How to Repair and Maintain Steel Pipe Piling
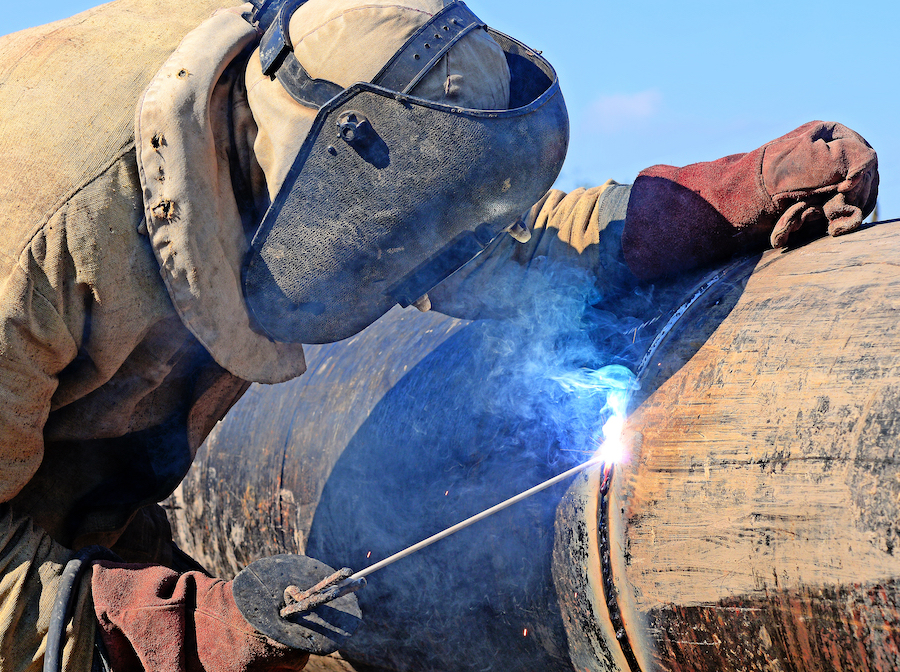
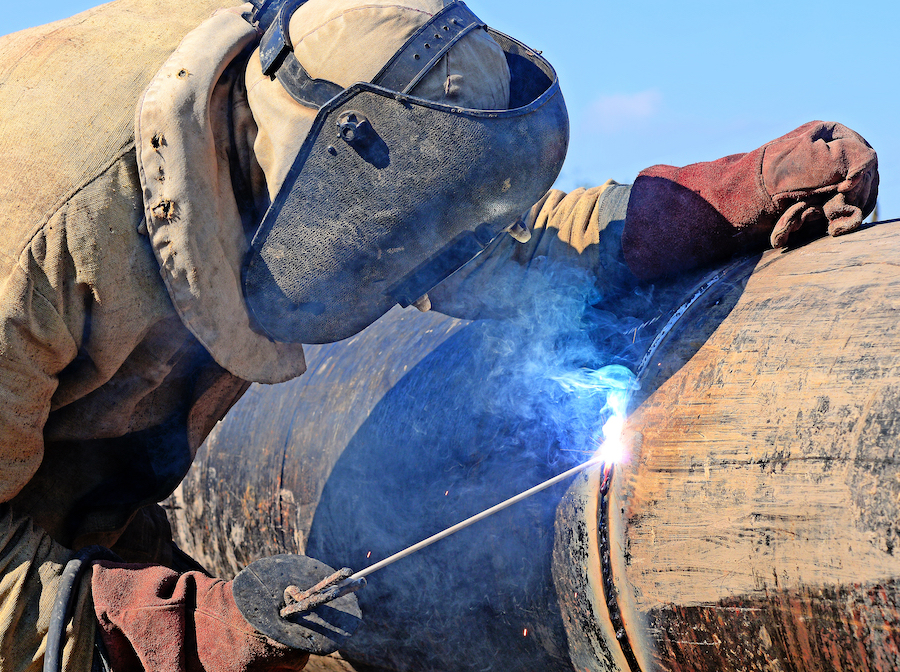
View the complete article here.
Like steel sheet pilings, steel pipe pilings are the unsung heroes of construction—providing critical support for a multitude of structures such as bridges, high-rise buildings, offshore oil platforms, and retaining walls of all sizes.
However—as resilient as they are—these crucial structural elements can succumb to environmental stressors and time—demanding effective repair and maintenance.
This comprehensive guide will discuss the processes involved in the repair and maintenance of steel pipe pilings—offering insights for effective management of these integral materials.
