Brextor – A Quantum Leap in Pile Head Processing
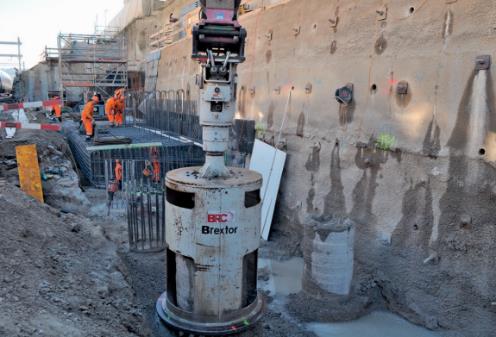
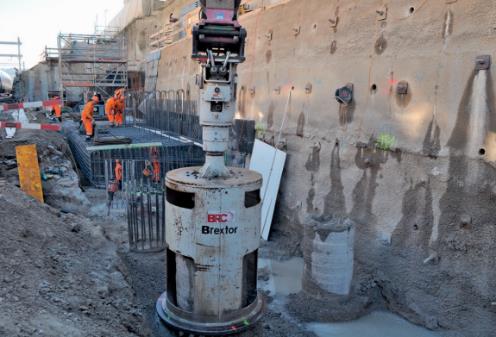
Authors: A. Portmann
Due to increased dense construction and building in exposed locations, pile foundations continue to gain in importance. Previous pile-heading methods involve risks that can be avoided with the newly developed Brextor method.
Bored piles & previous processing methods
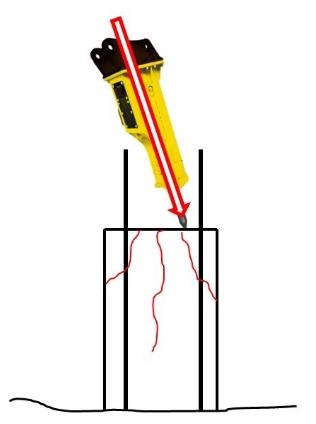
The world is becoming increasingly crowded. The annual population growth rate is currently 2%. The necessary building land is becoming increasingly rare and thus the call for denser construction is becoming stronger. The available building ground is more and more often in exposed locations and of poor bearing capacity. Pile foundations are the solution to ensure a safe foundation in such conditions. For this reason, pile foundations are becoming increasingly important. The pile head is the connection to the foundation. Highest quality without compromise is required. A foundation failure can end in disaster.
Up to now, bored piles have mainly been processed with air or hydraulic hammers. Air or hydraulic hammers work with a vertical impact energy. This processing energy cannot be controlled. Thus, there is a risk of cracks in the concrete body and spalling on the outer skin of the pile. This can cause corrosion damage in the medium term. Bent or torn reinforcements caused by air or hydraulic hammers additionally reduce the absorption capacity of the tensile load. Due to the design-related mode of operation of these devices, a correspondingly large working space is required. Furthermore, narrow & long reinforcements are difficult to process, and large obstructions occur with existing spiral reinforcement in the excavation area. In order to ensure quality and to break the surface tension, a cut must also be made to the definitive height. The last 30-50cm are only possible with a lot of manual work.
Brextor
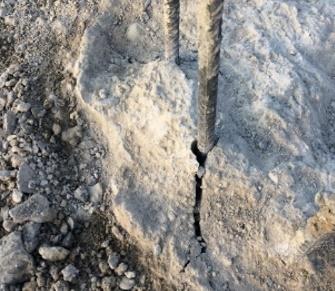
With Brextor, the working process remains under control. The horizontal force application allows 100% control of the applied processing energy. In addition to the best possible quality, the pile head is handed over to the succeeding gear with precise accuracy (height accuracy +/- 1cm). In addition, the concrete structure and reinforcements remain intact.
The core tension is broken with the Brextor internal cutter. The surface tension is broken with the Brextor external cutter. The remaining concrete border with the reinforcement inside can be broken away with the Brextor crusher without risk of damage. Thus, the finished bored pile head is achieved in four working steps:
1) prepare the pile with the milling disc,
2) mill to level (+/- 1cm height accuracy),
3) break out the remaining concrete with the BRC pile head crusher and
4. clean and align the reinforcement.
Brextor is manufactured in Switzerland in a CAD-drawn design and incorporates precision CNC machined parts. The process is patented worldwide.
