INTERVIEW: Everpads
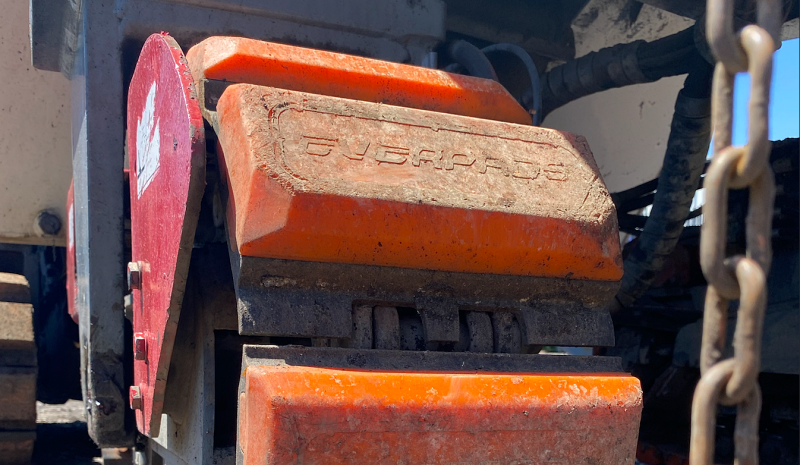
Pile Buck’s interview with EVERPADS, manufacturing cutting-edge spare parts for the global construction industry for over 90 years.
PB: How did EVERPADS get its start?
EP: Our founder, Mr. Leo Chiang, started EVERPADS as a single manufacturer of high-end solid rubber tires. To meet the growing demand for high-quality, cost-effective solutions for construction needs, Mr. Chiang expanded the manufacturing operations and product categories.
PB: What drives Mr. Chiang take such big risk to expanded from rubber expert to comprehensive heavy equipment spare part field?
EP: Actually, it was planned from the beginning and aligns with Mr. Chiang’s vision at the time. Mr. Chiang recognized the industry’s issues, particularly the low-quality infrastructure from contractors, which increased traffic difficulties and posed safety risks. After visiting these contractors, Mr. Chiang identified a key pain point at the time: they struggled to gather resources for construction due to the lack of high-quality aftermarket brand and the premium pricing of OEM parts. To solve this issue, Mr. Chiang founded Everpads!
PB: It sounds like Everpads was designed for contractors who struggled to balance cost and quality. However, it seems your current position might be slightly different. Can you clarify?
EP: Yes, you’re right. Some people might misunderstand Everpads’ position as purely cost-efficient. Our mission is to offer the best spare parts to help customer growth. This means that every product we introduce is designed to be durable, perform exceptionally well, and without premium priced.
PB: Okay, so whose Everpads target audience?
EP: We serve those who believe that providing high-quality infrastructure is essential to the world. This includes professionals focused on project optimization, who want to concentrate on their core work without worrying about spare parts issues.
PB: We’ve discussed Everpads’ brand commitment in depth, so let’s return to how you deliver it. Everpads has expanded well beyond high-end solid rubber tires. How did this growth unfold?
EP: Good, I hope readers will find it interesting. That’s right. We offer road engineering machinery parts, asphalt milling machines, pavers, and spare parts for excavators, compactors, and vibratory hammers, supporting construction projects in over 80 countries.
PB: Let’s talk about EVERPADS spare parts offerings starting with undercarriage parts for heavy equipment.
EP: Okay, our undercarriage system have three categories track rollers, poly pads, and idler rollers.
PB: What’s its claim to fame?
EP: It has an innovative heavy-duty sealed system that solves the challenge of unexpected oil leakage problems. We redesigned the structure of the track roller to prevent 99% of oil leakage.
PB: In the catalogue, it also says the E-generation track roller includes a safeguard mechanism design.
EP: This feature ensures uninterrupted functionality even in the event of unexpected failures, such as crushing hard objects or tilting to one side during construction.
PB: How?
EP: Thanks to the Gen-E sealed system, lubrication will still be contained within the roller, enabling continued movement capability. And the tapered bearing system also contribute a lot to the Gen-E track rollers.
PB: What is the value of the tapered bearing system?
EP: Its state-of-the-art tapered bearing system reduces friction and wear and tear on the machinery. This prevents equipment failures, even in the most punishing work environments.
PB: What type of loads can the tapered roller bearings handle?
EP: Both radial and axial loads efficiently. No matter the type of load you are moving, track roller products from EVERPADS are designed to facilitate movement in some ways, while restricting movement in others.
PB: What type of roller oil is best for the E-generation track roller?
EP: EVERPADS offers a high-quality roller oil that provides superior internal lubrication with a low heat coefficient.
PB: And that maintains an optimal internal temperature?
EP: It does. With our E-generation track roller, in conjunction with our roller oil, the heaviest equipment will perform at its best, even under extreme conditions.
PB: EVERPADS also offers several track pads. Tell us about your Polyurethane Pad for milling machines.
