Foundations of Solar Farms: Choosing the Right Piles and Installation Techniques
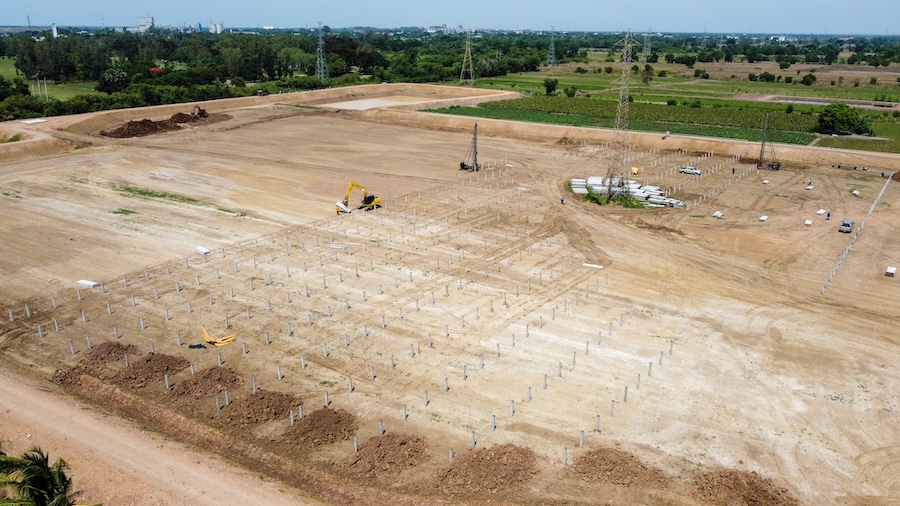
View the complete article here.
This guide is tailored for pile driving contractors and engineers involved in solar farm projects—providing an in-depth exploration of the techniques, materials, and challenges associated with pile driving in this growing sector. As the demand for renewable energy increases—solar farms are becoming an ideal market for pile driving contractors due to the need for stable, long-lasting foundations that can support large-scale solar installations.
Types of Piles Used in Solar Farm Construction
In solar farm construction, the selection of the appropriate pile type is crucial for ensuring the stability and longevity of the infrastructure.
Common Pile Materials
Steel is one of the most commonly used materials for piles in solar farm construction. Its high strength-to-weight ratio makes it ideal for bearing significant loads, and it can be driven into a variety of soil types. Steel piles are also highly durable and can be galvanized to resist corrosion, which is particularly important in environments with high moisture or salinity.
Concrete piles, including both precast and cast-in-situ types, are another popular option. They are often used in projects where the load requirements are substantial or where ground conditions are particularly challenging. Concrete piles provide excellent resistance to compression and can be customized in shape and size to suit specific project needs. However, they are typically more labor-intensive to install compared to steel piles.
Composite piles, which combine materials such as steel and concrete, offer a blend of the advantages of both. These piles are designed to provide superior performance in specific environments, such as those requiring high load capacity with minimal settlement. The combination of materials can also help manage costs and improve the lifespan of the pile system.
While less common in modern solar farm construction, timber piles can be used in certain low-impact or environmentally sensitive projects. They are typically limited to smaller installations and are best suited to regions with readily available timber resources and where sustainability is a key concern.
Selection Criteria for Piles
The choice of pile type is heavily influenced by the soil conditions at the construction site. For instance, steel piles may be preferred in softer soils where their driving ability is advantageous—while concrete piles might be more suitable for areas with hard, rocky ground. Geotechnical assessments are crucial to determine the appropriate pile material and design.
The load-bearing capacity needed for the solar farm is another critical factor in selecting the type of pile. Projects requiring high load capacities—such as those with large, heavy solar panels or in regions with significant wind forces—may necessitate the use of concrete or composite piles. Conversely, smaller installations might effectively utilize steel or even timber piles.
Environmental factors—including corrosion potential, seismic activity, and groundwater levels—play a significant role in pile selection. In corrosive environments, such as coastal areas, galvanized steel or concrete piles may be favored for their durability. In seismic zones—piles that can absorb and dissipate energy, such as ductile iron piles, might be selected.
The cost and local availability of materials can also dictate the choice of piles. In regions where steel or concrete is readily available, these materials may be preferred for economic reasons. Conversely, in areas where logistics are challenging, using locally sourced materials like timber may be more practical.
Case Studies
Case study #1 (steel piles in windy environments): A solar farm in a coastal area with high wind loads utilized steel piles with additional corrosion protection. The flexibility of steel allowed the piles to withstand both the high wind forces and the corrosive coastal environment.
Case study #2 (concrete piles in rocky terrain): A solar farm located in a mountainous region with rocky terrain opted for concrete piles. The high compressive strength of concrete made it the ideal choice to handle the challenging ground conditions and heavy loads.
