BSP and Colets Create New Piling Rig
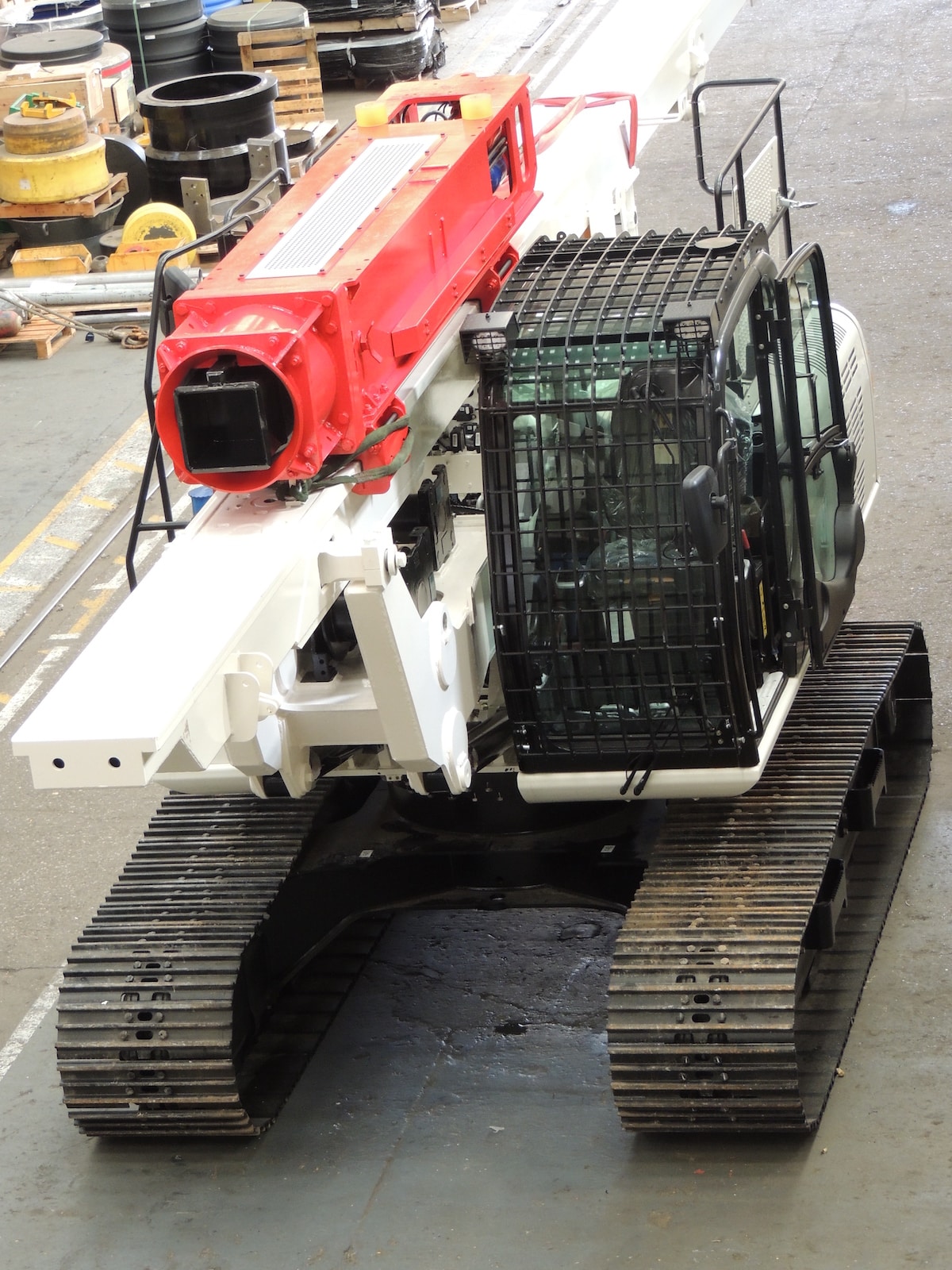
A new purpose-built piling rig to drive piles for smaller projects with limited access, working space or weight has been designed and built by BSP International Foundations (BSP) in collaboration with Colets Piling, the Sudbury, Suffolk-based contractor and piling equipment rental specialist.
Following discussions with its rental customers Colets Piling acknowledged there was a need for a piling rig to top drive steel or concrete foundation piles for small to medium-sized housing projects. According to Colets the main criteria for the new rig included ease of transportation without the need of movement orders, secondly a reduction in the costs of piling mats for the rig to operate on as this aspect can significantly increase the cost of a housing development and thirdly, increased productivity with quicker set-up, faster drive times and reliability.
