying to develop a practice in the high-risk area where structures were damaged. We were involved with that hospital I mentioned, we were involved with a radio tower that had the guy wires cut and we had to stabilize the tower until they brought in some big equipment to could take it down. We got into underpinning buildings which was fairly high-risk work and then the cofferdams, of course, which I consider high risk. I think most people do.
PB: What makes cofferdam work such high risk?
DH: It is high risk because there are so many things that can go wrong, so many unknowns and when something does go wrong, it sometimes involves injury or loss of life and it’s always very, very expensive to fix.
It’s never a one- or two-day fix. It’s always a longer time and hundreds of thousands of dollars. So that looked like a promising field.
In the early stages, in order to promote projects, I would design underwater projects such as water intakes which were constructed totally under water. I would offer the service of doing the design, doing the inspection, doing the diving and so forth.
PB: So you were a diver?
DH: Yes, the last time I dove was December, 2000 in the harbor of Oswego, New York with ice floating on the water. I was down there working, the hot water pump was not working all that well, it was dark and I was cold.
All of a sudden, I asked myself, “Just what am I doing here?
Why am I here?”
I answered myself, “I don’t have to be doing this anymore.” That was the last time I did that. I was a young kid then [laughter]. I was 59 years old.
One of the most spectacular projects was that falling hospital wing which was 40 years ago. Realistically, I think my business has evolved and there is less of the actual structural work like that was. With the wing that was saved, we ended up cutting the columns and jacking them up. Over the 30- or 40-year period, my work has gone almost entirely to cofferdams and retaining structures: cellular cofferdams and regular, single wall cofferdams which use Z shape sheet piling.
PB: You designed these shapes?
DH: Yes, I worked with Dave Fournie at Gerdau and designed the PZC1 sections that Gerdau now makes and L.B. Foster Company distributes. We did testing and research work and determined that the sheet piles were subject to, what we call, transverse stresses. They are bent in the horizontal plane, not just the vertical plane. We designed the sheet piling to resist those types of loads and, to the best of my knowledge, these are the only sheet piles that do that. We have the patents for them.
Another thing we have developed and have done a fair amount of work on is the large, circular cofferdam.
Not cellular, but circular: a single line of sheet piling around the outside and braced with concrete rings. We’ve developed that system so that we can do excavations that are 100- to 150-feet in diameter. With a clear space to work there is no interference to excavations or to building structures.
We designed a circular cofferdam that was built around a collapsed cofferdam in Puerto Rico. That was a situation into which we were called where a cofferdam had collapsed. After we put a circular cofferdam around the collapsed one, they were able to remove the collapsed cofferdam. I remember that cofferdam was 140-feet in diameter. That’s an area where we have helped to develop the technical expertise.
We put on seminars designing sheet pile structures. One important goal of the seminars is to try to give people a heads-up for problems they can run into. There have been some nasty accidents. The circular cofferdams are very tricky to design, especially in water. The engineers need to really think through each design.
The seminars are sponsored by Gerdau and L.B. Foster Company. We did one in Panama about a year-and-a-half ago for the Panama Canal Authority engineers who were designing the upgrades to the Canal.
In the seminars we talk about all types of sheet piling structures, from the simple ones to the more complicated ones, with the idea of helping to educate people, not only how to design them, but how to foresee problems and design it so that the problem can’t occur.
Again, this is an area where there can be real hazardous situations in terms of loss-of-life, but more frequently, when those problems occur it’s a big problem financial- and schedule-wise.
PB: What are some of the problems?
DH: An example of loss-of-life situation is the cofferdam collapsing on people.
The soil bottom of the cofferdam will not be stable because the water goes around the bottom of the sheet piling and up the inside and, after that occurs, the cofferdam collapses and has to be removed. The soil at the bottom of the cofferdam is disturbed so it’s not good foundation soil anymore so, again, you are talking hundreds of thousands of dollars of delays and reconstructions.
PB: What are the main ways you try to prevent these failures?
DH: In the seminars we review the basic concepts for the different types of construction: anchored and cantilever walls, trenches, cofferdams, rectangular and circular cofferdams, on land and in water.
Then we review the basic concepts and show them five or six photos of failures that occurred from each of those different categories. The photos and the case histories are excellent because the participants remember them and they have a “picture.”
One level of the seminar shows the concepts for designing. Another level shows an example of where a red flag should pop up. When you have a certain type of design, hopefully, they will think back to the seminar and say, “Oh, I remember seeing that photograph of that failure.”
PB: Who is the core staff at Hartman Engineering?
DH: We’ve got Sandy Goodemote … she’s been working here for 20 years. She keeps the place glued together.
Dale Maerten and Gerry Wagner have worked with me for more than 40 years. Dale is strong in CAD work and visits jobsites. Gerry is strong in geology and geotechnical work.
There are several more people who help us when we need their skills. It’s a great team.
We do three or four seminars per year for Gerdau – L.B. Foster Company. We help them with specific projects. We tend to help them when there is a problem in the field. For example, L.B. Foster has provided the sheets, we would do the analytical part for them. We’re hired by contractors, sometimes by owners and sometimes by attorneys.
We have an ongoing project with a privately owned toll bridge across the Delaware River between Pennsylvania and New Jersey. It is not a cofferdam project, but there were serious issues with the pier foundations. We were selected for that project because of our underwater experience. The pier foundations were repaired and are working well. We now provide engineering services for both the foundations and the superstructure. The bridge is now more than 100 years old. We have been working on it for 35 years.
PB: There is a lot of work on aging dam and levees such as the Herbert Hoover Dike around Lake Okeechobee in Florida. Were you involved with that?
DH: We worked in Lake Okeechobee, FL for the South Florida Water Management District. There had been a drought and Lake Okeechobee was so low that the District foresaw the scenario: if a heavy rainfall came suddenly, the surge of rain would cause high water on some sides of their “control structures” and low water on the other side could destroy these structures.
To be proactive, the District had an emergency project to build some weirs so that they could keep the tail water (low side of the water) relatively high and protect the structures.
We designed cellular sheet piling abutments for that. What was interesting was they contacted us in December and the whole team worked well together. Ours was a very small part of it but we had the entire project designed and built within nine months. Right after that a hurricane did hit and produced a tremendous amount of rain water. There could have been a collapse if the work had not been completed!
PB: Who are your primary clients?