Case study #3 (composite piles in seismic zones): In an earthquake-prone area, composite piles were used to provide the necessary load capacity while also offering flexibility to absorb seismic forces—ensuring the stability of the solar panels.
Pile Driving Techniques for Solar Farms
In solar farm construction, the choice of pile driving techniques is crucial not only for ensuring the structural integrity of the installation but also for optimizing efficiency and minimizing environmental impact.
Overview of Pile Driving Methods
Impact driving is a traditional and widely used method in pile installation—where a heavy weight, or hammer, repeatedly strikes the top of the pile—driving it into the ground. This method is effective for driving piles into dense or compact soils, ensuring a secure and stable foundation. However, impact driving can generate significant noise and vibrations—which may be a concern in environmentally sensitive areas or near residential zones.
Vibratory driving is another common technique, particularly well-suited for softer soils. In this method, a vibratory hammer applies rapid oscillations to the pile—reducing the soil’s friction and allowing the pile to sink into the ground more easily. Vibratory driving is often faster and quieter than impact driving, making it a preferred choice for projects with strict noise regulations. However, it may not be as effective in very dense soils where the friction is too high.
Press-in piling is a technique that uses hydraulic pressure to slowly push the pile into the ground. This method is ideal for urban or environmentally sensitive areas because it generates minimal noise and vibration. Press-in piling is particularly useful in soft to medium soil conditions but is generally slower and more costly compared to impact or vibratory driving.
Screw piling involves driving piles with helical screws into the ground, similar to turning a screw into wood. This method provides excellent load-bearing capacity and is particularly suitable for soils with varying densities. Screw piling is also advantageous in terms of installation speed and can be easily removed or repositioned if necessary, but the initial cost of equipment can be higher.
Equipment Used in Pile Driving
Hydraulic pile drivers are a versatile piece of equipment commonly used in solar farm construction. These machines offer the flexibility to switch between impact and vibratory driving methods, depending on the soil conditions and project requirements. They are also known for their efficiency and precision in driving piles to the desired depth and alignment.
Vibratory hammers are specialized tools designed to apply oscillations to the pile, facilitating its penetration into the ground. These hammers are often used in conjunction with cranes or excavators, allowing for the quick installation of piles in soft to medium soils. They are favored in projects where speed and noise reduction are priorities.
Silent pilers, used in press-in piling techniques, are designed for projects where minimizing environmental disruption is crucial. These machines apply hydraulic pressure to install piles with minimal noise and vibration, making them ideal for urban settings or near sensitive habitats. While silent pilers are effective in specific conditions, they are generally more expensive and require careful planning to use effectively.
Screw pile drivers are equipped with rotating heads that drive helical piles into the ground. This equipment is highly effective in creating strong foundations with minimal ground disturbance. Screw pile drivers are particularly useful in areas with challenging soil conditions, where other methods may struggle to achieve the required load capacity.
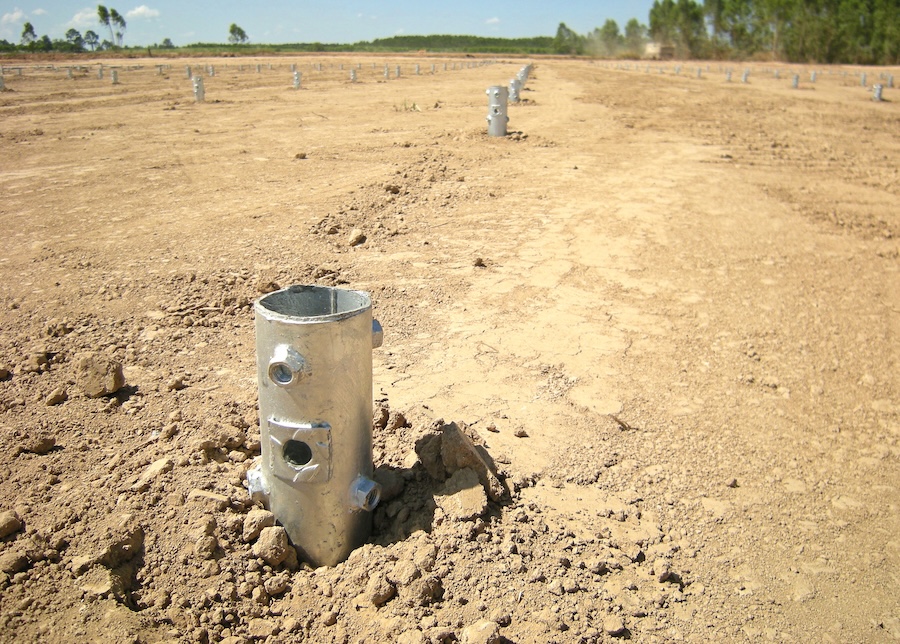
Site Preparation and Installation Process
Ensuring the success of a solar farm project begins with meticulous site preparation and a well-planned installation process.