The Indispensable Role of Steel Pipe Piling
Steel pipe pilings are essentially cylindrical sections driven deep into the ground to serve as a robust foundation for structures. Given their high load-bearing capacity, they’re primarily used in permanent structures that demand enhanced stability—such as bridges, piers, and seawalls. Their design facilitates penetration through various soil strata (different layers of soil) until they reach a level capable of supporting the proposed structure—ensuring unwavering strength and reliability.
Early Signs of Trouble: Recognizing Damage and the Need for Repair
Recognizing the early signs of damage is crucial to prolong the life of steel pipe pilings. The most common issues include corrosion, deformation, and cracks—primarily caused by environmental exposure, excessive loads, and occasional mishandling during installation. Timely identification of these problems is ideal to prevent the risk of structural instability, safety hazards, and potentially excessive repair costs.
Here is a list of potential issues or warning signs indicating that steel pipe piling should be repaired:
- Corrosion: One of the most common problems with steel pipe pilings is corrosion, which can occur over time due to environmental exposure. Rust or discolored spots on the piling can be visible signs of corrosion.
- Cracks or fractures: These can be caused by excessive load, ground movement, or other physical stresses. Even small cracks can lead to serious issues if not addressed promptly.
- Buckling or bending: If the piling appears bent or buckled, this is a clear sign that it’s unable to support the load it was designed for. This could be due to inadequate design, an increase in load, or degradation of the piling material.
- Displacement or movement: Any visible shift in the position of the piling could indicate a problem—likely due to soil movement, inadequate support during installation, or the effects of an extreme event such as an earthquake.
- Erosion around the base: Erosion of the soil around the base of the piling can reduce its support and stability.
- Material degradation: Beyond corrosion, other forms of material degradation can occur. This could be due to the effects of the surrounding environment—such as exposure to harsh chemicals in the soil or water.
- Water leaks or seepage: If the steel piling is used in a submerged or partially submerged environment, any sign of water leakage or seepage could indicate a problem with the integrity of the piling.
- Unusual noises: Sounds such as creaking, popping, or snapping could indicate that the pilings are under stress.
Remember that regular inspection and maintenance of pipe pilings are crucial to prevent minor issues from becoming major problems. If any of these warning signs are detected, it’s important to consult with a structural engineer or another qualified professional to assess the issue and determine the appropriate course of action.
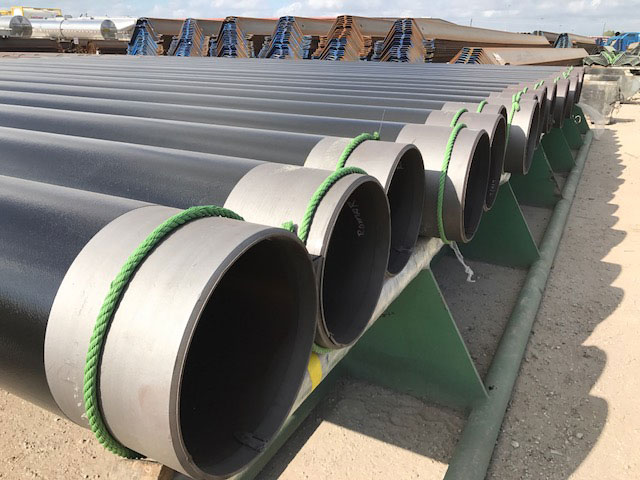
Techniques for Effective Repair
When it comes to repairing steel pipe pilings, the methods chosen will largely depend on the specific issues identified. Here are some of the most common repair methods:
- Liquid coating systems for new steel piles: New steel piles will need some sort of corrosion protection prior to being installed in marine environments. A factory-applied coating of either coal tar epoxy, coal tar replacement epoxy, or polyester glass flake reinforced coatings are exceptional options to prevent corrosion by protecting the steel from salts, acids, alkalis, and oxidizing chemicals. To learn more, visit the Denso, Inc. to see their wide range of liquid coatings for steel piles in aggressive marine environments.
- Steel jacketing: Steel jacketing involves placing a steel casing or sleeve around the damaged area of the piling and then filling the space between the casing and the pipe with grout. The casing provides additional structural support, while the grout further helps to bond the casing to the piling and seal any cracks or leaks. This method can be used for substantial structural repairs but is a bit more labor-intensive.
- Cathodic protection: Cathodic protection is a preventive measure against corrosion. There are two main types—sacrificial anode and impressed current. In the sacrificial anode method—a more reactive metal is attached to the steel, which corrodes preferentially and protects the steel. In the impressed current method, a power supply provides a current to counteract the corrosive electrical activity naturally occurring in the environment. This method can be highly effective but requires regular monitoring and maintenance to ensure it continues to function properly.
