Mastering Steel Pipe Pile Installation: Techniques, Challenges, and Solutions
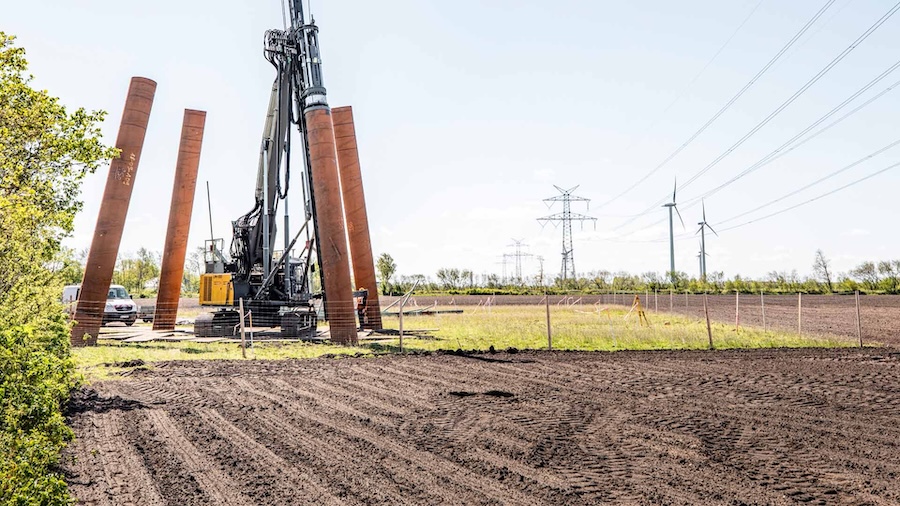
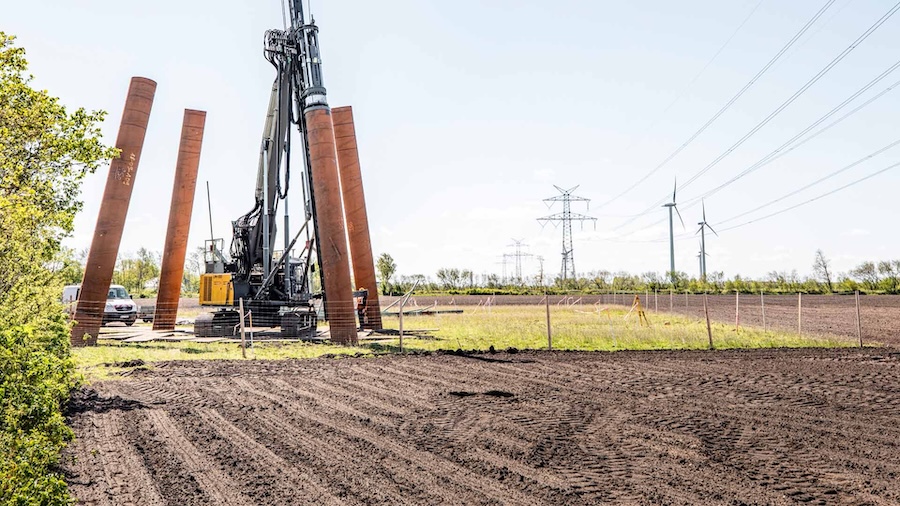
View the complete article here.
Steel pipe piles are essential in foundation and construction projects due to their strength and versatility. These cylindrical, hollow steel structures are driven or drilled deep into the ground to support heavy loads—making them ideal for challenging soil conditions. Commonly used in deep foundations, marine construction, and infrastructure projects—steel pipe piles are employed in applications like supporting buildings, bridges, docks, and offshore platforms. Their adaptability in terms of size and design allows them to meet the specific demands of various projects.
This guide focuses on the installation techniques for steel pipe piles, exploring the common challenges faced during the process and providing practical solutions. It aims to serve as a valuable resource for contractors, engineers, and industry professionals involved in projects that require deep foundation solutions—particularly those that utilize steel pipe piles.
Types of Steel Pipe Pile Installation Techniques
Steel pipe piles can be installed using various techniques, each suited to specific site conditions and project requirements.
