ShibataFenderTeam | Schuyler Companies |
---|---|
More information | More information |
![]() |
![]() |
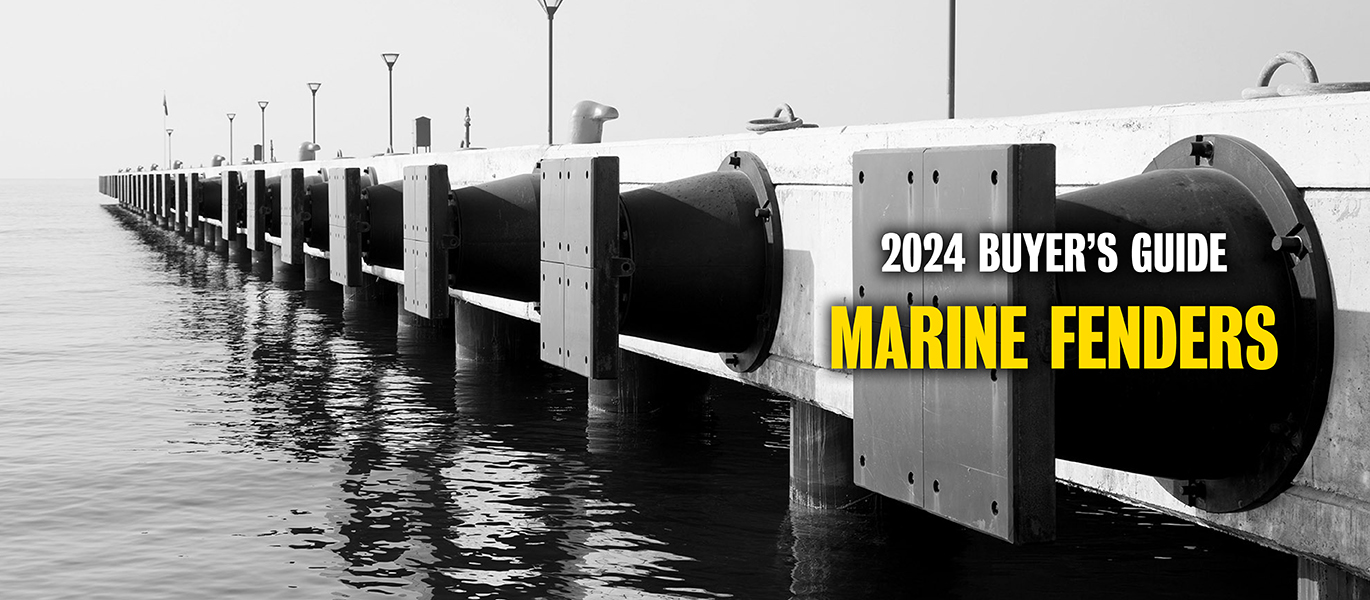
Pile Buck's Top Recommended Fender Suppliers
Fenders are often overlooked but are vital in maritime operations. These unassuming devices play a pivotal role in protecting vessels and infrastructure—effectively cushioning the impact of berthing, mooring, and docking. This guide will cover their diverse types, applications in different marine environments, and the essential considerations for selecting the right fender system.
Functions and Purpose of Fenders
Fenders play a pivotal role in marine construction, serving multiple functions that are crucial for safeguarding vessels, structures, and ensuring the overall safety and efficiency of maritime operations.
Protection of Vessels and Structures
One of the foremost functions of fenders is to provide essential protection to both vessels and the structures they come into contact with—including piers, docks, quays, and other infrastructure. This protective function serves several important purposes:
- Minimizing impact damage: Fenders act as a buffer, absorbing the energy generated during vessel berthing or mooring. This energy absorption prevents direct collisions between vessels and structures, significantly reducing the risk of damage.
- Preserving vessel integrity: By absorbing and dissipating kinetic energy, fenders protect the hulls and superstructures of vessels from structural damage and deformations that could compromise their seaworthiness.
- Extending infrastructure lifespan: Fenders also safeguard the longevity of port and harbor infrastructure by reducing wear-and-tear caused by repeated vessel impacts—garnering lower maintenance costs and increased operational efficiency over time.
Energy Absorption and Dispersion
Fenders are engineered to efficiently absorb and disperse kinetic energy, which is generated when vessels approach berthing facilities or during mooring. This critical function serves the following purposes:
- Energy dissipation: Fenders dissipate the kinetic energy of a vessel’s movement by deforming and rebounding, thus reducing the impact forces transmitted to the vessel and the structure. This controlled energy dissipation prevents sudden jolts and potential structural failures.
- Enhancing safety: By gradually slowing down and dispersing the energy, fenders contribute to a safer and more controlled berthing process—protecting crew, cargo, and the vessel itself from sudden and violent impacts.