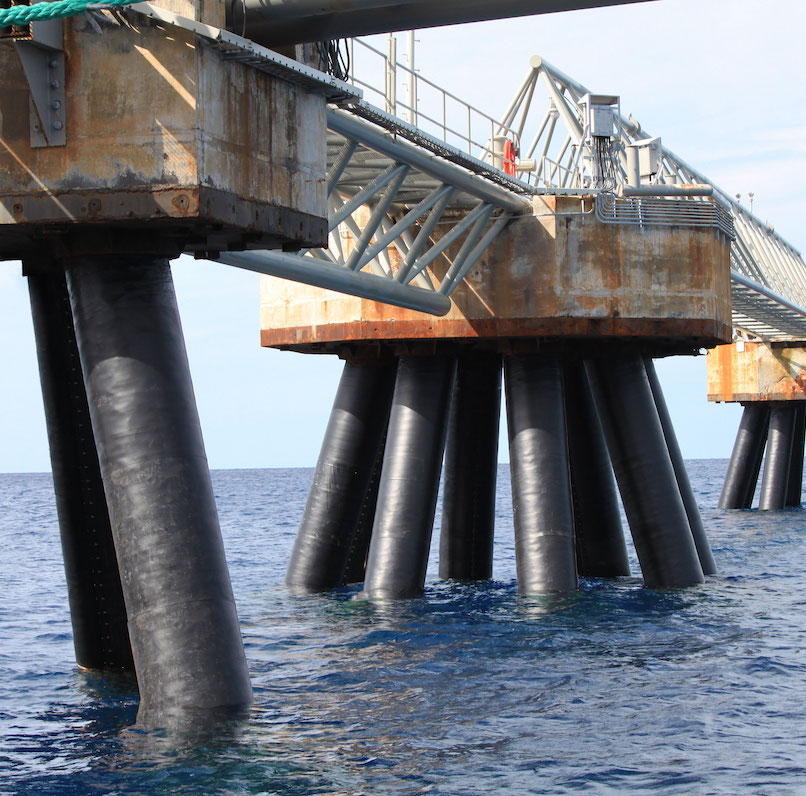
- Pile encapsulation (marine): Steel piles placed in a marine environment are crucial in supporting structures, and they take a beating due to corrosive areas at the splash-zone, inter-tidal, and subsea environments. Depending on the environment and other factors, you have a few options to help protect against corrosion. An effective anti-corrosion solution for steel piles exhibiting surface corrosion with minimal wall loss is an anti-corrosion system that utilizes a petrolatum tape to inhibit corrosion and a heavy-duty HDPE jacket for mechanical protection. For steel piles that are starting to show more severe corrosion with minimal structural integrity issues, a fiberglass jacket system using an underwater epoxy grout to encapsulate and rehabilitate the pile can be utilized. Denso, Inc. manufactures a wide range of corrosion prevention and pile rehabilitation systems for steel piles within their SeaShield Marine Pile Protection line that is featured here.
- Welding: Welding is a commonly used method to repair cracks or fractures in steel pipe pilings. A professional welder uses a high-temperature arc to melt a filler material into the crack or fracture—effectively filling and sealing the damaged area. This method restores the structural integrity of the pipe and prevents further damage. However, it should be noted that welding requires skilled labor and is not suitable for all types of fractures.
- Epoxy injection: Epoxy injection is particularly effective for smaller, hairline cracks. This method involves injecting a two-part epoxy resin into the crack under pressure, which then hardens to seal the crack and restore the strength of the steel piling. This method is primarily effective for sealing small cracks and may not be suitable for larger, structural ones.
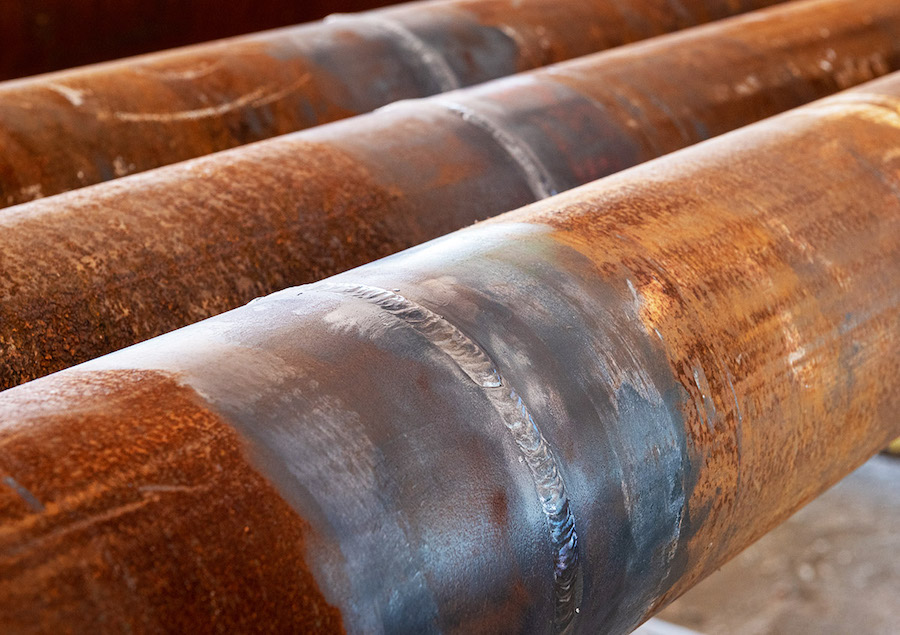
- Splicing: If a section of the steel piling is heavily damaged, it might need to be cut out and replaced. This new section can be attached via splicing, which involves either welding the new piece to the existing ones or using mechanical fasteners to join them. Splicing requires high precision and skilled work to ensure the restored piling maintains its structural integrity and alignment.