New applications
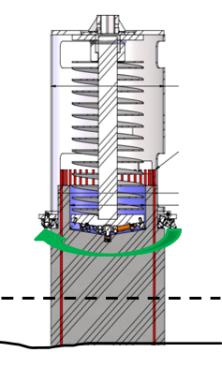
Brextor’s design allows it to be used with very little or even no lateral working space. This means that excavation can be saved. The cut at finished excavation level to break surface tension is made automatically with the external cutter. The clean-up effort is minimized to cleaning work. Brextor is suitable for all pile types/walls. The system uniformity allows easier use by site staff (1 system for all uses – bored pile, bored pile wall, earth auger). In addition, the excavated material (80% 0-30mm gravel) can very often be processed directly on-site.
Four-lane expansion Liestal, Switzerland
Figure 3 Brextor processBrextor was used for the four-lane expansion at Liestal station, which was carried out by Implenia. The expansion of the northern and southern station entrances to four lanes should ensure significantly fewer crossing conflicts and more punctual and disruption-free rail traffic for long-distance, regional, and freight traffic. “With manual removal by hydraulic hammer, there would always be a risk of damaging reinforcements and disturbing the concrete quality at the pile head. I minimize this risk with Brextor.” confirms Stefan Lang, site manager at Implenia.
Time & workspace saving
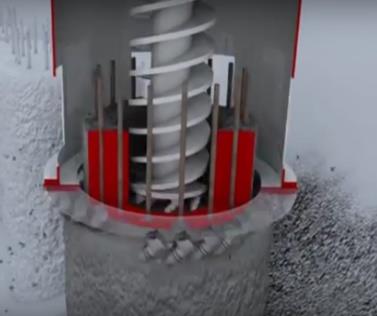
The client attaches great importance to timely execution of the work; after all, the four-track expansion is being carried out during ongoing rail operations. “The time pressure on this construction site is huge, as various milestones have to be met,” confirms Stefan Lang. “We only have a limited time window available and if this cannot be massively extended, such an undertaking would only be possible with a lot of resources and personnel without the Brextor.”
Time as a decisive factor was supplemented by the challenge of very little space. Stefan Lang “We would also need more space, which would be a big challenge here because you don’t have enough room for a pick hammer between the nail wall and the pile head.” For this reason, it would be necessary to move back the wall, which is up to 6 meters high, over a length of 300 meters, just to create enough space for the pile head to be worked. This would mean a massive increase in costs. Thanks to Brextor, these costs are saved”.
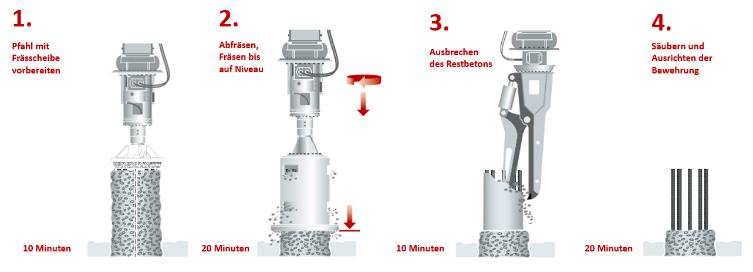
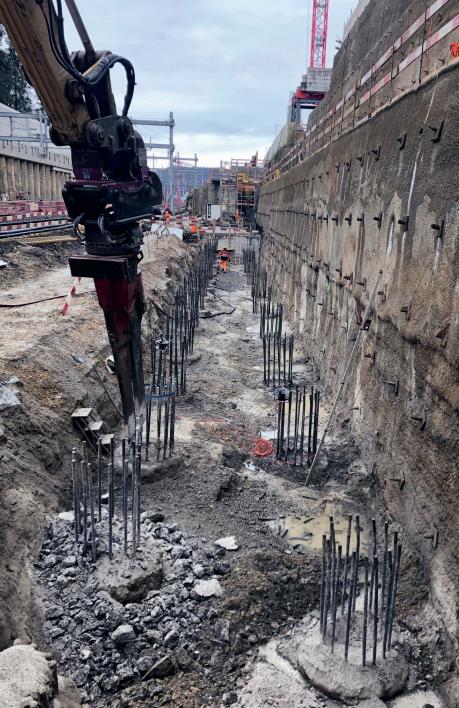
In the case of a railroad line extension, 80cm of working space could be dispensed with on the rear side. With an embankment of 6m height, over a distance of 300m, this results in 1’440m3 excavation (fixed measure) which did not have to be made. Besides the enormous cost savings for excavation, transport, landfill fee and material replacement, Brextor has made a great contribution to the environment and to the population. At least 280 truck trips of 40km each could be saved. Thus, the CO2 footprint was reduced and the population benefited from a less polluted road network.