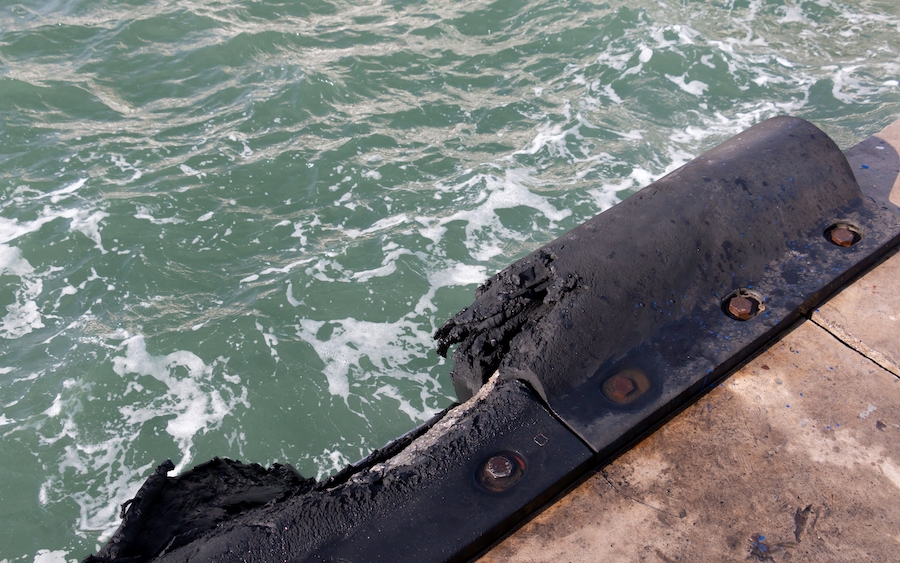
Preventing Damage During Vessel Berthing
Fenders are especially crucial during the vessel berthing process, where precise control is required to prevent costly and dangerous accidents. Their role in this context includes:
- Mitigating berthing forces: Fenders absorb the berthing forces that occur when a vessel makes contact with a quay or dock, preventing excessive loads on the vessel’s mooring lines and the infrastructure. This ensures that berthing is a controlled and damage-free operation.
- Maintaining operational continuity: Effective fender systems help minimize downtime by reducing the risk of damage to vessels and berthing facilities. This is particularly important in busy ports where efficient vessel turnaround times are essential.
Facilitating Safe Mooring and Docking
Fenders also play a pivotal role in facilitating safe mooring and docking procedures, ensuring that vessels can be securely anchored in place. Their contributions include:
- Steadying vessels: Fenders assist in stabilizing vessels during mooring and docking—preventing unwanted drifting and swaying, especially in adverse weather conditions.
- Reducing crew risks: By providing a cushioned and controlled contact point, fenders reduce the risk of accidents to crew members involved in mooring and docking activities.
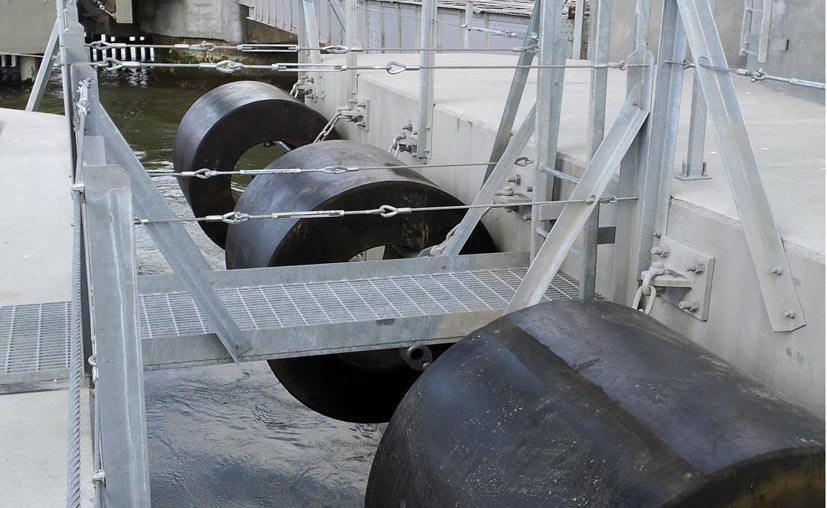
Types of Fenders
Understanding the various types of fenders available is essential for selecting the right fender system to meet the specific needs of a marine construction project. Each type of fender has its unique advantages and limitations, and choosing the appropriate fender type is crucial to ensure the safety and efficiency of a project.
Rubber Fenders
Rubber fenders are among the most widely employed fender types due to their versatility and effectiveness in absorbing and dissipating kinetic energy. For example, in busy container ports, cylindrical rubber fenders efficiently cushion and slow down massive cargo vessels as they make contact with the pier—preventing damage to both the ships and the terminal infrastructure.