Driven Piles
Driven piles involve the use of heavy machinery to drive steel pipe piles into the ground using a pile driver, which repeatedly strikes the pile head—forcing it into the soil. This technique is most effective in soils with sufficient bearing capacity and is commonly used in dense or cohesive soils. The main advantage of driven piles is their ability to be rapidly installed with precise control over the alignment and depth. However, the process can generate significant noise and vibration—which may be a limitation in sensitive areas.
Bored Piles
Bored piles are installed by drilling a hole into the ground and then placing a steel pipe or casing within the borehole. The drilled hole is typically filled with concrete after the steel pipe is positioned. This method is preferable in situations where ground vibrations need to be minimized, such as near existing structures or in densely populated areas. Bored piles are particularly useful in soils with large boulders or other obstructions that would make driven piles difficult to install.
Screw Piles (Helical Piles)
Screw piles, also known as helical piles, are installed by twisting the steel pipe into the ground using specialized machinery. The helical plates welded to the pipe create a screw effect, allowing the pile to be driven into the soil with minimal disturbance. Screw piles are advantageous in soils where traditional driving methods might cause too much disruption or where quick installation is required. They also offer the benefit of being removable and reusable, which is ideal for temporary structures or projects in sensitive environments.
Pressed-in Piles
The pressed-in piling technique involves the use of hydraulic machinery to press steel pipe piles into the ground without the use of impact force. This method is especially beneficial in environments where noise and vibration must be minimized, such as in urban areas or near historic structures. Pressed-in piles offer the advantage of quiet and vibration-free installation, reducing the risk of disturbance to surrounding areas while still providing robust foundation support.
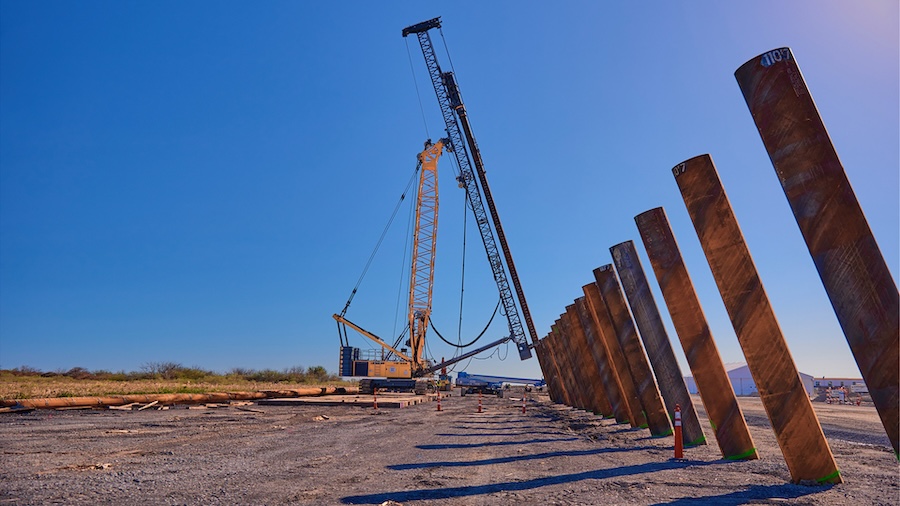
Common Challenges in Steel Pipe Pile Installation
Steel pipe pile installation presents a range of challenges, primarily influenced by site-specific conditions and project demands.
Soil and Subsurface Conditions
One of the primary challenges in steel pipe pile installation is dealing with varying soil and subsurface conditions. The type of soil—whether loose, cohesive, or rocky—can significantly impact the installation process. Loose soils may require additional stabilization, while rocky soils can complicate driving or drilling operations. Additionally, the presence of a high water table or underground obstacles such as boulders or old foundations can create further difficulties—necessitating careful planning and sometimes the use of specialized techniques to ensure the piles are installed correctly and securely.
Equipment Limitations
The success of steel pipe pile installation is often dependent on the availability and capability of the equipment used. Certain installation techniques, such as driving or pressing-in piles, require specific machinery that may not always be available on-site. Additionally, handling large diameter or deep piles can pose significant logistical challenges—particularly in tight or remote locations. The limitations of the equipment can impact the efficiency and effectiveness of the installation process, sometimes requiring modifications to the initial project design or the use of alternative methods.