- Underpinning: Underpinning is a method used to strengthen and stabilize foundations when they are not strong or stable enough. This might involve extending the pilings deeper into the ground to reach a more stable soil stratum or widening the pilings to better distribute the load. This is a significant undertaking that requires careful planning and execution to avoid causing further damage to the structure.
- Grout injection: Grout injection is often used when the soil around the pile is unstable or has voids that might be causing the pile to move or settle. By injecting grout into the soil, these voids are filled and loose soil is compacted—thereby stabilizing the pile. This method requires an understanding of the surrounding soil conditions and the right grout mixture to achieve effective results.
Of course, each repair method has its own pros and cons so it’s important to thoroughly assess the condition of the piling and the surrounding environment before deciding on a method. As always, it’s recommended to involve experts in this process to ensure the repairs are carried out safely and effectively.
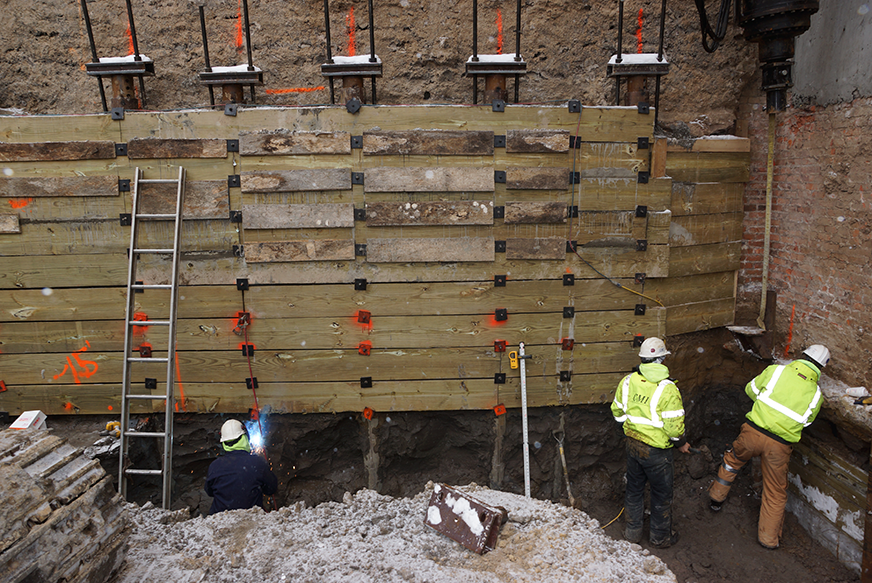
Conclusion
In conclusion, steel pipe pilings are indeed robust—but they are not impervious to wear and environmental stressors. Prompt identification and remediation of issues like corrosion, fractures, and displacement are essential to ensure safety and prevent high repair costs. Depending on the specific issues, various repair methods—including welding, epoxy injection, and steel jacketing—among others—can be employed. However, the key to the longevity of steel pipe pilings often lies in preventative maintenance—such as the regular application of protective measures and routine cleaning, especially in harsh environments.
View the complete article here.
Why is it necessary to repair and maintain steel pipe piling?
Repairing and maintaining steel pipe piling is crucial to prolong its service life and ensure the structural integrity of the construction it supports. Over time, steel piles can suffer from corrosion, fatigue, or damage from environmental factors which can compromise their strength and stability. Regular maintenance and timely repair can help prevent catastrophic failure, ensure safety, and save on costly replacements.
What steps can be taken to repair and maintain steel pipe piling?
To repair and maintain steel pipe piling, regular inspections should be performed to detect signs of damage or corrosion early. Any identified issues should be addressed promptly. Corrosion can be mitigated through various methods like cathodic protection or applying protective coatings. Damaged or critically corroded sections of a pile might need to be replaced or reinforced. It is also important to monitor and manage environmental factors that can accelerate damage, such as exposure to aggressive soils or water.