They come in several shapes, including:
- Cylindrical fenders: Cylindrical rubber fenders are characterized by their simple, cylindrical shape. They are often used in areas with moderate tidal variations and vessel sizes. Cylindrical fenders distribute forces evenly, making them suitable for various applications like marinas and ferry terminals.
- D-shaped fenders: D-shaped rubber fenders have a flat back and a semi-circular front, resembling the letter “D.” This design allows them to efficiently protect vessels and structures while also serving as a bumper during berthing operations.
- W fenders: W fenders, as the name suggests, feature a distinctive “W” shape. This design provides excellent energy absorption and dispersion capabilities, making them ideal for larger vessels and areas with high tidal fluctuations.
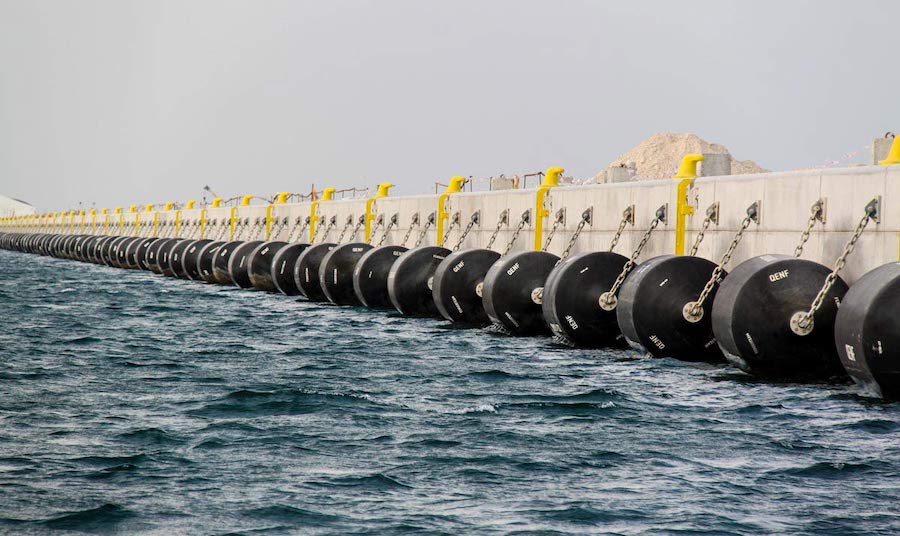
Foam Fenders
Foam fenders are lightweight and durable, making them suitable for specific marine construction scenarios. They are typically made of closed-cell foam encased in a tough polyurethane or elastomer skin. Foam fenders offer advantages such as low maintenance and high energy absorption.
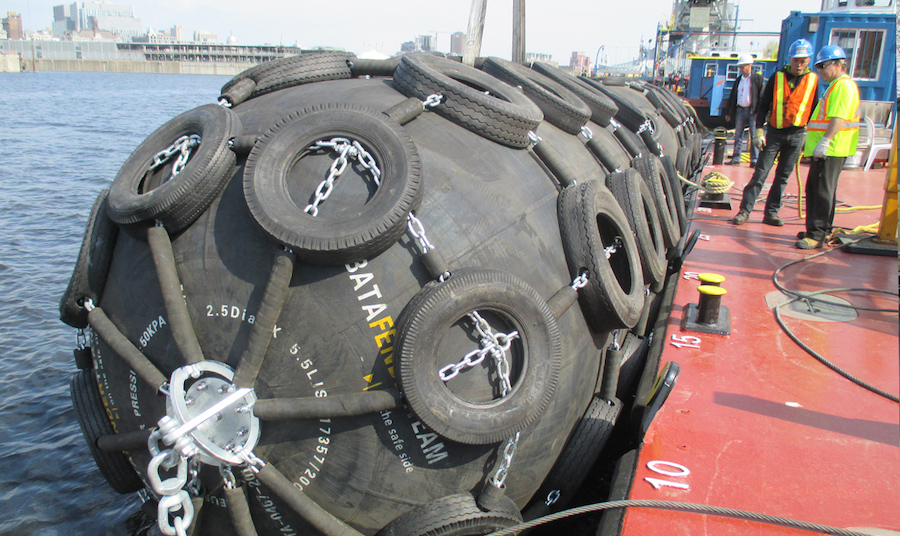
Pneumatic Fenders
Pneumatic fenders, also known as air-filled fenders, rely on air pressure to absorb impact energy. They are highly resilient and can adapt to variations in vessel size and shape. Pneumatic fenders are commonly used during ship-to-ship transfers and as temporary fenders in construction and maintenance projects.