Environmental and Regulatory Constraints
Environmental and regulatory constraints are significant factors in the installation of steel pipe piles. Environmental concerns, such as noise and vibration, can affect local ecosystems and may lead to restrictions on the use of certain installation techniques. For example, driven piles can produce significant noise—which might not be permissible in residential or environmentally sensitive areas. Compliance with local, state, and federal regulations is also crucial—as projects must adhere to guidelines that protect both the environment and the safety of nearby structures. Navigating these constraints often requires careful planning and potentially more costly mitigation strategies.
Project-Specific Design Requirements
Every construction project has unique design requirements that can pose challenges during the installation of steel pipe piles. Custom designs may require non-standard pile sizes or configurations, which can complicate the installation process. Additionally, meeting specific load requirements and ensuring the integration of piles with other structural elements can be complex—particularly in projects that involve retrofitting or expanding existing structures. These challenges necessitate close collaboration between engineers and contractors to develop solutions that meet both the design specifications and practical installation considerations.
Solutions and Best Practices for Overcoming Installation Challenges
Overcoming the challenges of steel pipe pile installation requires strategic solutions and best practices.
Pre-Construction Planning
Effective pre-construction planning is crucial for overcoming the challenges of steel pipe pile installation. This process begins with thorough site investigations and soil testing, which are essential to understanding the subsurface conditions that will affect the installation. By gathering detailed information on soil composition, water table levels, and potential underground obstacles—project teams can select the most appropriate installation methods and equipment for the specific site conditions. Proper planning helps in anticipating potential issues and enables the development of contingency plans to address unforeseen challenges.
Use of Advanced Equipment and Technology
The use of modern equipment and technology plays a vital role in streamlining the installation process and addressing equipment-related challenges. Hydraulic hammers, oscillators, and silent piling machines are examples of advanced equipment that can enhance installation efficiency while minimizing noise and vibration. Additionally, integrating real-time monitoring systems allows project teams to track installation progress and make adjustments as needed—ensuring that piles are installed to the correct depth and alignment. These technologies not only improve the precision of installation but also reduce the risk of delays and rework.
Collaboration with Experienced Contractors and Engineers
Collaboration with specialized contractors and experienced engineers is a best practice that can help address the complex challenges of steel pipe pile installation. These professionals bring valuable expertise and insights that can guide the project through difficult terrain, unique design requirements, or stringent environmental regulations. Case studies of successful collaborations often highlight the importance of teamwork and communication in overcoming obstacles.
Case Studies and Real-World Examples
These hypothetical examples illustrate how steel pipe pile installation can be successfully adapted to diverse and challenging environments.
Example 1: Urban Construction
In a densely populated urban environment, a major challenge faced during steel pipe pile installation was the need to minimize noise and vibration to avoid disrupting nearby residents and businesses. The project team implemented silent piling machines and employed pressed-in piles, a technique that significantly reduced noise levels and virtually eliminated vibrations. Additionally, the use of real-time monitoring systems allowed the team to track installation progress and make necessary adjustments quickly—ensuring that the piles were installed efficiently without compromising the structural integrity of adjacent buildings.
Example 2: Marine Installation
A marine construction project required the installation of steel pipe piles for a new dock structure, presenting unique challenges such as tidal influence and underwater obstacles. The project team conducted thorough underwater surveys to identify potential obstacles and employed a combination of driven and screw piles to navigate the varying seabed conditions. To counter the tidal influences, the team carefully timed the installation activities to coincide with low tide—reducing the impact of water movement on pile positioning. The successful completion of the project demonstrated the importance of adaptive techniques and precise planning in challenging marine environments.
Example 3: Seismic Region
In a seismically active region, the installation of steel pipe piles required additional considerations to ensure the stability and resilience of the foundation. The project team used advanced soil testing and geotechnical analysis to determine the best installation method and pile design to withstand potential seismic forces. They opted for a combination of driven piles and bored piles with reinforced casings to provide additional strength. Furthermore, the use of seismic isolation techniques during the installation process helped mitigate the impact of ground movements on the structure—ensuring long-term durability and safety.
View the complete article here.
What are the main techniques for installing steel pipe piles?
Techniques include driven piles, bored piles, screw piles, and pressed-in piles.
What are the common challenges in steel pipe pile installation?
Challenges include varying soil conditions, equipment limitations, and environmental constraints.