USCG Station Boston Gets New Docks & Cutters
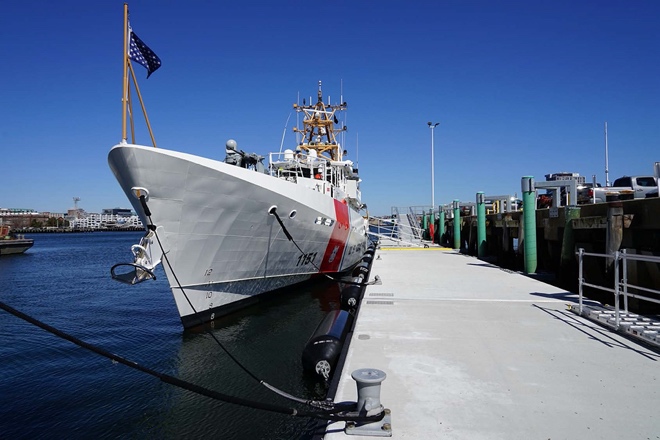
To accommodate a new fleet of Sentinel-class Fast Response Cutters, the Department of Homeland Security authorized modifications to US Coast Guard Station Boston. A significant portion of this renovation was the addition of three SF Marina floating concrete piers.
The overhaul of US Coast Guard Station Boston was a collaborative design-build project of SF Marina Systems USA, lead contractor Walsh Construction, and Collins Engineering. The floating concrete pontoons were manufactured at the Norfolk, Virginia SF Marina facility and delivered to the site by barge. Once ACK Marine had demolished and removed the existing fixed pier, the Walsh subcontractor installed the state-of-the-art Type 1850 floating pier complex.
SF Marina Type 1850 concrete pontoons are engineered for demanding applications and harsh winter weather. Their enormous mass and low center of gravity make them exceptionally stable, even with the occasional hard landing of a 154′, 353-ton Sentinel-class cutter. And with 23,018 lb.ft² of buoyancy, they’re virtually unsinkable.
ACK Marine installed three separate 16.4′ W piers: 375′, 355′, and 200′ L. Each has a 32″ freeboard that provides easier vessel access and line handling to the 20 bollards and cleats installed on each section. The docks have custom UHMW plastic wear surfaces and composite lumber rub rails. These support 4′ W x 10′ L foam-filled fenders. US Coast Guard Station Boston sees an average 10′ tide, so the floating concrete piers are secured on 16″ W steel piles with offset guides.
Founded in 1790, US Coast Guard Station Boston is home to Medium Endurance Cutters, Marine Protector-class coastal patrol boats, and numerous smaller vessels. The new 28-kt Sentinel-class Fast Response Cutters are tasked to perform a wide range of duties, from defense operations and law enforcement to search and rescue.
Since 1918, Gothenburg, Sweden-based SF Marina has engineered and manufactured floating breakwaters, concrete docks, and related marine structures that are built to withstand extreme weather events. Through a robust network of international offices and manufacturing facilities, it has completed recreational and commercial vessel projects around the globe.