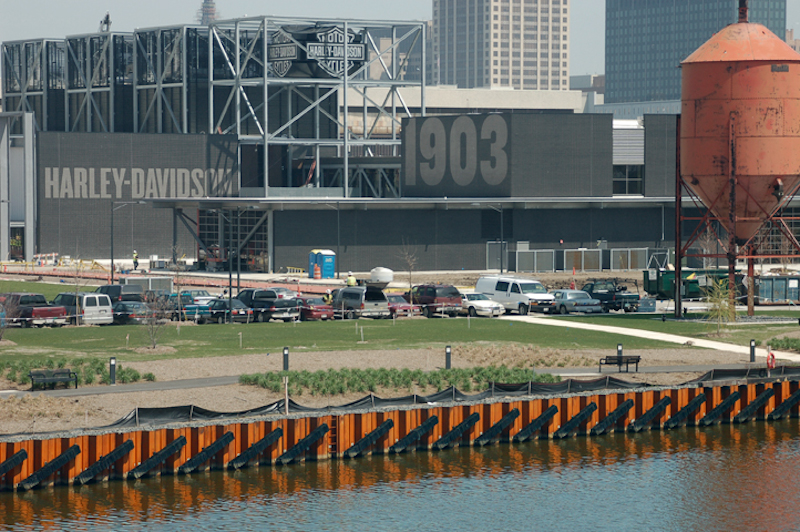
Sheet Pile & Concrete Dock Fenders
Sheet pile and concrete dock fenders are versatile options for shielding docks and quays from the forces of maritime operations. Sheet pile fenders are constructed from interlocking steel sheets, while concrete dock fenders are made of durable concrete. They serve as a solid buffer, minimizing impact damage and ensuring the longevity of structures in busy port environments.
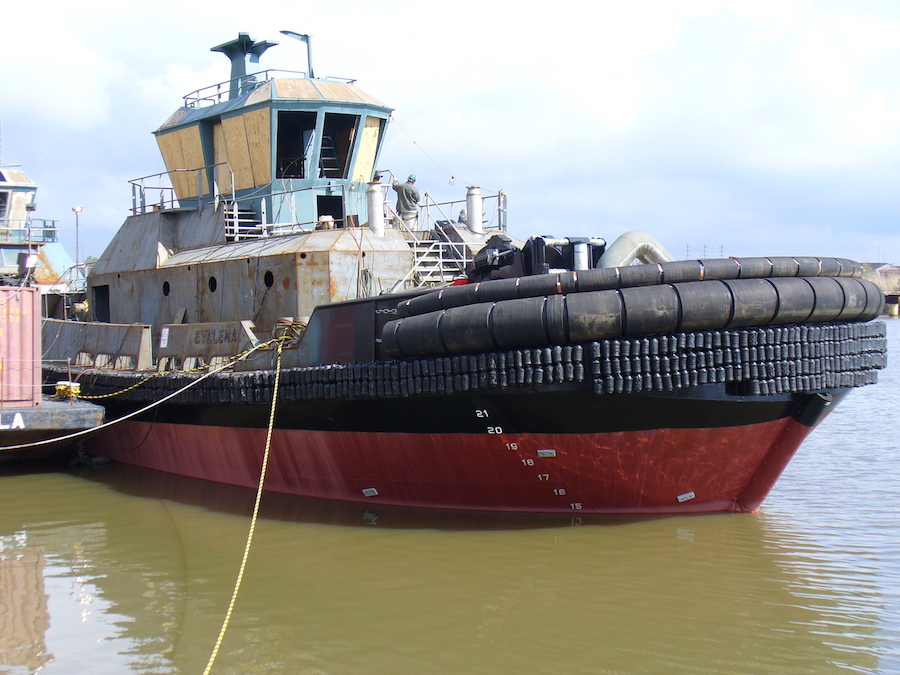
Tugboat Fenders
Tugboat fenders are specially designed to protect tugboats during pushing and towing operations. They are typically installed on the sides of tugboats to minimize damage during contact with larger vessels.
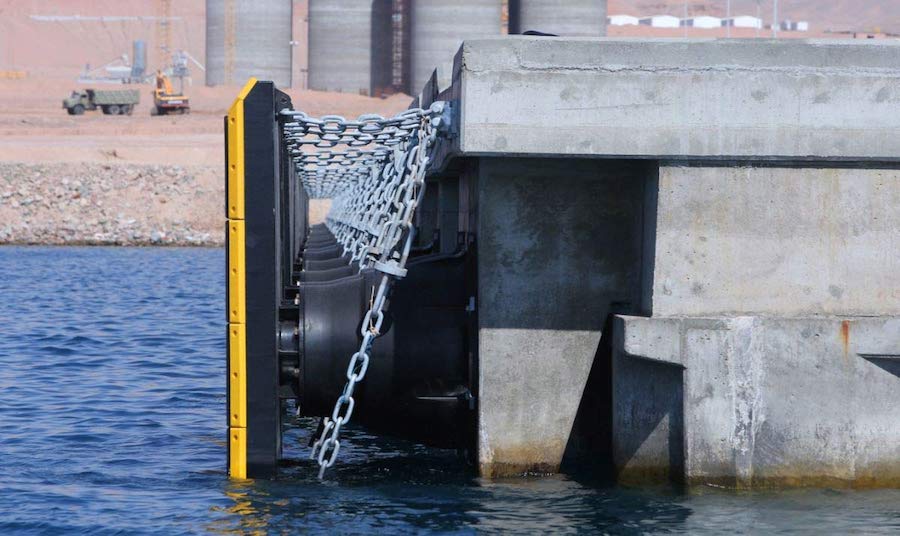
Cone Fenders
Cone fenders have a conical shape and are highly effective at absorbing energy in a compact design. They find application in various marine environments, including container terminals and oil and gas facilities.