John Walter, Colet’s sales manager says: “As BSP is one of the world’s leading manufacturers with over 110 years’ experience in designing and building foundation equipment we decided to approach the Ipswich-based company to collaborate with us in the manufacture and development of an excavator-mounted piling rig, built to our recommendations and specifications. This collaboration between our two companies has resulted in the JX model, the first purpose-built piling rig of its type in the UK which was built and ready for work in six months.”
“BSP is delighted to have been approached by Colets Piling to participate in the design and build of the new JX rig,” says Ray Ransome, BSP’s senior sales manager. “During the building process we encountered a few technical problems but these were resolved quickly with minimum production delay. Now that the machine is working in the piling field, we are extremely confident it will prove to be a valuable addition to the Colet Piling fleet and ultimately provide many years of productive service,” he adds.
To provide the base machine Colets Piling chose JCB to supply a number of JS excavator base units. These machines have already been introduced into the company’s contract and rental fleet in rotary drilling versions. A standard JS200 excavator with a 20t operating weight and equipped with JCB’s latest Tier 4 final emission compliant diesel engine developing 129kW, was supplied as the base machine but with a number of subtle changes to optimise the stability and performance of the completed JX unit.
As part of its involvement in the project BSP offered two hammer options. The JX20-6 fitted with a 1.5t dropweight and a 10m long mast or a JX25-8 fitted with a 2t dropweight hammer and a 13m long mast. Research showed more interest in a machine that could cope with 8m long piles, so the JX25-8 was the preferred option.
A key technical point of the project is the overall mass of the JX25-8 rig which exerts a ground pressure of only 0.57kg/cm2, further reduced once the hammer is in place and sitting on the pile – as the pile takes the weight of the hammer. The rig then only guides the pile into the ground while the hammer is driving. The JX square track configuration of the base provides maximum stability during driving.
With a working radius of 3.1m, the mast can be placed in any position around the base of the machine while the five degrees of mast rotation, left or right, helps keep the mast vertical when working on uneven ground. The rig can self-erect its mast without the aid of additional plant. It also has two dedicated lift winches, one to raise the hammer and the other to lift a pile with a maximum weight of 1.5t. Hydraulic arms retain the bottom of the pile to guide it in place once positioned at any point around the machine. There is also the option of a telescopic foot fitted to the bottom of the mast to guide the pile.
The hydraulic hammers driven by the base unit are from BSP’s popular compact DX range, designed for infrastructure foundation work in the rail sector market as an alternative option in a demanding environment. The DX hammer’s versatility and low power consumption of 40kW made it the obvious choice for the new JX rig.
According to BSP the hammer’s fully controllable hydraulically accelerated drop weight it will out-perform other hydraulic hammers in its weight class and, in some cases, has been recorded to double productivity. Estimates suggest that over 250 liner metres of pile can be driven in one shift using the JX rig. The DX range of hammers are equally capable of driving steel tubes, “H” piles, wooden or precast concrete pile sections to an ultimate load bearing capacity of over 1800kN.
In operation the hammer retains a dedicated helmet or cap suited to the pile to be driven, keeping the centre line of the hammer in line with the pile. This ensures maximum transfer of energy from the hammer to the pile. A plastic dolly is used in the helmet to prevent metal to metal contact of the drop weight onto the helmet.
Shock absorbers are also built into the hammer to dampen the pile recoil, reducing vibration to the cage and hydraulic cylinder assembly. This can reduce any down time of the hammer or the rig. Once piling is completed the mast is lowered and the JX rig can be driven on to a low loader, without the need to remove the hammer from the mast.
One of the first projects involving the JS Rig was the driving of concrete piles on the third phase of a new housing development being built by Bovis Homes in Congleton, Cheshire. The new rig was hired to Tritech Piling & Foundations by Colets Piling to drive 200mm square concrete piles between six and seven metres in depth on the site. All the piles were driven to a set with the DX hammer performing a 300mm long stroke.
Tritech operator Karl Amos, with many years’ experience of rig operation, was happy with its performance after getting to grips with the new controls and was able to achieve a production rate of 150 linier metres driven per day. Each pile requires two, four metre long sections driven but the rig was able to double this to meet the demands of competitive pricing for this particular application. Tritech have subsequently completed a number of jobs driving both concrete square piles and steel tubes and are still currently renting the rig for the foreseeable future.
In the meantime BSP is in the process of tailoring the rig for Tritech giving them the option to buy in the coming months.
The combination of an established JS excavator as the base unit and with a calculated ground force of only 0.57kg/cm2 it makes a good case for the JX rig as an economical solution for driving short piles of either steel or concrete on construction sites with restrictions on access, working space or weight.