EP: These pads are engineered for asphalt milling machines. No matter your machine’s load capacity, the Polyurethane Pad from EVERPADS is up to the task, even if it is above 80,000 pounds.
PB: What are some of the key features of your poly pads?
EP: Long-lasting and thicker pads compared to other conventional poly pad products, with a service life of over 1600 hours. Our poly pads have a patented Chamfer edge design for advanced steering agility.
PB: Your poly pads also have built-in plates.
EP: That’s right. Our patented built-in plate design significantly enhances the adhesive force, preventing unexpected breakage at each track pad.
PB: What are the hardness ranges for EVERPADS poly pads?
EP: To create good texture and high utilization against the surface, our hardness ranges from 90-95 HRC.
PB: What about installation?
EP: Our bolt-on track pads provide a more straightforward installation and cost-efficient solution.
PB: Okay, do you provide track pads for other kind of machines?
EP: Yeah, we also have rubber track pads for excavators, pavers, compactors. Excluding the shape and structure design for pads we mentioned above. By 90-year experiences on rubber generation, we designed these rubber pads with specific features for each machine types.
PB: Could you highlight them?
EP: For example pavers’ pads required oil resistance and steering stability, excavators’ required cut-resistance, steering agility and precision.
PB: What you just mentioned is about the operation performance and failure resistance, Is their serve time longer than others?
EP: Yeah our rubber pads provide 30-40% longer lifespan compared to upper-medium quality pads in the market.
PB: How?
EP: Our low-heat technology in rubber compound production empowers the final products to maintain temperatures below the degradation line. Additionally, the compound has excellent abrasion resistance. These two features ensure longevity in both lifespan and length of continuous use time of the pads.
PB: Tell us about the Gen-E Milling System.
EP: Our Gen-E milling system is an advanced suite of parts and components purpose-built for the demands of asphalt milling machines.
PB: In what way?
EP: Each element of the parts, from cutting tools to milling drum, is engineered with precision and attention to detail.
PB: EVERPADS has a great case study of your milling teeth.
EP: Hesheng Road Construction was milling very hard AC in Taiwan. They reduced their costs by 40% and increased performance by switching from OEM parts for their W100 milling machines and using EVERPADS’s Gen-E T6 Milling Teeth. Read the case study.
PB: That’s incredible. Tell us more about the Gen-E T6 milling teeth.
EP: Our patented shape design ensures the best rotating performance and better protection to the tool holder during the milling process.
PB: What are the milling teeth made of?
EP: High-quality steel. The tungsten carbide is made of German materials to cut tough hard pieces.
PB: Tell us about your conveyor belts.
EP: In 1999, we developed an ideal rubber material to make unparalleled conveyor belts and have expanded the selection of products for several planer makes and models.
PB: What are the features of your conveyor belts?
EP: EVERPADS conveyer belts feature an anti-asphalt surface layer, high elasticity middle layer, tear resistant polyester-polyamide textile layers (up to 5 layers), and a 3D pattern.
PB: What type of threads are used?
EP: Our Y –shape threads help to strengthen the whole structure.
PB: What type of augers does EVERPADS offer?
EP: EVERPADS is a renowned auger blade manufacturer in the heavy equipment industry. We provide a large selection of cost-effective auger blades for pavers.
PB: How are EVERPADS augers made?
EP: Our high-quality auger blade features extremely precise casting. It’s specially heat-treated, featuring HRC 55 of hardness, which includes outstanding wear resistance.
PB: Can you customize them?
EP: Our experts can customize auger blades that ensure the spiral parameters meet the requirements of the anti-segregation and uniformity of the paved pavement.
PB: What does EVERPADS offer for shock absorption systems?
EP: We have an array of high-quality parts for shock absorption. One great example is the IC05 rubber buffer series for vibratory hammers.
PB: What are the key features of the IC05 rubber buffer?
EP: The Formula E keeps the rubber heating down at 63 C/145 F to prevent the rubber from exceeding the fatigue temperature point. This triples rubber buffer service life.
PB: What about the steel plate?
EP: The steel plate of the IC05 rubber buffer features multi-process treatment with heating, electroplating, and anti-corrosion treatments.
PB: EVERPADS has another great case study using a customized rubber buffer.
EP: We developed a customized rubber buffer for the Starke SV series of suspended vibratory pile hammers.
PB: Why did Starke need a customized rubber buffer?
EP: They needed a higher force rubber buffer for a vibratory pile machine with a maximum centrifugal force of 350kn to 2498kn to expand users among heavy non-residential construction. The result was the IC108-9 rubber buffer. Learn more.
PB: What sets EVERPADS apart from other parts manufacturers?
EP: We understand the nuanced intricacies and perpetual challenges of project completion – from faulty parts and poorly engineered designs to inventory and supply chain bottlenecks.
PB: What else do you want our readers to know about EVERPADS?
EP: Our founder, Leo Chiang, said it best, “No matter the machine model, we stand ready to supply reliable parts and accessories tailored to your specific needs.”