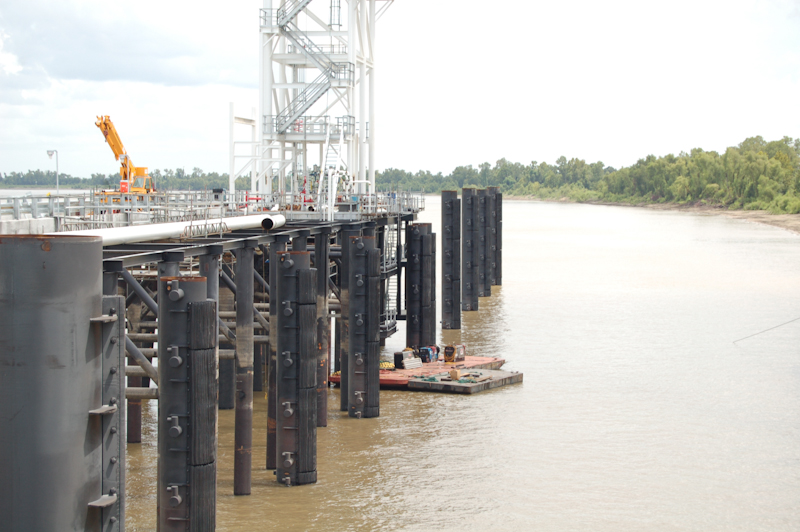
Pipe Pile Fenders
Pipe pile fenders are a robust and reliable solution for safeguarding marine structures. They consist of sturdy steel or concrete pipes driven into the seabed, creating a protective barrier that absorbs and dissipates energy during vessel berthing. Pipe pile fenders are commonly used in piers, wharves, and other waterfront structures—offering effective protection for both vessels and infrastructure.
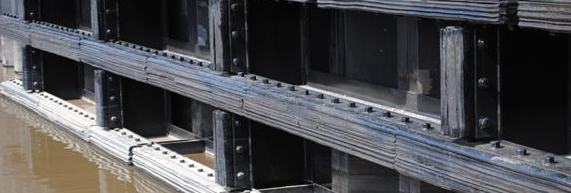
Steel Beam Fenders
Steel beam fenders are renowned for their exceptional strength and resilience. These fenders consist of steel beams positioned horizontally or vertically along the waterfront, effectively absorbing and dispersing kinetic energy from vessel impacts. Steel beam fenders are commonly deployed in heavy-duty applications, such as bulk cargo terminals and industrial facilities.
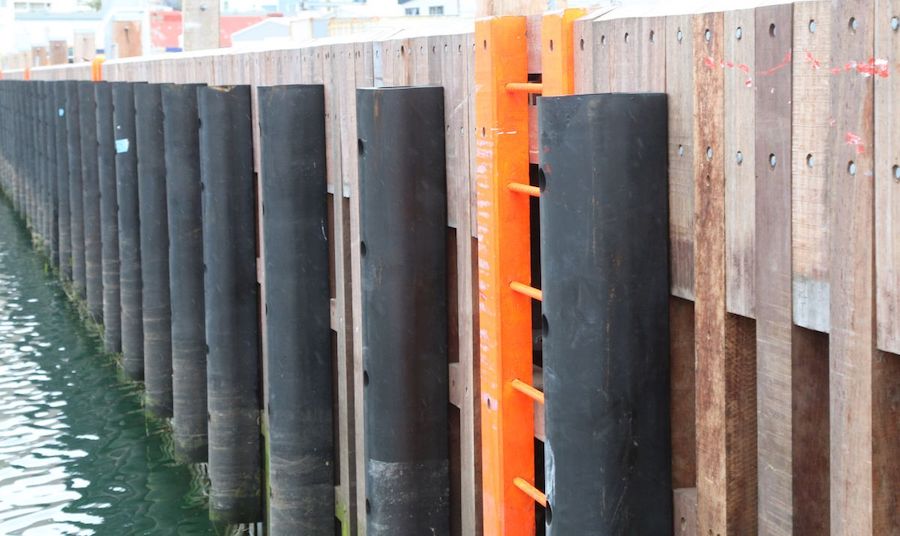
Extruded Fenders
Extruded fenders offer a streamlined and effective solution for vessel protection. These fenders are typically made from high-quality rubber compounds, featuring a continuous extruded profile that provides excellent energy absorption. Extruded fenders are frequently used in various marine settings—including marinas, ferry terminals, and offshore installations—where their reliability and durability shine through in demanding conditions.