Pre-Construction Site Assessment
Before any pile driving begins, conducting thorough site surveys and soil testing is essential to understand the ground conditions. These assessments help identify soil composition, groundwater levels, and any potential obstacles or challenges that could impact the pile installation process. Knowing the site’s geological characteristics allows engineers to choose the most suitable pile type and driving method, ensuring a stable foundation for the solar farm.
The data gathered during the pre-construction phase directly influences the pile driving strategy—including the selection of equipment, pile material, and installation method. For example, if soil tests reveal a high water table—contractors may opt for piles with anti-corrosion properties or choose a driving technique that minimizes soil displacement. By tailoring the approach to the specific conditions of the site, contractors can optimize the efficiency of the installation process and reduce the risk of future structural issues.
Step-by-Step Pile Installation Process
The pile driving installation process begins with site clearing and preparation—which involves removing any vegetation, debris, or obstructions that could interfere with the work. After the site is cleared, the locations where the piles will be installed are carefully marked based on the project’s layout plan. Next, the positioning of pile driving equipment is done accurately over the marked spots to ensure that each pile is driven at the correct location—maintaining the structural integrity of the entire solar farm. Once the equipment is in place, the driving of the piles begins using the selected method—whether impact, vibratory, press-in, or screw piling. Throughout this process, close monitoring is conducted to ensure that the piles are installed vertically and at the correct angle. Finally, the verification of depth and alignment takes place after driving each pile—using precision measuring tools to confirm that the piles meet the project’s engineering specifications and are prepared to support the solar panel structures.
During installation, several key considerations must be taken into account to ensure the success of the project. Alignment is crucial; maintaining proper alignment of the piles is essential to prevent issues during the installation of solar panels. Misaligned piles can lead to structural imbalances, which in turn cause inefficiencies in the solar farm’s performance. Additionally, depth control is vital to the stability of the foundation. Accurate control of the pile driving depth ensures that the piles reach the stable strata of the soil, providing the necessary load-bearing capacity. Any deviations in depth can compromise the foundation’s stability, potentially leading to long-term structural issues.
Quality Control and Inspection
Implementing rigorous quality control measures throughout the pile driving process is vital to ensure the long-term stability and safety of the solar farm. Regular inspections and adherence to industry standards help identify and rectify any issues early in the installation process, reducing the risk of costly repairs or failures later.
To ensure the integrity of installed piles, several techniques are employed throughout the construction process. Non-Destructive Testing (NDT) methods—such as ultrasonic testing, radiography, or pile integrity testing (PIT)—are used to assess the integrity of the piles without causing any damage. These tests are crucial for detecting flaws, cracks, or voids within the pile material that could potentially weaken its structural performance. Additionally, load testing is performed on a sample of installed piles to verify their capacity to withstand the expected loads. This process involves applying a controlled load to the pile and measuring its response, ensuring that the foundation is capable of supporting the solar panels effectively. Finally, regular inspections are conducted throughout the installation process to maintain high standards of quality. Inspectors check for proper alignment, depth, and material integrity—making necessary adjustments to ensure that all piles meet the project specifications.
Challenges and Solutions in Pile Driving for Solar Farms
Pile driving for solar farms often involves navigating a range of challenges, from difficult soil conditions to the logistical hurdles of remote locations and adverse weather.
Common Challenges
Pile driving for solar farms can present a variety of challenges, particularly due to the diverse environments in which these projects are undertaken. One of the most common challenges is dealing with difficult soil conditions—such as extremely hard or rocky ground, soft or unstable soils, or varying soil layers that require different approaches to pile driving. Remote locations also pose logistical challenges, as transporting equipment and materials to these sites can be difficult and costly. Additionally, working in remote areas often means limited access to necessary resources and services—which can delay the project. Weather conditions are another significant factor, as adverse weather—including high winds, heavy rains, or extreme temperatures—can interrupt pile driving operations and extend the project timeline.
Solutions and Innovations
To overcome these challenges, innovative solutions and technologies have been developed to improve the efficiency and effectiveness of pile driving in solar farm projects. For instance, advanced geotechnical surveys and soil testing techniques allow for a more accurate assessment of ground conditions before construction begins—enabling the selection of the most appropriate pile type and driving method. Modular and portable equipment has been designed to facilitate easier transport and assembly in remote locations, reducing the logistical burdens associated with these projects. Additionally, weather-resistant machinery and flexible scheduling practices help to minimize the impact of adverse weather on project timelines.
View the complete article here.
What types of piles are used in solar farm construction?
Common piles include steel, concrete, composite, and timber piles.
What are the main pile driving techniques for solar farms?
Techniques include impact driving, vibratory driving, press-in piling, and screw piling.