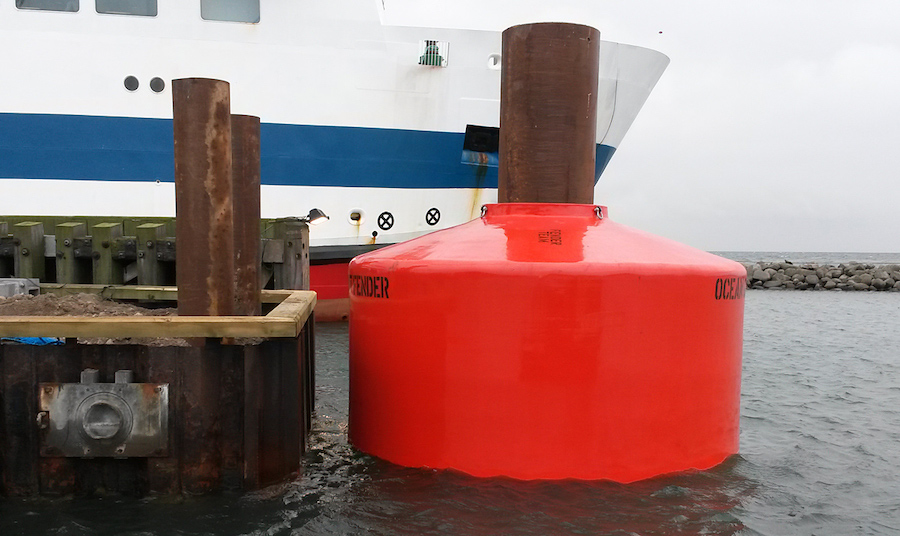
Donut Fenders
Donut fenders, also known as toroidal fenders, have a circular shape with a central hole. They are commonly used in offshore mooring and vessel-to-vessel transfers, offering reliable protection and stability.
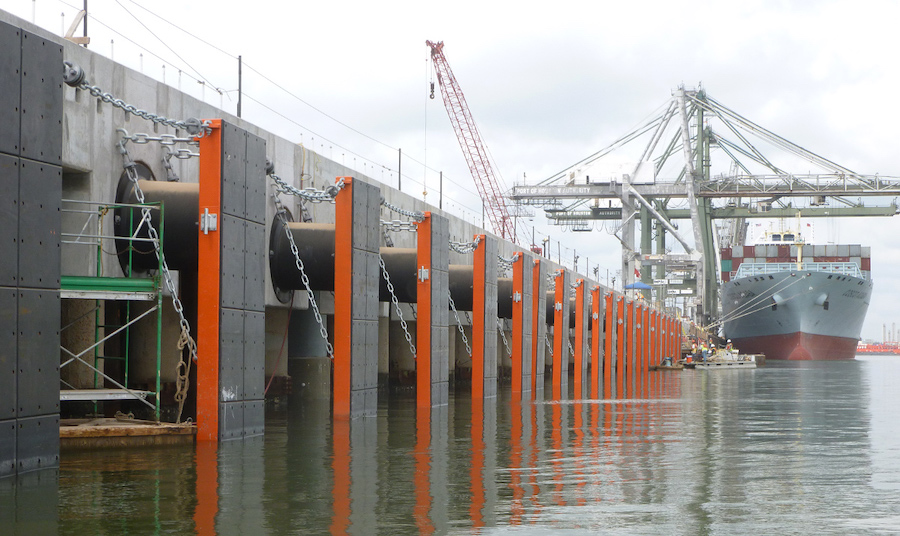
Cell Fenders
Cell fenders are characterized by a series of hollow cells, which provide exceptional energy absorption and low reaction forces. They are suitable for berths accommodating large vessels, such as bulk carriers and tankers.
Super cell fenders are an advanced version of cell fenders, featuring a larger contact area and improved energy absorption capabilities. They are often preferred for heavy-duty applications, such as LNG terminals and cruise ship docks.
Selection Criteria for Fenders
At the very least—the selection criteria for fenders should include design considerations, materials and durability, and maintenance requirements.
Factors to Consider When Choosing Fenders
The following factors should be considered during the fender selection process:
- Vessel size and type: The size and type of vessels that will be berthing or mooring at a facility are paramount in fender selection. Different vessels generate varying levels of kinetic energy during berthing, necessitating fenders that can adequately absorb and dissipate this energy.
- Berth configuration and conditions: The layout and configuration of the berthing area—including water depth, tidal variations, and available space—influence the choice of fenders. For instance, tight berths with limited maneuvering space may require fenders that offer precise protection.
- Impact energy calculation: Calculating the expected impact energy during vessel berthing is crucial. This involves analyzing factors such as vessel speed, weight, and angle of approach. Fender systems must be selected to match or exceed the calculated energy to ensure safety.
- Environmental factors: Environmental considerations—including wind, wave action, and water currents—can affect fender performance. Fenders must be chosen to withstand these conditions and maintain their effectiveness in adverse weather.
Fender Design Considerations
The design of the fender system itself plays a significant role in its suitability for a specific application. Key design considerations include:
- Type and shape: Different fender types—such as cylindrical, D-shaped, or cone fenders—have unique designs optimized for specific functions. Choosing the right type is essential for effective energy absorption.
- Mounting and attachment: Fenders can be installed in various ways, including fixed or floating configurations. The choice depends on the berthing facility’s design and requirements.
- Deflection capability: Fender systems should have the appropriate deflection characteristics to accommodate vessel movement and impact without exceeding their limits.
Materials and Durability
The materials from which fenders are constructed significantly impact their longevity and performance. Considerations include:
- Rubber quality: For rubber fenders, the type and quality of rubber used are critical. High-quality rubber compounds enhance durability and resistance to environmental factors.
- Reinforcement: Fenders may incorporate reinforcing materials such as steel or nylon to improve their structural integrity. The choice of reinforcement material should align with the intended application.
- Corrosion resistance: In corrosive environments, such as saltwater, selecting materials that resist corrosion, like stainless steel components, is essential to prolong fender life.
Maintenance Requirements
Fenders, like any other equipment, require regular maintenance to ensure their continued effectiveness and longevity. Maintenance considerations include:
- Inspection and monitoring: Scheduled inspections to check for signs of wear, damage, or degradation are essential. This helps identify and address issues promptly.
- Cleaning: Fenders should be kept clean and free of debris that could affect their performance.
- Repair and replacement: When fenders show signs of significant wear or damage, timely repair or replacement is crucial to maintain safety and operational efficiency.
Conclusion
Fenders are indispensable in marine construction, serving as crucial protectors of both vessels and infrastructure. The key takeaways to remember include recognizing the diversity of fender types, understanding the importance of meticulous selection criteria, and placing an unwavering emphasis on safety throughout their deployment.
PILE BUCK’S TOP RECOMMENDED FENDER SUPPLIERS
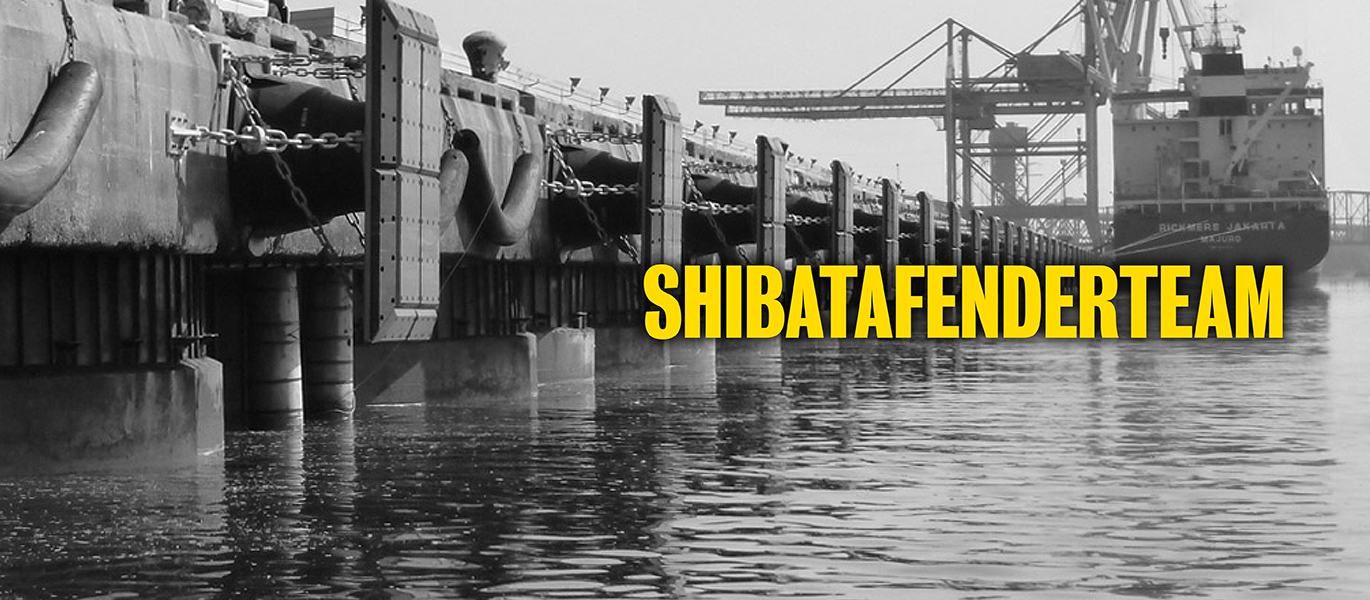
Description
The ShibataFenderTeam Group is the leading international fender manufacturer with 60+ years of group experience in fender production, +145,000 fenders in service, and 100 years of experience in the production of rubber products. They are headquartered in Germany with regional offices in the US, Europe, and Asia, supported by a large network of well-established local representatives on six continents. As a specialist for customized fender solutions, they focus on vertical integration with in-house manufacturing and full-scale testing.
SFT offers the full range of marine fender products, from simple rubber profiles up to highly engineered systems as well as accessories and fixings. Decades of experience have gained them a reputation as a dependable partner in the international port, harbor, and waterways market.
Products Available
- Rubber Fenders
- Foam Fenders
- Pneumatic Fenders
- Corner Fenders
- Rolling Fenders
- Extruded Fenders
- Komposite Fenders
- Tug Boat Fenders
- PE Sliding Plates and Fenders
- Special Solutions
- Accessories and Fixings
- Bollards
ShibataFenderTeam
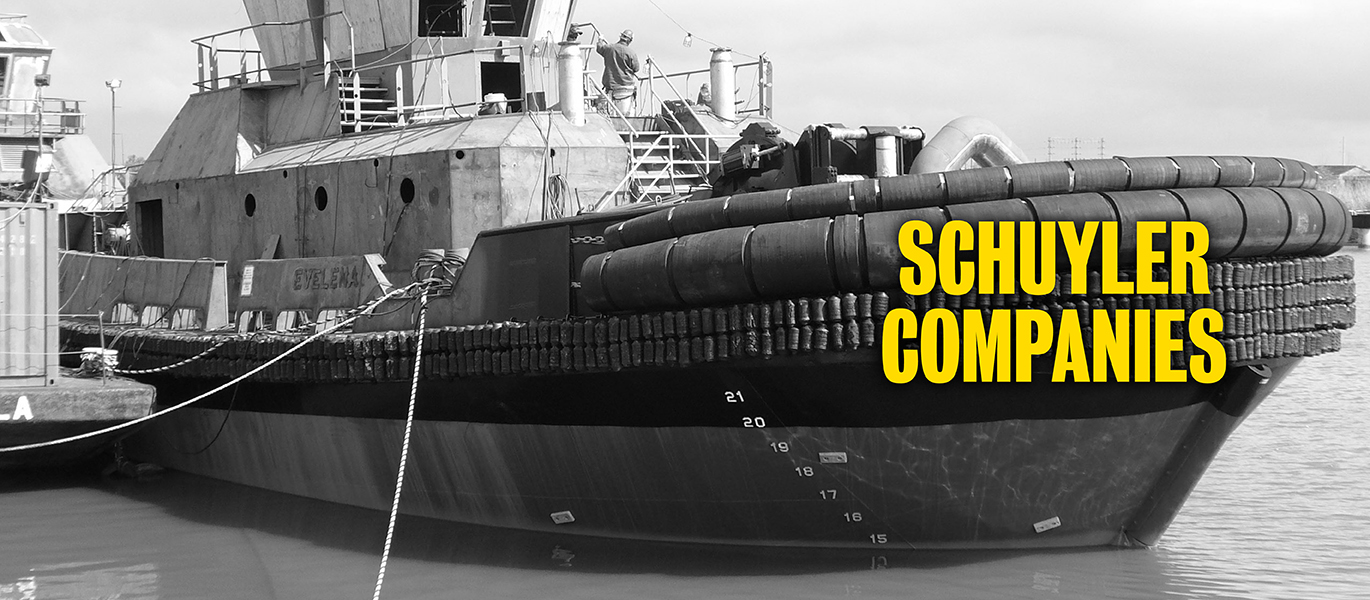
Description
Schuyler Companies is the leader in the marine fender business primarily serving the inland river operations industry. This includes all types of vessel fenders, as well as a unique array of dock fender solutions geared towards the tough barge berthing environment. Our fenders are specifically designed and crafted to be extremely durable under harsh marine conditions and our repeat clients are good evidence of the quality of our products.
Schuyler Companies’ product line includes many sizes and types of marine fenders to suit most applications. From our custom designed laminated rubber fenders that are manufactured from 100% recycled truck tire treads, to our line of extruded and molded type fenders, we have many options to offer our clients when determining their fendering needs. We understand the importance of our products for vessels and docks and work hard to ensure that our clients get the best quality, longest lasting fender at the most affordable price possible.
Products Available
- Pipe Pile Fenders
- Sheet Pile & Concrete Dock Fenders
- Steel Beam Fenders
- Bow Fenders
- Stern Fenders
- Push Knees
- D-Guard Fenders
- Side Fenders
- Extruded Fenders
- Tires for Dock & Vessel Protection